Discover the Latest Trends in Welding and Metal Fabrication
By:Admin
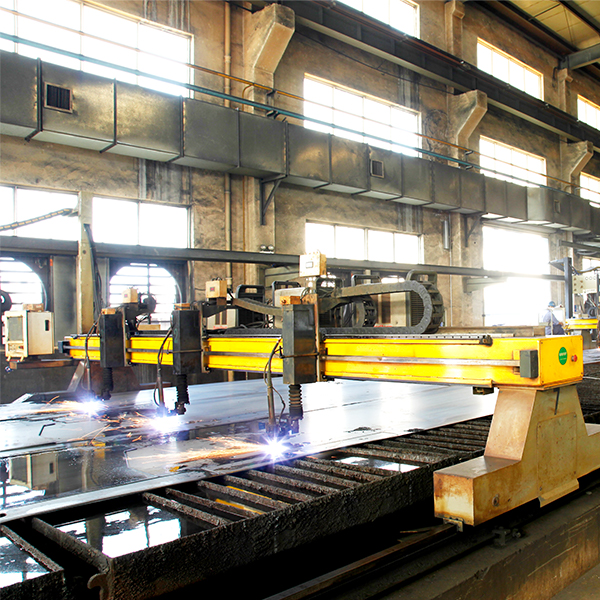
Introduction [Company Introduction: Remove brand name]
[Company Name], a renowned leader in the welding and metal fabrication industry, has consistently set new benchmarks through its innovative solutions and cutting-edge technologies. With a firm dedication towards quality and customer satisfaction, [Company Name] has revolutionized the sector and helped shape modern-day welding and metal fabrication practices. Through its unwavering commitment to excellence, it continues to drive advancements that redefine the industry's landscape.
Body:
1. History of Welding and Metal Fabrication:
Welding and metal fabrication have been integral to human civilization for centuries. From ancient blacksmiths shaping metal to modern-day industries constructing intricate structures, the art of welding and metal fabrication has undergone remarkable transformations. Over time, various techniques and equipment have evolved, allowing for stronger, more durable, and complex welds.
2. The Role of [Company Name] in Advancing the Industry:
[Company Name] has played a pivotal role in propelling the welding and metal fabrication industry forward through its relentless pursuit of innovation and excellence. By investing in research and development, [Company Name] has introduced groundbreaking techniques and technologies that have redefined the industry's capabilities.
3. Cutting-Edge Welding and Metal Fabrication Technologies:
[Company Name] has consistently pioneered modern welding and metal fabrication technologies, ensuring enhanced efficiency and precision in various applications. Some notable advancements introduced by [Company Name] include:
a. Laser Welding: [Company Name]'s revolutionary laser welding technology enables precise and high-speed welding, minimizing deformation and increasing productivity. The precise control offered by this technique ensures superior quality welds in various materials.
b. Robotic Welding: By incorporating robotic welding systems, [Company Name] has revolutionized productivity and accuracy in metal fabrication. These systems offer a level of consistency and repeatability that human operators find hard to match, resulting in impeccable weld quality and increased output.
c. CNC Plasma Cutting: [Company Name]'s CNC plasma cutting technology enables precise and efficient metal cutting, ensuring faster turnaround times and reduced material waste. This technology enables intricate designs to be translated flawlessly, expanding the possibilities for creative metal fabrication.
4. Advancements in Materials and Metallurgy:
[Company Name] has also focused on advancements in materials and metallurgy to cater to evolving industry needs. By harnessing innovative alloys and metals, [Company Name] has expanded the range of possible welding and fabrication applications. This includes developing high-strength materials suitable for demanding environments, as well as alloys specifically tailored for lightweight structures.
5. Commitment to Safety and Sustainability:
[Company Name] places great emphasis on safety and sustainability in welding and metal fabrication practices. It actively promotes the use of environmentally friendly processes, such as minimization of waste and pollution, as well as the adoption of safe welding procedures. By prioritizing sustainability, [Company Name] ensures a cleaner and greener future for the industry.
Conclusion:
As a frontrunner in the welding and metal fabrication industry, [Company Name] has consistently pushed the boundaries of what is possible. Through its relentless dedication to innovation, it has redefined the sector with groundbreaking technologies, materials, and safety practices. By setting new benchmarks, [Company Name] continues to shape the future of welding and metal fabrication, ensuring a more efficient, sustainable, and advanced industry for years to come.
Company News & Blog
Key Considerations for Choosing the Right Welding Techniques for Structural Projects
Structural Weld, a leading global provider of welding solutions has announced a new line of products which will enable manufacturers to improve efficiency while reducing downtime and production costs. The new product line, which includes welding equipment, consumables, and accessories, is designed to meet the growing demand for high-quality welding solutions for various applications.For over three decades, Structural Weld has established itself as a reputable provider of welding solutions across various industries, including fabrication, petrochemical, oil and gas, power generation, marine and offshore. The company has built a reputation for offering innovative and cost-effective welding solutions to meet the unique needs of its customers.Structural Weld's new product line is a result of the company's continued commitment to innovation and providing high-quality welding solutions to its customers. The new line of products features state-of-the-art welding equipment equipped with advanced technology to offer superior performance, speed, and accuracy. Customers can choose from a variety of welding machines, including MIG, TIG, stick welding, and plasma cutting machines.The company has also developed a range of welding consumables that are specifically designed to complement its welding machines. The welding consumables, which include electrodes, filler wires, and flux-cored wires, are manufactured to the highest quality standards to ensure that they deliver exceptional performance and reliability.In addition to the welding equipment and consumables, Structural Weld has also added a range of welding accessories to its product line. The welding accessories, which include welding helmets, gloves, and safety glasses, are designed to provide maximum comfort and protection to welders while they work. The company has also introduced a range of welding carts and plasma cutting tables to help welders transport and set up their welding equipment easily.Structural Weld's new product line is expected to provide significant benefits to manufacturers across various industries. The welding equipment is designed to reduce downtime and increase efficiency, allowing manufacturers to produce high-quality products at a faster rate. The welding consumables and accessories are also expected to help manufacturers reduce material waste, minimize defects, and improve overall productivity."While we have always been committed to providing our customers with high-quality welding solutions, our new product line represents a significant milestone for our company," said the Structural Weld spokesperson. "We are confident that our new line of products will help our customers improve their welding processes significantly and ultimately boost their bottom line."With its new product line, Structural Weld is poised to continue its growth trajectory by expanding its market reach and attracting new customers. The company's commitment to innovation, quality, and customer satisfaction has been at the forefront of its success, and this new product line is a testament to its enduring commitment to provide the best welding solutions to its customers.In conclusion, Structural Weld's new product line is a welcome development for manufacturers across various industries. With its state-of-the-art welding equipment, high-quality consumables, and innovative accessories, the company is well-positioned to provide cost-effective solutions that meet the unique needs of its customers. As the company continues to grow, it is clear that its commitment to innovation, quality, and customer satisfaction will continue to be the driving force behind its success.
Welding Techniques for Joining Stainless Steel and Mild Steel - Available for Sale in China
Welding stainless steel and mild steel together is a challenging task. It requires expertise, precision and high-quality equipment. The process involves joining two materials with different chemical and mechanical properties, which can lead to cracking, distortion and other issues if not done correctly. In this blog, we will explore the process of welding mild steel to stainless steel and some of the challenges that come with it.First, let's look at the materials themselves. Stainless steel has a high chromium content, which makes it resistant to corrosion and stains. It is also harder and more brittle than mild steel, which is why it is challenging to weld the two materials together. Mild steel, on the other hand, has a lower carbon content, making it more ductile and easier to work with when compared to stainless steel.When welding stainless steel to mild steel, there are several methods to consider. Let's take a closer look at some of the most popular welding techniques.1. TIG (Tungsten Inert Gas) Welding: This is one of the most popular welding techniques used in welding stainless steel to mild steel. It provides a precise, clean and high-quality weld, making it ideal for applications that require a high degree of accuracy.2. MIG (Metal Inert Gas) Welding: This is a more straightforward technique compared to TIG welding. It is faster, easier to learn and produces a durable weld. However, the quality of the weld is lower than TIG welding, which may not be suitable for high-end applications.3. Stick Welding: This is a versatile welding method that can be used to weld different materials. It produces a rugged and robust weld that can withstand high temperatures, making it ideal for industrial applications.Regardless of the welding technique used, welding stainless steel to mild steel requires proper preparation. The surface must be clean, free of rust, oil and other contaminants that can affect the quality of the weld. Additionally, the two metals must be preheated to ensure that the thermal stresses are minimized during the welding process.One of the biggest challenges when welding stainless steel to mild steel is the difference in melting points. Stainless steel has a much higher melting point than mild steel, which means that it can easily warp or crack if the welder is not careful. Hence, it is crucial to use specialized welding techniques and equipment to ensure that the two materials are welded together properly without cracking or distortion.In conclusion, welding stainless steel to mild steel can be a daunting task, but it is possible with the right skills, tools, and techniques. With proper preparation and welding processes, it is possible to achieve a strong and durable weld between the two materials. If you need more information on welding stainless steel to mild steel or other welding-related topics, please feel free to reach out to our team of experts.
Tips for Welding Stainless Steel for a Restaurant Steamer Tank Exposed to Heat
Welding stainless steel can be a challenging task, especially when it comes to repairing equipment that is constantly exposed to heat, such as a steamer tank in a restaurant. If you have been struggling to fix your stainless steel steamer tank and are getting frustrated with recurring leaks, it might be time to reconsider your repair techniques.One common mistake that people make when attempting to repair stainless steel is using adhesives like JB Weld. While JB Weld is known for its strength and versatility, it is not the ideal solution for repairing stainless steel. Adhesives like JB Weld lack the durability and temperature resistance required for withstanding the extreme conditions that stainless steel equipment in a restaurant setting endures.To effectively repair your stainless steel steamer tank, you need to consider welding as a more reliable solution. Welding provides a strong and permanent bond by joining separate metal pieces together using heat and pressure. When it comes to welding stainless steel, there are several techniques you can employ, such as TIG (Tungsten Inert Gas) welding, MIG (Metal Inert Gas) welding, and spot welding. However, TIG welding is often recommended for stainless steel due to its ability to provide precise and high-quality welds.Before attempting to weld your stainless steel steamer tank, it is crucial to prepare the surface properly. Stainless steel welding requires a clean and contamination-free surface, so make sure to remove any dirt, rust, or previous failed repair attempts. You can use a grinder or sanding tools to clean the surface and ensure a smooth and consistent finish.Once the surface is prepared, it is time to start the welding process. TIG welding stainless steel involves using a tungsten electrode to create an electric arc that generates extreme heat. This heat melts the stainless steel surface, allowing the filler material to be added to create a strong weld joint. It is important to choose the appropriate filler material that matches the stainless steel grade you are working with. Additionally, it is recommended to utilize a shielding gas such as argon or helium to protect the weld area from oxidation and prevent contamination.When welding the stainless steel steamer tank, ensure that you have the proper safety equipment, such as a welding helmet, gloves, and protective clothing. Safety should always be a priority when working with welding equipment and high temperatures.In order to prevent future leaks, it is crucial to pay attention to the welding technique and ensure a solid weld. Proper cleaning and preparation of the surface, precise heat control, and correct filler material selection are key factors in achieving a successful weld. It is also important to thoroughly inspect the weld joint after completing the repair to ensure its integrity.In conclusion, when it comes to repairing a stainless steel steamer tank in a restaurant setting, relying on adhesives like JB Weld may not provide a long-lasting solution. Welding stainless steel using techniques like TIG welding is a more reliable option. By properly preparing the surface, selecting the appropriate filler material, and employing proper welding techniques, you can achieve a strong and leak-free repair. Remember to prioritize safety during the welding process and conduct thorough inspections to ensure the quality of the weld.
Welding and Fabrication: Key Factors to Consider for Your Next Project
[Company Name], a Leading Player in the Metal and Fabrication Industry[City, Date] - [Company Name], an industry leader in metal and fabrication services, continues to drive innovation and raise the bar in the industry. With a commitment to excellence and customer satisfaction, the company has quickly become a trusted name in metal fabrication solutions.Established on the principles of quality, precision, and efficiency, [Company Name] has spent years focusing on developing its capabilities in metal and fabrication. Specializing in custom-designed metal products, the company caters to a diverse range of industries, including automotive, aerospace, construction, and more.At the core of [Company Name]'s success is its cutting-edge technology and state-of-the-art manufacturing processes. The company's facility is equipped with advanced machinery and tools, enabling the team of highly skilled technicians to deliver superior quality products that meet stringent industry standards.In addition to its commitment to quality, [Company Name] takes pride in its dedication to customer satisfaction. The company works closely with its clients to understand their specific requirements and collaborates with them throughout the production process to ensure the final product exceeds expectations.One of the key differentiators for [Company Name] is its highly knowledgeable and experienced team. The company's engineers and technicians possess a deep understanding of various metals and their unique properties, enabling them to develop tailor-made solutions for each client's needs. Whether it's fabricating intricate components or undertaking large-scale metal structures, [Company Name]'s team consistently delivers outstanding results.Furthermore, [Company Name] places a strong emphasis on sustainability and environmental responsibility. The company actively seeks ways to minimize its ecological footprint by adopting eco-friendly practices and implementing efficient waste management systems.With its strong foothold in the market, [Company Name] has successfully completed numerous projects of varying complexities. The company has a proven track record in delivering projects on time and within budget, making it the ideal partner for both small-scale and large-scale ventures.Looking toward the future, [Company Name] plans to continue pushing the boundaries of innovation in the metal and fabrication industry. The company invests heavily in research and development, exploring new techniques and technologies to further enhance its offerings.Additionally, [Company Name] intends to expand its presence in both domestic and international markets. With a growing customer base and a solid reputation, the company aims to become a global leader in metal and fabrication solutions.As [Company Name] strives for excellence, it remains committed to upholding its core values of quality, precision, and customer satisfaction. The company's unwavering dedication to its craft and its ability to adapt to changing market demands solidify its position as a significant player in the metal and fabrication industry.About [Company Name]:[Company Name] is a leading provider of metal and fabrication solutions, specializing in custom-designed metal products for clients across various industries. With a commitment to quality, innovation, and customer satisfaction, the company has established itself as a trusted name in the market. Backed by advanced technology and a highly skilled team, [Company Name] continually delivers superior results for its clients. For more information, visit www.companywebsite.com.Contact:[Company Name]Address: [Company Address]Phone: [Company Phone Number]Email: [Company Email]
Essential Equipment in TIG Welding: Advantages and Applications
Title: TIG Welding Equipment Revolutionizing Precision Welding: A Game Changer for Critical ApplicationsIntroduction:TIG (Tungsten Inert Gas) welding, an advanced welding technique that utilizes an inert gas shield instead of a slag to protect the weld pool, has emerged as a highly attractive alternative to gas and manual metal arc welding. This technology has played a pivotal role in the acceptance of high-quality welding in critical applications. Among the leading companies in the industry, (name of the company) has established itself as a prominent player in supplying essential TIG welding equipment. Their commitment to innovation and expertise in TIG welding steel have revolutionized the welding industry. This article will delve into the significance of TIG welding equipment and how it has transformed precision welding.The Advantages of TIG Welding Equipment:TIG welding equipment offers numerous advantages that have propelled its rise in popularity in critical applications. One of its key advantages lies in the inert gas shield used, which eliminates the need for a slag, resulting in cleaner and more precise welds. This technique allows for increased control over the welding process, ensuring minimal distortion and reduced spattering. With TIG welding, the welder can easily regulate the heat input, making it ideal for welding thin materials. Moreover, the absence of slag facilitates easier post-weld cleaning, minimizing time and effort required for finishing.Another significant advantage of TIG welding equipment is its ability to achieve high-quality welds. The process employs a non-consumable tungsten electrode, which retains its shape and does not melt during the welding process. This characteristic enhances the welder's precision, resulting in aesthetically appealing and durable welds. Moreover, the ability to work with a wide range of materials, including stainless steel, aluminum, and copper, further highlights the versatility and superiority of TIG welding equipment.Promoting Safety and Efficiency with TIG Welding Equipment:Apart from its technical benefits, TIG welding equipment also prioritizes safety and efficiency. The process utilizes an electric foot pedal, granting the welder precise control over the heat input and filler rod. This level of control reduces the risks of overheating, burn-throughs, and other imperfections. Additionally, the precise control enables welders to create intricate and detailed welds with ease, making TIG welding equipment highly popular in industries that demand exceptional precision, such as aerospace, automotive, and medical equipment manufacturing.The Role of (Company Name) in Advancing TIG Welding Steel:In this realm of TIG welding equipment, (Company Name) has established a commendable reputation for delivering high-quality products and exceptional service. With their commitment to continuous innovation and expertise in TIG welding steel, the company has played a pivotal role in promoting the acceptance and adoption of TIG welding in critical applications.(Company Name) offers a comprehensive range of TIG welding equipment, including state-of-the-art power sources, torches, and consumables. Their equipment is designed to provide welders with superior control, exceptional arc stability, and unmatched reliability. Leveraging advanced technologies, (Company Name) ensures that their TIG welding equipment optimizes weld quality, productivity, and safety.Conclusion:TIG welding equipment has transformed the welding industry, presenting an attractive alternative to traditional welding techniques. With its numerous advantages, including cleaner welds, increased control over heat, and the ability to work with various materials, TIG welding equipment has become indispensable in critical applications. Notably, (Company Name) has significantly contributed to the advancement of TIG welding, ensuring the highest quality welds for industries requiring precision and durability. Continuous innovation and expertise in TIG welding steel have firmly established (Company Name) as a leader in the field, empowering welders and revolutionizing the welding industry as a whole.
Professional Tube Bending and Rolling Services for Various Materials
Aluminum Bending Services Meet Growing Demands for Customized FabricationIn response to the increasing demand for specialized fabrication solutions, industry-leading tube bending and rolling experts have expanded their services to include aluminum bending. As aluminum continues to gain popularity in a wide range of industries, these specialized services offer a cost-effective and efficient solution for creating custom-designed products and structures.MetzFab, a renowned provider of tube bending and rolling services, has recently expanded its capabilities to include aluminum bending. With their expertise and state-of-the-art equipment, MetzFab is now capable of working with a variety of materials, including steel, stainless steel, and aluminum.Aluminum has become a sought-after material for its exceptional versatility, strength, and lightweight properties. It is widely used across a range of industries, including aerospace, automotive, construction, and marine, to name just a few. By offering aluminum bending services, MetzFab is dedicated to meeting the ever-growing demands of these industries and providing them with customized fabrication solutions.MetzFab's aluminum bending services utilize advanced bending machinery and techniques to create precise and complex shapes. The company's skilled technicians are experienced in handling the unique properties of aluminum, ensuring high-quality results and minimizing material waste. Whether it's a simple bend or a complex multi-plane shape, MetzFab's aluminum bending services can meet the needs of any project.One of the key advantages of aluminum bending services is the cost-effectiveness it offers compared to traditional fabrication methods. With the ability to create intricate shapes and designs, aluminum bending reduces the need for additional parts and assembly, resulting in significant cost savings. Additionally, aluminum's lightweight nature reduces transportation costs and makes it easier to handle during installation.MetzFab's aluminum bending services also offer exceptional durability and corrosion resistance. Aluminum naturally forms a protective oxide layer, making it highly resistant to rust and corrosion. This makes it an ideal choice for outdoor applications and industries that require high strength and longevity. With their precise bending techniques, the company ensures that the integrity of the aluminum is maintained, providing customers with long-lasting and reliable products.The versatility of aluminum bending extends to a wide range of applications. In the aerospace industry, aluminum's lightweight properties are crucial for reducing fuel consumption and increasing aircraft efficiency. MetzFab's aluminum bending services can create intricate shapes for aircraft frames, fuselages, and other components, ensuring optimal performance and safety.In the automotive sector, aluminum bending enables the production of lightweight and fuel-efficient vehicles. By reducing the weight of car bodies and structures, manufacturers can improve fuel economy without compromising safety. MetzFab's aluminum bending services can contribute to this industry's goal of sustainability and environmental responsibility.In the construction and architectural industries, aluminum bending allows for the creation of unique and aesthetically pleasing structures. From curved facades to custom-designed staircases, aluminum bending provides architects and designers with unparalleled creative possibilities. MetzFab's expertise in aluminum bending ensures that these structures are not only visually appealing but also structurally sound.MetzFab's expansion into aluminum bending services highlights their commitment to meeting the changing needs of various industries. With their expertise, state-of-the-art equipment, and dedication to quality, they are well-positioned to provide customized fabrication solutions that meet and exceed customer expectations. Whether it's steel, stainless steel, or aluminum, MetzFab's tube bending and rolling services are a reliable choice for all materials.
Fast and High-Quality Metal Sheet Laser Cutting Services for Stainless Steel and Aluminum – Request a Free Quote
Steel Laser Cutting Service: Efficient and Precise Metal CuttingLaser cutting has been becoming increasingly popular in the metal cutting industry due to its precision and efficiency. This advanced technology uses a laser beam to cut and shape metal sheets, stainless steel, and aluminum with high accuracy and speed. It offers significant advantages over traditional metal cutting methods such as sawing, shearing, and plasma cutting. In this article, we will discuss the benefits of steel laser cutting service and why you should consider this method for your next metal cutting project.Accurate and Precise CutsOne of the biggest advantages of laser cutting is its accuracy and precision. With laser technology, you can achieve a high level of precision and control over the cutting process. This precision enables you to produce intricate and complex shapes with ease, which is not possible with traditional cutting methods. Laser cutting also ensures clean and smooth edges, minimizing the need for secondary processing or finishing.Fast and EfficientLaser cutting is also known for its speed and efficiency. The laser beam can cut through metal sheets quickly, reducing the processing time required for each sheet. This efficiency is particularly beneficial for high-volume manufacturing or large-scale projects, where you need to produce a large amount of metal parts or components in a short amount of time.Reduced Material WasteLaser cutting also helps to minimize material waste. Unlike traditional cutting methods, laser cutting offers a more precise and accurate cutting method, reducing the amount of material waste. This also means that you can save money on materials and reduce your environmental footprint.VersatilityWith laser cutting technology, you can cut and shape a variety of materials, including stainless steel, aluminum, copper, brass, and more. This versatility allows you to utilize the same equipment for different metal cutting projects, making it easier to streamline your manufacturing processes and reduce costs.Customizable and FlexibleLaser cutting is a highly customizable and flexible process. You can create custom designs and shapes to meet your specific requirements. Whether you need components for industrial machinery, decorative metal art, or architectural elements, laser cutting can deliver the exact shapes and sizes you need.ConclusionOverall, steel laser cutting service is an efficient and precise method for cutting and shaping metal sheets. With advanced laser technology, you can achieve accuracy, speed, and versatility in metal cutting and manufacturing processes. Whether you’re working on a large-scale project or a custom design, laser cutting can help you meet your metal cutting needs while saving time and money. If you’re interested in utilizing our laser cutting services, feel free to contact us for a free quote.
Laser Cut Cutting: A Revolutionary Technique for Precision Designs
Laser Cut Cutting Revolutionizes Manufacturing ProcessesIn today's rapidly evolving world, technology continues to redefine the way we live and work. One such innovation that has transformed traditional manufacturing processes is laser cut cutting. With its precision and efficiency, laser cut cutting has revolutionized industries and companies around the globe.Laser cut cutting, as the name suggests, involves the use of a high-powered laser beam to precisely cut or engrave various materials, including metal, plastic, wood, and even fabric. The laser beam is directed onto the surface of the material, creating a localized heat zone that vaporizes or melts the material, resulting in a clean and accurate cut.The advantages of laser cut cutting are manifold. Firstly, it offers unparalleled precision and accuracy. Laser technology allows for incredibly fine cuts and intricate detailing that would be impossible to achieve using traditional cutting methods. This level of precision has opened up endless possibilities for design and fabrication in various industries, including automotive, aerospace, electronics, and jewelry.Furthermore, laser cut cutting is an incredibly fast and efficient process. The laser beam operates at high speeds, allowing for rapid cutting and increased productivity. Additionally, laser cutting does not require any physical contact with the material, eliminating the risk of mechanical damage or contamination. This aspect makes it particularly valuable for fragile materials or intricate designs.Another key advantage of laser cut cutting is its versatility. The laser beam can be guided by computer-controlled software, enabling it to cut and engrave intricate patterns, shapes, and even 3D designs. This versatility allows for customization and personalization in product manufacturing, catering to individual customer preferences and demands.One company that has harnessed the power of laser cut cutting for their manufacturing processes is {}. Established in {}, the company has become a leading player in the industry, offering a wide range of laser cutting services to a diverse customer base.Specializing in the fabrication of metal products, {} has integrated laser cut cutting into every aspect of their manufacturing operations. With state-of-the-art laser cutting machines and highly skilled technicians, the company has consistently delivered high-quality products to their clients, meeting the most demanding specifications.The implementation of laser cut cutting has not only enhanced the precision and efficiency of {}'s manufacturing processes but has also improved their overall customer experience. With the ability to easily customize designs and quickly produce prototypes, the company has been able to accommodate unique customer requests and deliver innovative solutions.Moreover, {}'s commitment to sustainable practices is further reinforced by laser cut cutting. As a non-contact process, laser cutting generates minimal waste and uses significantly less energy compared to traditional methods. This reduction in material waste and energy consumption aligns with the company's mission to minimize its environmental footprint and promote sustainability within the industry.Looking ahead, laser cut cutting is poised to continue shaping the future of manufacturing. As technology advances and becomes more accessible, more industries will adopt laser cutting techniques to streamline their production processes and remain competitive in the global market.In conclusion, laser cut cutting has revolutionized manufacturing by offering precision, efficiency, versatility, and customization. Companies like {} have embraced this technology, leveraging its advantages to deliver high-quality products and enhance customer satisfaction. With its endless possibilities and continual advancements, laser cut cutting is undeniably the future of manufacturing.
Key Tips for Structural Steel Welding to Ensure Strong and Reliable Connections
Structural Steel Welding: A Crucial Process in ConstructionIntroduction:Structural steel welding plays a critical role in the construction industry, ensuring the durability and stability of buildings, bridges, and other infrastructure projects. By joining pieces of steel together using specialized welding techniques, construction professionals can create strong and reliable structures capable of withstanding a range of challenging conditions.Steel is one of the most commonly used materials in construction due to its exceptional strength and durability. However, to harness its full potential, steel requires welding to create a solid and integrated structure. Many construction companies have utilized advanced welding processes and technologies to ensure the highest level of quality and safety in steel structures being built.The Importance of Structural Steel Welding:Structural steel welding is vital for several reasons. Firstly, it ensures the integrity of the structure by effectively joining steel beams, columns, and plates. Welding provides a secure connection that allows the load-bearing capacity of the steel to be maximized, making it an essential component in the construction industry.Additionally, welding enables architects and engineers to design complex and innovative structures. It allows for the creation of artistic and unique designs that may not be achievable with other construction materials. The flexibility and versatility of welding make it possible to construct intricate steel shapes, giving architects the freedom to explore their creativity while maintaining structural integrity.Moreover, structural steel welding ensures the longevity of a building or infrastructure project. By creating a solid bond between steel components, welding minimizes the risk of structural failure, enhancing the durability and lifespan of the structure. This is particularly crucial in high-demand sectors such as bridges, where welding plays a significant role in maintaining safety standards and preventing catastrophic accidents.Advanced Welding Technologies:In recent years, significant advancements have been made in welding techniques and technologies. These advancements have brought immense benefits to the construction industry, allowing for more efficient and precise welding processes.One notable technological development is the introduction of automated welding systems. These systems utilize robotics and computer-controlled machinery to perform welding tasks with higher precision and consistency. Automated welding not only reduces labor costs but also minimizes human error, resulting in stronger and more reliable welds.Furthermore, the emergence of laser welding has revolutionized the field of structural steel welding. Laser welding offers several advantages such as faster welding speeds, reduced heat input, and improved weld quality. It enables construction companies to achieve high-quality welds in less time, enhancing productivity without compromising on safety or durability.Safety and Quality Assurance:When it comes to structural steel welding, safety and quality assurance are paramount. Construction companies must adhere to strict industry standards and regulations to ensure the integrity of the welds and, ultimately, the entire structure.Inspection and quality assurance processes play a crucial role in verifying the quality of welds. Non-destructive testing methods, such as ultrasonic testing and X-ray inspection, are commonly employed to detect any potential defects in the welded joints. By identifying these defects early on, necessary repairs and modifications can be made, guaranteeing the reliability and safety of the structure.Moreover, certified welders with specialized training and skills are essential for executing structural steel welding. These professionals understand the complexities of different welding techniques and materials, ensuring that the welds meet the required strength and durability standards.Conclusion:Structural steel welding is an indispensable process in the construction industry, providing strength, durability, and safety to structures of all kinds. The advancements in welding technologies have significantly contributed to enhanced efficiency, precision, and overall project quality. However, it is crucial that construction companies prioritize safety and quality assurance through thorough inspection and employing certified welders. By doing so, they can ensure the longevity and reliability of the structures they build.
Key Information on Choosing the Right Welding Electrode for Your Project
Title: Revolutionary Welding Electrode Innovates the Industry - Improving Efficiency and QualityIntroduction:In the ever-evolving world of welding technology, companies are continuously seeking new advancements to enhance efficiency and quality. In line with this demand, {Company Name}, a renowned industry leader, has introduced an innovative welding electrode that promises to revolutionize the field. This welding electrode, which boasts incredible capabilities, is set to transform welding processes, streamline operations, and deliver exceptional results like never before.Company Overview:{Company Name}, a well-established welding solutions provider, has a rich history of delivering cutting-edge products. With a commitment to quality and continuous innovation, the company has become a trusted partner for various industries, including automotive, construction, oil and gas, and manufacturing. Their team of skilled engineers and technicians work diligently to develop advanced welding technologies that address industry challenges and meet customer needs.Revolutionary Welding Electrode:The latest offering from {Company Name}, which we shall refer to as the "Advanced Welding Electrode," is the result of years of research and development. This innovative product is designed to enhance welding operations by improving efficiency, productivity, versatility, and overall welding quality.Improved Efficiency and Productivity:The Advanced Welding Electrode incorporates state-of-the-art features that significantly improve efficiency and productivity. Its enhanced coating formulation ensures smooth and steady arc stability, resulting in reduced spatter and welding defects. This attribute greatly decreases post-welding clean-up time, allowing welders to operate more efficiently and complete projects in a shorter duration.Moreover, the electrode's excellent heat dissipation properties minimize the risk of overheating, reducing downtime due to material damage and equipment failure. This feature, combined with its exceptional tie-in wetting ability, ensures seamless fusion between metals, maximizing welding productivity and minimizing waste.Enhanced Versatility and Adaptability:{Company Name}'s Advanced Welding Electrode offers superior adaptability to a wide range of welding scenarios. It is suitable for various metals, including carbon steel, stainless steel, and non-ferrous alloys. This versatile electrode performs exceptionally well in all welding positions, allowing welders to work with ease and confidence while maintaining high-quality standards.Additionally, the electrode's unique self-releasing slag formula improves welder visibility during the welding process. This enhancement promotes precise control and accuracy, resulting in meticulously welded joints, especially in complex and intricate welding projects.Uncompromised Welding Quality:The focus on welding quality is evident in every aspect of the Advanced Welding Electrode. Its remarkable arc stability, combined with minimal spatter and excellent slag control, ensures clean and smooth welds with minimal defects. This remarkable weld integrity is further reinforced by the electrode's ability to eliminate undesirable elements like sulfur and phosphorus, guaranteeing welds of exceptional quality and longevity.Moreover, {Company Name} has implemented rigorous quality control processes to guarantee consistent electrode performance. The company subjects each electrode batch to comprehensive testing, including tensile strength, elongation, and impact toughness assessments. This dedication to quality assurance provides customers with utmost confidence in the product's reliability and performance.Conclusion:{Company Name}'s introduction of the Advanced Welding Electrode is poised to create a significant impact in the welding industry. With its advanced features, enhanced efficiency and productivity, versatility, and unwavering commitment to welding quality, this revolutionary electrode presents unmatched benefits for welders across various industries.As {Company Name} continues to innovate and provide cutting-edge solutions, the Advanced Welding Electrode is a testament to their dedication towards empowering welders and revolutionizing the welding industry. The progressive strides made by {Company Name} demonstrate their commitment to meeting the evolving needs of the market while ensuring sustainable success for their customers.