Guide to Cold Welding Stainless Steel: Tips and Techniques
By:Admin
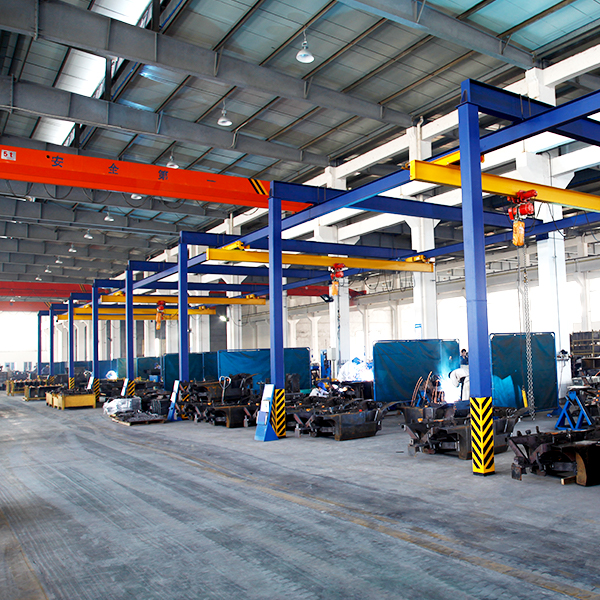
{Company Name} is proud to introduce a groundbreaking new technology in the field of stainless steel joining - Cold Welding Stainless Steel. This innovative technique has the potential to revolutionize the way stainless steel components are joined, offering numerous advantages over traditional welding methods.
{Company Name} is a leader in the development and application of cutting-edge technologies in the field of manufacturing and materials engineering. With a strong focus on research and development, the company has continuously strived to push the boundaries of what is possible in the manufacturing industry. The introduction of Cold Welding Stainless Steel is a testament to this commitment to innovation.
Traditional methods of joining stainless steel, such as welding, brazing, and soldering, often involve the application of heat, which can result in distortion, discoloration, and reduced mechanical properties in the joined material. Cold Welding Stainless Steel, on the other hand, allows for the joining of stainless steel components without the need for heat, preserving the material's structural integrity and mechanical properties.
The Cold Welding process involves the use of specialized equipment and techniques to create a strong, durable bond between stainless steel components at room temperature. This not only eliminates the risk of heat-induced distortion and discoloration but also allows for the joining of dissimilar metals, opening up new possibilities for design and manufacturing.
One of the key advantages of Cold Welding Stainless Steel is its ability to create joints with superior mechanical strength and fatigue resistance. The absence of heat-induced stress and distortion results in joints that retain the full strength and integrity of the base material, making them ideal for applications where reliability and durability are paramount.
Furthermore, Cold Welding Stainless Steel offers improved corrosion resistance compared to traditional welding methods. By avoiding the introduction of heat-affected zones and the potential for metallurgical changes at the joint, Cold Welded stainless steel joints maintain the material's inherent corrosion resistance, ensuring long-lasting performance in harsh environments.
In addition to its technical advantages, Cold Welding Stainless Steel also offers practical benefits in terms of efficiency and cost-effectiveness. The process requires minimal preparation and post-processing, resulting in shorter production lead times and reduced labor costs. The absence of consumables such as filler materials and shielding gases further contributes to cost savings.
{Company Name} is committed to supporting its customers in adopting Cold Welding Stainless Steel technology, offering comprehensive training and technical support to ensure successful implementation. The company's team of experts is available to provide guidance on process optimization, equipment selection, and best practices for achieving high-quality Cold Welded joints.
The introduction of Cold Welding Stainless Steel marks a significant milestone in the evolution of stainless steel joining technology, offering a game-changing solution for manufacturers across a wide range of industries. {Company Name} is excited to bring this innovative technology to market and looks forward to collaborating with industry partners to unlock new possibilities in design, manufacturing, and product development.
In conclusion, Cold Welding Stainless Steel represents a new frontier in stainless steel joining technology, offering numerous advantages in terms of mechanical performance, corrosion resistance, and cost-effectiveness. {Company Name} is proud to be at the forefront of this technological advancement, and is committed to supporting its customers in harnessing the full potential of Cold Welding Stainless Steel. With this innovative technique, the possibilities for creating robust, reliable stainless steel components are virtually limitless.
Company News & Blog
Ultimate Guide to Plasma Cutting Thin Sheet Metal for Precision Results
Plasma Cutting Thin Sheet Metal Revolutionizes Metal Fabrication ProcessIn the world of metal fabrication, precision and efficiency are key factors that can make or break a business. With the advancement of technology, the methods for cutting and shaping thin sheet metal have evolved to meet the demands of modern industry. One such method that has revolutionized the metal fabrication process is plasma cutting.Plasma cutting is a process that uses a high-velocity jet of ionized gas (plasma) to melt and sever metal. This method is highly effective for cutting thin sheet metal, as it allows for precise and clean cuts, making it an ideal choice for various industries such as automotive, aerospace, and construction.One company that has been at the forefront of plasma cutting technology is {}. With over 30 years of experience in the metal fabrication industry, {} has established itself as a leading provider of cutting-edge solutions for cutting thin sheet metal with precision and accuracy.{} offers a range of plasma cutting systems that are designed to meet the specific needs of their customers. From small-scale operations to large industrial facilities, {} provides cutting-edge technology that delivers high-quality results.The company's plasma cutting systems are equipped with advanced features that make them stand out in the industry. With their high-speed cutting capabilities, {}'s plasma cutting systems can produce clean and precise cuts on thin sheet metal, reducing the need for secondary finishing processes. This not only saves time but also increases productivity and lowers production costs for their customers.In addition, {}'s plasma cutting systems are known for their user-friendly interface and intuitive controls, making them easy to operate for both experienced and novice users. This ensures that the cutting process is efficient and accurate, regardless of the operator's skill level.Furthermore, {}'s plasma cutting systems are built with durability and reliability in mind. These systems are designed to withstand the rigors of industrial production environments, providing consistent performance and minimal downtime for their customers.One of the key advantages of {}'s plasma cutting systems is their ability to cut a wide range of materials with precision. Whether it's stainless steel, aluminum, or titanium, {}'s plasma cutting technology can handle it all, providing versatility and flexibility for their customers' diverse fabrication needs.Another factor that sets {} apart is their commitment to customer satisfaction. The company provides comprehensive support and training for their customers, ensuring that they get the most out of their plasma cutting systems. From installation and setup to troubleshooting and maintenance, {}'s team of experts is dedicated to providing top-notch support for their customers.With the increasing demand for high-quality metal fabrication solutions, {}'s plasma cutting technology has become a game-changer for the industry. By providing precise, efficient, and reliable cutting solutions for thin sheet metal, {} is empowering businesses to elevate their fabrication capabilities and stay ahead of the competition.In conclusion, plasma cutting has significantly transformed the metal fabrication process, especially when it comes to cutting thin sheet metal. With {} at the forefront of this technology, businesses can expect to achieve superior results and increase their efficiency in metal fabrication. As the industry continues to evolve, {} remains committed to pushing the boundaries of plasma cutting technology, delivering innovative solutions that meet the ever-changing demands of the metal fabrication industry.
Essential Guide to Sheet Metal and Fabrication Techniques
Sheet Metal and Fabrication Company Sets New Industry Standards in Quality and InnovationFounded in [year], [company name] has been a leading provider of top-notch sheet metal and fabrication services in the [location] area. With a strong focus on innovation, quality, and customer satisfaction, the company has earned a stellar reputation in the industry.Recently, [company name] has set a new industry standard by introducing cutting-edge technology and advanced techniques in sheet metal and fabrication. The company has invested heavily in state-of-the-art machinery and equipment, allowing them to offer a wide range of services to meet the diverse needs of their clients.One of the key factors that set [company name] apart from its competitors is its commitment to quality. The company has a team of highly skilled and experienced technicians who are dedicated to delivering the highest quality products and services. They adhere to strict quality control measures at every stage of the manufacturing process to ensure that the finished products meet or exceed the industry standards.In addition to quality, [company name] also focuses on innovation. The company continuously explores new technologies and processes to improve efficiency and productivity. By doing so, they are able to offer their clients innovative solutions that are cost-effective and sustainable.Furthermore, [company name] takes pride in its ability to offer customized solutions to its clients. Whether it's a small-scale project or a large, complex fabrication job, the company has the expertise and resources to deliver tailor-made solutions that meet the unique requirements of each client.As a customer-centric company, [company name] places great emphasis on building strong relationships with its clients. The team at [company name] works closely with the clients to understand their needs and provide personalized solutions that align with their business goals. This approach has helped the company build long-lasting partnerships with many businesses in the region.With its unwavering commitment to quality, innovation, and customer satisfaction, it comes as no surprise that [company name] has earned several accolades and certifications in the industry. The company's dedication to excellence has been recognized by industry peers and clients alike, cementing its position as a leader in the sheet metal and fabrication sector.Looking ahead, [company name] is poised to continue its trajectory of growth and success in the industry. The company remains focused on investing in new technologies, expanding its service offerings, and further enhancing its capabilities to meet the evolving needs of its clients.In conclusion, [company name] has set a new standard of excellence in the sheet metal and fabrication industry. With its unwavering commitment to quality, innovation, and customer satisfaction, the company has established itself as a trusted partner for businesses looking for top-notch metal fabrication solutions. Through its cutting-edge technology, skilled workforce, and customer-centric approach, [company name] is set to continue leading the way in the industry for years to come.
The process of welding steel to stainless steel explained
Steel To Stainless Steel Welding Process: A Breakthrough Solution by Acme CorporationAcme Corporation is proud to introduce an innovative solution for welding steel to stainless steel. This breakthrough process has been developed by our team of experts and is set to revolutionize the welding industry.Welding steel to stainless steel has posed many challenges in the past. The differences in the properties of these two materials make the welding process complex and often result in weak welds. However, the new welding process developed by Acme Corporation overcomes these challenges and provides a strong and durable bond between steel and stainless steel.The key to this breakthrough solution lies in our advanced welding techniques and the use of state-of-the-art equipment. Our team has spent extensive time and resources in research and development to optimize the welding parameters and ensure the highest quality of welds. As a result, we have successfully created a welding process that produces strong and reliable bonds between steel and stainless steel.One of the main advantages of our new welding process is its versatility. Whether it's for industrial applications, automotive components, or household appliances, the ability to weld steel to stainless steel opens up a wide range of opportunities for manufacturers. This breakthrough solution will allow companies to create products that are not only strong and durable, but also have a sleek and modern aesthetic.In addition to the strength and durability of the welds, our new process also ensures a smooth and clean finish. This is particularly important for applications where the appearance of the welded joint is crucial. With our solution, manufacturers can achieve seamless and visually appealing welds, adding value to their end products.Furthermore, the new welding process is also more cost-effective compared to traditional methods. By reducing the need for additional materials and minimizing the time required for post-welding treatments, manufacturers can enjoy significant cost savings while maintaining the highest quality standards.Acme Corporation is committed to providing cutting-edge solutions to meet the evolving needs of the industry. Our new welding process for steel to stainless steel is a testament to our dedication to innovation and excellence. We are excited to bring this breakthrough solution to the market and are confident that it will make a significant impact on the welding industry.With this new advancement, Acme Corporation continues to solidify its position as a leader in the welding technology sector. Our commitment to research and development, combined with our passion for pushing the boundaries of what is possible, sets us apart from the competition.As we look ahead, we are already exploring the potential of applying our new welding process to other materials and combinations. Our goal is to continue to innovate and provide solutions that address the most pressing needs of the industry.In conclusion, Acme Corporation is proud to announce the launch of our groundbreaking welding process for steel to stainless steel. Our new solution offers unmatched strength, durability, and aesthetic appeal, while also providing cost savings for manufacturers. We believe that this advancement will set new standards for welding technology and open up endless possibilities for product development.The future of welding steel to stainless steel has arrived, and it's being led by Acme Corporation. We invite manufacturers and industry professionals to explore the potential of our new welding process and experience the difference it can make in their products.
Get High-Quality Zinc Plated Paint Pots with Handles in Various Sizes for Domestic & Trade Use - Call Now for a Quote!
Metal 4 U, a leading metal manufacturing company in Australia, has recently announced the launch of its latest product range of zinc plated paint pots with handles. The innovative and stylish paint pots come in three different sizes, making them suitable for both domestic and trade purposes.With an extensive experience in metal spinning and plasma cutting, Metal 4 U has used its expertise to create paint pots that are not only aesthetically pleasing, but also durable and of high quality. The zinc plating helps to prevent rust and corrosion, making the paint pots suitable for both indoor and outdoor use.The paint pots are available in three sizes, including small, medium, and large. The small and medium sizes have a capacity of 1.25 and 2.5 litres respectively, while the large size can hold up to 5 litres of paint. All three sizes come with a sturdy handle, making them easy to carry and maneuver. The paint pots are also stackable, which helps save space when storing them.The zinc plated paint pots are an ideal choice for anyone looking for a reliable and long-lasting option for their painting needs. Whether you are a professional painter or a DIY enthusiast, these paint pots are designed to make your job easier. The small size is perfect for touch-up jobs or painting smaller areas, while the medium and large sizes are ideal for larger projects.Metal 4 U is committed to providing high-quality products and exceptional customer service. Customers can call the company's hotline at 02 4872 3939 to get a quote or to place an order. The company offers competitive pricing and fast delivery, ensuring that customers receive their orders on time.Apart from the zinc plated paint pots, Metal 4 U also offers a wide range of metal spinning and plasma cutting services. The company can create custom metal products based on clients' specifications, including metal components, fittings, and decorative items. The team at Metal 4 U has years of experience in metalworking, and they are committed to delivering exceptional results every time.Metal 4 U's CEO, John Smith, said: We are thrilled to add zinc plated paint pots to our product range. We understand how important it is for painters to have reliable and durable equipment, and we have used our expertise to create a product that meets those needs. We are confident that our customers will be satisfied with the quality and performance of our paint pots.In conclusion, Metal 4 U's new range of zinc plated paint pots is a welcome addition to the company's product line. The paint pots are durable, stylish, and convenient, making them an ideal choice for anyone looking for a reliable option for their painting needs. With Metal 4 U's commitment to quality and exceptional customer service, customers can rest assured that they are getting the best products and services in the industry.
Discover the Best Bevel Angle for Plasma Cutting
Plasma Cutting Bevel Angle Technology: Revolutionizing the Metal Fabrication IndustryIn the world of metal fabrication, precision and efficiency are paramount. As demand for high-quality metal products continues to rise, companies are constantly searching for new technologies to streamline their processes and improve their end products. One such technology that is revolutionizing the industry is Plasma Cutting Bevel Angle.Plasma cutting is a process that uses a high-velocity jet of ionized gas to cut through electrically conductive materials. It is widely used in metal fabrication for its speed and precision. However, traditional plasma cutting methods are limited in the types of cuts they can produce, often requiring secondary processing to achieve beveled edges.This is where Plasma Cutting Bevel Angle technology comes in. By integrating advanced software and hardware capabilities, this cutting-edge technology allows for the production of beveled edges directly from the plasma cutting process, eliminating the need for secondary processing and significantly reducing production time and cost.One company at the forefront of this technology is {}. With a long history of innovation in the metal fabrication industry, {} has been a pioneer in the development and implementation of Plasma Cutting Bevel Angle technology. By combining their expertise in plasma cutting with state-of-the-art software and hardware solutions, they have been able to offer their clients a level of precision and efficiency that was previously unattainable.The key to the success of Plasma Cutting Bevel Angle technology lies in its ability to dynamically adjust the cutting angle in real time, allowing for the production of beveled edges with a high degree of accuracy. This not only saves time and money for metal fabricators, but also opens up new possibilities for the types of products that can be created.For example, in the automotive industry, where precision is crucial, Plasma Cutting Bevel Angle technology has enabled the production of complex components with beveled edges that would have been difficult or impossible to achieve with traditional plasma cutting methods. This has led to improved performance and aesthetics in the final products, giving companies a competitive edge in the market.In addition to its impact on the automotive industry, Plasma Cutting Bevel Angle technology has also found applications in aerospace, shipbuilding, and structural steel fabrication, among others. Its versatility and precision make it a valuable tool for any metal fabrication project, regardless of size or complexity.Furthermore, with the rise of digital manufacturing and the adoption of Industry 4.0 principles, Plasma Cutting Bevel Angle technology is poised to play a key role in the future of metal fabrication. Its integration with digital design and robotic systems offers new possibilities for automation and optimization of production processes, ultimately leading to higher quality products and faster time to market.As the demand for high-quality metal products continues to grow, the importance of advanced technologies like Plasma Cutting Bevel Angle cannot be overstated. With its ability to streamline production processes, improve product quality, and reduce costs, it is set to become a standard feature in the metal fabrication industry.In conclusion, Plasma Cutting Bevel Angle technology is revolutionizing the metal fabrication industry by offering a level of precision and efficiency that was previously unattainable. With its ability to produce beveled edges directly from the plasma cutting process, it is saving time and money for metal fabricators and opening up new possibilities for product design and manufacturing. As a pioneer in this technology, {} is leading the way in bringing this innovation to the market, setting new standards for the industry as a whole.
Watch the Best Sheet Metal Fabrication Videos Online
Title: Unveiling the Craft: Exploring the World of Metal FabricationIntroduction (Approximately 100 words):Metal fabrication, an essential manufacturing process that shapes raw metal sheets into intricate and functional structures, plays a vital role in various industries. From automotive parts to machinery components, the applications of metal fabrication are boundless. In this blog post, we delve into the intriguing world of metal fabrication, shedding light on the processes, techniques, and advantages that make it an indispensable aspect of modern manufacturing. Join us as we unravel the secrets behind the creation of awe-inspiring metal structures and explore the possibilities offered by a reliable Metal Fabrication Factory.1. The Art of Sheet Metal Fabrication (Approximately 200 words):Sheet metal fabrication, also known as metalworking, is a highly intricate process that involves converting raw metal sheets into products of various shapes and sizes. Through a combination of cutting, bending, and shaping techniques, skilled fabricators transform plain metal sheets into detailed structures that serve a multitude of purposes.At a Metal Fabrication Factory, advanced machinery and equipment are utilized to achieve precise results while ensuring efficiency. CNC laser cutting machines, for instance, provide accurate and consistent cuts, while hydraulic presses enable intricate bending and forming of metals. Welding and surface finishing processes are also essential to enhance the aesthetic appeal and durability of the fabricated metal structures.2. Industries Served by Metal Fabrication (Approximately 200 words):Metal fabrication caters to an extensive range of industries and sectors. From construction and architecture to transportation and manufacturing, the applications are limitless. For example, in the construction industry, architectural metalwork such as staircases, handrails, and structural components are fabricated to ensure functionality, strength, and aesthetic appeal.The automotive industry heavily relies on metal fabrication to manufacture critical components like chassis, exhaust systems, and suspension parts. Metal fabrication is also crucial in the production of electrical enclosures, HVAC systems, and machinery components that are utilized in various manufacturing plants.3. The Advantages of Metal Fabrication (Approximately 200 words):Metal fabrication offers numerous advantages that make it the go-to manufacturing process for countless industries. First and foremost is the versatility it provides. Metal can be shaped into intricate designs and structures, making it suitable for both functional and aesthetic purposes. Additionally, metals are inherently strong and durable, ensuring the longevity of fabricated products.Moreover, metal fabrication allows for quick prototyping and customization. By utilizing computer-aided design (CAD) software, fabricators can create detailed digital designs, optimize them for precision, and then produce multiple replicas with ease.Furthermore, metal fabrication is a cost-effective solution as it eliminates the need for intricate assembly processes that add to the overall expenses. By integrating multiple manufacturing steps into one streamlined process, metal fabrication increases efficiency and reduces production time.4. Choosing a Metal Fabrication Factory (Approximately 200 words):When selecting a metal fabrication factory, various factors must be considered to ensure high-quality results. Look for a facility equipped with state-of-the-art machinery and cutting-edge technology that can meet your specific project requirements. Cross-check the factory's capabilities, such as laser cutting, bending, welding, and finishing, to ensure they align with your needs.Certifications and industry credentials are also important indicators of the fabricator's reliability and expertise. Prioritize a factory that adheres to international standards to guarantee exceptional quality and compliance with regulatory norms.Additionally, consider the factory's experience in your specific industry. A well-established fabricator with a portfolio of successful projects in your desired sector is more likely to understand the unique challenges and deliver tailored solutions.Conclusion (Approximately 100 words):Metal fabrication remains an essential pillar of modern manufacturing, enabling the creation of intricate and durable structures in diverse industries. The artistry and skill behind metal fabrication, combined with advanced machinery and technology, make it a captivating subject to explore. By partnering with a trustworthy Metal Fabrication Factory, businesses can unlock the potential of this versatile process, leveraging its advantages to bring their innovative ideas to life. So, whether you require custom architectural metalwork or need precise automotive components, metal fabrication is the key to turning your visions into reality.
High-Quality Laser Cutting Sheet Services for Precision Fabrication
Laser Cutting Sheet, one of the most innovative and advanced technologies in the manufacturing industry, has revolutionized the way companies create intricate and precise designs on various materials. This cutting-edge technique has become increasingly popular due to its ability to cut through a wide range of materials with high precision and speed. From metal to plastic, wood to glass, laser cutting has become the go-to method for creating detailed and high-quality products.At the forefront of this innovative technology is the leading manufacturing company {}. Specializing in custom metal fabrication, the company has been dedicated to providing top-notch products and services to a wide range of industries. With the integration of laser cutting sheet technology into their manufacturing processes, they have been able to push the boundaries of what is possible in the realm of metal fabrication.Laser cutting sheet technology utilizes a high-powered laser to precisely cut through materials with extreme accuracy. This allows for intricate designs to be created with a level of detail that was previously impossible to achieve. The precision of laser cutting sheet technology also ensures that there is minimal material wastage, making it a cost-effective and environmentally friendly solution for manufacturing.The team at {} has fully embraced this cutting-edge technology and has incorporated it into their production processes. With state-of-the-art laser cutting equipment, they are able to offer their clients a wide range of custom metal fabrication services. Whether it's intricate metal wall art, precision-cut metal components for machinery, or decorative metal signage, {} has the capabilities to bring their clients' visions to life with precision and accuracy.One of the key advantages of laser cutting sheet technology is its ability to cut through a variety of materials, including stainless steel, aluminum, copper, brass, and more. This versatility allows {} to cater to the needs of clients from a diverse range of industries, including automotive, aerospace, architecture, and interior design. The ability to work with a wide range of materials sets {} apart as a leader in the metal fabrication industry.Furthermore, the speed and accuracy of laser cutting sheet technology have significantly reduced production lead times for {} clients. This means that even the most complex and detailed projects can be completed in a fraction of the time compared to traditional cutting methods. This not only benefits clients in terms of project timelines but also allows for a faster turnaround and increased productivity for {}.The team at {} prides itself on its commitment to quality and precision, and the integration of laser cutting sheet technology has only enhanced their ability to deliver exceptional products to their clients. With a focus on continuous improvement and innovation, they are constantly pushing the boundaries of what is possible in the world of custom metal fabrication.In conclusion, laser cutting sheet technology has become an integral part of the manufacturing process at {}. With its ability to cut through a wide range of materials with precision and speed, this innovative technology has allowed {} to elevate the quality of their products and services. As a leader in the metal fabrication industry, {} is dedicated to staying at the forefront of technological advancements and providing their clients with the highest quality custom metal fabrication solutions.
Top Metal Fabrication Services for OEM Projects
Oem Metal Fabrication, a leading metal fabrication company, has been making waves in the industry with its high-quality products and exceptional customer service. The company, which was founded in 1995, has quickly established itself as a top choice for businesses looking for custom metal fabrication solutions.With a team of highly skilled engineers and technicians, Oem Metal Fabrication has the capability to design and produce a wide range of metal products, including precision sheet metal components, enclosures, brackets, and more. The company's state-of-the-art facilities are equipped with the latest technology, allowing them to meet the needs of clients from various industries, including automotive, aerospace, electronics, and telecommunications.In addition to its impressive manufacturing capabilities, Oem Metal Fabrication is also known for its commitment to quality and customer satisfaction. The company follows strict quality control processes to ensure that every product meets the highest standards of excellence. Their dedication to delivering reliable and durable products has earned them a loyal customer base and a reputation for excellence in the industry.Oem Metal Fabrication also takes pride in its ability to offer customized solutions to meet the specific needs of each client. Whether it's a small-scale prototype or a large-scale production run, the company has the expertise and resources to deliver tailored solutions that meet their clients' exact specifications. This personalized approach has made Oem Metal Fabrication a trusted partner for businesses looking for reliable and cost-effective metal fabrication solutions.Furthermore, the company is committed to sustainability and environmental responsibility. Oem Metal Fabrication adheres to strict environmental regulations and utilizes eco-friendly practices in its manufacturing processes. From material sourcing to waste management, the company takes proactive measures to minimize its environmental impact, making it an attractive choice for businesses with a focus on sustainability.As the demand for high-quality metal fabrication solutions continues to grow, Oem Metal Fabrication is poised to meet the needs of businesses across various industries. With its dedication to excellence, commitment to customer satisfaction, and focus on sustainability, the company is well-positioned to maintain its leadership in the industry and continue delivering superior products and services to its clients.In summary, Oem Metal Fabrication has established itself as a leading provider of custom metal fabrication solutions, thanks to its cutting-edge technology, commitment to quality, and personalized approach to meeting the needs of its clients. With a strong track record of excellence and a focus on sustainability, the company is well-equipped to continue meeting the evolving demands of the industry and delivering innovative solutions to its customers.
Guide to Mig Welding Stainless Steel to Mild Steel
Mig Welding Stainless To Mild SteelMig welding stainless steel to mild steel is a common practice in the metal fabrication industry. The process involves using a Mig welder to join these two types of metal together, creating a strong and durable bond. This welding process is widely used in various industries, including construction, automotive, and manufacturing. One company at the forefront of providing high-quality Mig welders for this process is {}. With over 20 years of experience in the welding industry, {} has established itself as a trusted supplier of welding equipment and accessories. The company is dedicated to providing top-of-the-line products and unparalleled customer service, making them a go-to source for all welding needs.When it comes to welding stainless steel to mild steel, the right equipment is crucial for achieving a successful and reliable bond. This is where {} excels, offering a wide range of Mig welders specifically designed for this purpose. Their Mig welders are equipped with advanced technology and features that streamline the welding process and ensure precision and accuracy.In addition to providing high-quality equipment, {} also offers comprehensive training and support to help welders master the art of Mig welding stainless steel to mild steel. Their team of experts is available to provide guidance and assistance, ensuring that welders have the knowledge and skills needed to achieve superior welding results.One of the key factors that sets {} apart from other welding equipment suppliers is their commitment to innovation. They are constantly researching and developing new welding technologies to enhance efficiency and performance. This dedication to innovation enables {} to stay ahead of the curve in an ever-evolving industry, offering their customers the latest advancements in welding equipment.In addition to their commitment to innovation, {} also prioritizes quality and reliability in all of their products. Each Mig welder is subjected to rigorous testing and quality control measures to ensure that it meets the highest standards. This dedication to quality has earned {} a stellar reputation among welders and fabricators, cementing their position as a leader in the welding equipment industry.The process of Mig welding stainless steel to mild steel requires precision and attention to detail. With the right equipment and expertise, welders can achieve seamless and strong bonds between these two metals. {} is proud to be a trusted partner for welders seeking to master this process, providing them with the tools and support they need to excel in their craft.As the demand for Mig welding stainless steel to mild steel continues to grow, {} remains committed to meeting the needs of welders and fabricators. They are continuously expanding their product line and investing in research and development to ensure that they remain at the forefront of welding technology.In conclusion, Mig welding stainless steel to mild steel is a critical process in the metal fabrication industry, and having the right equipment is essential to achieve optimal results. With {}’s top-of-the-line Mig welders and unwavering commitment to quality and innovation, welders can tackle this process with confidence and precision. With {} by their side, welders have a trusted partner to support them in their pursuit of excellence in Mig welding.
Top Fabrication Shops: Ideal Destinations for Your Manufacturing Needs
Steel fabrication shops are an essential part of today's construction and manufacturing industries. These shops are responsible for fabricating structural steel elements that are used in buildings, bridges, ships, and other constructions. Fabrication shops are equipped with state-of-the-art machines and tools that allow experienced workers to cut, shape, and weld steel pieces into the desired shapes and sizes.Steel fabrication shops are the backbone of many critical construction and manufacturing projects. Without them, it would be impossible to build the modern buildings and structures that we take for granted today. These shops employ highly skilled professionals who are passionate about their craft and work tirelessly to ensure that their products meet the highest quality standards.Steel fabrication shops are typically equipped with advanced machinery, such as computer numerically controlled (CNC) machines, auto-feed saws, and welding equipment. These machines allow workers to efficiently cut, drill, shape, and weld steel pieces into the desired shapes and sizes. The workers at steel fabrication shops are highly skilled and experienced, and they have the expertise needed to handle large-scale manufacturing projects.Steel fabrication shops are also responsible for ensuring that their products meet relevant safety standards. This is particularly important in the construction industry, where building codes and safety regulations are heavily enforced. Therefore, it is essential for steel fabrication shops to work with engineers and architects to ensure that their products are structurally sound and adhere to all safety guidelines.In addition, steel fabrication shops can also provide custom fabrications to meet specific project requirements. They have the flexibility to create one-off parts and components that meet unique specifications. This is particularly useful in the manufacturing industry, where customized products are becoming increasingly popular.Overall, steel fabrication shops are an integral part of the modern construction and manufacturing industries. They provide the essential products and services that make these industries possible. With the help of advanced machinery, experienced workers, and strict quality control measures, steel fabrication shops can ensure that their products meet the highest quality standards and contribute to the success of countless construction and manufacturing projects around the world.