The process of welding steel to stainless steel explained
By:Admin
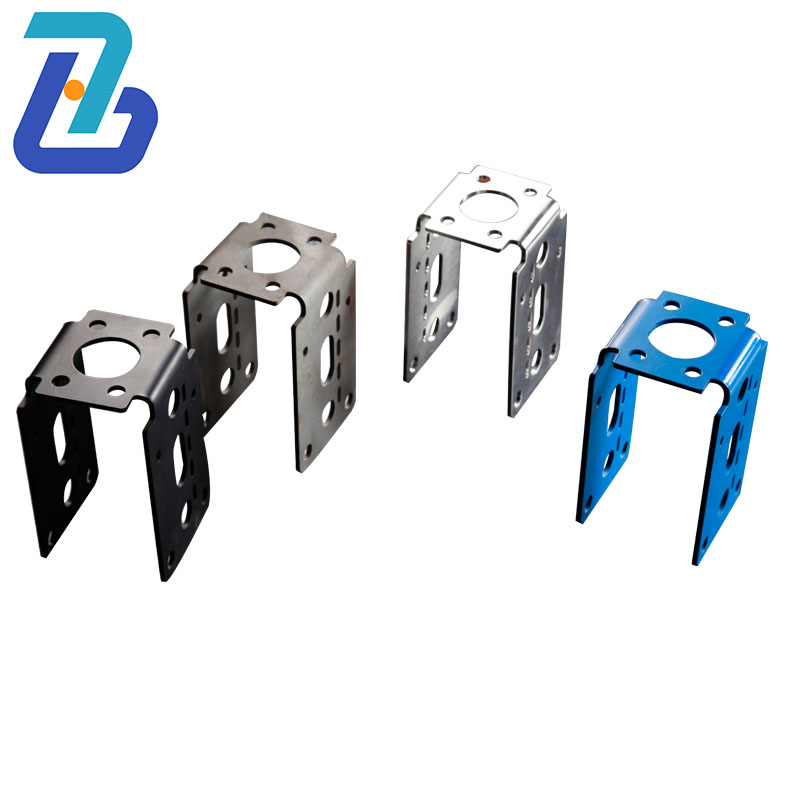
Acme Corporation is proud to introduce an innovative solution for welding steel to stainless steel. This breakthrough process has been developed by our team of experts and is set to revolutionize the welding industry.
Welding steel to stainless steel has posed many challenges in the past. The differences in the properties of these two materials make the welding process complex and often result in weak welds. However, the new welding process developed by Acme Corporation overcomes these challenges and provides a strong and durable bond between steel and stainless steel.
The key to this breakthrough solution lies in our advanced welding techniques and the use of state-of-the-art equipment. Our team has spent extensive time and resources in research and development to optimize the welding parameters and ensure the highest quality of welds. As a result, we have successfully created a welding process that produces strong and reliable bonds between steel and stainless steel.
One of the main advantages of our new welding process is its versatility. Whether it's for industrial applications, automotive components, or household appliances, the ability to weld steel to stainless steel opens up a wide range of opportunities for manufacturers. This breakthrough solution will allow companies to create products that are not only strong and durable, but also have a sleek and modern aesthetic.
In addition to the strength and durability of the welds, our new process also ensures a smooth and clean finish. This is particularly important for applications where the appearance of the welded joint is crucial. With our solution, manufacturers can achieve seamless and visually appealing welds, adding value to their end products.
Furthermore, the new welding process is also more cost-effective compared to traditional methods. By reducing the need for additional materials and minimizing the time required for post-welding treatments, manufacturers can enjoy significant cost savings while maintaining the highest quality standards.
Acme Corporation is committed to providing cutting-edge solutions to meet the evolving needs of the industry. Our new welding process for steel to stainless steel is a testament to our dedication to innovation and excellence. We are excited to bring this breakthrough solution to the market and are confident that it will make a significant impact on the welding industry.
With this new advancement, Acme Corporation continues to solidify its position as a leader in the welding technology sector. Our commitment to research and development, combined with our passion for pushing the boundaries of what is possible, sets us apart from the competition.
As we look ahead, we are already exploring the potential of applying our new welding process to other materials and combinations. Our goal is to continue to innovate and provide solutions that address the most pressing needs of the industry.
In conclusion, Acme Corporation is proud to announce the launch of our groundbreaking welding process for steel to stainless steel. Our new solution offers unmatched strength, durability, and aesthetic appeal, while also providing cost savings for manufacturers. We believe that this advancement will set new standards for welding technology and open up endless possibilities for product development.
The future of welding steel to stainless steel has arrived, and it's being led by Acme Corporation. We invite manufacturers and industry professionals to explore the potential of our new welding process and experience the difference it can make in their products.
Company News & Blog
The process of welding steel to stainless steel explained
Steel To Stainless Steel Welding Process: A Breakthrough Solution by Acme CorporationAcme Corporation is proud to introduce an innovative solution for welding steel to stainless steel. This breakthrough process has been developed by our team of experts and is set to revolutionize the welding industry.Welding steel to stainless steel has posed many challenges in the past. The differences in the properties of these two materials make the welding process complex and often result in weak welds. However, the new welding process developed by Acme Corporation overcomes these challenges and provides a strong and durable bond between steel and stainless steel.The key to this breakthrough solution lies in our advanced welding techniques and the use of state-of-the-art equipment. Our team has spent extensive time and resources in research and development to optimize the welding parameters and ensure the highest quality of welds. As a result, we have successfully created a welding process that produces strong and reliable bonds between steel and stainless steel.One of the main advantages of our new welding process is its versatility. Whether it's for industrial applications, automotive components, or household appliances, the ability to weld steel to stainless steel opens up a wide range of opportunities for manufacturers. This breakthrough solution will allow companies to create products that are not only strong and durable, but also have a sleek and modern aesthetic.In addition to the strength and durability of the welds, our new process also ensures a smooth and clean finish. This is particularly important for applications where the appearance of the welded joint is crucial. With our solution, manufacturers can achieve seamless and visually appealing welds, adding value to their end products.Furthermore, the new welding process is also more cost-effective compared to traditional methods. By reducing the need for additional materials and minimizing the time required for post-welding treatments, manufacturers can enjoy significant cost savings while maintaining the highest quality standards.Acme Corporation is committed to providing cutting-edge solutions to meet the evolving needs of the industry. Our new welding process for steel to stainless steel is a testament to our dedication to innovation and excellence. We are excited to bring this breakthrough solution to the market and are confident that it will make a significant impact on the welding industry.With this new advancement, Acme Corporation continues to solidify its position as a leader in the welding technology sector. Our commitment to research and development, combined with our passion for pushing the boundaries of what is possible, sets us apart from the competition.As we look ahead, we are already exploring the potential of applying our new welding process to other materials and combinations. Our goal is to continue to innovate and provide solutions that address the most pressing needs of the industry.In conclusion, Acme Corporation is proud to announce the launch of our groundbreaking welding process for steel to stainless steel. Our new solution offers unmatched strength, durability, and aesthetic appeal, while also providing cost savings for manufacturers. We believe that this advancement will set new standards for welding technology and open up endless possibilities for product development.The future of welding steel to stainless steel has arrived, and it's being led by Acme Corporation. We invite manufacturers and industry professionals to explore the potential of our new welding process and experience the difference it can make in their products.
Leveraging the Power of CNC Laser Services for Your Business's Needs
CNC Laser Service Launches Cutting-Edge Laser Technology to Meet the Needs of Modern BusinessesThe world of manufacturing and industrial production is constantly evolving, and businesses that want to stay ahead of the curve need to stay up to date with the latest technology. That's why CNC Laser Service (name removed) has recently launched their latest laser cutting system, designed to meet the needs of today's businesses.At CNC Laser Service, we have been providing high-quality laser cutting solutions to our customers for over twenty years. During that time, we have built a reputation for excellence, innovation, and customer service, and we are committed to continuing to meet the evolving needs of our clients.Our latest laser cutting system is a testament to that commitment, incorporating the latest technology and design features to deliver precision cutting solutions that are unmatched in the industry. With CNC Laser Service's state-of-the-art system, businesses can quickly and easily create custom parts, prototypes, and products with the highest level of accuracy and efficiency.One of the key benefits of CNC Laser Service's new laser cutting system is its speed. The system can produce parts and products at a significantly faster pace than traditional cutting methods, which means businesses can bring their products to market much more quickly. This speed also allows for faster changes and modifications to products, which is essential in today's fast-paced business environment.The precision of our system is another crucial attribute. Our laser cutting technology allows us to make cuts with an accuracy of 0.001 of an inch, which means we can create parts and products that are incredibly precise, with no room for error. This level of precision not only ensures the final product is of the highest quality, but it also minimizes waste and reduces costs associated with errors or rework.Another feature that sets CNC Laser Service's cutting-edge laser technology apart from traditional manufacturing solutions is its flexibility. Our system can work with a wide range of materials, including metals, plastics, and even delicate materials such as fabrics and ceramics. This versatility means we can tailor our processes to meet the unique needs of each of our clients, covering a wide range of industries.CNC Laser Service's laser machine also offers a high level of customization, allowing us to create parts and products with unique shapes, sizes, and textures. This customization is a vital feature for businesses that need to create parts that are tailored to specific needs, such as the medical or aerospace industries.Finally, our system's automation capabilities allow us to streamline our processes and reduce the need for manual labor, which translates to lower costs and faster turnaround times for our clients. Our laser cutting system allows us to quickly and easily produce large quantities of parts, making it an ideal solution for businesses with high-volume manufacturing needs.At CNC Laser Service, we are incredibly proud of our latest laser cutting system and the benefits it offers our clients. With its speed, precision, flexibility, customization, and automation capabilities, our technology is poised to take businesses to the next level of manufacturing excellence.Whether you're in the automotive, medical, aerospace, defense, or any other industry, CNC Laser Service's laser cutting system has the capability to meet your unique needs. We invite you to contact us today to learn more about our cutting-edge technology and discover how we can help you take your business to the next level of success.
Local Laser Cutting Services: Find Top-Notch Precision Cutting Near You
Title: Revolutionary Laser Cutting Technology Shaping the Future of ManufacturingIntroduction:In the fast-paced world of manufacturing, the demand for precise and efficient cutting techniques is ever-present. Cutting-edge technology has emerged to meet this demand, and one such innovation is laser cutting. With its ability to achieve high levels of precision, speed, and flexibility, laser cutting has become an indispensable tool for numerous industries.Company Introduction (Company Name):Established as a pioneer in laser cutting services, our company has been at the forefront of this transformative technology for over two decades. With a diverse range of state-of-the-art laser cutting machines and a team of highly skilled professionals, we have earned a reputation as a trusted partner in the manufacturing industry.1. Laser Cutting: An OverviewLaser cutting is a process that employs a high-powered laser beam to cut through various materials, ranging from metals to plastics and even fabrics. This technology offers distinct advantages over traditional cutting methods, including reduced material wastage, higher precision, and increased operational efficiency. It has found widespread applications across industries such as automotive, aerospace, electronics, and signage.2. High Precision and AccuracyThe key feature that sets laser cutting apart is its exceptional precision and accuracy. The focused laser beam allows for intricate, fine cuts without damaging the surrounding material. This precision is crucial in industries where even the slightest deviation can be detrimental. By adhering to strict quality control protocols, our company ensures that every product meets the highest standards of accuracy.3. Material Versatility and FlexibilityLaser cutting is compatible with a wide range of materials. From metals like stainless steel and aluminum to acrylics, wood, and even ceramics, this process effortlessly navigates diverse materials, allowing for versatile applications. Our cutting-edge laser machines can tackle varying material thicknesses and deliver results with exceptional repeatability.4. Efficiency and ProductivityWhen compared to traditional cutting methods, laser cutting excels in terms of speed and efficiency. The non-contact process eliminates the need for physical force, reducing material damage and minimizing production downtime. The rapid cutting speeds and automated capabilities of our laser machines enable faster production cycles, translating into enhanced productivity and reduced overall costs.5. Design Flexibility and CustomizationDesign flexibility is a crucial aspect in today's highly competitive market. Laser cutting provides unparalleled freedom in creating intricate shapes, patterns, and designs. Whether it is complex geometries or personalized engravings, our company's laser cutting services empower manufacturers to bring their visions to life, catering to the evolving demands of the market.6. Sustainable and Environmentally FriendlyLaser cutting is an environmentally conscious choice due to its minimal waste generation and reduced energy consumption. Traditional cutting methods often result in significant material wastage, while laser cutting optimizes material usage, contributing to both cost savings and environmental preservation.Conclusion:As technology continues to advance, laser cutting has emerged as a game-changer in the manufacturing landscape. With its high precision, speed, and versatility, it has revolutionized the way industries approach cutting processes. The expertise and cutting-edge capabilities of our company undoubtedly make it a go-to choice for businesses seeking best-in-class laser cutting solutions, ensuring their products are crafted with utmost precision and efficiency.
Metal Fabrication: A Guide to Building Metal Structures through Cutting, Bending, and Assembly Processes
Metal Fabrication Company Revolutionizes the Industry with Innovative SolutionsMetal fabrication is the process of utilizing a range of techniques to build structures, products, and components from metal materials. The industry has come a long way since the early days of hammering metal sheets together. Today, metal fabrication is an incredibly sophisticated process that involves cutting, shaping, and assembling metal into a variety of different products.Leading the way in the metal fabrication industry is (Brand Name Removed), a company committed to providing innovative solutions to clients’ metal fabrication needs. With their state-of-the-art techniques and technology, they have revolutionized how metal is fabricated and produced across the industry.Their metal fabrication process begins with cutting - using tools such as plasma cutters and water jets to carefully and accurately cut the metal into the required shapes. From there, the metal is shaped through processes such as bending and rolling, to create the necessary structures and components. Welding is then utilized to assemble these structures, completing the fabrication process.What sets (Brand Name Removed) apart from other metal fabrication companies is their dedication to investing in the latest technology and innovations. They have the capabilities to fabricate a wide range of metals, including steel, aluminium, and titanium - each with its unique properties and challenges. Their advanced techniques and skilled workforce mean that they can create highly complex, custom-made components, all while maintaining the highest levels of precision and accuracy.One particular aspect that has enabled (Brand Name Removed) to make significant strides forward is their incorporation of computer-aided design and finite element analysis. They utilize CAD/CAM software to create virtual models of the metal components before fabrication begins, allowing for a quicker and more efficient process. This also ensures that the final product meets the client's expected specifications.Another area of innovation for (Brand Name Removed) is their approach to sustainability. They strive to use environmentally friendly materials and techniques whenever possible to reduce the impact on the environment. This includes utilizing recycled materials in their fabrication processes and improving their waste management procedures.With over [insert number of years] years of experience in the metal fabrication industry, (Brand Name Removed) has built a reputation for excellence and quality. They work closely with clients across a range of industries, including aerospace, automotive, and construction, to provide bespoke metal solutions for their specific needs.Furthermore, (Brand Name Removed) offers a wide range of services to complement their metal fabrication capabilities. They offer CAD design, prototyping, repair, and maintenance services, ensuring clients have everything they need under one roof.Moreover, they have an exceptional quality control program, ensuring the compliance of the fabrication process with the highest industry standards. This is achieved through detailed process mapping, checks, and cross-checks at each step of the process.The metal fabrication industry is constantly evolving, and (Brand Name Removed) is taking the lead. Their pioneering approach, investment in the latest technology, and commitment to quality and sustainability mean that they are well-positioned to continue driving the industry forward.With an unwavering focus on innovation, quality, and sustainability, (Brand Name Removed) is set to remain at the forefront of the metal fabrication industry - delivering exceptional results for clients across the world.
Essential Equipment in TIG Welding: Advantages and Applications
Title: TIG Welding Equipment Revolutionizing Precision Welding: A Game Changer for Critical ApplicationsIntroduction:TIG (Tungsten Inert Gas) welding, an advanced welding technique that utilizes an inert gas shield instead of a slag to protect the weld pool, has emerged as a highly attractive alternative to gas and manual metal arc welding. This technology has played a pivotal role in the acceptance of high-quality welding in critical applications. Among the leading companies in the industry, (name of the company) has established itself as a prominent player in supplying essential TIG welding equipment. Their commitment to innovation and expertise in TIG welding steel have revolutionized the welding industry. This article will delve into the significance of TIG welding equipment and how it has transformed precision welding.The Advantages of TIG Welding Equipment:TIG welding equipment offers numerous advantages that have propelled its rise in popularity in critical applications. One of its key advantages lies in the inert gas shield used, which eliminates the need for a slag, resulting in cleaner and more precise welds. This technique allows for increased control over the welding process, ensuring minimal distortion and reduced spattering. With TIG welding, the welder can easily regulate the heat input, making it ideal for welding thin materials. Moreover, the absence of slag facilitates easier post-weld cleaning, minimizing time and effort required for finishing.Another significant advantage of TIG welding equipment is its ability to achieve high-quality welds. The process employs a non-consumable tungsten electrode, which retains its shape and does not melt during the welding process. This characteristic enhances the welder's precision, resulting in aesthetically appealing and durable welds. Moreover, the ability to work with a wide range of materials, including stainless steel, aluminum, and copper, further highlights the versatility and superiority of TIG welding equipment.Promoting Safety and Efficiency with TIG Welding Equipment:Apart from its technical benefits, TIG welding equipment also prioritizes safety and efficiency. The process utilizes an electric foot pedal, granting the welder precise control over the heat input and filler rod. This level of control reduces the risks of overheating, burn-throughs, and other imperfections. Additionally, the precise control enables welders to create intricate and detailed welds with ease, making TIG welding equipment highly popular in industries that demand exceptional precision, such as aerospace, automotive, and medical equipment manufacturing.The Role of (Company Name) in Advancing TIG Welding Steel:In this realm of TIG welding equipment, (Company Name) has established a commendable reputation for delivering high-quality products and exceptional service. With their commitment to continuous innovation and expertise in TIG welding steel, the company has played a pivotal role in promoting the acceptance and adoption of TIG welding in critical applications.(Company Name) offers a comprehensive range of TIG welding equipment, including state-of-the-art power sources, torches, and consumables. Their equipment is designed to provide welders with superior control, exceptional arc stability, and unmatched reliability. Leveraging advanced technologies, (Company Name) ensures that their TIG welding equipment optimizes weld quality, productivity, and safety.Conclusion:TIG welding equipment has transformed the welding industry, presenting an attractive alternative to traditional welding techniques. With its numerous advantages, including cleaner welds, increased control over heat, and the ability to work with various materials, TIG welding equipment has become indispensable in critical applications. Notably, (Company Name) has significantly contributed to the advancement of TIG welding, ensuring the highest quality welds for industries requiring precision and durability. Continuous innovation and expertise in TIG welding steel have firmly established (Company Name) as a leader in the field, empowering welders and revolutionizing the welding industry as a whole.
Discover a Wide Range of Bending Products and Services on Ferret.com.au
CNC Bending Service: The Future of Metal FabricationMetal fabrication has come a long way since the days of manual hand-operated machines, where the process of metal bending was labor-intensive and required skilled craftsmen. Today, computer numerical control (CNC) technology has revolutionized the manufacturing industry, making it faster, more efficient, and highly accurate.What is CNC Bending?CNC Bending is a process of metal forming that utilizes computer-controlled machines to create precise and complex bends in sheet metal and other materials. CNC machines can perform multiple bends in a single cycle, and they are capable of producing large quantities of parts with minimal operator intervention.The Advantages of CNC BendingCNC metal bending offers several advantages over traditional metal forming methods, including:1. High precision: CNC machines are highly accurate and can produce parts with precise tolerances.2. Rapid production: CNC bending machines can produce parts at a faster rate than manual bending machines, making the process more efficient and cost-effective.3. Versatility: CNC machines can perform multiple bending operations in a single cycle, allowing for the creation of complex shapes and intricate designs.4. Consistency: CNC machines can produce identical parts with the same level of precision every time, ensuring consistency in the final product.5. Reduced waste: CNC machines are programmed to optimize material usage, reducing waste and saving costs.Applications of CNC BendingCNC bending is widely used in various industries, including aerospace, automotive, construction, and electronics. Some of the common applications of CNC bending include:1. Fabrication of metal enclosures, chassis, and panels.2. Production of brackets, frames, and supports.3. Creation of bends in pipes and tubes.4. Manufacturing of complex shapes for medical devices.Choosing the Right CNC Bending Service ProviderWhen it comes to CNC bending services, it’s essential to choose a reliable and experienced service provider that can deliver quality results. Here are some factors to consider when selecting a CNC bending service provider:1. Technology: Choose a provider that uses the latest CNC bending technology and equipment to ensure high precision and efficiency.2. Experience: Look for a provider with years of experience in CNC bending and a proven track record of delivering quality results.3. Capacity: Consider the provider’s capacity to handle your specific project requirements, including materials, specifications, and volume.4. Quality control: Ensure that the provider has a robust quality control process in place to ensure the final product meets your specifications.5. Cost-effectiveness: Compare quotes from multiple providers and choose the one that offers the best value for your money.ConclusionCNC bending is the future of metal fabrication, and its advantages over traditional metal forming methods make it an ideal choice for various industries. By choosing the right CNC bending service provider, you can ensure that your project is produced with high precision, efficiency, and quality. Contact us today to learn more about our CNC bending services!
How to Spot Weld Galvanized Steel: A comprehensive guide
Spot Weld Galvanized Steel: A New Milestone in Innovative EngineeringIn the world of engineering and manufacturing, the need for durable and high-performing materials is always on the rise. The demand for materials that can withstand extreme conditions while maintaining their structural integrity has led to the development of innovative solutions. One such solution is the spot welding of galvanized steel, a process that has revolutionized the way in which manufacturers create and assemble various products.Galvanized steel is a type of steel that has been coated with a layer of zinc to protect it from corrosion. This coating not only increases the longevity of the steel but also provides excellent protection against the elements, making it an ideal material for a wide range of applications. However, welding galvanized steel has always posed a challenge due to the potential release of harmful fumes and the difficulty in achieving a strong and durable joint.Enter {Company Name}, a leading manufacturer in the field of engineering solutions and materials. With a strong focus on innovation and cutting-edge technology, {Company Name} has developed a revolutionary method for spot welding galvanized steel that addresses the challenges associated with this process. By combining their expertise in engineering with state-of-the-art equipment, {Company Name} has successfully created a solution that not only ensures the integrity of the galvanized coating but also produces exceptionally strong and durable welds.The process of spot welding galvanized steel involves the use of specialized welding equipment that is designed to work specifically with galvanized materials. This equipment is able to control the welding parameters with precision, minimizing the potential for damage to the galvanized coating while ensuring a reliable bond between the steel surfaces. This level of control and accuracy is what sets {Company Name}'s spot welding process apart from conventional methods, making it a game-changer in the industry.The benefits of spot welding galvanized steel are numerous. By preserving the integrity of the galvanized coating, manufacturers can be confident in the longevity and performance of the finished product. Additionally, the strength and durability of the weld itself ensure that the assembled components will withstand the rigors of their intended use, whether in automotive, construction, or any other industry. Furthermore, the elimination of harmful fumes during the welding process contributes to a safer and healthier work environment for the individuals involved in the manufacturing process.{Company Name}'s breakthrough in spot welding galvanized steel has garnered attention from manufacturers across various industries. The ability to create strong and reliable welds in galvanized steel opens up new possibilities for the design and construction of a wide range of products. From automotive components to structural frames, the applications of spot welded galvanized steel are virtually limitless.In addition to their innovative spot welding process, {Company Name} also offers a comprehensive range of engineering solutions, including design and fabrication services, materials testing, and technical support. Their commitment to quality and customer satisfaction has established them as a trusted and dependable partner for manufacturers seeking reliable and cost-effective engineering solutions.As the demand for high-performance materials continues to grow, the development of innovative processes such as spot welding galvanized steel is crucial for the advancement of various industries. With {Company Name} leading the way in this field, manufacturers can look forward to a future where the possibilities for creating durable and high-performing products are endless.
Key Considerations for Choosing the Right Welding Techniques for Structural Projects
Structural Weld, a leading global provider of welding solutions has announced a new line of products which will enable manufacturers to improve efficiency while reducing downtime and production costs. The new product line, which includes welding equipment, consumables, and accessories, is designed to meet the growing demand for high-quality welding solutions for various applications.For over three decades, Structural Weld has established itself as a reputable provider of welding solutions across various industries, including fabrication, petrochemical, oil and gas, power generation, marine and offshore. The company has built a reputation for offering innovative and cost-effective welding solutions to meet the unique needs of its customers.Structural Weld's new product line is a result of the company's continued commitment to innovation and providing high-quality welding solutions to its customers. The new line of products features state-of-the-art welding equipment equipped with advanced technology to offer superior performance, speed, and accuracy. Customers can choose from a variety of welding machines, including MIG, TIG, stick welding, and plasma cutting machines.The company has also developed a range of welding consumables that are specifically designed to complement its welding machines. The welding consumables, which include electrodes, filler wires, and flux-cored wires, are manufactured to the highest quality standards to ensure that they deliver exceptional performance and reliability.In addition to the welding equipment and consumables, Structural Weld has also added a range of welding accessories to its product line. The welding accessories, which include welding helmets, gloves, and safety glasses, are designed to provide maximum comfort and protection to welders while they work. The company has also introduced a range of welding carts and plasma cutting tables to help welders transport and set up their welding equipment easily.Structural Weld's new product line is expected to provide significant benefits to manufacturers across various industries. The welding equipment is designed to reduce downtime and increase efficiency, allowing manufacturers to produce high-quality products at a faster rate. The welding consumables and accessories are also expected to help manufacturers reduce material waste, minimize defects, and improve overall productivity."While we have always been committed to providing our customers with high-quality welding solutions, our new product line represents a significant milestone for our company," said the Structural Weld spokesperson. "We are confident that our new line of products will help our customers improve their welding processes significantly and ultimately boost their bottom line."With its new product line, Structural Weld is poised to continue its growth trajectory by expanding its market reach and attracting new customers. The company's commitment to innovation, quality, and customer satisfaction has been at the forefront of its success, and this new product line is a testament to its enduring commitment to provide the best welding solutions to its customers.In conclusion, Structural Weld's new product line is a welcome development for manufacturers across various industries. With its state-of-the-art welding equipment, high-quality consumables, and innovative accessories, the company is well-positioned to provide cost-effective solutions that meet the unique needs of its customers. As the company continues to grow, it is clear that its commitment to innovation, quality, and customer satisfaction will continue to be the driving force behind its success.
Top 10 Welding Electrodes for Your Next Project
In the world of welding technology, the welding electrode is a critical component that plays a key role in the process of creating strong and durable welds. There are many different types of welding electrodes available on the market, each designed for specific applications and welding processes. However, one company that has been making waves in the industry is {Company Name}, a leading manufacturer of high-quality welding electrodes.{Company Name} is a global leader in the production of welding electrodes, with a strong reputation for innovation, quality, and reliability. The company has been in the business for over 50 years and has grown to become a trusted name in the welding industry. Their commitment to excellence and dedication to meeting the needs of their customers has helped them to establish themselves as a preferred supplier of welding electrodes for a wide range of applications.One of the key factors that set {Company Name} apart from the competition is their focus on research and development. The company has a team of experienced engineers and scientists who are constantly working to improve the performance and capabilities of their welding electrodes. This dedication to innovation has led to the development of cutting-edge products that deliver superior results and exceed industry standards.{Company Name} offers a diverse range of welding electrodes, catering to various types of welding processes and applications. Whether it's for manual metal arc welding, gas tungsten arc welding, or submerged arc welding, the company has a comprehensive range of electrodes to meet the specific needs of their customers. Their products are designed to provide excellent arc stability, high weld quality, and superior mechanical properties, making them the preferred choice for professionals in the welding industry.Furthermore, {Company Name} is committed to sustainability and environmental responsibility. They have implemented eco-friendly manufacturing processes and use recycled materials in their production, minimizing their impact on the environment. This commitment to sustainability has earned them recognition and respect in the industry, as they continue to set new standards for environmentally conscious manufacturing practices.In addition to their dedication to product quality and innovation, {Company Name} places a strong emphasis on customer satisfaction. Their team of experts provides technical support and guidance to help their customers select the right welding electrodes for their specific needs. They also offer training programs and workshops to educate their customers on best practices for welding, ensuring that they achieve the best results with {Company Name} welding electrodes.Looking ahead, {Company Name} is set to continue its trajectory of growth and success in the welding industry. With a strong focus on innovation, quality, and customer satisfaction, the company is well-positioned to remain a leading supplier of welding electrodes for years to come. Their commitment to excellence and dedication to meeting the evolving needs of their customers ensures that they will continue to be at the forefront of the welding industry.In conclusion, {Company Name} is a company that has demonstrated its commitment to excellence and innovation in the field of welding electrodes. With a strong reputation for quality and reliability, the company has established itself as a trusted partner for professionals in the welding industry. Their focus on research and development, sustainability, and customer satisfaction sets them apart from the competition and positions them for continued success in the future. As the industry evolves, {Company Name} will undoubtedly continue to play a pivotal role in shaping the future of welding technology.