Top Metal Cutting Service Provider: Delivering Precision and Efficiency
By:Admin
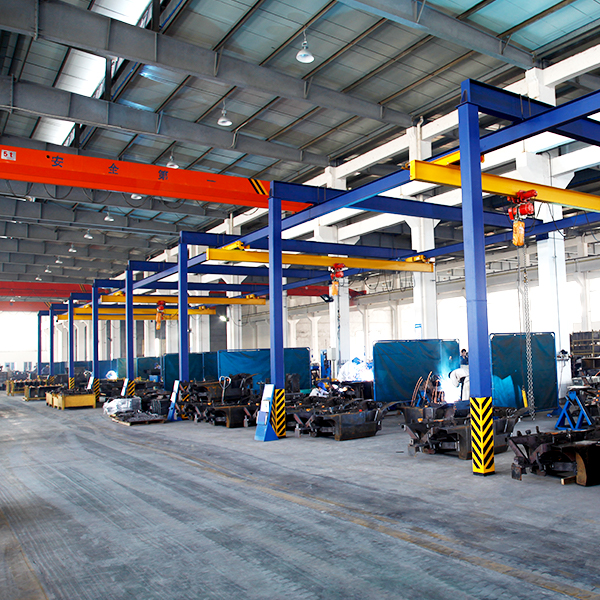
Leading Metal Cutting Service Provider Revolutionizes Industry with Advanced Technology and Unparalleled Precision
CITY, DATE – Metal Cutting Service (MCS), a prominent player in the metal cutting industry, has recently introduced a groundbreaking technology that is set to revolutionize the way metal components are cut and fabricated. With an extensive track record of delivering high-quality products and services, MCS continues to push boundaries, emphasizing precision, efficiency, and innovation.
Founded over two decades ago, MCS has steadily gained recognition in the industry as a reliable partner for all metal cutting requirements. The company has consistently stayed ahead of the competition by investing in state-of-the-art machinery and adopting cutting-edge techniques. Renowned for its commitment to perfection and unparalleled precision, MCS has been the go-to choice for clients across various sectors, ranging from aerospace and automotive to construction and healthcare.
At the heart of MCS's success lies their team of highly skilled technicians and engineers who possess profound expertise and experience in metal cutting and fabrication. Adhering to strict quality standards, the team meticulously examines each project, ensuring that all specifications are met to perfection. By focusing on the finest details, MCS consistently delivers exceptional results, earning them a trusted reputation within the industry.
What sets MCS apart from its competitors is its unwavering commitment to innovation. The company continually invests in cutting-edge technology to ensure optimal precision and efficiency. With the introduction of their latest revolutionary technology, MCS has taken metal cutting to an entirely new level. This cutting-edge advancement allows for intricate designs and complex geometries to be precisely fabricated with unparalleled accuracy, reducing lead times and significantly increasing production output.
MCS's new technology is equipped with advanced software that enables seamless integration between design and production, fostering a streamlined workflow. The software provides real-time feedback, allowing for quick adjustments and modifications, ultimately leading to improved overall project efficiency. Moreover, this technology enhances operator safety by minimizing human intervention during the cutting process.
One of the key advantages of MCS's advanced technology is its ability to handle a wide range of materials, including steel, aluminum, titanium, and more. The versatility of this technology positions MCS as a top-tier metal cutting service provider capable of catering to diverse industries and customizing solutions to meet the unique demands of each client.
With the introduction of this advanced technology, MCS aims to address the growing demands of the market, particularly in an era driven by rapid industrialization and innovation. By extending its capabilities and setting new industry standards, MCS remains steadfast in its commitment to delivering exceptional service to its clients.
As an environmentally conscious company, MCS places great emphasis on sustainability and eco-friendly practices. The utilization of advanced technology enables the optimization of material usage, reducing waste and minimizing the carbon footprint. By adopting sustainable measures, MCS ensures its role as a responsible industry leader.
As the metal cutting industry continues to evolve, MCS remains dedicated to staying at the forefront of innovation and excellence. With their unparalleled precision, commitment to quality, and advanced technology, MCS is poised to reshape the industry, empowering businesses to achieve unprecedented levels of success.
For more information about MCS, their state-of-the-art technology, and the services they offer, please visit [Company Website].
###
About Metal Cutting Service:
Metal Cutting Service (MCS) is a leading provider of metal cutting and fabrication solutions. With over two decades of experience, MCS is renowned for its precision, reliability, and commitment to excellence. The company's dedication to investing in advanced technology has allowed them to consistently deliver exceptional results, positioning them as an industry leader. MCS caters to a wide range of sectors, offering customized solutions to meet diverse client needs. For more information, visit [Company Website].
Company News & Blog
Laser Cutting and Fabrication: A Comprehensive Guide for Precision Metal Work
Laser Cutting And Fabrication - Delivering Top Quality Products to CustomersFor all your metal fabrication needs, Laser Cutting And Fabrication is the solution you need! With extensive experience in the industry, we offer custom laser cutting and fabrication services for a wide range of materials, including stainless steel, aluminum, brass, and copper. Our team of certified professionals is committed to producing high-quality products that meet or exceed customer expectations.At Laser Cutting And Fabrication, we pride ourselves on being a highly reliable and trusted service provider. We stand by our commitment to quality and ensure that each job we undertake meets the highest industry standards. Our equipment uses the latest technology available to produce superior results, ensuring that even the most complex designs are finished with precision and accuracy.Our team of experts has years of experience in laser cutting and fabrication, enabling us to accurately assess your needs, requirements, and design ideas. We can design and create a wide variety of products such as metal signs, brackets, and enclosures. We can also create custom-made prototype parts for your business. Our laser cutting services are catered to the unique needs of our customers, so you can be assured that every product we create is tailored to your specific requirements.Our state-of-the-art equipment helps us to remain at the top of our game. We use the best tools to make our services stand out. Laser Cutting And Fabrication has the latest, up-to-date technology, allowing us to be highly adaptable and flexible when it comes to fulfilling customers' needs. Our computer software allows for seamless integration between 3D designs and production, reducing production time while also increasing precision.Our laser cutting and fabrication techniques use a non-contact cutting method, which ensures that each product is free from deformation and does not require extra processing. With the use of laser, we are able to accommodate the production of even the thinnest of metals, with a very precise cut. Our CNC machining center also provides us with high-quality milling and turning processes, allowing for streamlining of all production phases.At Laser Cutting And Fabrication, we understand the importance of delivering products that meet or even exceed our customer's expectations. Our team is committed to ensuring that the end result is of top quality and that each project is delivered on time. We maintain open communication throughout the production process, to ensure that the product we deliver meets the customer's expectations, even when changes are made to the design.Our aim is to create long-term partnerships with our clients, providing them with reliable and trustworthy laser cutting and fabrication services. We pride ourselves on being a one-stop-shop for all your needs, delivering comprehensive services from start to finish. We value our customers, and in turn, are dedicated to providing them with the highest quality of service.Laser Cutting And Fabrication is a company that believes in adding value at all times through continuous improvement, leading to simplified and affordable prices for customers. We understand that each customer has unique needs and requirements, which is why we offer a completely customized solution. From the moment we receive your inquiry, our team of professionals ensures that we create an exceptional experience for our customers.Our commitment to quality and excellence is what sets us apart. We understand that a company's reputation is dependent on the products it produces. As such, we aim to exceed customer expectations by providing them with exceptional service at every stage of the process. We maintain our relationship with our customers by providing a trusted source for laser cutting and fabrication services.In conclusion, Laser Cutting And Fabrication is more than a business; it is a partner in production. Our team is dedicated to quality, reliability, and customer satisfaction. We are more than willing to work with you to achieve the desired outcome, whether it be custom parts for your small business or large-scale fabrication. Choose us for all your laser cutting and fabrication needs, and experience the best of what this industry has to offer!
Enhancing Industrial Efficiency with Advanced Robot Welding Services
Robot Welding Service Revolutionizes Manufacturing ProcessIn recent years, the manufacturing industry has witnessed a rapid transformation through the adoption of automation technologies. One particular area that has greatly benefited from automation is the welding process, traditionally a time-consuming and labor-intensive task. With the introduction of Robot Welding Service, companies can now take advantage of advanced robotic systems to enhance their manufacturing capabilities.Robot Welding Service, an industry-leading provider of innovative welding solutions, has pioneered a breakthrough approach to welding, utilizing state-of-the-art robotic technology. By leveraging the precision and efficiency of robots, they have created a service that is revolutionizing the manufacturing landscape.The company's goal is to address the challenges faced by manufacturers in achieving consistent weld quality, increasing productivity, and reducing costs. With their advanced robotic systems, they offer a comprehensive welding service that covers a wide range of applications, from small-scale projects to large-scale production lines.One of the key advantages of Robot Welding Service is their ability to handle complex welding tasks with ease. Traditional welding techniques often require highly skilled welders to perform intricate maneuvers, leading to higher labor costs and potential errors. However, by using robots equipped with advanced sensors and programming, the service ensures precise and flawless welds every time.Furthermore, Robot Welding Service significantly reduces the time required for welding operations. By employing robotics that work at exceptional speeds, the service can complete tasks much faster than human operators. This increased efficiency translates into higher productivity and shorter project lead times, enabling manufacturers to meet tight deadlines and enhance customer satisfaction.Moreover, Robot Welding Service's robotic systems offer substantial cost savings for manufacturers. With automation, companies can eliminate the need for multiple welders and associated expenses like training, safety equipment, and maintenance. The service also minimizes material waste and rework, resulting in significant cost reductions over time.To ensure seamless integration of their welding services, Robot Welding Service collaborates closely with their clients. Before commencing any project, their expert team conducts a thorough analysis of the manufacturer's needs, ensuring that the implemented solution is tailored to their specific requirements. This personalized approach guarantees optimal results and maximizes the overall efficiency of the manufacturing process.Additionally, Robot Welding Service provides comprehensive training and support to their clients, enabling them to navigate the new technology with ease. Their team of skilled technicians offers guidance at every stage, from initial setup to ongoing maintenance. This ensures that manufacturers can fully leverage the benefits of robotic welding and overcome any challenges that may arise.The impact of Robot Welding Service's innovations is already evident across various industries. Manufacturers who have embraced this advanced welding technology have reported significant improvements in product quality, reduced production costs, and increased overall profitability. Moreover, the service has created job opportunities in the field of robotics, as technicians are required to oversee and operate the robotic systems.Looking ahead, Robot Welding Service aims to further expand its offerings by continually refining its robotic systems and exploring new applications of automation. With their commitment to innovation and customer satisfaction, they are poised to shape the future of manufacturing and set new standards in the industry.In conclusion, Robot Welding Service has introduced a game-changing approach to welding through their advanced robotic systems. By combining precision, efficiency, and cost-effectiveness, they have revolutionized the manufacturing process for numerous companies. With their personalized approach and comprehensive support, the service is paving the way for a new era of automation in the welding industry.
Techniques for Welding Thin Sheets of Stainless Steel
Welding Thin Stainless Steel: Tips and Tricks for Perfect WeldsStainless steel is a popular choice of material for many applications due to its corrosion resistance, durability, and aesthetic appeal. However, welding thin sheets of stainless steel can be a challenging task, requiring careful preparation, skill, and the right equipment. In this blog post, we will provide some tips and tricks for welding thin stainless steel, including the use of advanced welding techniques and tools to achieve the perfect weld.PreparationBefore you begin welding thin stainless steel sheets, it is essential to prepare the workpiece properly. First, ensure that the surfaces to be welded are clean and free of any contaminants that may affect the quality of the weld. Use a degreaser or solvent to remove any oil, dirt, grease or oxide layers that may be present on the surface. You can also use a wire brush or grinder to remove the oxide layer and create a clean surface for welding.Next, ensure that the edges of the workpieces are aligned properly, with an even gap of around 1-2mm between them. A precise fit is essential for achieving a good weld, so take the time to check and recheck the alignment before beginning the welding process.TechniquesSeveral advanced welding techniques can be used to weld thin sheets of stainless steel, including TIG (Tungsten Inert Gas) welding and laser welding. TIG welding is a popular choice for welding thin stainless steel sheets because it offers precise control over the welding process, a high-quality finish, and the ability to weld various types of stainless steel.With TIG welding, the torch is held by the welder, and the other line feeds behind the weld using parts of pie plates and other forms of bendy stuff to dam the argon behind the weld. This technique ensures that the weld is protected by an argon gas shield, preventing the weld from being contaminated by oxygen and other atmospheric gases.Another option for welding thin stainless steel is laser welding. Laser welding uses a high-energy laser beam to join the workpieces, resulting in a precise, high-quality weld. Laser welding is particularly useful for welding complex shapes and contours, and it is ideal for welding thin sheets of stainless steel, where precision is essential.ToolsTo achieve the perfect weld on thin stainless steel, it is essential to have the right tools. Some of the key tools you will need for welding thin sheets of stainless steel include a TIG welding machine, a suitable electrode, filler wire, and an argon gas cylinder.A high-quality TIG welding machine is essential for achieving precise control over the welding process, enabling you to adjust the weld speed, current, and voltage for optimal results. The right electrode and filler wire are also critical, as they dictate the quality and strength of the weld.ConclusionWelding thin sheets of stainless steel requires careful preparation, skill, and the right equipment. By following the tips and tricks outlined in this blog post, including proper preparation, advanced welding techniques, and the use of quality tools, you can achieve perfect welds every time. Whether you choose TIG welding or laser welding, remember to take your time, stay focused, and enjoy the impressive results that you can achieve with thin steel.
Revolutionary Laser Cutting Technology Introduces Groundbreaking Solutions for Engineering Industry
Laser Cutting: The Optimal Solution for Aluminium Cutting Aluminium is a widely used material, utilized in various industries such as automotive, aerospace, construction, and electronics. Its unique properties such as lightweight, durable, corrosion-resistant, and versatile make it a sought-after material. However, cutting through Aluminium can prove to be a challenging task due to its high thermal conductivity and low melting point. To overcome this challenge, Aluminium Laser Cutting Service is the optimal solution.Laser cutting is a precision technique that uses a high-powered laser beam to cut through different materials, including Aluminium. The laser beam melts, burns, or vaporizes the Aluminium material, producing a clean and precise cut. This method provides various advantages compared to traditional cutting methods such as sawing or milling. Some of the benefits include:1. Precision: Laser cutting provides a precise and accurate cut that is difficult to achieve through other methods. This is because the laser beam follows a pre-programmed path, ensuring that the cut is exact and consistent throughout the material.2. Efficiency: Laser cutting is a quick and efficient method, with the ability to cut multiple shapes and sizes within seconds. This is ideal for large-scale production and can save a significant amount of time, cost, and labor.3. Clean Cut: The laser beam produces minimal heat and leaves no residue or burrs after cutting. This results in a clean and smooth cut that requires minimal post-processing compared to other cutting methods.4. Versatility: Laser cutting is a versatile method that can cut through a wide range of materials, including Aluminium, stainless steel, copper, and acrylics. This means that businesses can cut different materials using the same machine, eliminating the need for multiple setups and equipment.Aluminium Laser Cutting provides an array of applications in various industries. In the automotive industry, Aluminium laser cutting is used to produce lightweight car parts, which reduces fuel consumption and emissions. In the aerospace industry, Aluminium Laser Cutting is used to create intricate parts for aircraft such as wings, engine parts, and landing gear. In construction, Aluminium Laser Cutting is used to produce parts for doors, windows, and frames.In conclusion, Laser Cutting is the optimal solution for cutting Aluminium materials due to its precision, efficiency, and versatility. It provides a clean and consistent cut that is difficult to achieve through traditional cutting methods. As a result, Aluminium Laser Cutting can save time, cost, and labor while maintaining high-quality standards. Contact your local Aluminium Laser Cutting service provider today for all your Aluminium cutting needs.
MIG Welding Tips for Working with Thin Steel
Mig Welding Thin Steel – A Game-Changer in the Welding IndustryWelding is a crucial process in the manufacturing and construction industry. It involves the process of fusing two pieces of metal to create a strong bond. Mig welding is one of the most popular welding techniques used today. It stands for Metal Inert Gas welding and is sometimes referred to as Gas Metal Arc welding (GMAW).Mig welding uses a consumable electrode wire consisting of a metal wire placed on a spool that continuously feeds through a welding gun. The process involves the wire coming into contact with the base metal, generating an electrical arc that melts the wire and the base metal together to form a strong bond. The process is efficient, and it can be used to weld various metals, including carbon steel, stainless steel, aluminum, nickel alloys, and copper.However, Mig welding thin steel has always been a challenge, mainly due to the risk of burn-through, weld distortion, and poor weld quality. These challenges have been at the forefront of the welding industry, and many companies have been searching for a solution to solve these issues. Fortunately, one company has developed a solution that has been a game-changer in the welding industry.The company, which prefers to remain anonymous, has developed a new technique that enhances Mig welding thin steel, delivering exceptional results with minimal risks of distortion and burn-through. The company’s innovation is designed for use in the automotive, aerospace, and construction industries.Their solution is a new welding wire designed explicitly for thin steel. The wire comprises a unique combination of materials designed to deliver superior results when welding thin steel. Its construction comprises a specific blend of wire, shield gas, and other advanced technologies that enhance the welding process.The new welding wire boasts several benefits, including a lower melting point and higher heat conductivity, making it easier to weld thin steel without burning through. Additionally, it enhances the arc stability hence reducing the risk of weld defects.For the automotive industry, the new welding wire has been a game-changer. Automakers face the challenge of building lighter, fuel-efficient cars, and the new welding wire has been instrumental in achieving that. Thin sheet metal is used to construct body panels, hoods, and trunks. The new welding wire has helped automakers overcome the challenges of welding these thin sheets, resulting in lighter vehicles, increased fuel efficiency, and reduced manufacturing costs.In the aerospace industry, the new welding wire has also come in handy. Aircraft manufacturers use thin steel in the construction of wings, tail sections, and fuselage. These thin sheets require careful handling during the welding process to avoid distortions and burn-through. The new welding wire has enhanced the welding process, enabling manufacturers to construct high-quality aircraft with minimal defects, reduced manufacturing costs, and faster production times.For the construction industry, the new welding wire has decreased the risks of welding thin structural pipes. The welding of pipes is essential for the construction of various structures, including buildings, bridges, and tunnels. With the new welding wire, manufacturers can weld thin steel pipes without the risk of burn-through and distortions, creating a safer and more efficient construction environment.In summary, the development of the new welding wire designed for Mig welding thin steel has been a game-changer in the welding industry. Its unique combination of materials has enhanced the welding process, reducing the risks of burn-through, weld defects, and distortions. The new welding wire has been instrumental in facilitating the production of lighter, fuel-efficient vehicles in the automotive industry, the production of high-quality aircraft in the aerospace industry, and safer and more efficient welding for the construction industry.The company that developed the new welding wire has continued to innovate, seeking new ways to improve the welding process further. Their achievement serves as a testament to the power of innovation and the endless possibilities it presents. The welding industry will continue to benefit from advancements in technology, and we can expect even more innovations in the future.
Welding Techniques for Joining Stainless Steel and Mild Steel - Available for Sale in China
Welding stainless steel and mild steel together is a challenging task. It requires expertise, precision and high-quality equipment. The process involves joining two materials with different chemical and mechanical properties, which can lead to cracking, distortion and other issues if not done correctly. In this blog, we will explore the process of welding mild steel to stainless steel and some of the challenges that come with it.First, let's look at the materials themselves. Stainless steel has a high chromium content, which makes it resistant to corrosion and stains. It is also harder and more brittle than mild steel, which is why it is challenging to weld the two materials together. Mild steel, on the other hand, has a lower carbon content, making it more ductile and easier to work with when compared to stainless steel.When welding stainless steel to mild steel, there are several methods to consider. Let's take a closer look at some of the most popular welding techniques.1. TIG (Tungsten Inert Gas) Welding: This is one of the most popular welding techniques used in welding stainless steel to mild steel. It provides a precise, clean and high-quality weld, making it ideal for applications that require a high degree of accuracy.2. MIG (Metal Inert Gas) Welding: This is a more straightforward technique compared to TIG welding. It is faster, easier to learn and produces a durable weld. However, the quality of the weld is lower than TIG welding, which may not be suitable for high-end applications.3. Stick Welding: This is a versatile welding method that can be used to weld different materials. It produces a rugged and robust weld that can withstand high temperatures, making it ideal for industrial applications.Regardless of the welding technique used, welding stainless steel to mild steel requires proper preparation. The surface must be clean, free of rust, oil and other contaminants that can affect the quality of the weld. Additionally, the two metals must be preheated to ensure that the thermal stresses are minimized during the welding process.One of the biggest challenges when welding stainless steel to mild steel is the difference in melting points. Stainless steel has a much higher melting point than mild steel, which means that it can easily warp or crack if the welder is not careful. Hence, it is crucial to use specialized welding techniques and equipment to ensure that the two materials are welded together properly without cracking or distortion.In conclusion, welding stainless steel to mild steel can be a daunting task, but it is possible with the right skills, tools, and techniques. With proper preparation and welding processes, it is possible to achieve a strong and durable weld between the two materials. If you need more information on welding stainless steel to mild steel or other welding-related topics, please feel free to reach out to our team of experts.
Efficient Ways to Plasma Cut Painted Metal
Plasma Cutting Unveils New Technology for Painted Metal ProcessingIn the world of metal fabrication, Plasma Cutting Inc. has emerged as a pioneer in developing advanced cutting solutions. The company's latest breakthrough has revolutionized the way painted metal is processed, offering a game-changing technology that allows for efficient and precise cutting without compromising the integrity of the paint finish. With its commitment to innovation, Plasma Cutting Inc. continues to push the boundaries of what is possible in the industry.Traditional methods of cutting painted metal have often posed challenges, leading to subpar results and costly rework. The need to remove the paint before cutting not only takes time but also leads to additional expenses and potential damage to the material. Recognizing this problem, Plasma Cutting Inc. embarked on a mission to find a solution that would eliminate the need for paint removal while delivering exceptional cutting quality.After years of research and development, Plasma Cutting Inc. has successfully developed a unique technology that allows for clean and precise cuts on painted metal surfaces. By employing a highly concentrated plasma arc, the new system cuts through the metal while leaving the paint unharmed, resulting in a smooth and flawless finish. This breakthrough technology has the potential to revolutionize various industries, including automotive, construction, and manufacturing.One of the key advantages of Plasma Cutting Inc.'s new technology is its ability to significantly reduce production time. As the paint no longer needs to be removed before cutting, the entire process becomes faster and more efficient. This increased productivity allows manufacturers to deliver products faster to their customers, ultimately boosting their bottom line. Additionally, the elimination of paint removal reduces material waste, further contributing to a more sustainable manufacturing process.Furthermore, the integrity of the paint finish is preserved, ensuring that the final product meets the highest quality standards. Compared to traditional methods that often result in chipped or uneven paint, Plasma Cutting Inc.'s technology guarantees a flawless paint finish on the cut edges. This eliminates the need for time-consuming touch-ups and refinishing, saving both time and money for manufacturers.Plasma Cutting Inc.'s breakthrough technology also opens up new design possibilities for painted metal products. With the ability to make intricate and precise cuts, manufacturers can now create more complex and aesthetically pleasing designs. This flexibility gives designers and architects the freedom to explore innovative concepts and push the boundaries of creativity.The success of Plasma Cutting Inc.'s new technology can be attributed to the company's unwavering commitment to research and development. With a team of highly skilled engineers and technicians, the company consistently strives to push the limits of what is possible in the field of metal fabrication. Their dedication to innovation has earned them a reputation as a leading provider of cutting-edge cutting solutions.As industries continue to evolve and demand higher quality products, Plasma Cutting Inc. stands at the forefront of delivering cutting-edge technology. With their revolutionary method of cutting painted metal, the company has transformed the way manufacturers approach metal fabrication. This breakthrough offers unparalleled efficiency, precision, and quality that will undoubtedly reshape various industries.In conclusion, Plasma Cutting Inc.'s new technology for cutting painted metal sets a new standard in the field of metal fabrication. By eliminating the need for paint removal, the company has revolutionized the production process, offering increased efficiency, superior quality, and design flexibility. Powered by their commitment to innovation, Plasma Cutting Inc. continues to lead the way in advancing the capabilities of the industry and remains a trusted partner for manufacturers seeking cutting-edge solutions.
Top Fabrication Shops: Ideal Destinations for Your Manufacturing Needs
Steel fabrication shops are an essential part of today's construction and manufacturing industries. These shops are responsible for fabricating structural steel elements that are used in buildings, bridges, ships, and other constructions. Fabrication shops are equipped with state-of-the-art machines and tools that allow experienced workers to cut, shape, and weld steel pieces into the desired shapes and sizes.Steel fabrication shops are the backbone of many critical construction and manufacturing projects. Without them, it would be impossible to build the modern buildings and structures that we take for granted today. These shops employ highly skilled professionals who are passionate about their craft and work tirelessly to ensure that their products meet the highest quality standards.Steel fabrication shops are typically equipped with advanced machinery, such as computer numerically controlled (CNC) machines, auto-feed saws, and welding equipment. These machines allow workers to efficiently cut, drill, shape, and weld steel pieces into the desired shapes and sizes. The workers at steel fabrication shops are highly skilled and experienced, and they have the expertise needed to handle large-scale manufacturing projects.Steel fabrication shops are also responsible for ensuring that their products meet relevant safety standards. This is particularly important in the construction industry, where building codes and safety regulations are heavily enforced. Therefore, it is essential for steel fabrication shops to work with engineers and architects to ensure that their products are structurally sound and adhere to all safety guidelines.In addition, steel fabrication shops can also provide custom fabrications to meet specific project requirements. They have the flexibility to create one-off parts and components that meet unique specifications. This is particularly useful in the manufacturing industry, where customized products are becoming increasingly popular.Overall, steel fabrication shops are an integral part of the modern construction and manufacturing industries. They provide the essential products and services that make these industries possible. With the help of advanced machinery, experienced workers, and strict quality control measures, steel fabrication shops can ensure that their products meet the highest quality standards and contribute to the success of countless construction and manufacturing projects around the world.
Metal Fabrication: A Guide to Building Metal Structures through Cutting, Bending, and Assembly Processes
Metal Fabrication Company Revolutionizes the Industry with Innovative SolutionsMetal fabrication is the process of utilizing a range of techniques to build structures, products, and components from metal materials. The industry has come a long way since the early days of hammering metal sheets together. Today, metal fabrication is an incredibly sophisticated process that involves cutting, shaping, and assembling metal into a variety of different products.Leading the way in the metal fabrication industry is (Brand Name Removed), a company committed to providing innovative solutions to clients’ metal fabrication needs. With their state-of-the-art techniques and technology, they have revolutionized how metal is fabricated and produced across the industry.Their metal fabrication process begins with cutting - using tools such as plasma cutters and water jets to carefully and accurately cut the metal into the required shapes. From there, the metal is shaped through processes such as bending and rolling, to create the necessary structures and components. Welding is then utilized to assemble these structures, completing the fabrication process.What sets (Brand Name Removed) apart from other metal fabrication companies is their dedication to investing in the latest technology and innovations. They have the capabilities to fabricate a wide range of metals, including steel, aluminium, and titanium - each with its unique properties and challenges. Their advanced techniques and skilled workforce mean that they can create highly complex, custom-made components, all while maintaining the highest levels of precision and accuracy.One particular aspect that has enabled (Brand Name Removed) to make significant strides forward is their incorporation of computer-aided design and finite element analysis. They utilize CAD/CAM software to create virtual models of the metal components before fabrication begins, allowing for a quicker and more efficient process. This also ensures that the final product meets the client's expected specifications.Another area of innovation for (Brand Name Removed) is their approach to sustainability. They strive to use environmentally friendly materials and techniques whenever possible to reduce the impact on the environment. This includes utilizing recycled materials in their fabrication processes and improving their waste management procedures.With over [insert number of years] years of experience in the metal fabrication industry, (Brand Name Removed) has built a reputation for excellence and quality. They work closely with clients across a range of industries, including aerospace, automotive, and construction, to provide bespoke metal solutions for their specific needs.Furthermore, (Brand Name Removed) offers a wide range of services to complement their metal fabrication capabilities. They offer CAD design, prototyping, repair, and maintenance services, ensuring clients have everything they need under one roof.Moreover, they have an exceptional quality control program, ensuring the compliance of the fabrication process with the highest industry standards. This is achieved through detailed process mapping, checks, and cross-checks at each step of the process.The metal fabrication industry is constantly evolving, and (Brand Name Removed) is taking the lead. Their pioneering approach, investment in the latest technology, and commitment to quality and sustainability mean that they are well-positioned to continue driving the industry forward.With an unwavering focus on innovation, quality, and sustainability, (Brand Name Removed) is set to remain at the forefront of the metal fabrication industry - delivering exceptional results for clients across the world.
Discover Top-quality Bending Products and Services on Ferret.com.au
Are you searching for efficient and reliable CNC bending services for your business needs? Look no further than www.ferret.com.au to cater to all your bending requirements.At www.ferret.com.au, we offer a wide range of bending products and services from leading suppliers in the industry. Our suppliers are reputable and well-established, ensuring that you get the best quality products and services at an affordable price.CNC bending services are a vital component in the manufacturing industry. CNC (Computer Numerical Control) bending service is a highly automated process that reduces human error and increases efficiency. This advanced technology makes it possible to achieve high accuracy and precision in bending metal sheets.Our suppliers use modern CNC bending machines that are versatile and capable of bending different types of metal sheets in a range of sizes and thicknesses. These machines can also bend metal pipes and tubes, making them ideal for different manufacturing applications.CNC bending services offered at www.ferret.com.au include press brake bending, tube bending, and roll bending. Press brake bending is suitable for producing parts in large quantities and is used for both simple and complex bending operations. Tube bending is ideal for creating complex shapes and designs, while roll bending is ideal for producing curved and circular metal parts.We understand the importance of delivering high-quality products and services to our customers. Therefore, our suppliers use only the best materials and processes to ensure that the end product meets or exceeds your expectations.Our suppliers also offer customized CNC bending services to cater to specific needs and requirements. They work closely with customers to ensure that the end product meets their precise specifications. This personalized approach ensures that every customer gets the best possible bending solution for their business.In conclusion, if you require CNC bending services for your manufacturing needs, look no further than www.ferret.com.au. We offer a wide range of bending products and services from reputable and reliable suppliers in the industry. Our suppliers use modern CNC bending machines to provide high-quality products and services that meet or exceed your expectations. Contact us today to get started on your CNC bending project!