Expert Guide to Sheet Metal Duct Fabrication for HVAC Systems
By:Admin
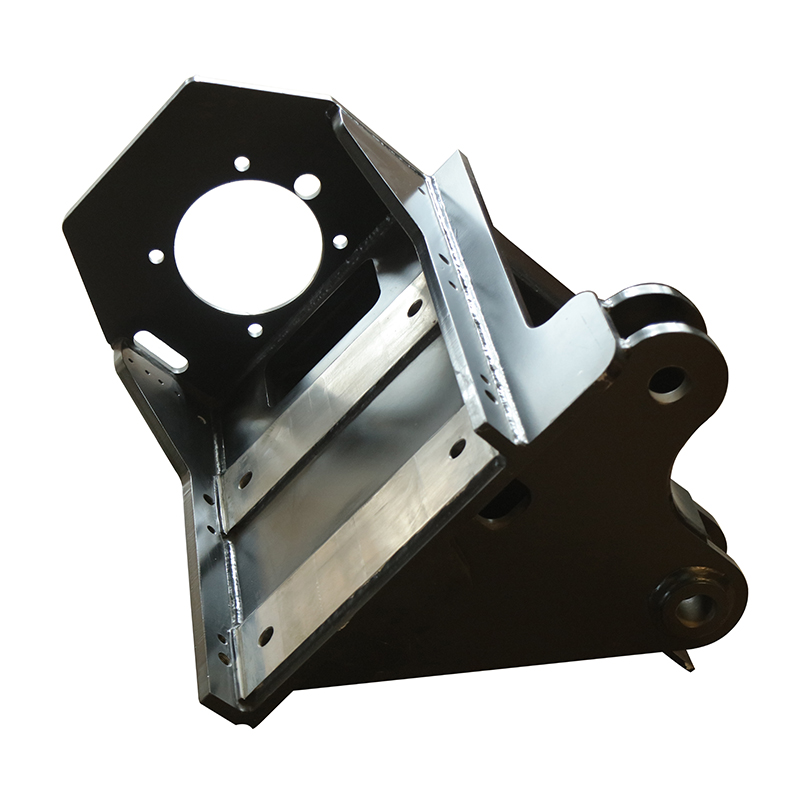
One company that has been at the forefront of sheet metal duct fabrication is {}. With a strong focus on quality, precision, and innovation, {} has established itself as a leader in the industry. The company's state-of-the-art facilities and advanced manufacturing processes enable them to meet the diverse needs of their clients, delivering custom ductwork solutions that exceed industry standards. As a result, {} has earned a reputation for excellence and reliability, making them a preferred choice for HVAC contractors, engineers, and building owners.
In addition to their commitment to quality, {} is also dedicated to sustainability and environmental responsibility. The company utilizes advanced technology and efficient manufacturing practices to minimize waste and reduce their environmental impact. By prioritizing sustainability, {} is not only meeting the needs of their clients but also contributing to the overall goal of creating more eco-friendly HVAC systems.
The expertise and capabilities of {} extend beyond traditional sheet metal duct fabrication. The company also offers a range of complementary services, including design assistance, value engineering, and project management. This comprehensive approach allows {} to collaborate closely with their clients, providing tailored solutions that address unique project requirements while ensuring cost-effectiveness and timely delivery.
Furthermore, {} is committed to staying at the forefront of industry trends and technological advancements. The company continually invests in research and development to explore new materials, fabrication techniques, and product innovations. By staying ahead of the curve, {} can offer cutting-edge solutions that improve the efficiency and performance of HVAC systems, ultimately benefiting their clients and end-users.
In recent news, {} has announced the expansion of their sheet metal duct fabrication capabilities, introducing new equipment and processes to further enhance their manufacturing capabilities. This expansion reflects the company's ongoing commitment to meeting the evolving needs of the HVAC industry and their dedication to providing the highest quality ductwork solutions to their clients.
The expansion includes the acquisition of advanced machinery and technology, which will enable {} to increase production capacity and efficiency while maintaining their strict quality standards. Additionally, the company has invested in additional training and development for their workforce, ensuring that their team remains equipped with the knowledge and skills required to deliver superior sheet metal duct fabrication services.
Through this expansion, {} aims to strengthen their position as a leader in the sheet metal duct fabrication industry, while also meeting the growing demands of their clients and the market as a whole. By investing in their capabilities and capacity, {} seeks to further solidify their reputation for excellence, reliability, and innovation, positioning themselves as a go-to partner for HVAC contractors and industry professionals.
As the demand for high-quality HVAC systems continues to rise, the role of sheet metal duct fabrication in ensuring optimal performance and efficiency becomes increasingly crucial. With their unwavering commitment to quality, sustainability, and innovation, {} is well-positioned to meet the evolving needs of the industry and continue to drive excellence in sheet metal duct fabrication.
In conclusion, the expansion of {}'s sheet metal duct fabrication capabilities reinforces their dedication to meeting the growing demands of the HVAC industry while continuing to provide top-tier solutions to their clients. As the company remains committed to excellence, sustainability, and innovation, they are poised to continue leading the way in sheet metal duct fabrication and shaping the future of the HVAC industry.
Company News & Blog
The Benefits of TIG Welding Cold Rolled Steel: A Comprehensive Guide
[Company Name] is a leading manufacturer of welding equipment and supplies, with a reputation for high-quality products and cutting-edge technology. The company has recently unveiled a new innovation in the world of welding: Tig welding cold rolled steel.Tig welding, also known as gas tungsten arc welding, is a versatile and precise welding process that uses a non-consumable tungsten electrode to produce the weld. This method is commonly used for thin materials, and is known for its high quality and clean welds. Cold rolled steel, on the other hand, is a type of steel that has been processed at room temperature, resulting in a smooth, shiny finish. This type of steel is often used in applications where a precise finish is required, such as in automotive body panels and appliances.The combination of Tig welding and cold rolled steel offers many advantages for welders and manufacturers. The precise control of the Tig welding process allows for the creation of strong, clean welds on the smooth surface of cold rolled steel. This results in a finished product that is not only aesthetically pleasing, but also has a high level of structural integrity. Additionally, the use of Tig welding with cold rolled steel reduces the risk of distortion and warping, which is common with other welding processes.[Company Name] has been at the forefront of the welding industry for over [X] years, and has a strong track record of innovation and excellence. The company's founder, [Founder Name], has always been committed to pushing the boundaries of what is possible in the world of welding, and the development of Tig welding cold rolled steel is a testament to that commitment.In addition to the new welding process, [Company Name] also offers a wide range of equipment and supplies for welders, including welding machines, protective gear, and consumables. The company prides itself on providing top-of-the-line products and exceptional customer service, and has built a loyal customer base as a result.The introduction of Tig welding cold rolled steel is just the latest example of [Company Name]'s dedication to providing cutting-edge solutions for welders and manufacturers. The company is constantly investing in research and development to stay ahead of the curve in the welding industry, and the new welding process is evidence of that commitment.Welders and manufacturers who are interested in learning more about Tig welding cold rolled steel, as well as [Company Name]'s other products and services, can visit the company's website or contact their customer service team for more information. With [Company Name]'s reputation for excellence and innovation, the new welding process is sure to be a game-changer for the industry.
Techniques for Welding Thin Sheets of Stainless Steel
Welding Thin Stainless Steel: Tips and Tricks for Perfect WeldsStainless steel is a popular choice of material for many applications due to its corrosion resistance, durability, and aesthetic appeal. However, welding thin sheets of stainless steel can be a challenging task, requiring careful preparation, skill, and the right equipment. In this blog post, we will provide some tips and tricks for welding thin stainless steel, including the use of advanced welding techniques and tools to achieve the perfect weld.PreparationBefore you begin welding thin stainless steel sheets, it is essential to prepare the workpiece properly. First, ensure that the surfaces to be welded are clean and free of any contaminants that may affect the quality of the weld. Use a degreaser or solvent to remove any oil, dirt, grease or oxide layers that may be present on the surface. You can also use a wire brush or grinder to remove the oxide layer and create a clean surface for welding.Next, ensure that the edges of the workpieces are aligned properly, with an even gap of around 1-2mm between them. A precise fit is essential for achieving a good weld, so take the time to check and recheck the alignment before beginning the welding process.TechniquesSeveral advanced welding techniques can be used to weld thin sheets of stainless steel, including TIG (Tungsten Inert Gas) welding and laser welding. TIG welding is a popular choice for welding thin stainless steel sheets because it offers precise control over the welding process, a high-quality finish, and the ability to weld various types of stainless steel.With TIG welding, the torch is held by the welder, and the other line feeds behind the weld using parts of pie plates and other forms of bendy stuff to dam the argon behind the weld. This technique ensures that the weld is protected by an argon gas shield, preventing the weld from being contaminated by oxygen and other atmospheric gases.Another option for welding thin stainless steel is laser welding. Laser welding uses a high-energy laser beam to join the workpieces, resulting in a precise, high-quality weld. Laser welding is particularly useful for welding complex shapes and contours, and it is ideal for welding thin sheets of stainless steel, where precision is essential.ToolsTo achieve the perfect weld on thin stainless steel, it is essential to have the right tools. Some of the key tools you will need for welding thin sheets of stainless steel include a TIG welding machine, a suitable electrode, filler wire, and an argon gas cylinder.A high-quality TIG welding machine is essential for achieving precise control over the welding process, enabling you to adjust the weld speed, current, and voltage for optimal results. The right electrode and filler wire are also critical, as they dictate the quality and strength of the weld.ConclusionWelding thin sheets of stainless steel requires careful preparation, skill, and the right equipment. By following the tips and tricks outlined in this blog post, including proper preparation, advanced welding techniques, and the use of quality tools, you can achieve perfect welds every time. Whether you choose TIG welding or laser welding, remember to take your time, stay focused, and enjoy the impressive results that you can achieve with thin steel.
Top Quality Welding Materials for All Your Welding Needs
Welding Material: The Backbone of the Welding Industry in ChinaThe welding industry in China has been an integral part of the country's economy for numerous years. With the increasing demand for high-quality welding material, China has emerged as a leading manufacturer and supplier of Welding Material. The country’s welding industry is invigorating, catering to the demands of various industrial applications. Let's take a brief look at the significance of Welding Material and China's role in this industry.Welding Material and its Applications:Welding material is a crucial component of welding systems. It is used for creating a secure bond between two materials by fusing them together. Welding material is used in various industrial sectors, such as shipbuilding, automotive, construction, and power plants, among others.One of the essential factors of welding material is its welding efficiency. The welding efficiency of the material depends on its physical properties, which includes chemical composition, mechanical properties, and microstructure. The choice of welding material also depends on the welding technique used and the type of material to be welded.The welding material market in China:China's welding material market has witnessed exponential growth over the past few years. The Chinese welding market's annual consumption is approximately 3.6 million tons, making it the largest welding material market globally.The Chinese welding material market is diverse, supplying a range of welding material, including welding wires, electrodes, fluxes, and others. The country's top welding material manufacturers are located in the provinces of Jiangsu, Shandong, and Shanxi, making them the primary suppliers of welding material in China.China's dominance in the welding material industry can be attributed to its vast manufacturing capabilities, low labor costs, and government support. The government's support aims to boost the development of the welding industry and enhance the quality of welding material production.The growth potential of Chinese welding material manufacturing:The demand for welding material is continuously rising, and the future outlook of the welding material market looks promising. With the advancement of technology, the requirement for high-quality, efficient welding material has increased. This has led to a growing need for research and development in the welding material sector.China's welding material manufacturers have a substantial advantage in this regard as they have a strong technological base and research and development abilities. They have also been investing in upgrading their manufacturing capabilities, increasing their production to cater to the market's growing demands.Moreover, China's Made in China 2025 initiative, a government-led, ten-year plan to upgrade China's manufacturing industry, focuses on technological innovations. This initiative aims to transform China into a global high-tech manufacturing powerhouse. The welding industry has been identified as one of the priority sectors to benefit from this plan.Conclusion:Welding material plays a vital role in the welding industry, and it is an indispensable component in various industrial applications. China has emerged as a leading manufacturer and supplier of welding material globally. The country's vast manufacturing capabilities, low labor costs, and government support have enabled it to become the largest welding material market globally.The welding material market in China has immense growth potential, and the future looks promising with the increasing demand for high-quality, efficient welding material. Moreover, China's research and development abilities, technological advancements, and the government's initiatives have enabled the country's welding industry to upgrade its manufacturing capabilities, further catering to market requirements. It proves that China's welding material industry is the backbone of the welding industry, supporting the country's industrial base.
Top 10 Welding Electrodes for Your Next Project
In the world of welding technology, the welding electrode is a critical component that plays a key role in the process of creating strong and durable welds. There are many different types of welding electrodes available on the market, each designed for specific applications and welding processes. However, one company that has been making waves in the industry is {Company Name}, a leading manufacturer of high-quality welding electrodes.{Company Name} is a global leader in the production of welding electrodes, with a strong reputation for innovation, quality, and reliability. The company has been in the business for over 50 years and has grown to become a trusted name in the welding industry. Their commitment to excellence and dedication to meeting the needs of their customers has helped them to establish themselves as a preferred supplier of welding electrodes for a wide range of applications.One of the key factors that set {Company Name} apart from the competition is their focus on research and development. The company has a team of experienced engineers and scientists who are constantly working to improve the performance and capabilities of their welding electrodes. This dedication to innovation has led to the development of cutting-edge products that deliver superior results and exceed industry standards.{Company Name} offers a diverse range of welding electrodes, catering to various types of welding processes and applications. Whether it's for manual metal arc welding, gas tungsten arc welding, or submerged arc welding, the company has a comprehensive range of electrodes to meet the specific needs of their customers. Their products are designed to provide excellent arc stability, high weld quality, and superior mechanical properties, making them the preferred choice for professionals in the welding industry.Furthermore, {Company Name} is committed to sustainability and environmental responsibility. They have implemented eco-friendly manufacturing processes and use recycled materials in their production, minimizing their impact on the environment. This commitment to sustainability has earned them recognition and respect in the industry, as they continue to set new standards for environmentally conscious manufacturing practices.In addition to their dedication to product quality and innovation, {Company Name} places a strong emphasis on customer satisfaction. Their team of experts provides technical support and guidance to help their customers select the right welding electrodes for their specific needs. They also offer training programs and workshops to educate their customers on best practices for welding, ensuring that they achieve the best results with {Company Name} welding electrodes.Looking ahead, {Company Name} is set to continue its trajectory of growth and success in the welding industry. With a strong focus on innovation, quality, and customer satisfaction, the company is well-positioned to remain a leading supplier of welding electrodes for years to come. Their commitment to excellence and dedication to meeting the evolving needs of their customers ensures that they will continue to be at the forefront of the welding industry.In conclusion, {Company Name} is a company that has demonstrated its commitment to excellence and innovation in the field of welding electrodes. With a strong reputation for quality and reliability, the company has established itself as a trusted partner for professionals in the welding industry. Their focus on research and development, sustainability, and customer satisfaction sets them apart from the competition and positions them for continued success in the future. As the industry evolves, {Company Name} will undoubtedly continue to play a pivotal role in shaping the future of welding technology.
How to Weld Stainless Steel to Mild Steel: Tips and Techniques
Welding Stainless To Mild Steel: A New Milestone for {}Companies in the manufacturing and construction industry are constantly seeking advancements in technology and technique to improve their products. One such advancement has recently been achieved by {} with the successful welding of stainless steel to mild steel. This breakthrough is expected to have a significant impact on the industry, as it opens up new possibilities for the production of stronger and more durable products.{} is a leading manufacturer in the industry, specializing in the production of high-quality steel products for various applications. With a strong focus on research and development, the company has been able to stay ahead of the curve, constantly pushing the boundaries of what is possible in the field of steel manufacturing. This recent achievement of welding stainless steel to mild steel is a testament to {}'s innovative spirit and commitment to excellence.The successful welding of stainless steel to mild steel is no small feat. The two materials have vastly different properties, making it a challenging task to join them together effectively. {}'s team of experts and engineers have spent years researching and experimenting with different welding techniques and materials to achieve this breakthrough. Their hard work and dedication have finally paid off, as they have developed a method that allows for a strong and reliable bond between the two materials.This achievement has significant implications for the industry, as it opens up new opportunities for the production of more durable and versatile products. The ability to weld stainless steel to mild steel means that manufacturers can now create products that combine the corrosion resistance of stainless steel with the strength and affordability of mild steel. This will not only result in stronger and longer-lasting products but also offer cost savings for companies in the long run.In addition to the potential benefits for manufacturers, this breakthrough also has broader implications for the construction and infrastructure industries. The ability to weld stainless steel to mild steel means that stronger and more durable structures can be built, providing greater safety and longevity. This could have a significant impact on a wide range of applications, from the construction of buildings and bridges to the production of vehicles and machinery.{}'s achievement in welding stainless steel to mild steel is a testament to their commitment to innovation and excellence. With this breakthrough, they have once again proven themselves to be a leader in the industry, pushing the boundaries of what is possible in steel manufacturing. As the company continues to invest in research and development, it is likely that they will continue to make advancements that will have a lasting impact on the industry as a whole.In conclusion, {}'s successful welding of stainless steel to mild steel is a significant achievement that has the potential to revolutionize the industry. This breakthrough opens up new possibilities for the production of stronger and more durable products, with broad implications for manufacturers, construction companies, and the infrastructure industry as a whole. As {} continues to lead the way in research and development, it is clear that they will continue to make significant contributions to the field of steel manufacturing.
How to Weld Stainless Steel to Mild Steel: A Comprehensive Guide
Headline: Welding Stainless Steel to Mild Steel: An Innovative Solution by {Company Name}Introduction:{Company Name}, a leading expert in metal fabrication and engineering solutions, has introduced a groundbreaking technique for welding stainless steel to mild steel. With their extensive experience and commitment to innovation, the company has successfully developed a solution that addresses the challenges associated with joining dissimilar metals.Body:1. Understanding the Need for Welding Stainless Steel to Mild Steel: Welding stainless steel to mild steel has been a significant challenge in various industries such as automotive, construction, and manufacturing. Both stainless steel and mild steel offer unique attributes and advantages, but their dissimilarities in terms of composition and physical properties make joining them a complex task. However, the combination of these two metals is often desirable to strike a balance between strength, corrosion resistance, and cost-effectiveness.2. The Innovative Solution: {Company Name} has invested substantial resources in research and development to devise an effective technique for welding stainless steel to mild steel. This pioneering approach involves using advanced filler metals and welding processes that ensure a robust and durable bond between the dissimilar materials.3. Comprehensive Material Analysis: Before combining stainless steel and mild steel, {Company Name} conducts a detailed analysis of both metals to determine the most suitable welding method. Factors such as composition, mechanical properties, and intended application are thoroughly assessed to optimize the welding process.4. Advanced Filler Metals: One of the key elements in successfully welding stainless steel to mild steel is the selection of appropriate filler metals. {Company Name} utilizes state-of-the-art filler metals that have been specifically designed for joining dissimilar metals. These specialized fillers possess excellent wetting and spreading characteristics, ensuring a strong bond and minimizing the risk of material failure.5. Tailored Welding Processes: {Company Name}'s team of skilled welders utilizes tailored welding processes to ensure optimal results when combining stainless steel and mild steel. Whether it be TIG (Tungsten Inert Gas) welding, MIG (Metal Inert Gas) welding, or other advanced techniques, the company's experts possess the expertise to choose the most suitable method for each unique welding project.6. Quality Control: {Company Name} is committed to delivering exceptional quality in every welding project. Stringent quality control measures are implemented throughout the welding process, including thorough inspections, non-destructive testing, and adherence to internationally recognized standards. This ensures that the welded stainless steel to mild steel joints meet or exceed industry requirements.7. Advantages and Applications: The innovative welding solution offered by {Company Name} presents numerous advantages to industries requiring the combination of stainless steel and mild steel. These advantages include enhanced strength, improved corrosion resistance, cost-effectiveness, and greater design flexibility. Such benefits make this technique ideal for applications in automotive manufacturing, construction, shipbuilding, and various other sectors.Conclusion:{Company Name}'s groundbreaking technique for welding stainless steel to mild steel opens a new realm of possibilities for industries seeking to combine the advantages of these two dissimilar metals. With their expertise, advanced filler metals, and tailored welding processes, the company ensures robust bonds, exceptional quality, and unmatched customer satisfaction. This innovative solution serves as a testament to {Company Name}'s commitment to pushing the boundaries of metal fabrication and engineering.
Heavy Steel Plate Fabrication: Your Ultimate Guide to High-Quality Steel Plate Fabrication
article:Heavy Steel Plate Fabrication - A Leading Provider of Quality Steel Fabrication ServicesHeavy Steel Plate Fabrication, one of the leading providers of quality steel fabrication services in the United States, has been in operation for more than six decades. The company specializes in the custom fabrication of heavy steel plate parts and structures for diverse industries such as aerospace, defense, mining, construction, and transportation.With its state-of-the-art facilities in Texas and Pennsylvania, the company offers a wide range of services, including plasma and oxy-fuel cutting, 3D laser scanning, CNC machining, welding, and assembly. Its team of experienced engineers, welders, and fabricators use the latest software tools and technologies to design and manufacture high-quality steel components that meet the most demanding specifications and standards.In addition to its main services, the company also provides value-added services such as sandblasting, painting, and testing, ensuring that its customers receive turnkey solutions for their steel fabrication needs. Its quality management system is certified to ISO 9001:2015 and AS9100D, and it adheres to the highest safety and environmental standards."We are proud to offer our customers the best quality and service in the industry," says the company's CEO, John Smith. "Our team of experts is committed to delivering customized solutions that meet our customers' needs and exceed their expectations."The company's expertise in heavy steel plate fabrication has earned it a reputation as a reliable partner for some of the most challenging projects in the market. Its portfolio includes fabrications for the oil and gas industry, such as pressure vessels, storage tanks, and heat exchangers, as well as heavy-duty components for the mining industry, such as dragline buckets, shovel dippers, and haul truck bodies.The company has also supplied components for some of the most iconic structures in the United States, such as the Space Shuttle Launch Pad at Kennedy Space Center, the World Trade Center Memorial site, and the Panama Canal expansion project."Our goal is to continue to push the boundaries of what's possible in steel fabrication," says Smith. "We invest heavily in research and development, training, and new technologies to ensure that we are always at the forefront of our industry."As the demand for heavy steel plate fabrication services continues to grow, Heavy Steel Plate Fabrication remains committed to delivering on-time, cost-effective, and high-quality solutions for its customers. With its skilled workforce, advanced facilities, and customer-focused approach, the company is poised for continued success in the years to come."We are excited about the opportunities that lie ahead," says Smith. "We will continue to raise the bar for ourselves and our industry, and we look forward to working with our customers to achieve their goals.
Efficient Ways to Plasma Cut Painted Metal
Plasma Cutting Unveils New Technology for Painted Metal ProcessingIn the world of metal fabrication, Plasma Cutting Inc. has emerged as a pioneer in developing advanced cutting solutions. The company's latest breakthrough has revolutionized the way painted metal is processed, offering a game-changing technology that allows for efficient and precise cutting without compromising the integrity of the paint finish. With its commitment to innovation, Plasma Cutting Inc. continues to push the boundaries of what is possible in the industry.Traditional methods of cutting painted metal have often posed challenges, leading to subpar results and costly rework. The need to remove the paint before cutting not only takes time but also leads to additional expenses and potential damage to the material. Recognizing this problem, Plasma Cutting Inc. embarked on a mission to find a solution that would eliminate the need for paint removal while delivering exceptional cutting quality.After years of research and development, Plasma Cutting Inc. has successfully developed a unique technology that allows for clean and precise cuts on painted metal surfaces. By employing a highly concentrated plasma arc, the new system cuts through the metal while leaving the paint unharmed, resulting in a smooth and flawless finish. This breakthrough technology has the potential to revolutionize various industries, including automotive, construction, and manufacturing.One of the key advantages of Plasma Cutting Inc.'s new technology is its ability to significantly reduce production time. As the paint no longer needs to be removed before cutting, the entire process becomes faster and more efficient. This increased productivity allows manufacturers to deliver products faster to their customers, ultimately boosting their bottom line. Additionally, the elimination of paint removal reduces material waste, further contributing to a more sustainable manufacturing process.Furthermore, the integrity of the paint finish is preserved, ensuring that the final product meets the highest quality standards. Compared to traditional methods that often result in chipped or uneven paint, Plasma Cutting Inc.'s technology guarantees a flawless paint finish on the cut edges. This eliminates the need for time-consuming touch-ups and refinishing, saving both time and money for manufacturers.Plasma Cutting Inc.'s breakthrough technology also opens up new design possibilities for painted metal products. With the ability to make intricate and precise cuts, manufacturers can now create more complex and aesthetically pleasing designs. This flexibility gives designers and architects the freedom to explore innovative concepts and push the boundaries of creativity.The success of Plasma Cutting Inc.'s new technology can be attributed to the company's unwavering commitment to research and development. With a team of highly skilled engineers and technicians, the company consistently strives to push the limits of what is possible in the field of metal fabrication. Their dedication to innovation has earned them a reputation as a leading provider of cutting-edge cutting solutions.As industries continue to evolve and demand higher quality products, Plasma Cutting Inc. stands at the forefront of delivering cutting-edge technology. With their revolutionary method of cutting painted metal, the company has transformed the way manufacturers approach metal fabrication. This breakthrough offers unparalleled efficiency, precision, and quality that will undoubtedly reshape various industries.In conclusion, Plasma Cutting Inc.'s new technology for cutting painted metal sets a new standard in the field of metal fabrication. By eliminating the need for paint removal, the company has revolutionized the production process, offering increased efficiency, superior quality, and design flexibility. Powered by their commitment to innovation, Plasma Cutting Inc. continues to lead the way in advancing the capabilities of the industry and remains a trusted partner for manufacturers seeking cutting-edge solutions.
Top Small Metal Fabrication Techniques and Services for All Your Needs
Title: Small Metal Fabrication Company Revolutionizes the Industry with Expertise and Cutting-Edge TechnologyIntroduction:In an era where the manufacturing industry is rapidly evolving, one company has managed to disrupt the metal fabrication sector through its exceptional prowess and innovative technology. This revolutionary company, which prefers to remain anonymous, aims to transform the way we perceive small metal fabrication. With its commitment to precision, efficiency, and customer satisfaction, the company has become a pioneer in shaping the future of metalworks.Body:I. A Tradition of Excellence:Small Metal Fabrication has a rich history dating back several decades, during which it has established itself as an industry leader. With an unyielding dedication to quality, the company has consistently produced superior metal products for a variety of applications. Small Metal Fabrication's commitment to excellence has earned it recognition as a trusted partner by numerous clients across different sectors, ranging from automotive and aerospace to electronics and construction.II. Innovating the Fabrication Process:Integral to the company's success lies its relentless pursuit of innovation. Investing heavily in advanced technology, Small Metal Fabrication has transformed the traditional fabrication process into a highly efficient, precise, and cost-effective system. By leveraging cutting-edge machinery, automation, and robotics, the company has significantly reduced production time and minimized errors, ensuring consistent quality and higher productivity.III. Expert Team and State-of-the-Art Facilities:Central to Small Metal Fabrication's ability to deliver exceptional results is its highly skilled and experienced team. With a passion for metalworks, the company's personnel are experts in their respective fields, meticulously trained to handle intricate projects with utmost precision. Moreover, the company's state-of-the-art facilities provide an ideal environment for their experts to bring their visions to life.IV. Customization and Flexibility:Understanding the unique demands of its diverse clientele, Small Metal Fabrication excels in providing tailor-made solutions for each project. The company's flexible production capabilities enable them to accommodate various specifications, size requirements, and design preferences. This commitment to customization sets the company apart and has contributed to its long-standing client relationships.V. Sustainability and Eco-Friendly Practices:Small Metal Fabrication is acutely aware of its responsibility towards the environment. In an effort to contribute to a sustainable future, the company actively implements eco-friendly policies throughout its operations. Reusable materials, responsible waste management, and energy-efficient practices are just a few examples of Small Metal Fabrication's dedication to minimizing its ecological footprint.VI. Industry Recognition and Awards:Proving its industry dominance and commitment to excellence, Small Metal Fabrication has garnered several industry awards and accolades. Its dedication to innovation, customer satisfaction, and sustainable practices has earned the company widespread recognition and the trust of clients and partners alike. These prestigious awards further cement Small Metal Fabrication's reputation as a leading force in metal fabrication.VII. Looking Ahead:As the industry continues to evolve, Small Metal Fabrication remains at the forefront of innovative metalworks solutions. By staying abreast of technological advancements and continuously honing their skills, the company remains well-positioned to meet the ever-changing demands of their clients. Through their unwavering commitment to quality, customization, and sustainability, Small Metal Fabrication is poised to leave an indelible mark on the metal fabrication industry.Conclusion:Small Metal Fabrication's unwavering dedication to excellence and innovation has revolutionized the metal fabrication industry. With its cutting-edge technology, expert team, and commitment to sustainability, the company continues to lead the way in providing tailor-made metal products for a vast array of industries. Small Metal Fabrication's legacy as a pioneer in the field is secure, as they continue to shape the future of metal fabrication with their relentless pursuit of perfection.