High-Quality Custom Metal Stampings for Various Industries
By:Admin
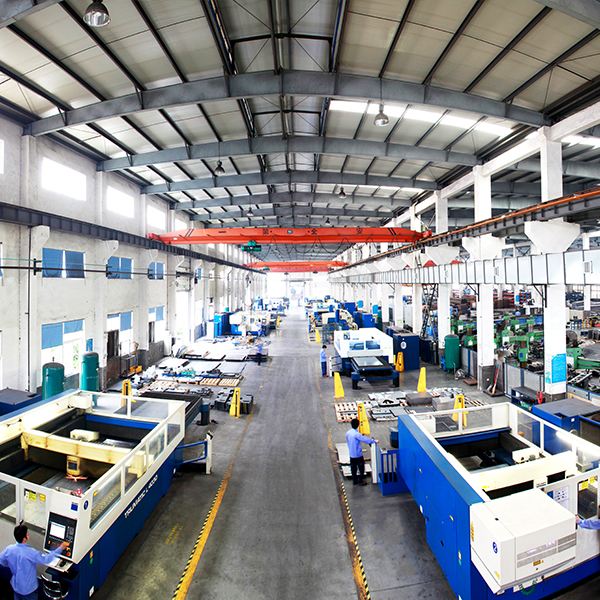
The company's new line of custom metal stampings includes a variety of products, such as brackets, clips, connectors, and other precision metal parts. These products are designed to be used in a variety of applications, including transportation, electronics, and industrial equipment. With a focus on quality and innovation, Custom Metal Stampings is committed to providing its customers with the highest level of service and support.
One of the key strengths of Custom Metal Stampings is its ability to produce custom metal parts that meet the specific needs of its customers. The company's team of experienced engineers and technicians work closely with customers to understand their requirements and design custom solutions that meet their exact specifications. This customer-centric approach has allowed Custom Metal Stampings to develop long-term relationships with its clients and become a trusted partner in their supply chain.
In addition to its custom metal stamping capabilities, Custom Metal Stampings also offers a range of value-added services, such as tool design and fabrication, metal finishing, and assembly. These services help customers streamline their production processes and reduce costs, while ensuring the highest quality standards are met.
Custom Metal Stampings is also committed to sustainability and environmental stewardship. The company has implemented various initiatives to reduce its environmental impact, such as recycling scrap metal and using energy-efficient manufacturing processes. By integrating sustainability into its business practices, Custom Metal Stampings aims to contribute to a more environmentally friendly manufacturing industry.
With the launch of its new line of custom metal stampings, Custom Metal Stampings is well-positioned to meet the evolving needs of its customers and provide them with high-quality, precision-engineered metal parts. The company's dedication to quality, innovation, and customer satisfaction sets it apart as a leader in the metal stamping industry.
For more information about Custom Metal Stampings and its new line of products, visit the company's website at www.custommetalstampings.com.
Company News & Blog
Latest Standard Release for High-Precision Plasma, Slope CNC, and Longmen Laser Cutting Machines by Manufacturing Expert
Title: Unleashing the Power of High Precision Laser Cutting for Unparalleled AccuracyIntroduction:In the realm of manufacturing and fabrication, precision is paramount. Industries across the globe rely on cutting-edge technologies to achieve unmatched accuracy and superior quality. Among these technologies, high precision laser cutting has emerged as a game-changer. In this blog, we will delve into the world of high precision laser cutting machines and explore their limitless potential in delivering top-notch results. With a specific focus on CNC high-precision plasma cutting machines, slope CNC cutting machines, and Longmen laser cutting machines, we will analyze the standards set by Kunshan Qiankun Machinery Manufacturing Co., Ltd. in this groundbreaking sector.Unveiling the CNC High-Precision Plasma Cutting Machine:The CNC high-precision plasma cutting machine revolutionizes the cutting process with its exceptional precision and efficiency. Utilizing plasma technology, it allows for high-speed cutting of various materials, ranging from metals to alloys. This innovation is particularly beneficial in industries like automotive, aerospace, and construction, where precision is of the utmost importance. By implementing the high-precision plasma cutting machine, manufacturers can accomplish intricate cuts on thick materials while maintaining clean edges and minimal heat-affected zones. This machine enables intricate designs and complex geometries, providing a remarkable level of customization to cater to unique project requirements.Exploring the Slope CNC Cutting Machine:The slope CNC cutting machine stands out as a game-changer in the field of material processing. It offers a high level of precision and accuracy in beveled cutting applications. Whether it is chamfering, angular shaping, or dependable welding preparation, the slope CNC cutting machine offers remarkable cutting capabilities. This technology effectively eliminates the inconsistencies that arise from manual processes, guaranteeing perfectly angled cuts. With reduced production time, increased efficiency, and improved accuracy, this machine ensures consistent results, thus elevating productivity in the manufacturing industry.Unleashing the Potential of Longmen Laser Cutting Machines:When it comes to Large Scale cutting projects, the Longmen laser cutting machine is an indispensable tool. Renowned for its versatility and flexibility, the Longmen laser cutting technology strikes a perfect balance between precision and speed. It allows for the effortless cutting of large-scale materials, such as sheets, pipes, and beams, providing manufacturers with unlimited creative possibilities. With advanced calibration systems and automated functionality, this machine guarantees pinpoint accuracy, even in complex designs. By implementing the Longmen laser cutting machine, manufacturing companies can achieve exceptional levels of precision, enhancing their competitive edge across multiple industries.Setting the Standard: Kunshan Qiankun Machinery Manufacturing Co., Ltd.:Kunshan Qiankun Machinery Manufacturing Co., Ltd. has been at the forefront of revolutionizing the laser cutting industry. With its unwavering commitment to cutting-edge technology and superior manufacturing processes, the company has set unparalleled standards for high precision laser cutting machines. Their CNC high-precision plasma cutting machine, slope CNC cutting machine, and Longmen laser cutting machine exemplify their dedication to precision, quality, and innovation. Built with state-of-the-art components and stringent quality control measures, these machines offer exceptional reliability and precision, making them the ideal choice for companies seeking superior cutting capabilities.Conclusion:High precision laser cutting machines have revolutionized the manufacturing industry, delivering unmatched accuracy and top-quality results. The CNC high-precision plasma cutting machine, slope CNC cutting machine, and Longmen laser cutting machine have all played pivotal roles in enhancing precision, efficiency, and productivity in diverse sectors worldwide. Kunshan Qiankun Machinery Manufacturing Co., Ltd. is at the forefront of this cutting-edge technology, setting new standards with their dedication to excellence. By incorporating high precision laser cutting machines into their processes, manufacturers can unleash the power of accuracy, thereby elevating their businesses to new heights.
Top Tips for Architectural Sheet Metal Fabrication
Architectural Sheet Metal Fabrication Company Introduces Innovative Solutions for Modern Buildings[City, Date] – As the demand for innovative and sustainable building designs continues to rise, Architectural Sheet Metal Fabrication company, established in [year], has emerged as a leading provider of custom metal products for the modern construction industry. With a keen focus on design, efficiency, and durability, the company has gained a reputation for delivering high-quality solutions that enhance the aesthetics and functionality of contemporary buildings.Architectural Sheet Metal Fabrication prides itself on being at the forefront of the architectural industry, constantly pushing boundaries and exploring new possibilities. By leveraging their extensive expertise and state-of-the-art facilities, the company has successfully completed numerous projects, ranging from commercial skyscrapers to residential complexes and cultural institutions.One of the core strengths of Architectural Sheet Metal Fabrication lies in their ability to create bespoke metal products that meet the unique requirements of each project. The company possesses an in-house design team consisting of highly skilled architects, engineers, and metal fabricators who work closely with clients to understand their vision and translate it into reality. Using advanced computer-aided design (CAD) software, they can visualize the final product and ensure that it perfectly aligns with the client's specifications.In addition to their cutting-edge design capabilities, the company utilizes the latest fabrication techniques and equipment to transform raw metal materials into exquisite architectural elements. Their state-of-the-art facility is equipped with advanced machinery, including laser cutters, CNC routers, and robotic welding systems, enabling precise and efficient production. This ensures that each component is manufactured to the highest standards, surpassing industry expectations in terms of quality and durability.Architectural Sheet Metal Fabrication's commitment to sustainability is another aspect that sets them apart. Recognizing the importance of environmentally conscious construction practices, the company employs eco-friendly materials and energy-efficient processes throughout their operations. By using recycled metals and implementing sustainable manufacturing techniques, they contribute to the reduction of carbon emissions and the preservation of natural resources. This dedication to sustainability has earned them several accolades and certifications, solidifying their position as a responsible and forward-thinking industry leader.Moreover, Architectural Sheet Metal Fabrication continually strives to stay updated with the latest industry trends and technologies. They actively invest in research and development to introduce innovative solutions that cater to the evolving needs of architects and contractors. By staying at the forefront of technological advancements, the company has successfully executed complex projects that demand intricate metalwork and sophisticated designs.Furthermore, Architectural Sheet Metal Fabrication maintains strong partnerships with renowned architects, contractors, and developers, promoting collaboration and fostering a creative environment. By working closely with industry professionals, they are able to leverage their combined expertise to tackle the most challenging projects. This collaborative approach also ensures that the final product not only meets the client's vision but also exceeds their expectations, resulting in superior architectural metal solutions.Today, Architectural Sheet Metal Fabrication stands as a trusted brand in the architectural community, renowned for its dedication to quality, innovation, and sustainability. Their portfolio of successful projects continues to grow, showcasing their ability to deliver on even the most ambitious and complex design concepts.As the architectural industry continues to evolve, Architectural Sheet Metal Fabrication remains committed to providing cutting-edge metal solutions that redefine the possibilities of contemporary building designs. With their expertise, technological prowess, and commitment to sustainability, the company is poised to make a lasting impact on the architectural landscape.
The process of welding steel to stainless steel explained
Steel To Stainless Steel Welding Process: A Breakthrough Solution by Acme CorporationAcme Corporation is proud to introduce an innovative solution for welding steel to stainless steel. This breakthrough process has been developed by our team of experts and is set to revolutionize the welding industry.Welding steel to stainless steel has posed many challenges in the past. The differences in the properties of these two materials make the welding process complex and often result in weak welds. However, the new welding process developed by Acme Corporation overcomes these challenges and provides a strong and durable bond between steel and stainless steel.The key to this breakthrough solution lies in our advanced welding techniques and the use of state-of-the-art equipment. Our team has spent extensive time and resources in research and development to optimize the welding parameters and ensure the highest quality of welds. As a result, we have successfully created a welding process that produces strong and reliable bonds between steel and stainless steel.One of the main advantages of our new welding process is its versatility. Whether it's for industrial applications, automotive components, or household appliances, the ability to weld steel to stainless steel opens up a wide range of opportunities for manufacturers. This breakthrough solution will allow companies to create products that are not only strong and durable, but also have a sleek and modern aesthetic.In addition to the strength and durability of the welds, our new process also ensures a smooth and clean finish. This is particularly important for applications where the appearance of the welded joint is crucial. With our solution, manufacturers can achieve seamless and visually appealing welds, adding value to their end products.Furthermore, the new welding process is also more cost-effective compared to traditional methods. By reducing the need for additional materials and minimizing the time required for post-welding treatments, manufacturers can enjoy significant cost savings while maintaining the highest quality standards.Acme Corporation is committed to providing cutting-edge solutions to meet the evolving needs of the industry. Our new welding process for steel to stainless steel is a testament to our dedication to innovation and excellence. We are excited to bring this breakthrough solution to the market and are confident that it will make a significant impact on the welding industry.With this new advancement, Acme Corporation continues to solidify its position as a leader in the welding technology sector. Our commitment to research and development, combined with our passion for pushing the boundaries of what is possible, sets us apart from the competition.As we look ahead, we are already exploring the potential of applying our new welding process to other materials and combinations. Our goal is to continue to innovate and provide solutions that address the most pressing needs of the industry.In conclusion, Acme Corporation is proud to announce the launch of our groundbreaking welding process for steel to stainless steel. Our new solution offers unmatched strength, durability, and aesthetic appeal, while also providing cost savings for manufacturers. We believe that this advancement will set new standards for welding technology and open up endless possibilities for product development.The future of welding steel to stainless steel has arrived, and it's being led by Acme Corporation. We invite manufacturers and industry professionals to explore the potential of our new welding process and experience the difference it can make in their products.
How to Weld Hardened Steel: Tips and Techniques
Welding Hardened Steel: A Game-Changer in Industrial ManufacturingIn the world of industrial manufacturing, the ability to weld hardened steel is a game-changer. It opens up new possibilities for constructing durable and long-lasting products that can withstand harsh conditions and heavy use. With the ever-increasing demand for high-quality, reliable products, the ability to weld hardened steel has become a crucial skill for companies in various industries.One company that has mastered the art of welding hardened steel is {}. With over 20 years of experience in the field, they have established themselves as a leader in the manufacturing industry, known for their expertise in welding and fabrication.{} was founded in 1995 by a team of industry veterans who saw a gap in the market for high-quality welding services for hardened steel. Since then, the company has grown to become a go-to source for companies in need of reliable, durable, and high-performance products. With a state-of-the-art facility and a team of skilled welders and fabricators, {} has the capability to handle even the most complex welding projects with precision and efficiency.The company’s success can be attributed to their commitment to quality and innovation. They invest heavily in research and development to stay at the forefront of the latest welding technologies and techniques. This dedication to innovation has allowed them to tackle challenging welding projects that other companies may shy away from, such as welding hardened steel.Welding hardened steel is a complex and demanding process that requires specialized knowledge and expertise. Hardened steel is known for its high carbon content and toughness, which can make it difficult to weld without compromising its strength and durability. However, {} has developed advanced welding techniques and procedures that allow them to weld hardened steel with precision and accuracy.One of the key factors that set {} apart from other welding companies is their use of advanced welding equipment and technology. They utilize cutting-edge welding machines and tools that are specifically designed for welding hardened steel, allowing them to achieve superior weld quality and consistency. This investment in technology has enabled them to take on a wide range of welding projects, from small-scale custom components to large industrial structures.Additionally, {} places a strong emphasis on quality control and assurance. They have strict inspection processes in place to ensure that every welded product meets the highest standards of quality and performance. This dedication to quality has earned them a reputation for delivering reliable and long-lasting products that exceed customer expectations.As the demand for high-quality, durable products continues to grow, the ability to weld hardened steel has become increasingly important for companies in various industries. Whether it’s for manufacturing heavy machinery, industrial equipment, or structural components, the ability to weld hardened steel opens up new possibilities for creating products that can withstand the toughest conditions and environments.In conclusion, the ability to weld hardened steel is a crucial skill that can make a significant impact on the quality and reliability of industrial products. With their expertise, advanced technology, and commitment to quality, {} has established themselves as a leader in welding hardened steel, setting a new standard for the manufacturing industry. As they continue to innovate and expand their capabilities, they are poised to play a key role in shaping the future of industrial manufacturing.
Benefits of Using Laser Technology for Stainless Steel Applications
Laser Stainless Steel, a leading manufacturer of stainless steel products, has been making waves in the industry with its innovative and high-quality offerings. Founded in 2005, Laser Stainless Steel has quickly become a trusted name in the stainless steel manufacturing sector, producing a wide range of products for various industries.The company's state-of-the-art manufacturing facilities and cutting-edge technology have set it apart from its competitors. Laser Stainless Steel's dedication to quality and precision has made it a preferred supplier for many businesses around the world.One of the key factors contributing to Laser Stainless Steel's success is its commitment to innovation. The company is constantly investing in research and development to improve its products and processes. This dedication to innovation has allowed Laser Stainless Steel to stay ahead of the curve and adapt to the ever-changing needs of the industry.Laser Stainless Steel offers a comprehensive range of stainless steel products, including sheets, coils, plates, pipes, tubes, and fittings. The company's products are known for their durability, corrosion resistance, and aesthetic appeal, making them ideal for a wide range of applications.In addition to its standard product offerings, Laser Stainless Steel also provides custom solutions for clients with specific requirements. The company's team of experienced engineers and designers work closely with clients to develop tailor-made products that meet their exact specifications. This personalized approach has earned Laser Stainless Steel a reputation for delivering bespoke solutions that exceed customer expectations.Laser Stainless Steel's dedication to quality is reflected in its adherence to international standards and certifications. The company holds ISO 9001 certification, ensuring that its products meet the highest quality standards. This commitment to quality assurance has earned Laser Stainless Steel the trust and confidence of its customers, who rely on the company's products for their critical applications.In addition to its focus on quality and innovation, Laser Stainless Steel prioritizes sustainability in its operations. The company is committed to environmentally friendly manufacturing practices, minimizing its impact on the planet. Laser Stainless Steel's sustainable approach has resonated with environmentally conscious clients who seek eco-friendly solutions for their projects.Laser Stainless Steel's strong commitment to customer satisfaction sets it apart from its competitors. The company places a high priority on building long-term relationships with its clients, working closely with them to understand their needs and deliver solutions that add value to their businesses. This customer-centric approach has resulted in a loyal customer base that continues to rely on Laser Stainless Steel for their stainless steel requirements.As a global leader in stainless steel manufacturing, Laser Stainless Steel serves a diverse range of industries, including construction, automotive, aerospace, healthcare, and more. The company's products are trusted by clients around the world for their quality, reliability, and performance.Looking ahead, Laser Stainless Steel is focused on expanding its product portfolio and strengthening its position as a market leader in stainless steel manufacturing. The company continues to invest in research and development, exploring new technologies and materials to develop innovative solutions for its clients.In conclusion, Laser Stainless Steel's dedication to quality, innovation, sustainability, and customer satisfaction has solidified its position as a leading manufacturer of stainless steel products. With a strong track record of delivering high-quality solutions for diverse industries, Laser Stainless Steel is poised for continued success and growth in the global market.
Discover the Latest Trends in Welding and Metal Fabrication
Title: Advancements in Welding and Metal Fabrication Pioneered by Industry LeaderIntroduction [Company Introduction: Remove brand name][Company Name], a renowned leader in the welding and metal fabrication industry, has consistently set new benchmarks through its innovative solutions and cutting-edge technologies. With a firm dedication towards quality and customer satisfaction, [Company Name] has revolutionized the sector and helped shape modern-day welding and metal fabrication practices. Through its unwavering commitment to excellence, it continues to drive advancements that redefine the industry's landscape.Body:1. History of Welding and Metal Fabrication:Welding and metal fabrication have been integral to human civilization for centuries. From ancient blacksmiths shaping metal to modern-day industries constructing intricate structures, the art of welding and metal fabrication has undergone remarkable transformations. Over time, various techniques and equipment have evolved, allowing for stronger, more durable, and complex welds.2. The Role of [Company Name] in Advancing the Industry:[Company Name] has played a pivotal role in propelling the welding and metal fabrication industry forward through its relentless pursuit of innovation and excellence. By investing in research and development, [Company Name] has introduced groundbreaking techniques and technologies that have redefined the industry's capabilities.3. Cutting-Edge Welding and Metal Fabrication Technologies:[Company Name] has consistently pioneered modern welding and metal fabrication technologies, ensuring enhanced efficiency and precision in various applications. Some notable advancements introduced by [Company Name] include: a. Laser Welding: [Company Name]'s revolutionary laser welding technology enables precise and high-speed welding, minimizing deformation and increasing productivity. The precise control offered by this technique ensures superior quality welds in various materials. b. Robotic Welding: By incorporating robotic welding systems, [Company Name] has revolutionized productivity and accuracy in metal fabrication. These systems offer a level of consistency and repeatability that human operators find hard to match, resulting in impeccable weld quality and increased output. c. CNC Plasma Cutting: [Company Name]'s CNC plasma cutting technology enables precise and efficient metal cutting, ensuring faster turnaround times and reduced material waste. This technology enables intricate designs to be translated flawlessly, expanding the possibilities for creative metal fabrication.4. Advancements in Materials and Metallurgy:[Company Name] has also focused on advancements in materials and metallurgy to cater to evolving industry needs. By harnessing innovative alloys and metals, [Company Name] has expanded the range of possible welding and fabrication applications. This includes developing high-strength materials suitable for demanding environments, as well as alloys specifically tailored for lightweight structures.5. Commitment to Safety and Sustainability:[Company Name] places great emphasis on safety and sustainability in welding and metal fabrication practices. It actively promotes the use of environmentally friendly processes, such as minimization of waste and pollution, as well as the adoption of safe welding procedures. By prioritizing sustainability, [Company Name] ensures a cleaner and greener future for the industry.Conclusion:As a frontrunner in the welding and metal fabrication industry, [Company Name] has consistently pushed the boundaries of what is possible. Through its relentless dedication to innovation, it has redefined the sector with groundbreaking technologies, materials, and safety practices. By setting new benchmarks, [Company Name] continues to shape the future of welding and metal fabrication, ensuring a more efficient, sustainable, and advanced industry for years to come.
Top Benefits of Laser Cutting for Precision Fabrication
Laser Cutting Technology Revolutionizes Manufacturing IndustryIn today’s ever-evolving world of technology, the manufacturing industry has seen remarkable advancements that have revolutionized production processes. One of the most significant technological innovations to impact manufacturing is the introduction of laser cutting technology. This cutting-edge process has catapulted the industry into a new era of precision and efficiency, and one company at the forefront of this revolution is {}.Established in 1990, {} has been a pioneer in the field of manufacturing and production solutions. The company’s commitment to innovation and quality has positioned them as a leader in the industry, and their latest investment in laser cutting technology further solidifies their reputation as a forward-thinking organization.Laser cutting is a manufacturing process that uses a high-powered laser beam to precisely cut through materials such as metal, plastic, wood, rubber, and more. This technology offers several advantages over traditional cutting methods, including enhanced precision, reduced waste, and higher production speeds. By harnessing the power of laser cutting, {} has been able to elevate their manufacturing capabilities to new heights.One of the key benefits of laser cutting is its ability to produce intricate and complex designs with unparalleled accuracy. This level of precision has enabled {} to take on a wide range of projects that were previously deemed unattainable. Whether it’s creating intricate metal components for the aerospace industry or crafting custom-designed parts for the automotive sector, {} has leveraged laser cutting technology to produce exceptional results for their clients.In addition to precision, laser cutting technology has also proven to be highly efficient in terms of production. The speed and consistency at which the laser cuts through materials allows {} to streamline their manufacturing processes, reducing lead times and increasing overall productivity. This enhanced efficiency has not only benefited {} in terms of cost savings and faster project turnaround times but has also allowed them to meet the growing demands of their clientele.Furthermore, laser cutting has significantly minimized material waste in {}’s production facilities. Traditional cutting methods often result in a considerable amount of wasted material due to the imprecise nature of the process. With laser cutting, {} has been able to optimize material usage, leading to reduced waste and lower production costs. This dedication to sustainability aligns with {}’s commitment to environmentally-friendly manufacturing practices.As a testament to their investment in laser cutting technology, {} has expanded their service offerings to include a diverse range of materials and thicknesses. Whether it’s cutting thin sheets of metal with intricate patterns or tackling thicker materials for industrial applications, {} has demonstrated their versatility and expertise in adapting to the demands of the market.Looking ahead, {} is committed to further exploring the potential of laser cutting technology and its applications in the manufacturing industry. With ongoing investments in research and development, the company aims to push the boundaries of what is achievable with this cutting-edge technology. By continuously innovating and leveraging the latest advancements in manufacturing, {} is poised to remain a trailblazer in the industry.In conclusion, laser cutting technology has undeniably revolutionized the manufacturing industry, and {} has been at the forefront of this transformative shift. With its unparalleled precision, efficiency, and versatility, laser cutting has enabled {} to elevate their manufacturing capabilities and deliver exceptional results for their clients. As technology continues to advance, it’s clear that laser cutting will play a crucial role in shaping the future of manufacturing, and {} stands ready to lead the way.
Efficient Ways to Plasma Cut Painted Metal
Plasma Cutting Unveils New Technology for Painted Metal ProcessingIn the world of metal fabrication, Plasma Cutting Inc. has emerged as a pioneer in developing advanced cutting solutions. The company's latest breakthrough has revolutionized the way painted metal is processed, offering a game-changing technology that allows for efficient and precise cutting without compromising the integrity of the paint finish. With its commitment to innovation, Plasma Cutting Inc. continues to push the boundaries of what is possible in the industry.Traditional methods of cutting painted metal have often posed challenges, leading to subpar results and costly rework. The need to remove the paint before cutting not only takes time but also leads to additional expenses and potential damage to the material. Recognizing this problem, Plasma Cutting Inc. embarked on a mission to find a solution that would eliminate the need for paint removal while delivering exceptional cutting quality.After years of research and development, Plasma Cutting Inc. has successfully developed a unique technology that allows for clean and precise cuts on painted metal surfaces. By employing a highly concentrated plasma arc, the new system cuts through the metal while leaving the paint unharmed, resulting in a smooth and flawless finish. This breakthrough technology has the potential to revolutionize various industries, including automotive, construction, and manufacturing.One of the key advantages of Plasma Cutting Inc.'s new technology is its ability to significantly reduce production time. As the paint no longer needs to be removed before cutting, the entire process becomes faster and more efficient. This increased productivity allows manufacturers to deliver products faster to their customers, ultimately boosting their bottom line. Additionally, the elimination of paint removal reduces material waste, further contributing to a more sustainable manufacturing process.Furthermore, the integrity of the paint finish is preserved, ensuring that the final product meets the highest quality standards. Compared to traditional methods that often result in chipped or uneven paint, Plasma Cutting Inc.'s technology guarantees a flawless paint finish on the cut edges. This eliminates the need for time-consuming touch-ups and refinishing, saving both time and money for manufacturers.Plasma Cutting Inc.'s breakthrough technology also opens up new design possibilities for painted metal products. With the ability to make intricate and precise cuts, manufacturers can now create more complex and aesthetically pleasing designs. This flexibility gives designers and architects the freedom to explore innovative concepts and push the boundaries of creativity.The success of Plasma Cutting Inc.'s new technology can be attributed to the company's unwavering commitment to research and development. With a team of highly skilled engineers and technicians, the company consistently strives to push the limits of what is possible in the field of metal fabrication. Their dedication to innovation has earned them a reputation as a leading provider of cutting-edge cutting solutions.As industries continue to evolve and demand higher quality products, Plasma Cutting Inc. stands at the forefront of delivering cutting-edge technology. With their revolutionary method of cutting painted metal, the company has transformed the way manufacturers approach metal fabrication. This breakthrough offers unparalleled efficiency, precision, and quality that will undoubtedly reshape various industries.In conclusion, Plasma Cutting Inc.'s new technology for cutting painted metal sets a new standard in the field of metal fabrication. By eliminating the need for paint removal, the company has revolutionized the production process, offering increased efficiency, superior quality, and design flexibility. Powered by their commitment to innovation, Plasma Cutting Inc. continues to lead the way in advancing the capabilities of the industry and remains a trusted partner for manufacturers seeking cutting-edge solutions.
High-Quality Metal Laser Cutting Services
Custom Metal Laser Cutting: The Perfect Solution for Precision Metal FabricationIn today's fast-paced manufacturing industry, precision and efficiency are key factors in delivering high-quality metal products. Custom metal laser cutting has become an indispensable technology for manufacturers seeking to meet their customers' demands for precision and complex metal designs. With its ability to cut through various types of metals with precision and speed, custom metal laser cutting has revolutionized the metal fabrication process.At the forefront of this cutting-edge technology is [Company Name], a leading provider of custom metal laser cutting services. With a state-of-the-art facility and a team of skilled engineers and technicians, [Company Name] has been delivering top-quality metal cutting solutions for a wide range of industries, including automotive, aerospace, medical, and more. The company's commitment to innovation, precision, and superior customer service has made them a trusted partner for manufacturers nationwide.The custom metal laser cutting process offered by [Company Name] utilizes advanced laser cutting machines that are capable of cutting a variety of metals, including stainless steel, aluminum, copper, and more. The use of laser technology allows for unparalleled precision and accuracy, resulting in clean cuts and smooth edges. This ensures that the finished metal products meet the highest standards and exceed customer expectations.One of the key advantages of custom metal laser cutting is its ability to handle complex designs and intricate patterns with ease. Traditional cutting methods often struggle with intricate designs, but with custom metal laser cutting, manufacturers can bring even the most intricate designs to life with precision and efficiency. This level of precision allows for greater design flexibility and opens up new possibilities for creating unique and innovative metal products.Furthermore, custom metal laser cutting offers cost-effective solutions for manufacturers. The speed and efficiency of laser cutting machines reduce the turnaround time for metal fabrication, leading to increased productivity and cost savings. In addition, the precise nature of laser cutting minimizes material waste, which further contributes to cost reduction. This makes custom metal laser cutting an attractive option for manufacturers looking to optimize their production processes.[Company Name] takes pride in its ability to fulfill the precise and diverse needs of its customers. From prototype development to full-scale production runs, the company delivers tailor-made solutions to meet the specific requirements of each project. The in-house team of design and engineering experts at [Company Name] works closely with clients to understand their unique needs and create customized metal cutting solutions that exceed expectations.The company's commitment to quality and precision is evident in its rigorous quality control procedures. Every metal product that comes out of [Company Name]'s facility undergoes thorough inspection to ensure that it meets the highest standards of quality and accuracy. This dedication to quality has earned [Company Name] a reputation for reliability and excellence in the metal fabrication industry.In conclusion, custom metal laser cutting has become an indispensable technology for manufacturers seeking precision, efficiency, and cost-effective solutions in metal fabrication. [Company Name] has established itself as a leader in the field, offering top-quality custom metal laser cutting services to a wide range of industries. Their state-of-the-art facility, skilled team, and dedication to precision and quality make them a trusted partner for manufacturers looking to elevate their metal fabrication processes. With custom metal laser cutting, manufacturers can bring their most intricate designs to life, all while achieving greater efficiency and cost savings.
Essential Guide to Structural Welding Techniques and Safety Measures
Structural Weld, a leading provider of high-quality welding solutions, has announced the launch of their latest advanced welding technology. With over 20 years of experience in the industry, the company has established a strong reputation for delivering innovative and reliable welding products to meet the diverse needs of their customers. This new technology sets a new standard for structural welding, providing improved efficiency, performance, and quality in welding applications across various industries.The new welding technology from Structural Weld is designed to enhance productivity and precision in welding operations. Equipped with advanced features and cutting-edge technology, this latest offering is set to revolutionize the welding industry. Whether it is for heavy-duty structural applications, automotive manufacturing, or aerospace engineering, the new technology is engineered to deliver exceptional results and meet the growing demands of modern welding processes.One of the key highlights of this new technology is its superior welding capabilities. The advanced welding system offers greater control and precision, allowing for the seamless joining of metal components with enhanced strength and durability. This is particularly crucial in structural welding applications, where the integrity and quality of welds are critical for the safety and performance of the final product. With the new welding technology, customers can expect to achieve superior weld quality and consistency, thereby reducing the need for rework and improving overall operational efficiency.Moreover, the new technology from Structural Weld also brings significant advancements in terms of efficiency and cost-effectiveness. By optimizing the welding process and minimizing material wastage, the technology enables customers to achieve higher productivity while reducing operational costs. This is particularly beneficial for companies looking to streamline their welding operations and improve their bottom line. Additionally, the new technology is designed to be user-friendly, offering ease of operation and maintenance, further enhancing its value proposition for customers.In addition to its technical capabilities, Structural Weld has also emphasized the importance of safety in the design and implementation of the new welding technology. Integrated safety features and robust quality control mechanisms are incorporated into the system to ensure that welding operations are carried out in compliance with industry standards and regulations. This commitment to safety not only reflects the company's dedication to delivering reliable and secure welding solutions but also reinforces their position as a trusted partner for customers across various sectors."We are excited to introduce our latest welding technology, which represents a significant milestone in our ongoing commitment to innovation and excellence," said [spokesperson] at Structural Weld. "With this new offering, we aim to empower our customers with the advanced capabilities they need to elevate their welding processes to new heights of performance and efficiency. We believe that the technology will make a meaningful impact on the industry and provide unparalleled value for our customers."As an industry leader in welding solutions, Structural Weld has consistently demonstrated their ability to stay at the forefront of technological advancements and deliver best-in-class products and services. The company's commitment to continuous improvement and customer satisfaction has earned them a strong reputation within the welding community. With the introduction of their latest welding technology, Structural Weld is poised to further solidify their position as a preferred partner for welding solutions among businesses and professionals seeking superior quality and reliability.In conclusion, the launch of the new welding technology from Structural Weld represents a significant development in the welding industry. By combining advanced capabilities, efficiency, and safety features, the technology sets a new standard for structural welding, addressing the evolving needs of modern manufacturing and engineering practices. With its potential to enhance productivity, precision, and cost-effectiveness, the new technology is expected to make a positive impact on the welding operations of businesses across various sectors. Structural Weld continues to demonstrate their dedication to innovation and excellence, positioning themselves as a trusted leader in welding solutions for the future.