The Ultimate Guide to Profitable Plasma Cutting Techniques
By:Admin
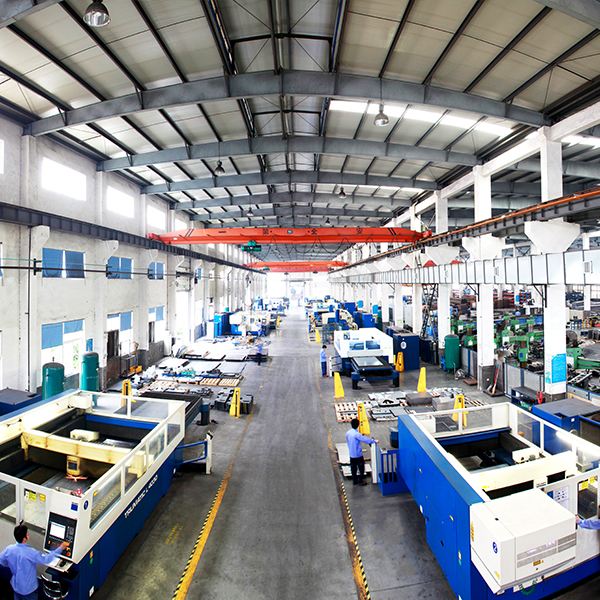
One company at the forefront of this industry is {Company Name}. Founded in 1995, {Company Name} has established itself as a leading provider of plasma cutting solutions for a wide range of industries, including automotive, aerospace, and construction. With state-of-the-art technology and a team of experienced professionals, {Company Name} has built a reputation for delivering high-quality products and exceptional customer service.
The key to {Company Name}'s success lies in its ability to understand the unique needs of its customers and provide tailored cutting solutions that optimize their production processes. By offering a wide selection of plasma cutting systems and consumables, {Company Name} has positioned itself as a one-stop-shop for businesses looking to invest in this cutting-edge technology.
One of the primary advantages of plasma cutting is its ability to produce clean, precise cuts on a variety of materials, including steel, aluminum, and stainless steel. This level of precision not only enhances the quality of the finished product but also reduces the need for secondary processing, ultimately saving businesses time and money in their production processes. Additionally, plasma cutting is known for its fast cutting speeds, further increasing efficiency and reducing production time.
In recent years, {Company Name} has expanded its product line to include a range of automated plasma cutting systems, further enhancing its capabilities and enabling its customers to automate their cutting processes. These automated systems offer advanced features such as CNC controls, automatic gas consoles, and high-definition plasma systems, allowing businesses to achieve even greater levels of precision and efficiency in their operations.
As the demand for high-quality metal products continues to grow, businesses are increasingly turning to plasma cutting as a means of staying competitive in the market. {Company Name} recognizes this trend and is committed to providing cutting-edge solutions that enable its customers to maximize their productivity and profitability.
Moreover, {Company Name} offers comprehensive training and support services to ensure that its customers are able to fully leverage the capabilities of their plasma cutting systems. With a team of highly skilled technicians and engineers, {Company Name} is dedicated to providing ongoing support to its customers, helping them overcome any challenges they may encounter in their cutting processes.
In addition to its cutting-edge technology and exceptional customer support, {Company Name} is also dedicated to sustainability and environmental responsibility. Its plasma cutting systems are designed to minimize waste and reduce energy consumption, aligning with the growing trend of eco-friendly manufacturing practices.
As the manufacturing and metal fabrication industry continues to evolve, businesses are constantly seeking new ways to improve their processes and increase their profit margins. Plasma cutting has emerged as a powerful tool in achieving these goals, and companies like {Company Name} are playing a pivotal role in driving this transformation.
With its cutting-edge technology, comprehensive product line, and commitment to customer satisfaction, {Company Name} is poised to remain a leader in the plasma cutting industry for years to come. As businesses strive to stay ahead in a competitive market, partnering with a trusted and reliable provider like {Company Name} can make all the difference in achieving success and profitability.
Company News & Blog
MIG Welding Tips for Working with Thin Steel
Mig Welding Thin Steel – A Game-Changer in the Welding IndustryWelding is a crucial process in the manufacturing and construction industry. It involves the process of fusing two pieces of metal to create a strong bond. Mig welding is one of the most popular welding techniques used today. It stands for Metal Inert Gas welding and is sometimes referred to as Gas Metal Arc welding (GMAW).Mig welding uses a consumable electrode wire consisting of a metal wire placed on a spool that continuously feeds through a welding gun. The process involves the wire coming into contact with the base metal, generating an electrical arc that melts the wire and the base metal together to form a strong bond. The process is efficient, and it can be used to weld various metals, including carbon steel, stainless steel, aluminum, nickel alloys, and copper.However, Mig welding thin steel has always been a challenge, mainly due to the risk of burn-through, weld distortion, and poor weld quality. These challenges have been at the forefront of the welding industry, and many companies have been searching for a solution to solve these issues. Fortunately, one company has developed a solution that has been a game-changer in the welding industry.The company, which prefers to remain anonymous, has developed a new technique that enhances Mig welding thin steel, delivering exceptional results with minimal risks of distortion and burn-through. The company’s innovation is designed for use in the automotive, aerospace, and construction industries.Their solution is a new welding wire designed explicitly for thin steel. The wire comprises a unique combination of materials designed to deliver superior results when welding thin steel. Its construction comprises a specific blend of wire, shield gas, and other advanced technologies that enhance the welding process.The new welding wire boasts several benefits, including a lower melting point and higher heat conductivity, making it easier to weld thin steel without burning through. Additionally, it enhances the arc stability hence reducing the risk of weld defects.For the automotive industry, the new welding wire has been a game-changer. Automakers face the challenge of building lighter, fuel-efficient cars, and the new welding wire has been instrumental in achieving that. Thin sheet metal is used to construct body panels, hoods, and trunks. The new welding wire has helped automakers overcome the challenges of welding these thin sheets, resulting in lighter vehicles, increased fuel efficiency, and reduced manufacturing costs.In the aerospace industry, the new welding wire has also come in handy. Aircraft manufacturers use thin steel in the construction of wings, tail sections, and fuselage. These thin sheets require careful handling during the welding process to avoid distortions and burn-through. The new welding wire has enhanced the welding process, enabling manufacturers to construct high-quality aircraft with minimal defects, reduced manufacturing costs, and faster production times.For the construction industry, the new welding wire has decreased the risks of welding thin structural pipes. The welding of pipes is essential for the construction of various structures, including buildings, bridges, and tunnels. With the new welding wire, manufacturers can weld thin steel pipes without the risk of burn-through and distortions, creating a safer and more efficient construction environment.In summary, the development of the new welding wire designed for Mig welding thin steel has been a game-changer in the welding industry. Its unique combination of materials has enhanced the welding process, reducing the risks of burn-through, weld defects, and distortions. The new welding wire has been instrumental in facilitating the production of lighter, fuel-efficient vehicles in the automotive industry, the production of high-quality aircraft in the aerospace industry, and safer and more efficient welding for the construction industry.The company that developed the new welding wire has continued to innovate, seeking new ways to improve the welding process further. Their achievement serves as a testament to the power of innovation and the endless possibilities it presents. The welding industry will continue to benefit from advancements in technology, and we can expect even more innovations in the future.
The Ultimate Guide to Profitable Plasma Cutting Techniques
Plasma cutting has become increasingly popular in the manufacturing and metal fabrication industry due to its efficiency and precision. This cutting method utilizes a high-velocity jet of ionized gas to cut through various types of metals with extreme accuracy, making it an ideal choice for businesses looking to streamline their production processes and increase their profit margins.One company at the forefront of this industry is {Company Name}. Founded in 1995, {Company Name} has established itself as a leading provider of plasma cutting solutions for a wide range of industries, including automotive, aerospace, and construction. With state-of-the-art technology and a team of experienced professionals, {Company Name} has built a reputation for delivering high-quality products and exceptional customer service.The key to {Company Name}'s success lies in its ability to understand the unique needs of its customers and provide tailored cutting solutions that optimize their production processes. By offering a wide selection of plasma cutting systems and consumables, {Company Name} has positioned itself as a one-stop-shop for businesses looking to invest in this cutting-edge technology.One of the primary advantages of plasma cutting is its ability to produce clean, precise cuts on a variety of materials, including steel, aluminum, and stainless steel. This level of precision not only enhances the quality of the finished product but also reduces the need for secondary processing, ultimately saving businesses time and money in their production processes. Additionally, plasma cutting is known for its fast cutting speeds, further increasing efficiency and reducing production time.In recent years, {Company Name} has expanded its product line to include a range of automated plasma cutting systems, further enhancing its capabilities and enabling its customers to automate their cutting processes. These automated systems offer advanced features such as CNC controls, automatic gas consoles, and high-definition plasma systems, allowing businesses to achieve even greater levels of precision and efficiency in their operations.As the demand for high-quality metal products continues to grow, businesses are increasingly turning to plasma cutting as a means of staying competitive in the market. {Company Name} recognizes this trend and is committed to providing cutting-edge solutions that enable its customers to maximize their productivity and profitability.Moreover, {Company Name} offers comprehensive training and support services to ensure that its customers are able to fully leverage the capabilities of their plasma cutting systems. With a team of highly skilled technicians and engineers, {Company Name} is dedicated to providing ongoing support to its customers, helping them overcome any challenges they may encounter in their cutting processes.In addition to its cutting-edge technology and exceptional customer support, {Company Name} is also dedicated to sustainability and environmental responsibility. Its plasma cutting systems are designed to minimize waste and reduce energy consumption, aligning with the growing trend of eco-friendly manufacturing practices.As the manufacturing and metal fabrication industry continues to evolve, businesses are constantly seeking new ways to improve their processes and increase their profit margins. Plasma cutting has emerged as a powerful tool in achieving these goals, and companies like {Company Name} are playing a pivotal role in driving this transformation.With its cutting-edge technology, comprehensive product line, and commitment to customer satisfaction, {Company Name} is poised to remain a leader in the plasma cutting industry for years to come. As businesses strive to stay ahead in a competitive market, partnering with a trusted and reliable provider like {Company Name} can make all the difference in achieving success and profitability.
How to Weld Stainless Steel to Mild Steel: Tips and Techniques
Welding Stainless To Mild Steel: A New Milestone for {}Companies in the manufacturing and construction industry are constantly seeking advancements in technology and technique to improve their products. One such advancement has recently been achieved by {} with the successful welding of stainless steel to mild steel. This breakthrough is expected to have a significant impact on the industry, as it opens up new possibilities for the production of stronger and more durable products.{} is a leading manufacturer in the industry, specializing in the production of high-quality steel products for various applications. With a strong focus on research and development, the company has been able to stay ahead of the curve, constantly pushing the boundaries of what is possible in the field of steel manufacturing. This recent achievement of welding stainless steel to mild steel is a testament to {}'s innovative spirit and commitment to excellence.The successful welding of stainless steel to mild steel is no small feat. The two materials have vastly different properties, making it a challenging task to join them together effectively. {}'s team of experts and engineers have spent years researching and experimenting with different welding techniques and materials to achieve this breakthrough. Their hard work and dedication have finally paid off, as they have developed a method that allows for a strong and reliable bond between the two materials.This achievement has significant implications for the industry, as it opens up new opportunities for the production of more durable and versatile products. The ability to weld stainless steel to mild steel means that manufacturers can now create products that combine the corrosion resistance of stainless steel with the strength and affordability of mild steel. This will not only result in stronger and longer-lasting products but also offer cost savings for companies in the long run.In addition to the potential benefits for manufacturers, this breakthrough also has broader implications for the construction and infrastructure industries. The ability to weld stainless steel to mild steel means that stronger and more durable structures can be built, providing greater safety and longevity. This could have a significant impact on a wide range of applications, from the construction of buildings and bridges to the production of vehicles and machinery.{}'s achievement in welding stainless steel to mild steel is a testament to their commitment to innovation and excellence. With this breakthrough, they have once again proven themselves to be a leader in the industry, pushing the boundaries of what is possible in steel manufacturing. As the company continues to invest in research and development, it is likely that they will continue to make advancements that will have a lasting impact on the industry as a whole.In conclusion, {}'s successful welding of stainless steel to mild steel is a significant achievement that has the potential to revolutionize the industry. This breakthrough opens up new possibilities for the production of stronger and more durable products, with broad implications for manufacturers, construction companies, and the infrastructure industry as a whole. As {} continues to lead the way in research and development, it is clear that they will continue to make significant contributions to the field of steel manufacturing.
Quality Metal Fabrication Services for Your Business: A Complete Guide
Best Metal Fabrication (BMF) is a leading metal fabrication company that specializes in providing high-quality and custom metal fabrication services to a wide range of industries. With a focus on precision, efficiency, and innovation, BMF has established itself as a trusted partner for businesses looking for reliable metal fabrication solutions.Founded in 2005, BMF has quickly grown to become a prominent player in the metal fabrication industry. The company's state-of-the-art facilities are equipped with advanced machinery and technology, allowing them to take on projects of all sizes and complexities. Whether it's custom metal parts, structural steel fabrication, or specialized welding services, BMF is dedicated to delivering exceptional results that meet and exceed their clients' expectations.One of the key strengths of BMF is their team of highly skilled and experienced metal fabricators. With a strong commitment to quality and craftsmanship, BMF's team takes pride in their ability to turn raw materials into precision-engineered metal components. From concept to completion, BMF works closely with their clients to understand their specific needs and deliver tailor-made solutions that are both functional and aesthetically pleasing.In addition to their in-house capabilities, BMF also takes a customer-centric approach to their business. They understand that each project is unique, and they strive to provide personalized attention and support to their clients throughout the fabrication process. This includes comprehensive project planning, design assistance, and quality control measures to ensure that the final product meets the highest industry standards.With a strong focus on continuous improvement, BMF is always exploring new technologies and methods to enhance their metal fabrication processes. This commitment to innovation has enabled them to stay ahead of the curve and deliver cutting-edge solutions that are efficient, cost-effective, and environmentally friendly. From adopting sustainable practices to embracing new materials and techniques, BMF is dedicated to creating a positive impact on the industry and the communities they serve.Furthermore, BMF has built a reputation for reliability and dependability. They understand the importance of meeting deadlines and adhering to project specifications, and they take pride in their ability to deliver on their promises. This level of professionalism has earned BMF the trust and respect of their clients, who rely on them for their most challenging and time-sensitive fabrication needs.As BMF continues to grow and expand its reach, the company remains committed to upholding its core values of integrity, excellence, and customer satisfaction. Whether it's serving local businesses or multinational corporations, BMF is driven by a passion for precision metal fabrication and a dedication to providing superior products and services.In conclusion, Best Metal Fabrication is a leading force in the metal fabrication industry and a trusted partner for businesses seeking top-notch fabrication solutions. With a focus on quality, innovation, and customer satisfaction, BMF is well-positioned to continue its upward trajectory and set new standards for excellence in metal fabrication. Their dedication to precision, efficiency, and reliability makes them a sought-after partner for companies looking to bring their metal fabrication projects to life.
How to Achieve Cold Welding with Stainless Steel
Cold Welding Stainless Steel Sets New Standards in Metal JoiningCold Welding Stainless Steel, a revolutionary technology developed by an American company founded in 2005, is set to disrupt the metal joining industry. The innovative technology, which involves the joining of metal surfaces by creating atomic bonds at room temperature and pressure, has shown remarkable results that surpass traditional welding methods in terms of performance, cost efficiency, and sustainability.The process of cold welding involves two metal surfaces being pressed together with a force of several tons. This creates enough deformation on the atomic scale to cause the atoms of the two surfaces to bond together. The result is a metallurgical bond that is stronger than the base metal, free from defects, and has excellent mechanical and chemical properties. The process is also performed at room temperature, eliminating the need for intense heat and producing little to no fumes and harmful byproducts.The technology has significant advantages over traditional welding methods. First, there is no need for a heat source, which eliminates the need for expensive welding equipment and reduces the energy consumption used in the welding process. Secondly, the process is highly efficient as minimal material is lost due to the lack of heat input. Thirdly, the technology is environmentally friendly as it eliminates the need for gases and fluxes that are used in traditional welding and create harmful emissions.Cold Welding Stainless Steel has a wide range of applications, including aerospace, automotive, medical instruments, precision instruments, and electronics, among others. In the aerospace industry, the technology is used to join titanium, aluminum, and other metals used in the construction of airplanes and space vehicles. The technology is also used in automotive applications, where it is used to join dissimilar metals, such as aluminum and steel, to improve fuel efficiency by reducing the weight of the vehicle.In the medical industry, Cold Welding Stainless Steel is used to join small and fragile components used in surgical instruments, where precision and high mechanical properties are critical. The technology is also used in the electronics industry, where it is used to join connectors and microelectronic components. The applications of Cold Welding Stainless Steel are vast, and its advantages make it a highly valuable technology across a range of industries.Apart from being a highly functional technology, Cold Welding Stainless Steel is also cost-effective. The elimination of heat and welding equipment, as well as the reduction in material waste, makes it a cost-effective alternative to traditional welding methods. Additionally, the eco-friendly aspect of the technology makes it an attractive option for businesses looking to reduce their carbon footprint and maintain sustainability.Furthermore, the technology is user-friendly as it doesn't require specialized training or certification to operate. Only simple tools are needed to perform cold welding, making it easily accessible to a wide range of operators.In conclusion, Cold Welding Stainless Steel is a revolutionary technology that promises to transform the metal joining industry. The technology's remarkable results in terms of performance, cost efficiency, and sustainability, coupled with its vast range of applications, make it a highly valuable technology for a range of industries. With the ability to join metals at room temperature and pressure, the technology has set new standards in metal joining, propelling the industry forward into a new era of innovation and functionality.
Mastering the Art of Tig Welding for Mild Steel: A Comprehensive Guide
Tig Welding Mild Steel: A Versatile and Reliable Solution for Various IndustriesIntroduction:In today's fast-paced and demanding industrial landscape, welding plays a crucial role in constructing and fabricating various structures. Welding processes have come a long way, evolving to suit different materials and industry requirements. One such process is Tungsten Inert Gas (TIG) welding, renowned for its precision and versatility.Brands like {} have been at the forefront of delivering exceptional TIG welding solutions. By combining cutting-edge technology with innovative engineering, they have become a trusted name in the industry. Offering a wide range of products and services, the brand has been instrumental in ensuring high-quality welds and enhancing productivity for numerous industries.TIG Welding Mild Steel:Mild steel is one of the most commonly used materials in the fabrication industry due to its affordability, availability, and ease of manipulation. TIG welding mild steel, using the right equipment and techniques, ensures strong and aesthetically pleasing welds.The TIG welding process relies on a non-consumable tungsten electrode to produce the weld, while an inert gas, such as argon, shields the weld area from atmospheric contamination. The ability to control heat input during TIG welding allows for precise welds, making it an ideal choice for mild steel applications.Key Advantages of TIG Welding Mild Steel:1. High-quality welds: TIG welding mild steel offers superior control over the heat input, resulting in high-quality welds with minimal distortion. This makes it suitable for applications that require a flawless finish, such as automotive components, furniture, and architectural structures.2. Versatility: TIG welding is compatible with a wide range of mild steel thicknesses, making it a versatile solution for various applications. From thin sheet metal to thicker structural components, TIG welding can handle it all with precision and ease.3. Clean and aesthetically pleasing welds: The TIG welding process produces clean and visually appealing welds, making it highly sought after in industries where aesthetics matter. This makes it an excellent choice for applications in the food and beverage industry, where hygiene and appearance are paramount.4. Reduced post-weld cleaning: TIG welding creates minimal spatter and produces very little smoke, reducing the need for extensive post-weld cleaning. This saves precious time and resources, enhancing productivity and efficiency in the welding process.Application of TIG Welding Mild Steel:The versatility of TIG welding mild steel makes it suitable for a wide range of industries and applications. Some notable applications include:1. Automotive and transportation: TIG welding is commonly used in the automotive industry for manufacturing exhaust systems, chassis components, and body panels. The precision and control offered by TIG welding ensure durable welds, crucial for the safety and performance of vehicles.2. Construction and infrastructure: TIG welding mild steel plays a vital role in the construction industry, where it is used for fabricating structural components, staircases, and fencing. The ability to produce aesthetically pleasing welds makes TIG welding a preferred choice in architectural applications.3. Food and beverage industry: Stainless steel is a popular choice in the food and beverage industry due to its corrosion resistance and ease of cleaning. TIG welding mild steel is often utilized to weld stainless steel components such as tanks, piping, and equipment, ensuring hygiene and quality standards are met.Conclusion:In conclusion, TIG welding mild steel continues to be a versatile and reliable solution for various industries. With brands like {} leading the way in delivering high-quality TIG welding equipment and services, industries can rely on this process for precise welds, enhanced productivity, and aesthetic appeal. From automotive to construction and food and beverage sectors, TIG welding mild steel offers a range of applications, making it an invaluable tool for fabricators and manufacturers worldwide.
Essential Tips for Mig Welding Stainless Steel to Mild Steel
The process of welding stainless steel to mild steel using the MIG welding technique has become increasingly popular in the manufacturing and construction industries. This innovative method allows for the joining of dissimilar metals, providing a strong, durable bond that is essential for a wide range of applications.{Company Name} is a leading provider of welding solutions, specializing in MIG welding equipment and accessories. With a strong commitment to quality and innovation, {Company Name} has been at the forefront of developing cutting-edge technologies that cater to the evolving needs of the welding industry.The process of MIG welding stainless steel to mild steel involves the use of a filler material that is compatible with both metals. This filler material is fed through the MIG welding torch, which generates an electric arc to heat and melt the metals, creating a strong bond as the filler material cools and solidifies.One of the primary advantages of MIG welding stainless steel to mild steel is the ability to create a joint that is highly resistant to corrosion and oxidation. This is particularly important in applications where the welded joint is exposed to harsh environmental conditions, such as in the manufacturing of chemical processing equipment or outdoor structures. The resulting weld is also highly durable, with excellent strength and ductility properties, making it suitable for a wide range of load-bearing applications.{Company Name} has developed a range of MIG welding equipment and consumables specifically designed for welding stainless steel to mild steel. These include specialized welding torches, shielding gases, and filler materials that are optimized for achieving high-quality welds with minimal heat input, reducing the risk of distortion and warping in the welded components.In addition to its technical expertise, {Company Name} provides comprehensive training and support services for welders and fabricators looking to adopt the MIG welding process for joining stainless steel to mild steel. This includes on-site training programs, technical support, and access to a network of certified welding professionals who can provide guidance and assistance in achieving the desired weld quality and performance.The ability to MIG weld stainless steel to mild steel opens up new possibilities for manufacturing and construction projects, allowing for the seamless integration of different materials to meet specific design and performance requirements. This is particularly relevant in industries such as aerospace, automotive, and marine engineering, where the demand for lightweight, corrosion-resistant materials is driving the need for advanced welding solutions.{Company Name} is dedicated to pushing the boundaries of what is possible in the field of welding, and its commitment to research and development has led to numerous breakthroughs in MIG welding technology. By offering a comprehensive range of solutions for welding stainless steel to mild steel, {Company Name} is empowering welders and fabricators to take on new challenges and achieve exceptional results in their craft.As the demand for MIG welding stainless steel to mild steel continues to grow, {Company Name} is well-positioned to lead the way with its innovative products, technical expertise, and unwavering commitment to customer satisfaction. With a strong track record of delivering superior welding solutions, {Company Name} is poised to remain a trusted partner for welders and fabricators seeking to elevate their capabilities and achieve outstanding results in their work.
High-Quality CNC Component Parts in China: The Ultimate Guide
China CNC Component Parts Achieves Remarkable Growth and Expands Global ReachChina CNC Component Parts, a leading manufacturer of precision CNC components, has experienced significant growth in recent years and expanded its global reach, solidifying its position as a key player in the industry. With a dedication to innovation, quality, and customer satisfaction, the company has continuously exceeded expectations and set new benchmarks for excellence.Founded in [year], China CNC Component Parts has steadily grown its capabilities and product offerings to meet the evolving needs of a diverse customer base. The company's commitment to investing in advanced technology and talent has allowed it to deliver high-quality products with unmatched precision and efficiency. As a result, China CNC Component Parts has become a trusted partner for a wide range of industries, including automotive, aerospace, medical, and more.One of the driving forces behind China CNC Component Parts' success is its relentless pursuit of excellence in every aspect of its operations. From the selection of raw materials to the final inspection of finished products, the company adheres to the highest standards to ensure the reliability and performance of its components. By utilizing state-of-the-art CNC machining equipment and stringent quality control measures, China CNC Component Parts has earned a reputation for producing parts that meet the most demanding specifications.In addition to its unwavering focus on quality, China CNC Component Parts places great importance on customer satisfaction and collaboration. The company works closely with its clients to understand their unique requirements and provide tailored solutions that address their specific needs. By fostering meaningful partnerships and delivering exceptional service, China CNC Component Parts has established long-lasting relationships with its customers, earning their trust and loyalty.As part of its commitment to continuous improvement and growth, China CNC Component Parts has expanded its global reach to better serve its international clientele. With a well-established network of distribution partners and representatives, the company has been able to extend its presence to new markets and enhance its accessibility to customers worldwide. This strategic expansion has allowed China CNC Component Parts to provide localized support and expedited delivery times, further strengthening its position as a global leader in the industry.Looking ahead, China CNC Component Parts remains focused on driving innovation and pushing the boundaries of what is possible in CNC machining. By staying at the forefront of technological advancements and industry trends, the company is poised to introduce new capabilities and solutions that will continue to raise the bar for precision engineering. With a dedicated team of engineers and experts, China CNC Component Parts is well-equipped to tackle complex challenges and deliver cutting-edge products that exceed expectations.In conclusion, China CNC Component Parts has demonstrated remarkable growth and success, solidifying its position as a premier manufacturer of precision CNC components. Through its unwavering commitment to quality, customer satisfaction, and innovation, the company has established itself as a trusted partner for a wide range of industries and expanded its global reach to better serve its international clientele. As China CNC Component Parts continues to push the boundaries of CNC machining, the future looks bright for the company and its customers alike.
Top CNC Sheet Metal Cutting Techniques for Precision Results
CNC sheet metal cutting is a highly advanced and precise method of cutting metal sheets using computer numerical control technology. This technology allows for accurate and efficient cutting of metal sheets, making it ideal for a wide range of industries such as automotive, aerospace, construction, and manufacturing.With the increasing demand for high-quality sheet metal cutting, the need for advanced and automated cutting technologies has become imperative. This is where the innovative solutions offered by {} come into play.Established in 1998, {} has become a renowned name in the field of sheet metal cutting, thanks to its commitment to delivering cutting-edge solutions and exceptional customer service. The company's dedication to embracing the latest technological advancements has allowed it to stay ahead of the competition and consistently meet the evolving needs of its clients.{} offers a wide range of CNC sheet metal cutting services, including laser cutting, plasma cutting, and waterjet cutting. These services are tailored to meet the specific requirements of each client, ensuring that they receive the highest quality cuts with minimal material waste.The company's state-of-the-art facilities are equipped with the latest CNC machines, which are operated by highly skilled and experienced technicians. This ensures that every cut is precise, accurate, and of the highest quality.One of the key advantages of {} is its ability to handle both small-scale and large-scale projects with equal ease. Whether it's a small prototype or a mass production run, the company has the capacity and expertise to deliver exceptional results within tight deadlines.In addition to its cutting-edge technology and exceptional capabilities, {} is also committed to sustainability and environmental responsibility. The company implements eco-friendly practices in its operations, including the recycling of metal waste and the use of energy-efficient machinery.Furthermore, {} places a strong emphasis on customer satisfaction, striving to exceed client expectations in every project it undertakes. The company works closely with its clients to understand their unique requirements and provide tailored solutions that meet and exceed their expectations.The combination of cutting-edge technology, skilled workforce, commitment to sustainability, and customer-centric approach has made {} a trusted partner for companies across various industries.As the demand for high-quality sheet metal cutting continues to rise, {} remains at the forefront of the industry, constantly pushing the boundaries of what is possible with CNC sheet metal cutting technology. With its unwavering dedication to excellence, innovation, and customer satisfaction, the company is well-positioned to meet the evolving needs of its clients and maintain its leadership in the sheet metal cutting industry.
How to Weld Stainless Steel to Mild Steel: A Comprehensive Guide
Headline: Welding Stainless Steel to Mild Steel: An Innovative Solution by {Company Name}Introduction:{Company Name}, a leading expert in metal fabrication and engineering solutions, has introduced a groundbreaking technique for welding stainless steel to mild steel. With their extensive experience and commitment to innovation, the company has successfully developed a solution that addresses the challenges associated with joining dissimilar metals.Body:1. Understanding the Need for Welding Stainless Steel to Mild Steel: Welding stainless steel to mild steel has been a significant challenge in various industries such as automotive, construction, and manufacturing. Both stainless steel and mild steel offer unique attributes and advantages, but their dissimilarities in terms of composition and physical properties make joining them a complex task. However, the combination of these two metals is often desirable to strike a balance between strength, corrosion resistance, and cost-effectiveness.2. The Innovative Solution: {Company Name} has invested substantial resources in research and development to devise an effective technique for welding stainless steel to mild steel. This pioneering approach involves using advanced filler metals and welding processes that ensure a robust and durable bond between the dissimilar materials.3. Comprehensive Material Analysis: Before combining stainless steel and mild steel, {Company Name} conducts a detailed analysis of both metals to determine the most suitable welding method. Factors such as composition, mechanical properties, and intended application are thoroughly assessed to optimize the welding process.4. Advanced Filler Metals: One of the key elements in successfully welding stainless steel to mild steel is the selection of appropriate filler metals. {Company Name} utilizes state-of-the-art filler metals that have been specifically designed for joining dissimilar metals. These specialized fillers possess excellent wetting and spreading characteristics, ensuring a strong bond and minimizing the risk of material failure.5. Tailored Welding Processes: {Company Name}'s team of skilled welders utilizes tailored welding processes to ensure optimal results when combining stainless steel and mild steel. Whether it be TIG (Tungsten Inert Gas) welding, MIG (Metal Inert Gas) welding, or other advanced techniques, the company's experts possess the expertise to choose the most suitable method for each unique welding project.6. Quality Control: {Company Name} is committed to delivering exceptional quality in every welding project. Stringent quality control measures are implemented throughout the welding process, including thorough inspections, non-destructive testing, and adherence to internationally recognized standards. This ensures that the welded stainless steel to mild steel joints meet or exceed industry requirements.7. Advantages and Applications: The innovative welding solution offered by {Company Name} presents numerous advantages to industries requiring the combination of stainless steel and mild steel. These advantages include enhanced strength, improved corrosion resistance, cost-effectiveness, and greater design flexibility. Such benefits make this technique ideal for applications in automotive manufacturing, construction, shipbuilding, and various other sectors.Conclusion:{Company Name}'s groundbreaking technique for welding stainless steel to mild steel opens a new realm of possibilities for industries seeking to combine the advantages of these two dissimilar metals. With their expertise, advanced filler metals, and tailored welding processes, the company ensures robust bonds, exceptional quality, and unmatched customer satisfaction. This innovative solution serves as a testament to {Company Name}'s commitment to pushing the boundaries of metal fabrication and engineering.