Benefits of Using Laser Technology for Stainless Steel Applications
By:Admin
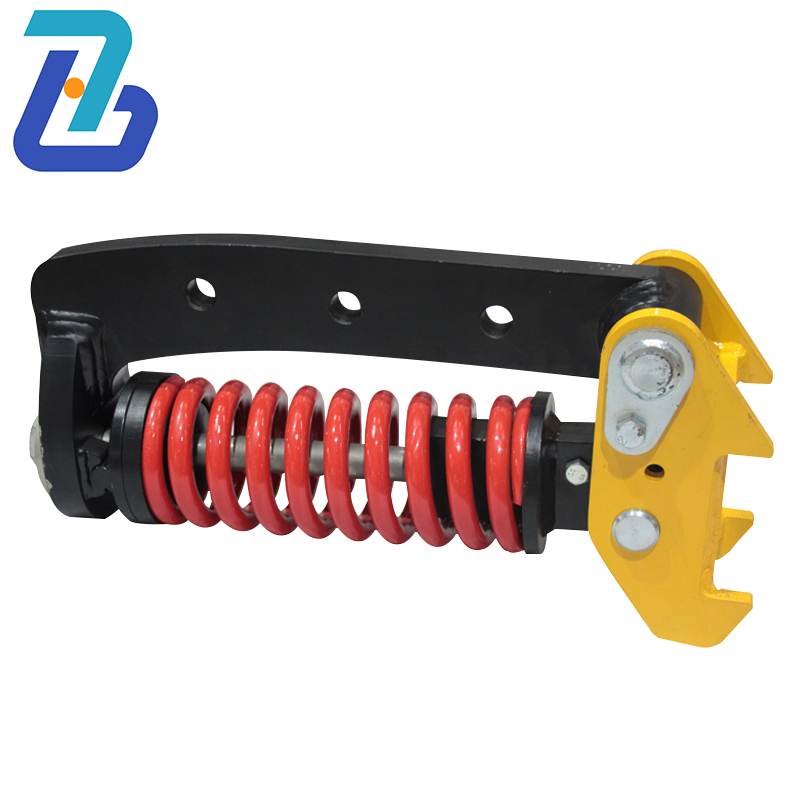
The company's state-of-the-art manufacturing facilities and cutting-edge technology have set it apart from its competitors. Laser Stainless Steel's dedication to quality and precision has made it a preferred supplier for many businesses around the world.
One of the key factors contributing to Laser Stainless Steel's success is its commitment to innovation. The company is constantly investing in research and development to improve its products and processes. This dedication to innovation has allowed Laser Stainless Steel to stay ahead of the curve and adapt to the ever-changing needs of the industry.
Laser Stainless Steel offers a comprehensive range of stainless steel products, including sheets, coils, plates, pipes, tubes, and fittings. The company's products are known for their durability, corrosion resistance, and aesthetic appeal, making them ideal for a wide range of applications.
In addition to its standard product offerings, Laser Stainless Steel also provides custom solutions for clients with specific requirements. The company's team of experienced engineers and designers work closely with clients to develop tailor-made products that meet their exact specifications. This personalized approach has earned Laser Stainless Steel a reputation for delivering bespoke solutions that exceed customer expectations.
Laser Stainless Steel's dedication to quality is reflected in its adherence to international standards and certifications. The company holds ISO 9001 certification, ensuring that its products meet the highest quality standards. This commitment to quality assurance has earned Laser Stainless Steel the trust and confidence of its customers, who rely on the company's products for their critical applications.
In addition to its focus on quality and innovation, Laser Stainless Steel prioritizes sustainability in its operations. The company is committed to environmentally friendly manufacturing practices, minimizing its impact on the planet. Laser Stainless Steel's sustainable approach has resonated with environmentally conscious clients who seek eco-friendly solutions for their projects.
Laser Stainless Steel's strong commitment to customer satisfaction sets it apart from its competitors. The company places a high priority on building long-term relationships with its clients, working closely with them to understand their needs and deliver solutions that add value to their businesses. This customer-centric approach has resulted in a loyal customer base that continues to rely on Laser Stainless Steel for their stainless steel requirements.
As a global leader in stainless steel manufacturing, Laser Stainless Steel serves a diverse range of industries, including construction, automotive, aerospace, healthcare, and more. The company's products are trusted by clients around the world for their quality, reliability, and performance.
Looking ahead, Laser Stainless Steel is focused on expanding its product portfolio and strengthening its position as a market leader in stainless steel manufacturing. The company continues to invest in research and development, exploring new technologies and materials to develop innovative solutions for its clients.
In conclusion, Laser Stainless Steel's dedication to quality, innovation, sustainability, and customer satisfaction has solidified its position as a leading manufacturer of stainless steel products. With a strong track record of delivering high-quality solutions for diverse industries, Laser Stainless Steel is poised for continued success and growth in the global market.
Company News & Blog
Custom Stainless Steel Sheet Metal Fabrication Services for Non-Standard Brackets: Laser Cutting, Forming, Stamping, Bending, Punching, and Welding
Laser Cutting and Sheet Metal Forming of Stainless Steel Sheets: Custom Processing of Non-Standard Stainless Steel BracketsStainless steel is a popular material used in a wide range of industries, including construction, automotive, and kitchenware. It is known for its durability, resistance to corrosion, and high aesthetic appeal. However, working with stainless steel can be a challenge. Its strength and hardness make it difficult to cut, bend, and shape, requiring specialized machinery and skilled technicians.To meet the growing demand for custom stainless steel products, (company name) offers a range of sheet metal forming services, including laser cutting, stamping, bending, punching, and welding. As a leader in the industry, we have the experience and expertise to handle complex projects and meet the high standards of our clients.One of our specialties is custom processing of non-standard stainless steel brackets. Many industries require brackets with unique shapes and sizes to fit their specific applications. Our team of engineers and technicians work closely with clients to design and produce brackets that meet their exact specifications. We use advanced software and equipment to ensure accuracy and precision in every step of the process. Our laser cutting machines can cut stainless steel sheets up to 6mm thick with a maximum sheet size of 3000x1500mm.We also offer a range of sheet metal forming services to complement our laser cutting capabilities. Our stamping presses range from 5 to 200 tons, allowing us to produce parts with varying thicknesses and complexities. Our CNC bending machines can bend stainless steel sheets up to 4mm thick and 3000mm long. We use state-of-the-art punching machines and welding robots to ensure fast and efficient production.At (company name), we are committed to providing high-quality stainless steel products that meet the needs of our clients. We understand that every project is unique and have the expertise to handle any challenge. Whether you need a single custom bracket or a large-scale production run, we have the capabilities and resources to meet your requirements.About (company name):Founded in (year), (company name) is a leading provider of custom sheet metal fabrication services. We specialize in processing stainless steel, aluminum, and other metals for a wide range of industries, including construction, automotive, and electronics. We have a state-of-the-art factory with advanced equipment and a team of skilled technicians. Our mission is to provide high-quality products and exceptional customer service at competitive prices.
Efficient Stainless Steel Cutting Techniques: Plasma Cutting Guide
Plasma Cutting Stainless - A New Milestone in Precision Metal Fabrication{Company name} is proud to announce the addition of plasma cutting stainless to its list of outstanding metal fabrication services. This innovative process allows for cutting and shaping stainless steel with unmatched precision and efficiency, opening up new possibilities for high-quality metal products and components.With over 20 years of experience in the metal fabrication industry, {company name} has established itself as a leading provider of custom metal fabrication solutions. The addition of plasma cutting stainless is a testament to the company's commitment to staying at the forefront of technology and innovation in the industry.Plasma cutting stainless is a highly versatile and efficient method of cutting stainless steel, offering a number of advantages over traditional cutting methods. Using a high-temperature, ionized gas, plasma cutting can effortlessly slice through stainless steel with remarkable precision, producing clean, smooth cuts in a fraction of the time it would take using other methods.The introduction of plasma cutting stainless at {company name} represents a significant step forward for the company, as it expands its capabilities and enhances its ability to meet the diverse needs of its clients. The ability to efficiently cut and shape stainless steel with such precision opens up new opportunities for the company to produce a wide range of metal products and components, from intricate, detailed designs to large-scale industrial parts.One of the key benefits of plasma cutting stainless is its ability to produce high-quality cuts with minimal heat-affected zones, resulting in cleaner edges and reduced post-processing requirements. This not only saves time and resources but also ensures that the integrity of the stainless steel is maintained, preserving its corrosion resistance and mechanical properties.In addition to its efficiency and precision, plasma cutting stainless also offers the flexibility to cut a wide range of thicknesses, making it well-suited for a variety of applications across different industries. Whether it's creating custom metal parts for the automotive industry, producing intricate designs for architectural projects, or fabricating complex components for the aerospace sector, {company name} is well-equipped to deliver exceptional results with plasma cutting stainless.As part of its commitment to quality and customer satisfaction, {company name} has invested in state-of-the-art plasma cutting equipment and technology, ensuring that its clients receive the highest standard of workmanship and precision. The company's team of skilled technicians and engineers are trained and experienced in utilizing plasma cutting techniques to achieve the best results, working closely with clients to understand their specific requirements and deliver tailored solutions.The launch of plasma cutting stainless at {company name} has already garnered significant attention from existing and prospective clients, who recognize the potential for this innovative process to transform their metal fabrication projects. From small-scale custom orders to large-scale industrial contracts, the company is poised to meet the needs of a diverse range of clients, providing them with the unmatched quality and precision that plasma cutting stainless offers.As {company name} continues to expand its capabilities and invest in cutting-edge technologies, the addition of plasma cutting stainless represents a significant milestone in the company's journey towards excellence in metal fabrication. By harnessing the power of plasma cutting, the company is well-positioned to drive innovation and deliver exceptional results for its clients, setting new benchmarks for precision and quality in the industry.
Highly Efficient Precision Laser Cutter for Metals: Cut Steel, Aluminum, Copper, and Titanium With Ease Using Advanced Fiber Laser Technology - Mechanical Kingdom
Precision Laser Cutting: Unlocking New Possibilities with SS Laser CuttingWhen it comes to precision cutting, Ss stainless steel is one of the most challenging materials to work with. But with the rise of advanced laser cutting technology, what was once considered difficult has now become achievable with ease. One such technology is the Fy4050b Precision Laser Cutter from Feiyue Laser.The Fy4050b Precision Laser Cutter is a top-of-the-line CNC cutting machine that can handle a variety of materials, including stainless steel plates, aluminum, copper, titanium sheets, and jewelry metal. What sets this machine apart is its fixed optical path design, which provides a maintenance-free optical path and low operating cost while delivering high processing efficiency and cutting quality. Equipped with an international advanced fiber laser, the Fy4050b machine is capable of cutting through thick metal sheets with precision and accuracy, providing you with clean and smooth edges that require minimal post-processing. This makes it ideal for a range of applications, from industrial to jewelry making.The cutting head of the Fy4050b machine uses the LASERMECH optical fiber cutting head imported from the United States. It's also fitted with a capacitive sensor, which provides high sensing accuracy, sensitive response, and stable and reliable performance. This means you get a quality cut every time, regardless of the shape or size of the material.The CNC system of the Fy4050b machine is specially designed for laser cutting. It uses an imported non-contact height tracking system that's sensitive and accurate, and is not affected by the shape of the material. This helps to eliminate potential errors during the cutting process, ensuring that you get precise and clean cuts every time. Overall, the Fy4050b Precision Laser Cutter is a valuable investment for anyone looking to get into laser cutting. It's affordable, versatile, and reliable, making it a great choice for businesses and hobbyists alike. With its exceptional cutting quality and high processing efficiency, this machine is sure to unlock new possibilities in your metal cutting projects.In conclusion, choosing the right laser cutter is crucial, especially when it comes to working with tough materials like Ss stainless steel. With the Fy4050b Precision Laser Cutter from Feiyue Laser, you're assured of a quality machine that can handle all your metal cutting needs with ease, precision, and efficiency. This cutting-edge technology is transforming the metal-cutting industry, making it easier and more affordable to achieve precision cuts than ever before. So, invest in the Fy4050b Precision Laser Cutter today and take your metal cutting projects to a whole new level!
Fiber Laser Engraving Service: Enhancing Precision and Efficiency for Your Engraving Needs
Essential Equipment in TIG Welding: Advantages and Applications
Title: TIG Welding Equipment Revolutionizing Precision Welding: A Game Changer for Critical ApplicationsIntroduction:TIG (Tungsten Inert Gas) welding, an advanced welding technique that utilizes an inert gas shield instead of a slag to protect the weld pool, has emerged as a highly attractive alternative to gas and manual metal arc welding. This technology has played a pivotal role in the acceptance of high-quality welding in critical applications. Among the leading companies in the industry, (name of the company) has established itself as a prominent player in supplying essential TIG welding equipment. Their commitment to innovation and expertise in TIG welding steel have revolutionized the welding industry. This article will delve into the significance of TIG welding equipment and how it has transformed precision welding.The Advantages of TIG Welding Equipment:TIG welding equipment offers numerous advantages that have propelled its rise in popularity in critical applications. One of its key advantages lies in the inert gas shield used, which eliminates the need for a slag, resulting in cleaner and more precise welds. This technique allows for increased control over the welding process, ensuring minimal distortion and reduced spattering. With TIG welding, the welder can easily regulate the heat input, making it ideal for welding thin materials. Moreover, the absence of slag facilitates easier post-weld cleaning, minimizing time and effort required for finishing.Another significant advantage of TIG welding equipment is its ability to achieve high-quality welds. The process employs a non-consumable tungsten electrode, which retains its shape and does not melt during the welding process. This characteristic enhances the welder's precision, resulting in aesthetically appealing and durable welds. Moreover, the ability to work with a wide range of materials, including stainless steel, aluminum, and copper, further highlights the versatility and superiority of TIG welding equipment.Promoting Safety and Efficiency with TIG Welding Equipment:Apart from its technical benefits, TIG welding equipment also prioritizes safety and efficiency. The process utilizes an electric foot pedal, granting the welder precise control over the heat input and filler rod. This level of control reduces the risks of overheating, burn-throughs, and other imperfections. Additionally, the precise control enables welders to create intricate and detailed welds with ease, making TIG welding equipment highly popular in industries that demand exceptional precision, such as aerospace, automotive, and medical equipment manufacturing.The Role of (Company Name) in Advancing TIG Welding Steel:In this realm of TIG welding equipment, (Company Name) has established a commendable reputation for delivering high-quality products and exceptional service. With their commitment to continuous innovation and expertise in TIG welding steel, the company has played a pivotal role in promoting the acceptance and adoption of TIG welding in critical applications.(Company Name) offers a comprehensive range of TIG welding equipment, including state-of-the-art power sources, torches, and consumables. Their equipment is designed to provide welders with superior control, exceptional arc stability, and unmatched reliability. Leveraging advanced technologies, (Company Name) ensures that their TIG welding equipment optimizes weld quality, productivity, and safety.Conclusion:TIG welding equipment has transformed the welding industry, presenting an attractive alternative to traditional welding techniques. With its numerous advantages, including cleaner welds, increased control over heat, and the ability to work with various materials, TIG welding equipment has become indispensable in critical applications. Notably, (Company Name) has significantly contributed to the advancement of TIG welding, ensuring the highest quality welds for industries requiring precision and durability. Continuous innovation and expertise in TIG welding steel have firmly established (Company Name) as a leader in the field, empowering welders and revolutionizing the welding industry as a whole.
Expert Laser Cutting and Bending Services for Precise Results
Laser Cutting and Bending Services Foster Innovation and Growth in Manufacturing IndustryAs the manufacturing industry continues to advance and innovate, the need for efficient and precise laser cutting and bending services becomes increasingly significant. These technologies have revolutionized the manufacturing process by allowing for faster, more accurate parts production and customization. With the latest laser cutting and bending technologies, manufacturers are able to create complex designs and shapes that were previously impossible, ushering in a new era of creativity and efficiency in manufacturing.One company at the forefront of this technological revolution is [company name], a leading provider of laser cutting and bending services. With state-of-the-art equipment and experienced staff, the company has established itself as a reliable and efficient partner for manufacturers in a wide range of industries.Laser cutting is a non-contact process that uses a high-powered laser to cut through various materials, including metals, plastics, and composites. This method produces clean and precise cuts, with minimal waste and distortion. Laser cutting is ideal for creating intricate designs and shapes, making it a popular choice for industries such as aerospace, automotive, and electronics.One of the most significant advantages of laser cutting is its ability to create complex designs with high precision. This allows manufacturers to create parts with tight tolerances, resulting in a more efficient and reliable final product. In addition, laser cutting is much faster than traditional cutting methods, reducing production times and increasing output.Bending is another critical process in manufacturing, and it has also benefited greatly from technological advancements. The latest bending machines use computer-controlled systems to accurately bend and shape metal parts. This technology allows for precise and repeatable bends, with minimal setup time, reducing wastage and material costs.The combination of laser cutting and bending has revolutionized the manufacturing industry, making it possible to produce parts and components with greater accuracy and efficiency than ever before. Manufacturers are now able to create complex shapes and designs, all while keeping production times and costs low.[company name] offers a wide range of laser cutting and bending services to meet the unique needs of their customers. The company has invested heavily in the latest technology to ensure that they can offer the most accurate and efficient services possible. With their advanced equipment and experienced staff, they are able to handle projects of all sizes and complexities.In addition to their laser cutting and bending services, [company name] offers a range of value-added services, including design consultation, prototype development, and assembly. This allows their customers to enjoy a full range of services, from initial product development to final assembly and delivery.The company's commitment to quality and customer satisfaction has earned them a reputation as a reliable and innovative partner for manufacturers in all industries. They work closely with their clients to ensure that their needs are met and that the final product meets the highest standards of quality.In conclusion, laser cutting and bending services are essential for modern-day manufacturing, and companies like [company name] play a critical role in meeting the growing demand for these services. With their advanced technology and innovative solutions, they are helping manufacturers to innovate and grow, creating products that are more efficient, reliable, and affordable than ever before.
The Benefits of TIG Welding Cold Rolled Steel: A Comprehensive Guide
[Company Name] is a leading manufacturer of welding equipment and supplies, with a reputation for high-quality products and cutting-edge technology. The company has recently unveiled a new innovation in the world of welding: Tig welding cold rolled steel.Tig welding, also known as gas tungsten arc welding, is a versatile and precise welding process that uses a non-consumable tungsten electrode to produce the weld. This method is commonly used for thin materials, and is known for its high quality and clean welds. Cold rolled steel, on the other hand, is a type of steel that has been processed at room temperature, resulting in a smooth, shiny finish. This type of steel is often used in applications where a precise finish is required, such as in automotive body panels and appliances.The combination of Tig welding and cold rolled steel offers many advantages for welders and manufacturers. The precise control of the Tig welding process allows for the creation of strong, clean welds on the smooth surface of cold rolled steel. This results in a finished product that is not only aesthetically pleasing, but also has a high level of structural integrity. Additionally, the use of Tig welding with cold rolled steel reduces the risk of distortion and warping, which is common with other welding processes.[Company Name] has been at the forefront of the welding industry for over [X] years, and has a strong track record of innovation and excellence. The company's founder, [Founder Name], has always been committed to pushing the boundaries of what is possible in the world of welding, and the development of Tig welding cold rolled steel is a testament to that commitment.In addition to the new welding process, [Company Name] also offers a wide range of equipment and supplies for welders, including welding machines, protective gear, and consumables. The company prides itself on providing top-of-the-line products and exceptional customer service, and has built a loyal customer base as a result.The introduction of Tig welding cold rolled steel is just the latest example of [Company Name]'s dedication to providing cutting-edge solutions for welders and manufacturers. The company is constantly investing in research and development to stay ahead of the curve in the welding industry, and the new welding process is evidence of that commitment.Welders and manufacturers who are interested in learning more about Tig welding cold rolled steel, as well as [Company Name]'s other products and services, can visit the company's website or contact their customer service team for more information. With [Company Name]'s reputation for excellence and innovation, the new welding process is sure to be a game-changer for the industry.
Top Quality Precision Sheet Metal Services for Your Needs
Precision Sheet Metal, a leading provider of high-quality sheet metal fabrication services, has recently announced the expansion of their facilities to accommodate the growing demand for their products and services.The company, which has been in operation for over 20 years, specializes in providing precision sheet metal fabrication for a wide range of industries including aerospace, automotive, electronics, and medical devices. With state-of-the-art equipment and a team of highly skilled engineers and technicians, Precision Sheet Metal is able to produce complex and intricate sheet metal components with tight tolerances and high precision.The expansion of their facilities comes as a result of increased demand for their services, driven by their commitment to providing their customers with the highest quality products and exceptional customer service. The new facility will allow Precision Sheet Metal to increase their production capacity and improve their efficiency in order to better serve their clients."We are thrilled to announce the expansion of our facilities, which will allow us to better meet the needs of our customers and continue to provide them with the high-quality products and services they have come to expect from us," said the CEO of Precision Sheet Metal. "This expansion is a testament to our continued growth and success in the industry, and we are excited to see where it will take us in the future."The new facility will feature the latest in sheet metal fabrication technology, including advanced CNC machines, laser cutting equipment, and robotic welding systems. This will allow Precision Sheet Metal to further enhance their capabilities and continue to deliver superior quality products to their customers.In addition to the expansion of their facilities, Precision Sheet Metal is also investing in the training and development of their workforce to ensure that they maintain their high standards of quality and performance. By providing ongoing training and education to their employees, Precision Sheet Metal is ensuring that they remain at the forefront of the industry and are able to adapt to the ever-changing needs of their customers."We understand the importance of investing in our people and providing them with the tools and resources they need to succeed," said the CEO. "By continuously investing in the training and development of our workforce, we are able to maintain the highest level of quality and expertise in everything we do."With their expanded facilities and continued commitment to excellence, Precision Sheet Metal is poised to continue their success and further solidify their position as a leader in the sheet metal fabrication industry. Their dedication to providing the highest quality products and exceptional customer service has earned them a strong reputation in the industry, and they are poised to continue to grow and thrive in the years to come.The expansion of their facilities is a clear indication of Precision Sheet Metal's commitment to meeting the needs of their customers and to continue providing them with the best possible products and services. With their state-of-the-art equipment, highly skilled workforce, and dedication to excellence, it is clear that Precision Sheet Metal will remain a force to be reckoned with in the sheet metal fabrication industry for years to come.
Efficient Ways to Plasma Cut Painted Metal
Plasma Cutting Unveils New Technology for Painted Metal ProcessingIn the world of metal fabrication, Plasma Cutting Inc. has emerged as a pioneer in developing advanced cutting solutions. The company's latest breakthrough has revolutionized the way painted metal is processed, offering a game-changing technology that allows for efficient and precise cutting without compromising the integrity of the paint finish. With its commitment to innovation, Plasma Cutting Inc. continues to push the boundaries of what is possible in the industry.Traditional methods of cutting painted metal have often posed challenges, leading to subpar results and costly rework. The need to remove the paint before cutting not only takes time but also leads to additional expenses and potential damage to the material. Recognizing this problem, Plasma Cutting Inc. embarked on a mission to find a solution that would eliminate the need for paint removal while delivering exceptional cutting quality.After years of research and development, Plasma Cutting Inc. has successfully developed a unique technology that allows for clean and precise cuts on painted metal surfaces. By employing a highly concentrated plasma arc, the new system cuts through the metal while leaving the paint unharmed, resulting in a smooth and flawless finish. This breakthrough technology has the potential to revolutionize various industries, including automotive, construction, and manufacturing.One of the key advantages of Plasma Cutting Inc.'s new technology is its ability to significantly reduce production time. As the paint no longer needs to be removed before cutting, the entire process becomes faster and more efficient. This increased productivity allows manufacturers to deliver products faster to their customers, ultimately boosting their bottom line. Additionally, the elimination of paint removal reduces material waste, further contributing to a more sustainable manufacturing process.Furthermore, the integrity of the paint finish is preserved, ensuring that the final product meets the highest quality standards. Compared to traditional methods that often result in chipped or uneven paint, Plasma Cutting Inc.'s technology guarantees a flawless paint finish on the cut edges. This eliminates the need for time-consuming touch-ups and refinishing, saving both time and money for manufacturers.Plasma Cutting Inc.'s breakthrough technology also opens up new design possibilities for painted metal products. With the ability to make intricate and precise cuts, manufacturers can now create more complex and aesthetically pleasing designs. This flexibility gives designers and architects the freedom to explore innovative concepts and push the boundaries of creativity.The success of Plasma Cutting Inc.'s new technology can be attributed to the company's unwavering commitment to research and development. With a team of highly skilled engineers and technicians, the company consistently strives to push the limits of what is possible in the field of metal fabrication. Their dedication to innovation has earned them a reputation as a leading provider of cutting-edge cutting solutions.As industries continue to evolve and demand higher quality products, Plasma Cutting Inc. stands at the forefront of delivering cutting-edge technology. With their revolutionary method of cutting painted metal, the company has transformed the way manufacturers approach metal fabrication. This breakthrough offers unparalleled efficiency, precision, and quality that will undoubtedly reshape various industries.In conclusion, Plasma Cutting Inc.'s new technology for cutting painted metal sets a new standard in the field of metal fabrication. By eliminating the need for paint removal, the company has revolutionized the production process, offering increased efficiency, superior quality, and design flexibility. Powered by their commitment to innovation, Plasma Cutting Inc. continues to lead the way in advancing the capabilities of the industry and remains a trusted partner for manufacturers seeking cutting-edge solutions.
High-Quality CNC Machining and Sand Blasting Services for Aluminum Materials
Axis CNC Machining Sand Blasting AluminumThe process of CNC machining and sand blasting aluminum is a crucial part of the manufacturing industry. It requires precision, skill, and expertise to produce high-quality aluminum parts that are used in various industries such as aerospace, automotive, and electronics. {Company Name} is a leading provider of axis CNC machining and sand blasting services for aluminum materials. With their state-of-the-art facilities and highly skilled team, they are able to deliver top-quality products to meet the needs of their customers.Axis CNC machining is a computer-controlled process that uses multi-axis machines to remove material from aluminum blocks and create precision parts. This process is highly efficient and accurate, ensuring that the final products meet the exact specifications required by the customers. With the advanced technology used by {Company Name}, they are able to produce complex and intricate aluminum parts with tight tolerances, making them a preferred choice for many businesses in need of high-precision components.In addition to CNC machining, {Company Name} also provides sand blasting services for aluminum materials. Sand blasting is a surface treatment process that uses abrasive materials to clean, smooth, or shape a hard surface. In the case of aluminum, sand blasting can be used to remove any surface impurities, create a matte finish, or prepare the material for further coating or painting. The skilled technicians at {Company Name} have the expertise to carry out sand blasting with precision and attention to detail, ensuring that the aluminum parts are of the highest quality and finish.One of the key advantages of axis CNC machining and sand blasting aluminum at {Company Name} is their commitment to quality and continuous improvement. They have implemented strict quality control measures at every stage of the manufacturing process to ensure that the final products meet the highest standards. This includes thorough inspections, rigorous testing, and adherence to industry regulations and guidelines. As a result, customers can have full confidence in the reliability and durability of the aluminum parts produced by {Company Name}.Furthermore, {Company Name} takes pride in their dedication to customer satisfaction. They work closely with their clients to understand their specific requirements and provide tailored solutions to meet their needs. Whether it's a one-off prototype or a large-scale production run, {Company Name} has the capacity and capability to deliver on time and within budget. Their customer-centric approach has earned them a solid reputation in the industry, making them a trusted partner for businesses looking for high-quality axis CNC machining and sand blasting services for aluminum materials.The team at {Company Name} is comprised of highly skilled and experienced professionals who are passionate about their craft. They are committed to staying ahead of the curve in terms of technology, techniques, and industry trends to ensure that they continue to deliver excellence in every project they undertake. Their expertise, dedication, and attention to detail are what set them apart from their competitors, making them a go-to source for axis CNC machining and sand blasting aluminum.In conclusion, axis CNC machining and sand blasting are essential processes in the manufacturing of aluminum parts, and {Company Name} is a trusted provider of these services. With their advanced technology, skilled team, and commitment to quality, they are able to produce high-precision aluminum components for various industries. Their customer-centric approach and dedication to excellence make them a valuable partner for businesses in need of top-quality axis CNC machining and sand blasting services.