Dissimilar Metals Tig Welding: A Guide for Success
By:Admin
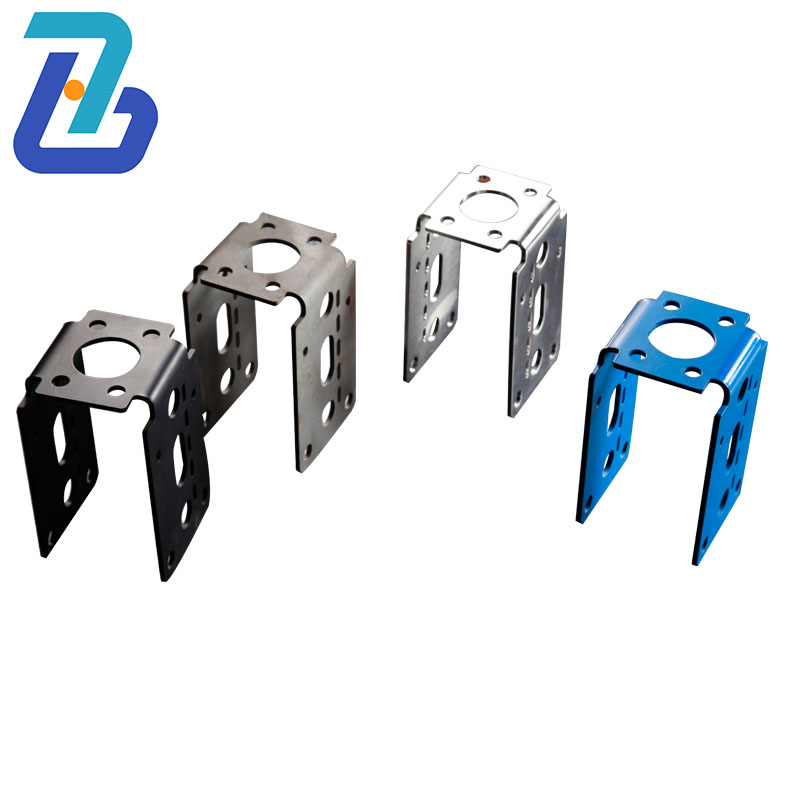
The welding industry has seen significant advancements in recent years, particularly in the field of Tig welding of dissimilar metals. This technological development has enabled welders to join different types of metals together, resulting in enhanced strength and durability of welded components.
One company at the forefront of this cutting-edge welding technology is {}. With decades of experience in the welding industry, {} has established itself as a leading provider of high-quality welding solutions for a wide range of applications. The company's commitment to innovation and continuous improvement has contributed to its success in the highly competitive welding market.
The process of Tig welding dissimilar metals involves the use of a non-consumable tungsten electrode to create the weld. This method offers several advantages over traditional welding processes, including improved control over the welding arc, reduced spatter, and a higher quality weld with minimal distortion. Additionally, Tig welding is suitable for a variety of metals, including stainless steel, aluminum, copper, and titanium, making it a versatile and efficient welding technique.
One of the key benefits of Tig welding dissimilar metals is the ability to join metals with different physical properties, such as thermal conductivity and coefficient of expansion. This is particularly advantageous in industries where components are subjected to extreme temperatures and conditions, as it ensures a strong and reliable weld that can withstand the demands of the application.
Furthermore, the use of Tig welding for dissimilar metals has opened up new possibilities for the manufacturing of complex and intricate components. By enabling the welding of different metal alloys, {} has created opportunities for the production of hybrid components that offer superior performance and longevity.
In addition to its expertise in Tig welding dissimilar metals, {} is renowned for its dedication to quality and precision in all aspects of its welding services. The company's team of highly skilled welders and technicians undergo rigorous training to ensure the highest standards of craftsmanship and workmanship. This commitment to excellence has earned {} a reputation for delivering superior welding solutions that meet the specific requirements of its customers.
Moreover, {} is equipped with state-of-the-art welding equipment and technologies, allowing the company to handle a wide range of welding projects, from small-scale precision welding to large-scale fabrication. The company's investment in advanced welding machinery demonstrates its commitment to staying at the forefront of welding technology and meeting the evolving needs of its clients.
As a leader in the welding industry, {} has consistently demonstrated its ability to adapt to emerging trends and technologies. The company's proactive approach to embracing Tig welding of dissimilar metals underscores its dedication to providing innovative and reliable welding solutions to its customers.
In conclusion, the advancements in Tig welding dissimilar metals have revolutionized the welding industry, offering enhanced strength and durability for a wide range of applications. With its expertise in this cutting-edge welding technology, combined with its dedication to quality and precision, {} is well-positioned to continue leading the way in delivering superior welding solutions for its clients. As the demand for high-quality welding services continues to grow, {} remains committed to remaining at the forefront of the industry, driving innovation and excellence in the field of welding.
Company News & Blog
Efficient and Precise Sheet Metal Laser Cutting Services for Your Business
Sheet metal laser cutting technology has revolutionized the manufacturing industry, enabling precise and efficient cutting of various metal materials. This innovative technology has been widely adopted by companies across the globe to enhance their manufacturing processes and produce high-quality products. With the increasing demand for precision-cut sheet metal components, the need for advanced cutting techniques has become more apparent, leading to the widespread adoption of laser cutting technology.One company at the forefront of sheet metal laser cutting is {}. With state-of-the-art facilities and a team of experienced professionals, {} has successfully integrated laser cutting technology into its manufacturing processes, allowing for the production of intricate and precise sheet metal components. The company has always been committed to staying ahead of the curve when it comes to adopting advanced manufacturing technologies, and its investment in sheet metal laser cutting is a testament to this commitment.Sheet metal laser cutting involves using a high-powered laser to cut through flat sheet metal materials with extreme precision. This process is highly efficient and produces minimal waste, making it an environmentally friendly and cost-effective cutting solution. Laser cutting technology also allows for the creation of complex shapes and designs that would be difficult to achieve with traditional cutting methods. By utilizing this advanced technology, companies like {} can offer their customers a wider range of design possibilities for their sheet metal components.One of the key advantages of sheet metal laser cutting is its ability to produce clean and accurate cuts without the need for additional finishing processes. This results in a faster production turnaround time and ultimately contributes to overall cost savings for manufacturers. Additionally, laser cutting technology allows for greater flexibility in terms of cutting speed and the ability to switch between different cutting patterns quickly, further enhancing the efficiency of the manufacturing process.{} has integrated sheet metal laser cutting technology into its production line to meet the growing demand for high-quality sheet metal components. By leveraging this advanced cutting technology, the company is able to offer its customers precision-cut parts with a quick turnaround time, ultimately improving overall customer satisfaction. In addition, {} has invested in state-of-the-art laser cutting machines to ensure the highest level of accuracy and efficiency in the cutting process.The adoption of sheet metal laser cutting technology has also strengthened {}'s position as a leading provider of sheet metal solutions. The company's ability to deliver complex and precise sheet metal components has set it apart from the competition and solidified its reputation as a reliable and innovative manufacturing partner. By continually investing in advanced technologies such as laser cutting, {} demonstrates its commitment to meeting and exceeding the evolving needs of its customers.As the demand for high-quality sheet metal components continues to grow, the importance of advanced cutting technologies like laser cutting cannot be overstated. Manufacturers that embrace these innovative technologies, such as {}, are better positioned to meet the ever-increasing demands for precision and efficiency in sheet metal fabrication. With sheet metal laser cutting, companies can look forward to a future of enhanced manufacturing capabilities and the ability to deliver superior products to their customers.
Tig Welding Tips for Cast Stainless Steel: A Comprehensive Guide
Tig Welding Cast Stainless Steel - A Game Changer in the Manufacturing IndustryIn today's fast-paced manufacturing industry, the need for advanced welding techniques has become more crucial than ever before. This is where Tig welding cast stainless steel comes into play. Tig welding, also known as gas tungsten arc welding (GTAW), is a welding process that uses a non-consumable tungsten electrode to produce the weld. It is widely utilized in the fabrication of stainless steel products due to its precision and control over the welding process.One company at the forefront of this innovative welding technique is {Company}. With decades of experience in the welding industry, {Company} has established itself as a pioneer in the development and implementation of advanced welding technologies. Their expertise lies in providing high-quality welding solutions to various industries, including automotive, aerospace, and medical equipment manufacturing.Tig welding cast stainless steel has revolutionized the way stainless steel components are fabricated. Due to its ability to produce clean and precise welds, it has become the preferred method for welding complex and intricate stainless steel parts. The process involves using a filler material to join the cast stainless steel components, resulting in a strong and durable weld that meets the highest quality standards.{Company} has taken Tig welding cast stainless steel to new heights by investing in state-of-the-art equipment and training its team of expert welders to master this technique. They have also collaborated with industry leaders to develop advanced welding procedures and best practices to ensure the highest level of quality and performance.The benefits of Tig welding cast stainless steel are manifold. Not only does it produce aesthetically pleasing welds, but it also offers superior strength and corrosion resistance. This makes it an ideal choice for applications where the welded components are exposed to harsh operating conditions or corrosive environments.Furthermore, the precision and control offered by Tig welding make it suitable for welding thin gauge materials without causing distortion or warpage. This is particularly advantageous in the manufacturing of complex and intricate stainless steel components, where maintaining the original shape and dimensions is crucial.{Company}'s commitment to excellence and continuous improvement has positioned them as a leader in Tig welding cast stainless steel. By staying ahead of industry trends and technological advancements, they have been able to consistently deliver superior welding solutions to their clients, helping them achieve their manufacturing goals with the highest level of quality and precision.In addition to providing cutting-edge welding services, {Company} also offers comprehensive consultation and support to their clients. Their team of welding experts works closely with customers to understand their specific requirements and provide customized solutions that meet and exceed their expectations.The future of manufacturing lies in advanced welding techniques such as Tig welding cast stainless steel. As industries continue to demand higher quality and precision in their fabricated components, companies like {Company} are paving the way for a new era of welding excellence.In conclusion, Tig welding cast stainless steel has become a game changer in the manufacturing industry, enabling the fabrication of complex and intricate stainless steel components with unmatched precision and quality. {Company}'s dedication to mastering this advanced welding technique has solidified their position as a leader in the field, providing their clients with the highest level of welding excellence. As the manufacturing industry continues to evolve, the importance of innovative welding solutions like Tig welding cast stainless steel will only grow, and {Company} is at the forefront of this revolution.
Discover the Latest Trends in Welding and Metal Fabrication
Title: Advancements in Welding and Metal Fabrication Pioneered by Industry LeaderIntroduction [Company Introduction: Remove brand name][Company Name], a renowned leader in the welding and metal fabrication industry, has consistently set new benchmarks through its innovative solutions and cutting-edge technologies. With a firm dedication towards quality and customer satisfaction, [Company Name] has revolutionized the sector and helped shape modern-day welding and metal fabrication practices. Through its unwavering commitment to excellence, it continues to drive advancements that redefine the industry's landscape.Body:1. History of Welding and Metal Fabrication:Welding and metal fabrication have been integral to human civilization for centuries. From ancient blacksmiths shaping metal to modern-day industries constructing intricate structures, the art of welding and metal fabrication has undergone remarkable transformations. Over time, various techniques and equipment have evolved, allowing for stronger, more durable, and complex welds.2. The Role of [Company Name] in Advancing the Industry:[Company Name] has played a pivotal role in propelling the welding and metal fabrication industry forward through its relentless pursuit of innovation and excellence. By investing in research and development, [Company Name] has introduced groundbreaking techniques and technologies that have redefined the industry's capabilities.3. Cutting-Edge Welding and Metal Fabrication Technologies:[Company Name] has consistently pioneered modern welding and metal fabrication technologies, ensuring enhanced efficiency and precision in various applications. Some notable advancements introduced by [Company Name] include: a. Laser Welding: [Company Name]'s revolutionary laser welding technology enables precise and high-speed welding, minimizing deformation and increasing productivity. The precise control offered by this technique ensures superior quality welds in various materials. b. Robotic Welding: By incorporating robotic welding systems, [Company Name] has revolutionized productivity and accuracy in metal fabrication. These systems offer a level of consistency and repeatability that human operators find hard to match, resulting in impeccable weld quality and increased output. c. CNC Plasma Cutting: [Company Name]'s CNC plasma cutting technology enables precise and efficient metal cutting, ensuring faster turnaround times and reduced material waste. This technology enables intricate designs to be translated flawlessly, expanding the possibilities for creative metal fabrication.4. Advancements in Materials and Metallurgy:[Company Name] has also focused on advancements in materials and metallurgy to cater to evolving industry needs. By harnessing innovative alloys and metals, [Company Name] has expanded the range of possible welding and fabrication applications. This includes developing high-strength materials suitable for demanding environments, as well as alloys specifically tailored for lightweight structures.5. Commitment to Safety and Sustainability:[Company Name] places great emphasis on safety and sustainability in welding and metal fabrication practices. It actively promotes the use of environmentally friendly processes, such as minimization of waste and pollution, as well as the adoption of safe welding procedures. By prioritizing sustainability, [Company Name] ensures a cleaner and greener future for the industry.Conclusion:As a frontrunner in the welding and metal fabrication industry, [Company Name] has consistently pushed the boundaries of what is possible. Through its relentless dedication to innovation, it has redefined the sector with groundbreaking technologies, materials, and safety practices. By setting new benchmarks, [Company Name] continues to shape the future of welding and metal fabrication, ensuring a more efficient, sustainable, and advanced industry for years to come.
Top Supplier of Welding and Steel for Interstate Projects: Get Quality Supplies Now!
Interstate Welding And Steel Supply Announces Exciting Developments in the Welding IndustryIn a recent announcement, Interstate Welding And Steel Supply, a leading player in the welding and steel supply market, confirmed a series of exciting developments that are set to reshape the industry. As one of the most trusted and reliable companies in this sector, Interstate Welding And Steel Supply has been at the forefront of providing cutting-edge solutions and high-quality services to its customers. With a strong focus on innovation and customer satisfaction, the company has cemented its position as a market leader.Interstate Welding And Steel Supply prides itself on having a team of highly skilled professionals who are dedicated to delivering the best possible results. By constantly striving for excellence, the company has been able to create a strong reputation for its commitment to exceptional customer service and top-of-the-line products. Whether it is providing welding equipment and accessories or supplying high-grade steel, Interstate Welding And Steel Supply ensures that it stays ahead of the competition by understanding market demands and addressing them proactively.To further strengthen its position in the welding industry, Interstate Welding And Steel Supply has invested in advanced technologies and machinery. By doing so, the company enables its clients to benefit from next-generation welding solutions that allow for greater precision and efficiency. This strategic investment not only sets the company apart but also allows it to meet the evolving needs of modern industries.Recognizing the significance of sustainability and environmental responsibility, Interstate Welding And Steel Supply has incorporated eco-friendly practices into its operations. By implementing energy-saving measures and reducing waste, the company is committed to minimizing its environmental footprint. This dedication to sustainable practices not only showcases Interstate Welding And Steel Supply's commitment to the future but also highlights the company's efforts to align its business with global environmental goals.As part of its ongoing commitment to fostering innovation and collaboration, Interstate Welding And Steel Supply has also formed strategic partnerships with key industry players. By joining forces with other leading companies, the organization aims to exchange knowledge, share resources, and drive the industry forward collectively. By collaborating with trusted partners, Interstate Welding And Steel Supply is confident that it can deliver unprecedented value to its customers.Furthermore, Interstate Welding And Steel Supply understands the importance of investing in its workforce. By providing comprehensive training and development programs, the company ensures that its employees stay up-to-date with the latest industry trends and advancements. This investment in human capital not only plays a crucial role in maintaining the company's competitive edge but also contributes to the growth and success of its employees.In conclusion, Interstate Welding And Steel Supply's recent developments are a testament to the company's unwavering commitment to excellence and innovation. By investing in advanced technologies, ensuring sustainability, fostering collaborations, and prioritizing employee development, the company continues to solidify its position as a market leader in the welding and steel supply industry. As Interstate Welding And Steel Supply moves forward, it remains focused on delivering exceptional products and services to its valued customers while shaping the future of the industry through its continuous efforts and dedication.
Expert Steel Fabricators: Providing Top-Quality Steel Services" could be rewritten as "Premium Steel Fabrication Services: Delivering Exceptional Results" without mentioning the specific brand name.
Steel Fabrication Services, a leading provider of high-quality steel fabrication solutions, is revolutionizing the industry with its cutting-edge technology and exceptional customer service. With years of expertise and a commitment to innovation, the company has become synonymous with excellence in the field.Specializing in custom-made fabricated steel products, Steel Fabrication Services caters to a wide range of industries including construction, manufacturing, oil and gas, and infrastructure. The company offers a diverse range of services such as structural steel fabrication, welding, and engineering design. From large-scale projects to small tailor-made solutions, their team of highly skilled professionals ensures top-notch quality and timely delivery every time.One of the main factors that sets Steel Fabrication Services apart from its competitors is its state-of-the-art manufacturing facility equipped with the latest technology. The company utilizes advanced computer-aided design (CAD) software and high-precision machinery to deliver accurate and finely crafted steel products. This combination of cutting-edge technology and skilled craftsmanship allows for the production of complex and intricate steel structures that meet the highest standards of quality and precision.In addition to its advanced manufacturing capabilities, Steel Fabrication Services takes great pride in its commitment to customer satisfaction. The company understands that every client has unique requirements and works closely with them to provide tailored solutions that fulfill their specific needs. With a customer-centric approach, Steel Fabrication Services aims to build long-term relationships with its clients based on trust and mutual success.An integral part of Steel Fabrication Services' success is its team of highly trained and experienced professionals. The company employs a dedicated workforce that is passionate about what they do and strives for excellence in every project. From project managers to welders, every member of the team plays a crucial role in ensuring the highest level of workmanship and attention to detail.Furthermore, Steel Fabrication Services is committed to maintaining the highest industry standards and certifications. The company follows strict quality control procedures to ensure that all steel products meet or exceed customer expectations and industry regulations. With a strong emphasis on safety and efficiency, Steel Fabrication Services consistently delivers safe and reliable steel solutions to its clients.The company's dedication to innovation and continuous improvement is reflected in its investment in research and development. Steel Fabrication Services constantly seeks new ways to enhance its manufacturing processes and efficiency, resulting in cost-effective solutions for its clients without compromising on quality. By staying at the forefront of technological advancements, the company maintains its competitive edge in the industry.As an environmentally conscious organization, Steel Fabrication Services strives to minimize its carbon footprint. The company implements sustainable practices throughout its operations and consistently explores ways to reduce waste and promote energy efficiency. By adopting eco-friendly approaches, Steel Fabrication Services contributes to a greener future while providing top-notch steel fabrication solutions.With its exceptional services, state-of-the-art technology, and commitment to customer satisfaction, Steel Fabrication Services continues to lead the way in the steel fabrication industry. As the company looks towards the future, it remains focused on innovation, quality, and providing customized solutions to meet the evolving needs of its clients.In conclusion, Steel Fabrication Services is a trusted name in the steel fabrication industry, offering a wide range of high-quality products and services. With its advanced technology, skilled workforce, and customer-centric approach, the company strives to exceed customer expectations and deliver excellence in every project.
Benefits of Plasma Cutting Welding for Metal Fabrication
Plasma cutting welding is a cutting-edge cutting and welding technology that has been revolutionizing the industrial manufacturing sector. This advanced method, which utilizes a high-velocity jet of ionized gas to make precise and efficient cuts, has been gaining popularity due to its speed, accuracy, and ability to work with a wide range of materials.In the forefront of this innovative technology is {}, a leading provider of industrial cutting and welding solutions. With over 20 years of experience in the industry, {} has been at the forefront of developing and implementing cutting-edge technologies to meet the diverse needs of its clients.Plasma cutting welding is a highly versatile and efficient process that can be used for a wide range of applications, including metal fabrication, automotive manufacturing, shipbuilding, and aerospace engineering. This method is particularly well-suited for cutting and welding materials such as stainless steel, aluminum, and other non-ferrous metals.One of the key advantages of plasma cutting welding is its ability to produce highly precise cuts with minimal heat-affected zones, which results in clean and smooth edges. This is essential for industries that require high-quality, precision cutting and welding, such as the aerospace and defense sectors.Furthermore, plasma cutting welding is known for its high cutting speeds and ability to handle a wide range of material thicknesses, making it a cost-effective and efficient solution for manufacturers. This technology also offers greater flexibility and maneuverability, allowing for intricate and complex cutting patterns with ease.{} has been leading the charge in the advancement of plasma cutting welding technology, constantly innovating and refining its solutions to meet the evolving needs of its clients. The company's team of experienced engineers and technicians are dedicated to developing cutting-edge equipment and providing comprehensive support and training to ensure optimal performance and efficiency.In addition to its cutting-edge technology, {} takes pride in its commitment to sustainability and environmental consciousness. The company's plasma cutting welding solutions are designed to minimize waste and reduce energy consumption, contributing to a cleaner and more sustainable manufacturing process.As the demand for precision cutting and welding solutions continues to grow in the industrial sector, {} remains at the forefront of the industry, providing cutting-edge plasma cutting welding technology that delivers superior performance, efficiency, and reliability.With its unwavering dedication to innovation, quality, and customer satisfaction, {} is poised to remain a leading provider of plasma cutting welding solutions, shaping the future of industrial manufacturing. From aerospace engineering to automotive manufacturing, {}'s cutting-edge technology is driving the industry forward, revolutionizing the way manufacturers cut and weld a wide range of materials.As the industry continues to evolve, {} will continue to push the boundaries of plasma cutting welding technology, setting new standards for performance, precision, and efficiency. With its proven track record of excellence and dedication to customer satisfaction, {} is poised to remain a driving force in the advancement of plasma cutting welding technology for years to come.
Fiber Laser Engraving Service: Enhancing Precision and Efficiency for Your Engraving Needs
How Laser Cutting is Revolutionizing Manufacturing Processes
Laser Plate Cutting: The Future of Precision ManufacturingIn our increasingly tech-savvy world, precision and accuracy have become more important than ever before. As such, precision manufacturing has taken center stage, with companies constantly seeking new and innovative ways to create perfect, intricate, and detailed products. One such innovation is laser plate cutting, a process that uses lasers to make precise cuts in a variety of materials. In this blog, we'll dive into the world of laser plate cutting and explore why it's the future of precision manufacturing.What is Laser Plate Cutting?Laser plate cutting is a process that uses a high-powered laser to cut through a variety of materials, including steel, aluminum, and other metals. The laser beam is directed at the material, creating a highly focused point of heat that melts or vaporizes the material in a precise and controlled manner. This process results in clean, sharp, and accurate cuts that are free of burrs or other imperfections.How Does Laser Plate Cutting Work?To understand how laser plate cutting works, it's helpful to understand how a laser works in the first place. A laser (which stands for Light Amplification by Stimulated Emission of Radiation) emits a highly concentrated beam of light that is focused on a small area. This beam is made up of photons, which are particles of light. When the photons hit a material, they transfer energy to it, causing it to heat up and melt or vaporize.In laser plate cutting, the laser beam is directed onto a plate of material using a series of mirrors and lenses. The laser can be adjusted to various settings, including power and speed, to ensure the most precise cut possible. The process can be automated using computer-controlled systems, which allows for even greater precision and speed.Benefits of Laser Plate CuttingSo why is laser plate cutting the future of precision manufacturing? There are several key benefits to the process that set it apart from other types of cutting:1. Precision and accuracy: Laser plate cutting allows for incredibly precise cuts that are free of burrs or other imperfections.2. Speed: Laser cutting is faster than many other cutting methods, which means that products can be created more quickly.3. Versatility: Laser cutting can be used on a wide range of materials, including metals, plastics, and even glass.4. Cost-effectiveness: Although laser plate cutting requires expensive equipment, it can ultimately save money in the long run by reducing waste and the need for additional finishing processes.Applications of Laser Plate CuttingLaser plate cutting has a wide range of applications across many industries. Here are just a few examples:1. Aerospace: Laser cutting is used to create precise components for aircraft engines, landing gear, and other systems.2. Automotive: Laser cutting is used to create parts for cars and trucks, including body panels, suspension components, and exhaust systems.3. Medical: Laser cutting is used to create surgical tools, implants, and other medical equipment that requires precision and accuracy.4. Technology: Laser cutting is used to create components for consumer electronics, such as smartphones and tablets.ConclusionIn conclusion, laser plate cutting is the future of precision manufacturing. With its ability to create precise, accurate cuts on a wide range of materials, laser cutting has become an essential tool for many industries. As technology continues to advance, we can expect to see even greater innovations in laser cutting, making it an even more important part of the manufacturing process. So if you're looking for the most precise and accurate cuts for your next project, consider laser plate cutting.
How to Tig Weld Mild Steel: A Complete Guide
[Company Introduction]Established in [year], [Company Name] has been a leading provider of welding equipment and supplies for industrial, commercial, and personal use. With a strong commitment to quality and customer satisfaction, [Company Name] has built a reputation for excellence in the welding industry.Specializing in a wide range of welding processes and products, [Company Name] offers everything from basic welding machines to advanced robotic welding systems. Our team of experienced professionals is dedicated to helping our customers find the right welding solutions for their specific needs. We also provide comprehensive training and support to ensure that our clients are able to use our products to their full potential.As part of our commitment to staying at the forefront of the welding industry, we constantly strive to improve and expand our product offerings. We are proud to announce that we have recently added a new line of TIG welding machines specially designed for mild steel. This addition to our product range is a testament to our dedication to meeting the evolving needs of our customers and providing them with the latest and most efficient welding solutions.[News Content]TIG welding, short for Tungsten Inert Gas welding, is a popular welding process known for its versatility and precision. It is widely used in various industries, including automotive, aerospace, and manufacturing, for the fabrication of high-quality welds. One of the key advantages of TIG welding is its ability to produce clean and precise welds, making it ideal for applications that demand a high level of accuracy and aesthetics.TIG welding is commonly performed on stainless steel, aluminum, and other non-ferrous metals, but it can also be used for welding mild steel with the right equipment and expertise. With the increasing demand for TIG welding mild steel in the industry, [Company Name] has introduced a new line of TIG welding machines specifically tailored for this purpose.The new TIG welding machines for mild steel offered by [Company Name] are designed to deliver superior performance and consistent results. Equipped with advanced features and capabilities, these machines enable welders to achieve strong and precise welds on mild steel, while maintaining excellent control over the welding process.One of the key features of the new TIG welding machines is their ability to provide smooth and stable arc characteristics, which are essential for welding mild steel with precision. In addition, these machines offer a high level of control over the heat input, ensuring that the weld pool is properly formed and the metal is fused in a consistent manner.Moreover, the new TIG welding machines are designed to be user-friendly, allowing welders of all skill levels to operate them with ease. This is in line with [Company Name]'s commitment to providing welding solutions that are accessible and practical for a wide range of users. With comprehensive training and support available, customers can rely on [Company Name] to help them maximize the potential of these new TIG welding machines for mild steel."We are excited to introduce our new line of TIG welding machines for mild steel," said [Spokesperson's Name], [Title] at [Company Name]. "With the increasing demand for high-quality welding on mild steel, we saw an opportunity to develop specialized equipment that would meet this need. Our new TIG welding machines offer the precision, control, and performance that our customers expect from us, and we are confident that they will be well received in the market."In conclusion, the introduction of the new TIG welding machines for mild steel by [Company Name] demonstrates the company's commitment to innovation and meeting the evolving needs of its customers. With advanced features, superior performance, and user-friendly design, these machines are poised to become valuable assets for welders working with mild steel. As [Company Name] continues to expand its product offerings and support services, it remains a trusted partner for welding solutions in various industries.
The Process of Steel Butt Welding: A Complete Guide
Steel Butt Welding, a leading welding technology company specializing in the manufacturing of high-quality welding equipment, is making waves in the industry with its innovative and advanced welding solutions. With a strong emphasis on research and development, the company has been able to create cutting-edge welding technologies that are not only efficient but also cost-effective.The company, with its headquarters located in the heart of the industrial sector, has been at the forefront of providing welding solutions to a wide range of industries, including automotive, aerospace, construction, and more. With a team of highly skilled and experienced professionals, Steel Butt Welding has been able to develop a diverse range of welding equipment that meets the specific needs of its customers.One of the key factors that set Steel Butt Welding apart from its competitors is its commitment to quality. The company has implemented strict quality control measures to ensure that all its products meet the highest industry standards. This dedication to quality has earned Steel Butt Welding a stellar reputation among its customers, who have come to rely on the company for their welding needs.In addition to its focus on quality, Steel Butt Welding also places a strong emphasis on innovation. The company continuously invests in research and development to stay ahead of the curve and introduce new and improved welding solutions to the market. This commitment to innovation has enabled Steel Butt Welding to introduce state-of-the-art welding technologies that offer improved efficiency, productivity, and cost savings to its customers.Among the company's most notable achievements is the development of its butt welding equipment, which has gained significant attention in the industry. The butt welding process is a highly effective method of joining two pieces of metal together end-to-end. This method results in a strong and durable weld, making it ideal for industries that require high-quality and reliable welds.Steel Butt Welding's butt welding equipment is designed to deliver precision and consistency in the welding process, ensuring that the resulting weld is of the highest quality. The company's equipment is also known for its user-friendly design, making it easy for operators to set up and operate, further contributing to the efficiency and effectiveness of the welding process.Another notable aspect of Steel Butt Welding's butt welding equipment is its versatility. The equipment is designed to accommodate a wide range of materials and thicknesses, making it suitable for a variety of welding applications across different industries. This versatility has made Steel Butt Welding's equipment a popular choice among businesses looking for reliable and efficient welding solutions.Steel Butt Welding's commitment to providing top-of-the-line welding equipment, coupled with its dedication to customer satisfaction, has positioned the company as a trusted partner for businesses seeking welding solutions. The company's customer-centric approach has earned it a loyal customer base that values its reliable products and excellent service.Looking ahead, Steel Butt Welding is poised to continue its trajectory of success in the welding industry. The company is committed to further advancing its welding technologies and expanding its range of solutions to meet the evolving needs of its customers. With a focus on innovation, quality, and customer satisfaction, Steel Butt Welding is well-positioned to remain a leader in the welding industry for years to come.