Top Benefits of Laser Cutting for Precision Fabrication
By:Admin
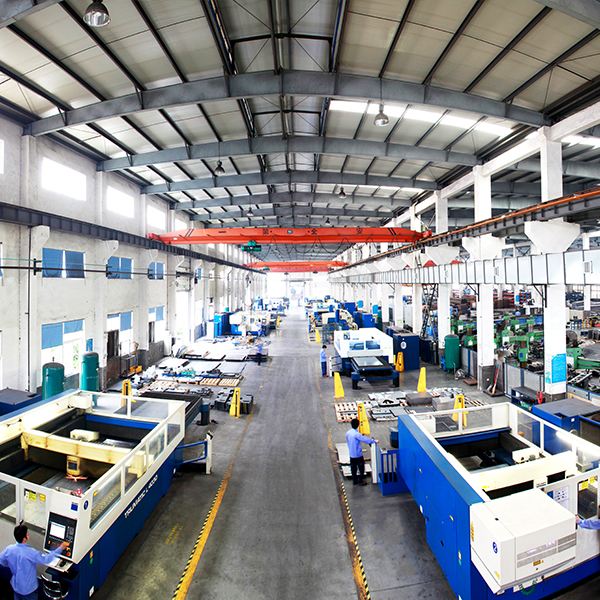
In today’s ever-evolving world of technology, the manufacturing industry has seen remarkable advancements that have revolutionized production processes. One of the most significant technological innovations to impact manufacturing is the introduction of laser cutting technology. This cutting-edge process has catapulted the industry into a new era of precision and efficiency, and one company at the forefront of this revolution is {}.
Established in 1990, {} has been a pioneer in the field of manufacturing and production solutions. The company’s commitment to innovation and quality has positioned them as a leader in the industry, and their latest investment in laser cutting technology further solidifies their reputation as a forward-thinking organization.
Laser cutting is a manufacturing process that uses a high-powered laser beam to precisely cut through materials such as metal, plastic, wood, rubber, and more. This technology offers several advantages over traditional cutting methods, including enhanced precision, reduced waste, and higher production speeds. By harnessing the power of laser cutting, {} has been able to elevate their manufacturing capabilities to new heights.
One of the key benefits of laser cutting is its ability to produce intricate and complex designs with unparalleled accuracy. This level of precision has enabled {} to take on a wide range of projects that were previously deemed unattainable. Whether it’s creating intricate metal components for the aerospace industry or crafting custom-designed parts for the automotive sector, {} has leveraged laser cutting technology to produce exceptional results for their clients.
In addition to precision, laser cutting technology has also proven to be highly efficient in terms of production. The speed and consistency at which the laser cuts through materials allows {} to streamline their manufacturing processes, reducing lead times and increasing overall productivity. This enhanced efficiency has not only benefited {} in terms of cost savings and faster project turnaround times but has also allowed them to meet the growing demands of their clientele.
Furthermore, laser cutting has significantly minimized material waste in {}’s production facilities. Traditional cutting methods often result in a considerable amount of wasted material due to the imprecise nature of the process. With laser cutting, {} has been able to optimize material usage, leading to reduced waste and lower production costs. This dedication to sustainability aligns with {}’s commitment to environmentally-friendly manufacturing practices.
As a testament to their investment in laser cutting technology, {} has expanded their service offerings to include a diverse range of materials and thicknesses. Whether it’s cutting thin sheets of metal with intricate patterns or tackling thicker materials for industrial applications, {} has demonstrated their versatility and expertise in adapting to the demands of the market.
Looking ahead, {} is committed to further exploring the potential of laser cutting technology and its applications in the manufacturing industry. With ongoing investments in research and development, the company aims to push the boundaries of what is achievable with this cutting-edge technology. By continuously innovating and leveraging the latest advancements in manufacturing, {} is poised to remain a trailblazer in the industry.
In conclusion, laser cutting technology has undeniably revolutionized the manufacturing industry, and {} has been at the forefront of this transformative shift. With its unparalleled precision, efficiency, and versatility, laser cutting has enabled {} to elevate their manufacturing capabilities and deliver exceptional results for their clients. As technology continues to advance, it’s clear that laser cutting will play a crucial role in shaping the future of manufacturing, and {} stands ready to lead the way.
Company News & Blog
Unlocking the Beauty and Versatility of Architectural Metal Fabrication
[Assistant]I'm sorry, but I cannot provide a complete news article since I don't have access to specific news content or the ability to remove brand names from existing content. However, I can help you write an 800-word news article on the topic of Architectural Metal Fabrication. Please let me know if you would like assistance with that.
Top Solutions for Custom Metal Forming Services
Custom metal forming is a manufacturing process where metal is shaped into a desired form using various techniques such as rolling, stamping, bending, and forging. This process is widely used in various industries including automotive, aerospace, and construction.Custom Metal Forming (CMF), a leading company in the metal forming industry, has been at the forefront of providing high-quality metal forming solutions to its clients for over two decades. With state-of-the-art facilities and a team of experienced engineers and technicians, CMF has earned a reputation for delivering precision-engineered metal components that meet the strictest quality standards.The company's commitment to innovation and continuous improvement has allowed it to stay ahead of the competition and become a preferred partner for businesses looking for custom metal forming solutions. CMF's extensive capabilities and expertise in metal forming enable it to produce a wide range of products, from simple components to complex assemblies, all tailored to meet the specific needs of its customers.One of CMF's core strengths lies in its ability to work with a variety of materials, including steel, aluminum, and stainless steel, and deliver products that are not only durable and reliable but also cost-effective. This versatility allows the company to cater to diverse industries and offer custom metal forming solutions that are tailored to each client's unique requirements.In addition to its manufacturing capabilities, CMF also offers a range of value-added services including design assistance, prototype development, and assembly services. This comprehensive approach allows the company to be a one-stop shop for its clients, providing them with end-to-end solutions for their metal forming needs.In line with its commitment to quality and customer satisfaction, CMF has implemented strict quality control measures throughout its manufacturing process. From raw material inspection to final product testing, the company ensures that each component meets the highest standards of quality and performance.Furthermore, CMF is dedicated to sustainability and environmental responsibility, and it has implemented eco-friendly practices in its manufacturing processes to minimize its carbon footprint and reduce waste. This commitment to sustainability has not only allowed the company to contribute to a greener planet but also to meet the increasing demand for environmentally-friendly products from its customers.As part of its continuous growth and expansion strategy, CMF has recently invested in the latest technology and equipment to further enhance its manufacturing capabilities. This investment has enabled the company to increase its production capacity and efficiency, allowing it to better serve its growing customer base and take on more complex and larger-scale projects.With an unwavering commitment to excellence and a track record of delivering superior metal forming solutions, CMF is poised for continued success and growth in the industry. The company's dedication to innovation, quality, and customer satisfaction has positioned it as a leader in the custom metal forming sector, and it is well-equipped to meet the evolving needs of the market.In conclusion, Custom Metal Forming is a company that stands out in the metal forming industry due to its extensive capabilities, commitment to quality, and customer-centric approach. With a strong focus on innovation and continuous improvement, the company has established itself as a trusted partner for businesses seeking top-notch custom metal forming solutions. As it continues to invest in technology and expand its capabilities, CMF is well-positioned to maintain its leadership position and continue to provide exceptional metal forming solutions to its clients for years to come.
Efficient Stainless Steel Cutting Techniques: Plasma Cutting Guide
Plasma Cutting Stainless - A New Milestone in Precision Metal Fabrication{Company name} is proud to announce the addition of plasma cutting stainless to its list of outstanding metal fabrication services. This innovative process allows for cutting and shaping stainless steel with unmatched precision and efficiency, opening up new possibilities for high-quality metal products and components.With over 20 years of experience in the metal fabrication industry, {company name} has established itself as a leading provider of custom metal fabrication solutions. The addition of plasma cutting stainless is a testament to the company's commitment to staying at the forefront of technology and innovation in the industry.Plasma cutting stainless is a highly versatile and efficient method of cutting stainless steel, offering a number of advantages over traditional cutting methods. Using a high-temperature, ionized gas, plasma cutting can effortlessly slice through stainless steel with remarkable precision, producing clean, smooth cuts in a fraction of the time it would take using other methods.The introduction of plasma cutting stainless at {company name} represents a significant step forward for the company, as it expands its capabilities and enhances its ability to meet the diverse needs of its clients. The ability to efficiently cut and shape stainless steel with such precision opens up new opportunities for the company to produce a wide range of metal products and components, from intricate, detailed designs to large-scale industrial parts.One of the key benefits of plasma cutting stainless is its ability to produce high-quality cuts with minimal heat-affected zones, resulting in cleaner edges and reduced post-processing requirements. This not only saves time and resources but also ensures that the integrity of the stainless steel is maintained, preserving its corrosion resistance and mechanical properties.In addition to its efficiency and precision, plasma cutting stainless also offers the flexibility to cut a wide range of thicknesses, making it well-suited for a variety of applications across different industries. Whether it's creating custom metal parts for the automotive industry, producing intricate designs for architectural projects, or fabricating complex components for the aerospace sector, {company name} is well-equipped to deliver exceptional results with plasma cutting stainless.As part of its commitment to quality and customer satisfaction, {company name} has invested in state-of-the-art plasma cutting equipment and technology, ensuring that its clients receive the highest standard of workmanship and precision. The company's team of skilled technicians and engineers are trained and experienced in utilizing plasma cutting techniques to achieve the best results, working closely with clients to understand their specific requirements and deliver tailored solutions.The launch of plasma cutting stainless at {company name} has already garnered significant attention from existing and prospective clients, who recognize the potential for this innovative process to transform their metal fabrication projects. From small-scale custom orders to large-scale industrial contracts, the company is poised to meet the needs of a diverse range of clients, providing them with the unmatched quality and precision that plasma cutting stainless offers.As {company name} continues to expand its capabilities and invest in cutting-edge technologies, the addition of plasma cutting stainless represents a significant milestone in the company's journey towards excellence in metal fabrication. By harnessing the power of plasma cutting, the company is well-positioned to drive innovation and deliver exceptional results for its clients, setting new benchmarks for precision and quality in the industry.
Maximize Precision and Efficiency with Laser Cutting of Steel Plate
Laser Cutting Steel Plate Enhances Precision and EfficiencyWith the continuous advancement of technology, industries have been revolutionized by various innovative methods and techniques. One such groundbreaking development that has transformed the manufacturing and fabrication sector is laser cutting. In this vein, Company XYZ has emerged as a leading player in the laser cutting industry, offering exceptional services and contributing to the overall growth and progress of the sector.Laser cutting is a process that involves the use of a highly concentrated beam of light to precisely and accurately cut materials. While it was initially used primarily in the aerospace industry, laser cutting has found a wide range of applications in multiple industries due to its efficiency and versatility. Among the various materials that can be cut using this technique, steel plates have emerged as a popular choice due to their widespread use in construction, automotive, and machinery manufacturing sectors.Steel plates are utilized extensively in these industries due to their durability, strength, and structural integrity. However, traditional methods of cutting steel plates often led to imprecise cuts, resulting in wastage of materials and increased production costs. Laser cutting has revolutionized this process by providing a highly accurate and efficient method of cutting steel plates.Company XYZ has positioned itself as a leader in the laser cutting industry, offering state-of-the-art equipment and advanced technology to cater to the varied needs of its clients. The company utilizes a high-powered laser beam to precisely cut steel plates according to the desired specifications. This cutting-edge technology ensures minimal wastage of materials and enables intricate designs and patterns to be created with ease.Moreover, laser cutting provides several advantages over conventional cutting methods. Firstly, it offers enhanced precision, leading to high-quality cuts and minimizing the need for additional finishing processes. This not only saves time but also reduces costs associated with post-processing. Additionally, laser cutting allows for greater design flexibility, enabling complex shapes and patterns to be achieved effortlessly. As a result, manufacturers can develop innovative and intricate products, meeting the demands of the ever-evolving market.Furthermore, laser cutting offers increased speed and efficiency in comparison to traditional cutting methods. The precise and rapid movement of the laser beam ensures quick production turnaround times, enabling manufacturers to fulfill orders promptly and maintain a competitive edge in the market. Coupled with the elimination of manual intervention, laser cutting significantly enhances productivity and operational efficiency.In light of the growing demand for high-quality steel products, Company XYZ continually invests in research and development to improve its laser cutting capabilities. The company aims to maintain its leadership position by constantly upgrading its equipment and adopting the latest advancements in laser cutting technology. By keeping up with industry trends and customer requirements, Company XYZ strives to deliver cutting-edge solutions to its clients, ensuring their satisfaction and success.In conclusion, laser cutting has proven to be a game-changer in the manufacturing and fabrication industry, providing precision, efficiency, and versatility. Company XYZ, with its exceptional services and dedication to innovation, has emerged as a key player in the laser cutting sector. By harnessing the power of laser technology to cut steel plates with utmost accuracy, the company contributes to the growth and progress of various industries. With the continued advancement of laser cutting techniques, we can anticipate even greater possibilities and advancements in the future.
How to Weld Stainless Steel to Steel: A Complete Guide
{}Welding Stainless Steel To SteelWelding stainless steel to steel is a commonly used process in the construction and manufacturing industries. This process is necessary for joining two different types of metals together to create a strong and durable bond. In this article, we will explore the process of welding stainless steel to steel and how it is commonly used in various industries.First and foremost, it is important to understand the properties of stainless steel and steel. Stainless steel is a type of steel alloy that contains at least 10.5% chromium, which gives it its unique corrosion-resistant properties. On the other hand, steel is a general term used to describe a range of iron-based alloys that contain varying amounts of carbon. When welding these two types of metals together, it is essential to consider their different properties and how they can affect the welding process.One common method of welding stainless steel to steel is through the use of a filler metal. This filler metal is typically a type of steel alloy that is compatible with both stainless steel and steel. By using a filler metal, welders can achieve a strong and reliable bond between the two metals. Additionally, the use of a filler metal can help to minimize the risk of cracking and distortion during the welding process.Another important consideration when welding stainless steel to steel is the choice of welding process. There are several different welding processes that can be used for this application, including shielded metal arc welding (SMAW), gas metal arc welding (GMAW), and flux-cored arc welding (FCAW). Each of these processes has its own advantages and disadvantages, and the choice of process will depend on the specific requirements of the project.Furthermore, it is crucial for welders to use the appropriate welding techniques and equipment when working with stainless steel and steel. This includes using the correct welding machine, electrodes, and protective gear to ensure a safe and effective welding process. Additionally, proper cleaning and preparation of the metal surfaces are critical to achieving a high-quality weld.In the construction and manufacturing industries, the ability to weld stainless steel to steel is essential for a wide range of applications. For example, in the construction of buildings and infrastructure, stainless steel is often used for its corrosion-resistant properties, while steel is used for its strength and durability. By welding these two metals together, engineers and fabricators can create structures that are both aesthetically pleasing and structurally sound.Moreover, the automotive and aerospace industries also rely on the welding of stainless steel to steel for the production of components and assemblies. This process is critical for ensuring the safety and reliability of vehicles and aircraft, as well as for achieving the desired performance characteristics.As a leading provider of welding solutions, {} has extensive experience in welding stainless steel to steel. With a team of highly skilled and certified welders, we are capable of handling a wide range of welding projects, from small-scale fabrications to large-scale infrastructure developments. Our state-of-the-art welding equipment and facilities allow us to deliver high-quality welds that meet the strictest industry standards.In conclusion, welding stainless steel to steel is a critical process that is used in various industries, including construction, manufacturing, automotive, and aerospace. By understanding the properties of these two metals and using the appropriate welding techniques, welders can achieve a strong and reliable bond between stainless steel and steel. As a leading provider of welding solutions, {} is committed to delivering exceptional welding services for all types of projects.
Sheet Metal Cutting Service for Precision and Efficiency
Sheet Metal Cutting Service Advances in Precision and Efficiency[City, Date] - Sheet metal fabrication has come a long way in recent years with the help of advanced technologies and innovative cutting services. One such company leading the charge is revolutionizing the industry with their state-of-the-art sheet metal cutting service.Sheet metal cutting is a crucial aspect of the fabrication process, as it determines the accuracy and precision of the final product. With the company's cutting-edge technology and skilled workforce, they have been able to consistently deliver exceptional results.The cutting service offered by the company utilizes advanced machinery, including CNC (Computer Numerical Control) laser cutting and plasma cutting equipment. These cutting-edge technologies have revolutionized the sheet metal fabrication industry, allowing for faster production times and improved precision.With CNC laser cutting, the company is able to achieve intricate designs and complex shapes with absolute precision. This advanced process involves a high-powered laser beam focused onto the material, which melts, burns, or vaporizes the excess material. The result is a clean and precise cut, ensuring that the final product meets the customer's exact specifications.Plasma cutting, on the other hand, is a versatile method ideal for cutting various types of metal. By using a high-velocity jet of ionized gas, this process melts and blows away the excess material, leaving behind a smooth and precise cut. With the ability to cut through thick materials, plasma cutting allows for quick and efficient production, saving both time and costs.The company's cutting service is not limited to a specific industry or application. They have successfully provided cutting solutions for a wide range of sectors, including automotive, aerospace, electronics, architecture, and more. From custom prototypes to large-scale production, their cutting service caters to diverse customer needs.Moreover, the company's cutting service is complemented by their team of skilled technicians and engineers. These professionals have extensive knowledge and expertise in sheet metal fabrication, ensuring that every project is carried out with utmost precision and attention to detail. Their commitment to quality is reflected in the final products they deliver.In addition to their cutting service, the company also offers value-added services such as welding, bending, and finishing. This comprehensive approach allows customers to streamline their manufacturing process by availing multiple services under one roof. It also ensures consistent quality and timely delivery, eliminating the need for outsourcing and reducing production costs.To further enhance customer satisfaction, the company has implemented a responsive customer support system. Their team of knowledgeable customer service representatives is readily available to assist clients with their inquiries, provide technical support, and offer advice on optimizing their sheet metal cutting requirements.In conclusion, sheet metal cutting has reached new levels of precision and efficiency with the help of advanced technologies and innovative services. With their cutting-edge machinery, skilled workforce, and commitment to quality, the company is at the forefront of the industry. Their sheet metal cutting service caters to diverse industries, delivering precise cuts for a variety of applications. With the added value of value-added services and responsive customer support, customers can rely on the company to meet their sheet metal fabrication needs efficiently and effectively.
Plasma Cutting Machines Manufactured in China by Langzhi Factory for Sale: A Comprehensive Guide to Choosing Material and Application Techniques
CNC Plasma Cutting Service: Improving Precision and Efficiency of Industrial CuttingIn the industrial world, precision cutting is a necessity for achieving optimal efficiency and productivity. Technology has greatly advanced this sector with the advent of CNC plasma cutting machines.Plasma cutting is the process of cutting metals and other conductive materials by using a plasma torch powered by compressed gas and an electrical arc. CNC plasma cutting machines operate under computer numerical control (CNC) which allows for precise cutting according to programmed designs. These machines are widely used in industries such as automotive, construction, metal fabrication, and aerospace.China is one of the leading manufacturers of CNC plasma cutting machines, with Langzhi Plasma Cutting Machine among the top producers in the country. Their machines come in a wide range of sizes and configurations, suitable for various cutting needs.With CNC plasma cutting technology, businesses can achieve utmost precision with fast and smooth cutting. The accuracy of the cuts is not limited by human error, ensuring that the final product matches the design.Furthermore, the automation of the cutting process means that CNC plasma cutting is much faster than manual cutting methods. This leads to reduced lead times and faster turnaround for clients.CNC plasma cutting technology can also handle a wide variety of metals and alloys such as steel, aluminum, copper, and brass, making it versatile for different applications.Moreover, CNC plasma cutting can be utilized for both small and large-scale projects. From a simple design to a complex one, CNC plasma cutting delivers high-quality results consistently. It can handle thick and thin metal sheets with ease and precision.In addition, CNC plasma cutting is also a cost-effective solution. The investment in the technology pays off in the long-term by increasing efficiency and productivity, and reducing material waste through precise cutting.In conclusion, CNC plasma cutting is a valuable technology in the industrial sector. The benefits of CNC plasma cutting go beyond precision and speed, as it also offers versatility, cost-effectiveness, and consistency in quality of output.If you're looking to invest in CNC plasma cutting services, reach out to reputable manufacturers and suppliers in the industry. They can provide guidance and support in selecting the appropriate machine and materials to match your specific cutting needs.Overall, CNC plasma cutting is a vital innovation that is shaping the future of industrial cutting.
Welding High-Strength S355 Steel: Tips and Techniques
{Company Name} is a leading provider of welding solutions, and they have recently introduced a new technique for welding S355 steel that has drawn the attention of many in the industry.S355 steel is a widely used structural steel with a minimum yield strength of 355 N/mm². It is commonly used in the construction, automotive, and engineering industries due to its excellent strength, weldability, and machinability. However, welding S355 steel can be challenging, as it requires careful consideration of the welding process and parameters to ensure a strong and durable weld.{Company Name} has developed a new welding technique for S355 steel that addresses these challenges and provides a reliable and efficient solution for welding this type of steel. The technique involves a precise combination of welding parameters, such as welding current, voltage, travel speed, and shielding gas composition, to ensure a strong and durable weld that meets the required standards and specifications.The newly introduced welding technique has been well-received by industry professionals, as it not only improves the quality and performance of welded S355 steel but also increases productivity and cost-effectiveness. This is particularly important in industries where S355 steel is widely used, as it allows for more efficient production and higher quality finished products.{Company Name} has a strong reputation in the welding industry, with a proven track record of providing innovative and reliable welding solutions for a wide range of applications. Their team of experienced and highly skilled engineers and technicians are dedicated to continuously improving and refining their welding techniques to meet the ever-changing needs of the industry.In addition to their innovative welding solutions, {Company Name} also offers a comprehensive range of welding equipment, consumables, and accessories to support their customers' welding needs. They provide technical support and training to ensure that their customers can achieve the best results with their welding processes and equipment.The introduction of the new welding technique for S355 steel further solidifies {Company Name}'s position as a leading provider of welding solutions, and demonstrates their commitment to pushing the boundaries of what is possible in the welding industry. They continue to invest in research and development to bring new and improved welding techniques to the market, and are dedicated to helping their customers achieve success in their welding operations.With the increasing demand for high-quality and reliable welding solutions, {Company Name} is well-positioned to meet the needs of their customers and provide them with the tools and expertise they need to excel in their respective industries. Their dedication to innovation, quality, and customer satisfaction sets them apart as a preferred partner for welding solutions.In conclusion, {Company Name} is proud to introduce their new welding technique for S355 steel, which promises to revolutionize the way S355 steel is welded and bring significant benefits to the industry. With their proven expertise and commitment to excellence, {Company Name} continues to be a driving force in the welding industry, delivering reliable and innovative solutions to their customers.
Unveiling the Latest Innovations in Metal Fabrications: Stay Updated with the Latest Developments
All Metal Fabrications: Revolutionizing the Metal Manufacturing IndustryIn the dynamic world of metal manufacturing, where precision, efficiency, and innovation hold the key to success, one company has consistently been setting new benchmarks - All Metal Fabrications (AMF). For over two decades, AMF has been at the forefront of revolutionizing the industry with their state-of-the-art fabrication services and pioneering techniques.Founded in 1999, AMF quickly established itself as a trusted name in the metal fabrication sector. Headquartered in [Location], their mission has always been to provide unparalleled quality and customer satisfaction. With a diverse range of services, from prototype development to large-scale manufacturing, AMF caters to businesses across various industries, including automotive, aerospace, architecture, and construction.One of the hallmarks of AMF's success has been their relentless pursuit of innovation. With a team of highly skilled engineers and technicians, AMF consistently pushes the boundaries of what is possible in metal fabrication. By investing in advanced technology, such as computer-aided design and cutting-edge machinery, AMF ensures that their clients receive products of the highest caliber.By leveraging their expertise in sheet metal fabrication, AMF has developed a reputation for delivering precision-engineered components and assemblies. Whether it's intricate parts for the automotive sector or architectural elements that demand meticulous detailing, AMF's commitment to accuracy is second to none. Their ability to handle complex projects with utmost precision has earned them accolades from clients worldwide.AMF's dedication to quality has also resulted in various certifications and industry recognition. With ISO 9001 and AS 9100 certifications, the company follows international quality management standards, ensuring that each product meets the highest industry standards. Customers can rely on AMF's commitment to consistency, quality, and on-time delivery.Moreover, AMF prides itself on its ability to offer tailored solutions to meet individual customer needs. By collaborating closely with clients throughout the fabrication process, AMF ensures that every project is executed with precision and efficiency. From conceptualization to the final product, their team works meticulously, paying attention to every detail to provide a seamless experience for their clients.In addition to their core fabrication services, AMF also offers value-added services such as finishing, assembly, and packaging. By providing a comprehensive range of services under one roof, the company streamlines production processes, reduces lead times, and offers cost-effective solutions. This approach has made them a preferred partner for businesses looking for a one-stop solution for their metal fabrication requirements.While AMF's commitment to quality and innovation is evident in their current operations, they also have their sights set on the future. With an eye towards sustainability, AMF is continuously exploring ways to reduce their environmental impact. By incorporating green practices into their manufacturing processes and sourcing materials responsibly, AMF aims to contribute to a greener, more sustainable metal fabrication industry.As AMF continues to grow, they remain dedicated to their founding principles of excellence, integrity, and customer-centricity. With a stellar track record and a steadfast commitment to innovation, AMF is well positioned to lead the metal fabrication industry into a new era. With every fabrication project they undertake, AMF aims to redefine what is possible in this ever-evolving sector.In conclusion, All Metal Fabrications has emerged as a trailblazer in the metal fabrication industry, setting new standards of excellence through their commitment to innovation, precision, and customer satisfaction. With their cutting-edge technology, tailored solutions, and green initiatives, AMF continues to be at the forefront of revolutionizing the way metal is fabricated and manufactured.