- Home
- Blog
- Seamless Stainless Steel Pipe Fittings: The Latest Innovation in Elbow Technology from China
Seamless Stainless Steel Pipe Fittings: The Latest Innovation in Elbow Technology from China
By:Admin
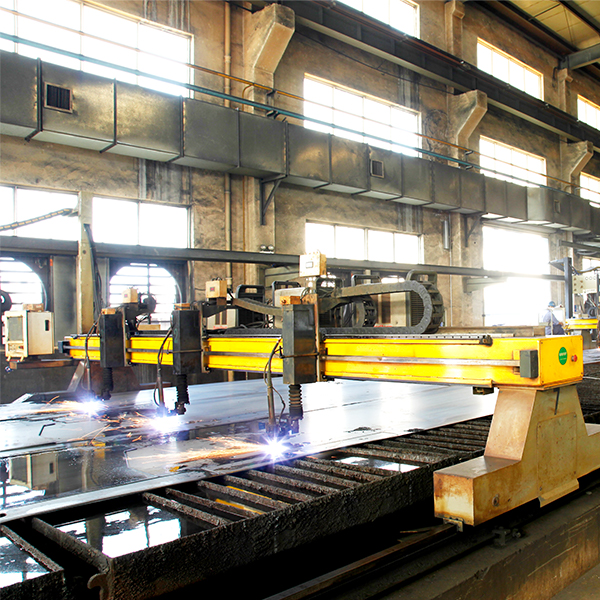
Seamless Stainless Steel Pipe Fitting Elbow prides itself on its ability to provide seamless pipe fittings, which are manufactured using the best quality materials and state-of-the-art technology. The company's product line includes elbow, tee, reducer, cap, flange, and other components needed in the plumbing and piping industry.
With years of experience, the company has built a reputation based on its commitment to delivering only premium-quality products and services to its customers worldwide. The company believes in the continued investment in research and development, which helps them to keep up with the latest technologies and trends in the industry.
Seamless Stainless Steel Pipe Fitting Elbow's products are used in various industries including chemical, petrochemical, oil and gas, water treatment, power generation, mining, and many more. The stainless steel fittings are corrosion-resistant and have high strength, making them ideal for use in hostile environments.
One of the key features of Seamless Stainless Steel Pipe Fitting Elbow is its ability to customize products based on clients' unique needs. The company offers a wide range of customization options to meet the specific needs of the customers.
The company has a team of highly experienced and skilled engineers who work tirelessly to ensure that the products are of the highest quality. Before release, the products go through a rigorous testing process to ensure they meet the required standards.
The company's management is committed to providing excellent customer service by maintaining constant communication with clients and providing timely solutions to any issues that arise.
Seamless Stainless Steel Pipe Fitting Elbow has a global outreach with products widely distributed in Asia, Europe, Africa, and the Americas. The company has a vast client base that ranges from small and medium-sized enterprises to large multinational corporations.
Recently, the company unveiled a state-of-the-art production facility, which is aimed at increasing production capacity and improving product quality. The new plant has incorporated the latest technologies to ensure smooth and efficient operations.
Seamless Stainless Steel Pipe Fitting Elbow is committed to adhering to highest ethical standards and has implemented various measures to ensure that its operations are environmentally friendly. By being eco-friendly, the company hopes to contribute to environmental conservation and sustainable development.
In conclusion, Seamless Stainless Steel Pipe Fitting Elbow is a top-quality brand in the manufacturing of stainless steel pipe fittings. The company's commitment to quality, efficiency, and durability has earned it a global reputation. Its products are widely used in various industries and its ability to customize products to meet specific needs sets it apart from the competition. The company continues to invest in research and development to keep up with the latest technologies and innovations in the industry. With a global outreach, Seamless Stainless Steel Pipe Fitting Elbow is set to remain a market leader in the stainless steel pipe fittings industry.
Company News & Blog
Sheet Metal Fabrication Services in the USA at Competitive Prices
Sheet Metal Fabrication Shop: Providing Quality Sheets for Your Manufacturing NeedsIn today's manufacturing industry, sheet metal fabrication is an integral part of producing finished products. From appliances, automotive parts, to custom enclosures, sheet metal is the backbone of every product that requires strength, durability, and precision.To meet the demands of this competitive market, industries turn to sheet metal fabrication shops to provide high-quality sheets and services. These shops specialize in the production, designing, and finishing of sheet metal products that meet the unique requirements of every client.Sheet metal fabrication shops play a crucial role in the manufacturing industry. Here's why:Fabrication CapabilitiesSheet metal fabrication shops have advanced technology and a team of skilled professionals that can handle even the most complex sheet metal projects. They use computer-aided design (CAD) and computer-aided manufacturing (CAM) to create precise and accurate designs that can be easily edited and modified. With their cutting-edge machines and techniques, they can create any shape, size, or design you require.High-Volume Precision ServicesSheet metal fabrication shops pride themselves on providing high-volume precision services. They ensure that every piece of sheet metal they produce meets the exact specifications set by the client. They use a variety of tools and techniques, such as CNC machining, stamping, laser cutting, and welding, to produce sheet metal products that are durable, safe, and meet all industry standards.Fast Delivery OptionsThe fast-paced manufacturing industry demands quick turnaround times. Sheet metal fabrication shops understand the importance of delivering finished products on time, every time. They prioritize meeting deadlines and have streamlined processes to ensure that each project is delivered promptly without compromising quality.Competitive PricingSheet metal fabrication shops offer competitive pricing for their products and services. With their advanced technology and streamlined processes, they can provide cost-effective solutions to meet every client's needs while maintaining the highest quality standards.In conclusion, sheet metal fabrication shops play an essential role in the manufacturing industry. They take pride in providing high-quality sheet metal products that meet the specific needs of their clients. They have the experience, expertise, and technology to handle any sheet metal project, big or small, and deliver it on time and within budget with competitive pricing. If you require sheet metal products, turn to a reputable sheet metal fabrication shop to ensure that your products are safe, durable, and of the highest quality.
Welding Techniques for Joining Stainless Steel and Mild Steel - Available for Sale in China
Welding stainless steel and mild steel together is a challenging task. It requires expertise, precision and high-quality equipment. The process involves joining two materials with different chemical and mechanical properties, which can lead to cracking, distortion and other issues if not done correctly. In this blog, we will explore the process of welding mild steel to stainless steel and some of the challenges that come with it.First, let's look at the materials themselves. Stainless steel has a high chromium content, which makes it resistant to corrosion and stains. It is also harder and more brittle than mild steel, which is why it is challenging to weld the two materials together. Mild steel, on the other hand, has a lower carbon content, making it more ductile and easier to work with when compared to stainless steel.When welding stainless steel to mild steel, there are several methods to consider. Let's take a closer look at some of the most popular welding techniques.1. TIG (Tungsten Inert Gas) Welding: This is one of the most popular welding techniques used in welding stainless steel to mild steel. It provides a precise, clean and high-quality weld, making it ideal for applications that require a high degree of accuracy.2. MIG (Metal Inert Gas) Welding: This is a more straightforward technique compared to TIG welding. It is faster, easier to learn and produces a durable weld. However, the quality of the weld is lower than TIG welding, which may not be suitable for high-end applications.3. Stick Welding: This is a versatile welding method that can be used to weld different materials. It produces a rugged and robust weld that can withstand high temperatures, making it ideal for industrial applications.Regardless of the welding technique used, welding stainless steel to mild steel requires proper preparation. The surface must be clean, free of rust, oil and other contaminants that can affect the quality of the weld. Additionally, the two metals must be preheated to ensure that the thermal stresses are minimized during the welding process.One of the biggest challenges when welding stainless steel to mild steel is the difference in melting points. Stainless steel has a much higher melting point than mild steel, which means that it can easily warp or crack if the welder is not careful. Hence, it is crucial to use specialized welding techniques and equipment to ensure that the two materials are welded together properly without cracking or distortion.In conclusion, welding stainless steel to mild steel can be a daunting task, but it is possible with the right skills, tools, and techniques. With proper preparation and welding processes, it is possible to achieve a strong and durable weld between the two materials. If you need more information on welding stainless steel to mild steel or other welding-related topics, please feel free to reach out to our team of experts.
Plasma Cutting Machines Manufactured in China by Langzhi Factory for Sale: A Comprehensive Guide to Choosing Material and Application Techniques
CNC Plasma Cutting Service: Improving Precision and Efficiency of Industrial CuttingIn the industrial world, precision cutting is a necessity for achieving optimal efficiency and productivity. Technology has greatly advanced this sector with the advent of CNC plasma cutting machines.Plasma cutting is the process of cutting metals and other conductive materials by using a plasma torch powered by compressed gas and an electrical arc. CNC plasma cutting machines operate under computer numerical control (CNC) which allows for precise cutting according to programmed designs. These machines are widely used in industries such as automotive, construction, metal fabrication, and aerospace.China is one of the leading manufacturers of CNC plasma cutting machines, with Langzhi Plasma Cutting Machine among the top producers in the country. Their machines come in a wide range of sizes and configurations, suitable for various cutting needs.With CNC plasma cutting technology, businesses can achieve utmost precision with fast and smooth cutting. The accuracy of the cuts is not limited by human error, ensuring that the final product matches the design.Furthermore, the automation of the cutting process means that CNC plasma cutting is much faster than manual cutting methods. This leads to reduced lead times and faster turnaround for clients.CNC plasma cutting technology can also handle a wide variety of metals and alloys such as steel, aluminum, copper, and brass, making it versatile for different applications.Moreover, CNC plasma cutting can be utilized for both small and large-scale projects. From a simple design to a complex one, CNC plasma cutting delivers high-quality results consistently. It can handle thick and thin metal sheets with ease and precision.In addition, CNC plasma cutting is also a cost-effective solution. The investment in the technology pays off in the long-term by increasing efficiency and productivity, and reducing material waste through precise cutting.In conclusion, CNC plasma cutting is a valuable technology in the industrial sector. The benefits of CNC plasma cutting go beyond precision and speed, as it also offers versatility, cost-effectiveness, and consistency in quality of output.If you're looking to invest in CNC plasma cutting services, reach out to reputable manufacturers and suppliers in the industry. They can provide guidance and support in selecting the appropriate machine and materials to match your specific cutting needs.Overall, CNC plasma cutting is a vital innovation that is shaping the future of industrial cutting.
Understanding Welding Processes for Strong Material Joining
article on the latest advances in welding technology and their applications.Welding Technology Takes a Leap ForwardThe art of welding has come a long way since its inception in the late 19th century. With the advent of technology, welding has become a complex process that requires specialized knowledge and expertise. Over the years, developments in welding technology have made strides in advancing the science of welding and its applications. Today, welding technology encompasses a wide range of processes that cater to various needs across industries.One such technological advancement in welding is the emergence of TIG welding. TIG welding, or tungsten inert gas welding, is a high-precision process that utilizes a non-consumable tungsten electrode to produce a weld. The method involves striking an arc between the electrode and the workpiece, creating a pool of molten material that forms a strong bond between the two.The advantages of TIG welding are many. Firstly, it produces cleaner welds with little or no spatter. Secondly, the welds produced are of high quality and strength, making them ideal for use in critical applications. Thirdly, TIG welding allows for greater control over the welding process. This makes it possible to weld thin materials that would be difficult or impossible to weld using other welding methods.TIG welding technology has seen many advancements over the years. Some of the latest developments include the use of automated TIG welding systems that use robotics to produce high-quality welds with minimal human intervention. These systems are ideal for use in mass production environments, where speed and accuracy are critical.Another advancement in TIG welding technology is the use of pulsed TIG welding. Pulsed TIG welding produces a steady, low-voltage arc that alternates between high and low current pulses. This process makes it possible to weld with greater control and accuracy, producing welds that are free from distortion and other defects.In addition to TIG welding, there are several other welding technologies that have seen significant advancements in recent years. One such technology is laser welding. Laser welding is a high-precision process that uses a focused laser beam to melt and join materials. Laser welding produces welds that are strong, precise, and repeatable. This makes it ideal for use in the aerospace, automotive, and medical industries, among others.Another welding technology that has seen significant progress is friction stir welding (FSW). Friction stir welding is a solid-state process that involves using a rotating tool to join materials. Unlike conventional welding methods, FSW does not involve melting the materials. Instead, the process creates a solid-state bond between the materials, producing a weld that is stronger than the base materials.The advancements in welding technology have opened up new opportunities across industries. For example, TIG welding is now widely used in the aerospace industry to produce high-quality welds on critical components. Likewise, laser welding has found applications in the medical industry, where precision is essential. FSW has been used extensively in the automotive industry, where it has helped manufacturers produce lightweight, high-strength components.In conclusion, the advancements in welding technology have revolutionized the way materials are joined together. The emergence of TIG welding, laser welding, FSW, and other welding technologies has made it possible to produce high-quality welds that are strong, precise, and repeatable. As the demand for high-quality, precision welding continues to grow, we can expect to see further advancements in welding technology in the years to come.
Professional Welding Services: MIG and TIG Welding for Aluminum and Steel - Hourly Rates Available
Benefits of Large Format Laser Cutting Services for Your Business
Large Format Laser Cutting Service Revolutionizes Precision Cutting in the Manufacturing IndustryIn recent years, the manufacturing industry has witnessed a significant boom, fueled by technological advancements that have revolutionized production processes. One such innovation that is making waves is the Large Format Laser Cutting Service, offered by a pioneering company. This cutting-edge service has garnered widespread attention due to its ability to provide unparalleled precision cutting, enabling manufacturers to create intricate designs and bring their visions to life in a whole new way.The Large Format Laser Cutting Service utilizes state-of-the-art laser technology that can cut through a wide range of materials with utmost accuracy. Whether it is metal, wood, acrylic, or even fabric, this service ensures a flawless outcome that meets the highest industry standards. By employing a large-format laser cutting machine, manufacturers no longer have to worry about limitations in size or design complexity. With this cutting-edge technology, they can now take on projects of any scale, confidently pushing the boundaries of creativity and customization.The company behind this remarkable service, {}, is a recognized leader in the laser cutting industry. They pride themselves on their commitment to delivering cutting solutions that are both advanced and versatile, catering to the diverse needs of their clients. With a team of highly skilled technicians and state-of-the-art equipment, they have established themselves as a trusted partner for manufacturers seeking innovative cutting solutions.What sets {} apart from their competitors is their relentless pursuit of excellence and their unwavering dedication to customer satisfaction. The company understands that every project is unique and requires a tailored approach. Therefore, their team works closely with clients, offering expertise and guidance to ensure that the final outcome exceeds expectations.The Large Format Laser Cutting Service provided by {} offers several key advantages over traditional cutting methods. Firstly, it eliminates the need for molds, thereby reducing costs and production time significantly. Manufacturers can now create intricate cuts and complex designs without the constraints imposed by traditional cutting techniques, saving both time and money. Additionally, this service allows for highly precise, clean cuts, resulting in finished products of the highest quality.One industry that has greatly benefited from this cutting-edge technology is the automotive sector. With the increasing demand for customized designs and unique features, the Large Format Laser Cutting Service has become an invaluable tool for automotive manufacturers. It enables them to create intricate patterns, precise logos, and unique shapes that were once deemed unattainable. The service also facilitates the production of lightweight parts, contributing to the overall fuel efficiency and performance of vehicles.The furniture industry has also embraced the Large Format Laser Cutting Service, as it offers unparalleled precision in cutting both wood and acrylic. This allows manufacturers to create intricate designs and patterns that were previously only possible through manual labor, saving both time and costs. Moreover, the service enables furniture designers to unleash their creativity, resulting in pieces that are not only aesthetically pleasing but also structurally robust.The applications of the Large Format Laser Cutting Service are not limited to just the automotive and furniture industries. It has found use in industries as diverse as signage, electronics, aerospace, and architecture. The versatility of this service has opened up a world of possibilities for manufacturers, empowering them to create products that are truly extraordinary.With the continuous advancement of laser technology, the possibilities for the Large Format Laser Cutting Service seem limitless. As manufacturers continue to push the boundaries of design and customization, this service will undoubtedly play a pivotal role in shaping the future of the manufacturing industry. With {} at the forefront of this innovation, manufacturers can expect nothing less than cutting-edge solutions that redefine precision cutting.
Demand for High-Quality Elbow Fittings Increases in Construction Industry
In the world of plumbing and construction, stainless steel is an essential material that has earned its reputation for its durability, strength, and resistance to corrosion. One of the primary components of plumbing systems that use stainless steel pipes is the stainless steel elbow, which is indispensable in redirecting the flow of fluids through the system.One of the leading manufacturers of stainless steel elbows in the industry is [Company name], a company that has cemented its place as a reliable and innovative manufacturer of plumbing fittings. The company has been in operation for over {number of years} years and has earned a reputation for maintaining the highest standards of quality in all its products.[Company name] manufactures various types of stainless steel elbows that are designed, developed, and manufactured to meet the diverse needs of the plumbing and construction industries. The company uses state-of-the-art technology, coupled with high-quality raw materials, to create durable and functional stainless steel elbows that are ideal for a wide range of applications.One of the standout features of [Company name]'s stainless steel elbows is their ability to withstand high-pressure environments. This is because the company uses high-grade stainless steel that has been engineered to maintain its structural integrity even under intense pressure. As a result, their products are ideal for use in systems that deal with corrosive fluids, high-temperature environments, and other challenging conditions.Additionally, [Company name]'s stainless steel elbows exhibit excellent resistance to a wide range of chemicals, ensuring that they can be used in an array of plumbing applications. This feature makes their products a popular choice for use in industries such as pharmaceuticals, food and beverage, and chemical production, among others.[Company name]'s team of skilled and experienced professionals is committed to ensuring that their products meet the highest standards of quality and safety. The company adheres to stringent quality control measures, from sourcing raw materials to the finished product's final inspection, to ensure that their stainless steel elbows are of the highest quality possible.The company's customer-centric approach has earned them a loyal customer base, with clients singling out their exceptional customer service experience. [Company name] provides comprehensive support to its customers, from initial product recommendations to after-sales support.In summary, [Company name] is a leading manufacturer of high-quality stainless steel elbows that are engineered to meet the highest standards of quality, durability, and functionality. Their products are ideal for use in a wide range of plumbing applications and are designed to withstand harsh environments, high-pressure systems, and corrosive fluids. By maintaining excellent customer service standards, [Company name] has earned its place as a trusted and reliable plumbing fittings manufacturer in the industry.
Techniques for Welding Thin Sheets of Stainless Steel
Welding Thin Stainless Steel: Tips and Tricks for Perfect WeldsStainless steel is a popular choice of material for many applications due to its corrosion resistance, durability, and aesthetic appeal. However, welding thin sheets of stainless steel can be a challenging task, requiring careful preparation, skill, and the right equipment. In this blog post, we will provide some tips and tricks for welding thin stainless steel, including the use of advanced welding techniques and tools to achieve the perfect weld.PreparationBefore you begin welding thin stainless steel sheets, it is essential to prepare the workpiece properly. First, ensure that the surfaces to be welded are clean and free of any contaminants that may affect the quality of the weld. Use a degreaser or solvent to remove any oil, dirt, grease or oxide layers that may be present on the surface. You can also use a wire brush or grinder to remove the oxide layer and create a clean surface for welding.Next, ensure that the edges of the workpieces are aligned properly, with an even gap of around 1-2mm between them. A precise fit is essential for achieving a good weld, so take the time to check and recheck the alignment before beginning the welding process.TechniquesSeveral advanced welding techniques can be used to weld thin sheets of stainless steel, including TIG (Tungsten Inert Gas) welding and laser welding. TIG welding is a popular choice for welding thin stainless steel sheets because it offers precise control over the welding process, a high-quality finish, and the ability to weld various types of stainless steel.With TIG welding, the torch is held by the welder, and the other line feeds behind the weld using parts of pie plates and other forms of bendy stuff to dam the argon behind the weld. This technique ensures that the weld is protected by an argon gas shield, preventing the weld from being contaminated by oxygen and other atmospheric gases.Another option for welding thin stainless steel is laser welding. Laser welding uses a high-energy laser beam to join the workpieces, resulting in a precise, high-quality weld. Laser welding is particularly useful for welding complex shapes and contours, and it is ideal for welding thin sheets of stainless steel, where precision is essential.ToolsTo achieve the perfect weld on thin stainless steel, it is essential to have the right tools. Some of the key tools you will need for welding thin sheets of stainless steel include a TIG welding machine, a suitable electrode, filler wire, and an argon gas cylinder.A high-quality TIG welding machine is essential for achieving precise control over the welding process, enabling you to adjust the weld speed, current, and voltage for optimal results. The right electrode and filler wire are also critical, as they dictate the quality and strength of the weld.ConclusionWelding thin sheets of stainless steel requires careful preparation, skill, and the right equipment. By following the tips and tricks outlined in this blog post, including proper preparation, advanced welding techniques, and the use of quality tools, you can achieve perfect welds every time. Whether you choose TIG welding or laser welding, remember to take your time, stay focused, and enjoy the impressive results that you can achieve with thin steel.
Watch the Best Sheet Metal Fabrication Videos Online
Title: Unveiling the Craft: Exploring the World of Metal FabricationIntroduction (Approximately 100 words):Metal fabrication, an essential manufacturing process that shapes raw metal sheets into intricate and functional structures, plays a vital role in various industries. From automotive parts to machinery components, the applications of metal fabrication are boundless. In this blog post, we delve into the intriguing world of metal fabrication, shedding light on the processes, techniques, and advantages that make it an indispensable aspect of modern manufacturing. Join us as we unravel the secrets behind the creation of awe-inspiring metal structures and explore the possibilities offered by a reliable Metal Fabrication Factory.1. The Art of Sheet Metal Fabrication (Approximately 200 words):Sheet metal fabrication, also known as metalworking, is a highly intricate process that involves converting raw metal sheets into products of various shapes and sizes. Through a combination of cutting, bending, and shaping techniques, skilled fabricators transform plain metal sheets into detailed structures that serve a multitude of purposes.At a Metal Fabrication Factory, advanced machinery and equipment are utilized to achieve precise results while ensuring efficiency. CNC laser cutting machines, for instance, provide accurate and consistent cuts, while hydraulic presses enable intricate bending and forming of metals. Welding and surface finishing processes are also essential to enhance the aesthetic appeal and durability of the fabricated metal structures.2. Industries Served by Metal Fabrication (Approximately 200 words):Metal fabrication caters to an extensive range of industries and sectors. From construction and architecture to transportation and manufacturing, the applications are limitless. For example, in the construction industry, architectural metalwork such as staircases, handrails, and structural components are fabricated to ensure functionality, strength, and aesthetic appeal.The automotive industry heavily relies on metal fabrication to manufacture critical components like chassis, exhaust systems, and suspension parts. Metal fabrication is also crucial in the production of electrical enclosures, HVAC systems, and machinery components that are utilized in various manufacturing plants.3. The Advantages of Metal Fabrication (Approximately 200 words):Metal fabrication offers numerous advantages that make it the go-to manufacturing process for countless industries. First and foremost is the versatility it provides. Metal can be shaped into intricate designs and structures, making it suitable for both functional and aesthetic purposes. Additionally, metals are inherently strong and durable, ensuring the longevity of fabricated products.Moreover, metal fabrication allows for quick prototyping and customization. By utilizing computer-aided design (CAD) software, fabricators can create detailed digital designs, optimize them for precision, and then produce multiple replicas with ease.Furthermore, metal fabrication is a cost-effective solution as it eliminates the need for intricate assembly processes that add to the overall expenses. By integrating multiple manufacturing steps into one streamlined process, metal fabrication increases efficiency and reduces production time.4. Choosing a Metal Fabrication Factory (Approximately 200 words):When selecting a metal fabrication factory, various factors must be considered to ensure high-quality results. Look for a facility equipped with state-of-the-art machinery and cutting-edge technology that can meet your specific project requirements. Cross-check the factory's capabilities, such as laser cutting, bending, welding, and finishing, to ensure they align with your needs.Certifications and industry credentials are also important indicators of the fabricator's reliability and expertise. Prioritize a factory that adheres to international standards to guarantee exceptional quality and compliance with regulatory norms.Additionally, consider the factory's experience in your specific industry. A well-established fabricator with a portfolio of successful projects in your desired sector is more likely to understand the unique challenges and deliver tailored solutions.Conclusion (Approximately 100 words):Metal fabrication remains an essential pillar of modern manufacturing, enabling the creation of intricate and durable structures in diverse industries. The artistry and skill behind metal fabrication, combined with advanced machinery and technology, make it a captivating subject to explore. By partnering with a trustworthy Metal Fabrication Factory, businesses can unlock the potential of this versatile process, leveraging its advantages to bring their innovative ideas to life. So, whether you require custom architectural metalwork or need precise automotive components, metal fabrication is the key to turning your visions into reality.
Key Information on Choosing the Right Welding Electrode for Your Project
Title: Revolutionary Welding Electrode Innovates the Industry - Improving Efficiency and QualityIntroduction:In the ever-evolving world of welding technology, companies are continuously seeking new advancements to enhance efficiency and quality. In line with this demand, {Company Name}, a renowned industry leader, has introduced an innovative welding electrode that promises to revolutionize the field. This welding electrode, which boasts incredible capabilities, is set to transform welding processes, streamline operations, and deliver exceptional results like never before.Company Overview:{Company Name}, a well-established welding solutions provider, has a rich history of delivering cutting-edge products. With a commitment to quality and continuous innovation, the company has become a trusted partner for various industries, including automotive, construction, oil and gas, and manufacturing. Their team of skilled engineers and technicians work diligently to develop advanced welding technologies that address industry challenges and meet customer needs.Revolutionary Welding Electrode:The latest offering from {Company Name}, which we shall refer to as the "Advanced Welding Electrode," is the result of years of research and development. This innovative product is designed to enhance welding operations by improving efficiency, productivity, versatility, and overall welding quality.Improved Efficiency and Productivity:The Advanced Welding Electrode incorporates state-of-the-art features that significantly improve efficiency and productivity. Its enhanced coating formulation ensures smooth and steady arc stability, resulting in reduced spatter and welding defects. This attribute greatly decreases post-welding clean-up time, allowing welders to operate more efficiently and complete projects in a shorter duration.Moreover, the electrode's excellent heat dissipation properties minimize the risk of overheating, reducing downtime due to material damage and equipment failure. This feature, combined with its exceptional tie-in wetting ability, ensures seamless fusion between metals, maximizing welding productivity and minimizing waste.Enhanced Versatility and Adaptability:{Company Name}'s Advanced Welding Electrode offers superior adaptability to a wide range of welding scenarios. It is suitable for various metals, including carbon steel, stainless steel, and non-ferrous alloys. This versatile electrode performs exceptionally well in all welding positions, allowing welders to work with ease and confidence while maintaining high-quality standards.Additionally, the electrode's unique self-releasing slag formula improves welder visibility during the welding process. This enhancement promotes precise control and accuracy, resulting in meticulously welded joints, especially in complex and intricate welding projects.Uncompromised Welding Quality:The focus on welding quality is evident in every aspect of the Advanced Welding Electrode. Its remarkable arc stability, combined with minimal spatter and excellent slag control, ensures clean and smooth welds with minimal defects. This remarkable weld integrity is further reinforced by the electrode's ability to eliminate undesirable elements like sulfur and phosphorus, guaranteeing welds of exceptional quality and longevity.Moreover, {Company Name} has implemented rigorous quality control processes to guarantee consistent electrode performance. The company subjects each electrode batch to comprehensive testing, including tensile strength, elongation, and impact toughness assessments. This dedication to quality assurance provides customers with utmost confidence in the product's reliability and performance.Conclusion:{Company Name}'s introduction of the Advanced Welding Electrode is poised to create a significant impact in the welding industry. With its advanced features, enhanced efficiency and productivity, versatility, and unwavering commitment to welding quality, this revolutionary electrode presents unmatched benefits for welders across various industries.As {Company Name} continues to innovate and provide cutting-edge solutions, the Advanced Welding Electrode is a testament to their dedication towards empowering welders and revolutionizing the welding industry. The progressive strides made by {Company Name} demonstrate their commitment to meeting the evolving needs of the market while ensuring sustainable success for their customers.