High-Quality CNC Component Parts in China: The Ultimate Guide
By:Admin
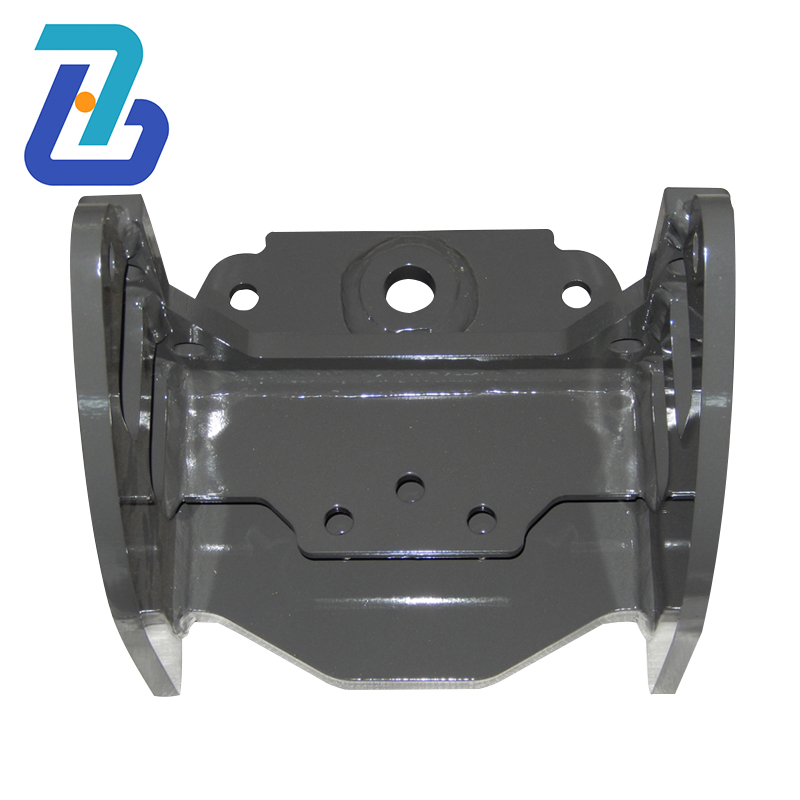
China CNC Component Parts, a leading manufacturer of precision CNC components, has experienced significant growth in recent years and expanded its global reach, solidifying its position as a key player in the industry. With a dedication to innovation, quality, and customer satisfaction, the company has continuously exceeded expectations and set new benchmarks for excellence.
Founded in [year], China CNC Component Parts has steadily grown its capabilities and product offerings to meet the evolving needs of a diverse customer base. The company's commitment to investing in advanced technology and talent has allowed it to deliver high-quality products with unmatched precision and efficiency. As a result, China CNC Component Parts has become a trusted partner for a wide range of industries, including automotive, aerospace, medical, and more.
One of the driving forces behind China CNC Component Parts' success is its relentless pursuit of excellence in every aspect of its operations. From the selection of raw materials to the final inspection of finished products, the company adheres to the highest standards to ensure the reliability and performance of its components. By utilizing state-of-the-art CNC machining equipment and stringent quality control measures, China CNC Component Parts has earned a reputation for producing parts that meet the most demanding specifications.
In addition to its unwavering focus on quality, China CNC Component Parts places great importance on customer satisfaction and collaboration. The company works closely with its clients to understand their unique requirements and provide tailored solutions that address their specific needs. By fostering meaningful partnerships and delivering exceptional service, China CNC Component Parts has established long-lasting relationships with its customers, earning their trust and loyalty.
As part of its commitment to continuous improvement and growth, China CNC Component Parts has expanded its global reach to better serve its international clientele. With a well-established network of distribution partners and representatives, the company has been able to extend its presence to new markets and enhance its accessibility to customers worldwide. This strategic expansion has allowed China CNC Component Parts to provide localized support and expedited delivery times, further strengthening its position as a global leader in the industry.
Looking ahead, China CNC Component Parts remains focused on driving innovation and pushing the boundaries of what is possible in CNC machining. By staying at the forefront of technological advancements and industry trends, the company is poised to introduce new capabilities and solutions that will continue to raise the bar for precision engineering. With a dedicated team of engineers and experts, China CNC Component Parts is well-equipped to tackle complex challenges and deliver cutting-edge products that exceed expectations.
In conclusion, China CNC Component Parts has demonstrated remarkable growth and success, solidifying its position as a premier manufacturer of precision CNC components. Through its unwavering commitment to quality, customer satisfaction, and innovation, the company has established itself as a trusted partner for a wide range of industries and expanded its global reach to better serve its international clientele. As China CNC Component Parts continues to push the boundaries of CNC machining, the future looks bright for the company and its customers alike.
Company News & Blog
Highly Efficient 3 Axis CNC Vertical Machining Center Unveiled in China's Manufacturing Industry
China's 3 Axis CNC Vertical Machining Center has taken the manufacturing industry by storm. This specialized machine is designed to be used by manufacturers who want to deliver consistent precision and accuracy in their production processes. The technology behind this equipment is a marvel, and the manufacturers of this CNC Machining Center have refined it to near perfection.The Chinese manufacturer behind this innovative product has built a strong reputation for delivering high-quality machines that help revolutionize manufacturing processes. Their deep understanding of the industry's needs, coupled with their focus on innovative and cutting-edge technology, has seen them feature prominently in the industry's success stories.Like many of their machines, the 3 Axis CNC Vertical Machining Center is built to handle large volumes of material. It is ideal for a wide range of industries such as automotive, aerospace, medical devices, and many more, where precision and accuracy are critical.The 3 Axis CNC Vertical Machining Center is designed with the user in mind. It is easy to operate, and the user interface is intuitive, eliminating the need for specialized training. This machine is a perfect fit for users who want to optimize their process as it enables them to deliver higher quality products quickly.One of the standout features of this machine is that it can handle complex and intricate shapes and designs. With the 3-axis configuration, this machining center allows for multi-dimensional cutting, which provides the user with a wide range of processing capabilities.Another notable feature of this machining center is the spindle speed. The spindle speed is an important aspect of machining, and the 3 Axis CNC Vertical Machining Center delivers on this. It has a high speed, and the spindle can handle a wide range of materials, including steel, copper, and aluminum. This means that manufacturers can process materials with a high degree of efficiency since they can handle varying degrees of hardness.In addition, this machine is highly versatile. Its configuration can be customized to meet specific production requirements. Whether it's a varying range of material types or shapes, the 3 Axis CNC Vertical Machining Center is a machine you can count on to deliver precision and accuracy with every cut.The Chinese manufacturer of this machine has demonstrated their commitment to delivering machines that are not only efficient, but that help customers achieve excellence in their manufacturing processes. They have invested in research and development to ensure this machine aligns with the latest technological advancements. They are always looking for ways to make their machines more efficient and more effective.Through their extensive network of authorized dealers and support mechanisms, the Chinese manufacturer ensures that customers get the support they need to optimize their processes. They offer technical support, machine maintenance, and a wide range of spare parts associated with their machines.Overall, the 3 Axis CNC Vertical Machining Center is a machine that is setting new standards in the manufacturing industry. With its high precision, versatility, and efficiency, it is no surprise that it has become a popular choice for manufacturers and businesses in various industries. The Chinese manufacturer behind this machine has proven to be a reliable partner for businesses looking to refine their processes, and with their commitment to excellence, we can expect more innovative products from them in the future.
Expert Steel Fabricators: Providing Top-Quality Steel Services" could be rewritten as "Premium Steel Fabrication Services: Delivering Exceptional Results" without mentioning the specific brand name.
Steel Fabrication Services, a leading provider of high-quality steel fabrication solutions, is revolutionizing the industry with its cutting-edge technology and exceptional customer service. With years of expertise and a commitment to innovation, the company has become synonymous with excellence in the field.Specializing in custom-made fabricated steel products, Steel Fabrication Services caters to a wide range of industries including construction, manufacturing, oil and gas, and infrastructure. The company offers a diverse range of services such as structural steel fabrication, welding, and engineering design. From large-scale projects to small tailor-made solutions, their team of highly skilled professionals ensures top-notch quality and timely delivery every time.One of the main factors that sets Steel Fabrication Services apart from its competitors is its state-of-the-art manufacturing facility equipped with the latest technology. The company utilizes advanced computer-aided design (CAD) software and high-precision machinery to deliver accurate and finely crafted steel products. This combination of cutting-edge technology and skilled craftsmanship allows for the production of complex and intricate steel structures that meet the highest standards of quality and precision.In addition to its advanced manufacturing capabilities, Steel Fabrication Services takes great pride in its commitment to customer satisfaction. The company understands that every client has unique requirements and works closely with them to provide tailored solutions that fulfill their specific needs. With a customer-centric approach, Steel Fabrication Services aims to build long-term relationships with its clients based on trust and mutual success.An integral part of Steel Fabrication Services' success is its team of highly trained and experienced professionals. The company employs a dedicated workforce that is passionate about what they do and strives for excellence in every project. From project managers to welders, every member of the team plays a crucial role in ensuring the highest level of workmanship and attention to detail.Furthermore, Steel Fabrication Services is committed to maintaining the highest industry standards and certifications. The company follows strict quality control procedures to ensure that all steel products meet or exceed customer expectations and industry regulations. With a strong emphasis on safety and efficiency, Steel Fabrication Services consistently delivers safe and reliable steel solutions to its clients.The company's dedication to innovation and continuous improvement is reflected in its investment in research and development. Steel Fabrication Services constantly seeks new ways to enhance its manufacturing processes and efficiency, resulting in cost-effective solutions for its clients without compromising on quality. By staying at the forefront of technological advancements, the company maintains its competitive edge in the industry.As an environmentally conscious organization, Steel Fabrication Services strives to minimize its carbon footprint. The company implements sustainable practices throughout its operations and consistently explores ways to reduce waste and promote energy efficiency. By adopting eco-friendly approaches, Steel Fabrication Services contributes to a greener future while providing top-notch steel fabrication solutions.With its exceptional services, state-of-the-art technology, and commitment to customer satisfaction, Steel Fabrication Services continues to lead the way in the steel fabrication industry. As the company looks towards the future, it remains focused on innovation, quality, and providing customized solutions to meet the evolving needs of its clients.In conclusion, Steel Fabrication Services is a trusted name in the steel fabrication industry, offering a wide range of high-quality products and services. With its advanced technology, skilled workforce, and customer-centric approach, the company strives to exceed customer expectations and deliver excellence in every project.
Professional Steel Welding Services for Your Project Needs
Steel Welding Service, a leading provider of welding and fabrication services, is pleased to announce the launch of their newest location in the heart of the industrial district. With over 20 years of experience in the welding industry, Steel Welding Service has established itself as a trusted partner for businesses in need of high-quality welding and fabrication solutions.The new facility is equipped with state-of-the-art machinery and a team of highly skilled welders and fabricators, allowing Steel Welding Service to meet the increasing demand for their services in the area. The company's commitment to excellence and customer satisfaction has been a driving force behind their expansion, and the new location will enable them to better serve their growing client base."We are thrilled to open our newest location in the industrial district," said the CEO of Steel Welding Service. "This expansion is a testament to our dedication to providing top-notch welding and fabrication services to our clients. We are excited to bring our expertise and craftsmanship to the businesses in this area and look forward to fostering new partnerships."Steel Welding Service offers a wide range of welding and fabrication services, including MIG welding, TIG welding, stainless steel fabrication, aluminum fabrication, custom metal fabrication, and more. Their team of experts is capable of handling projects of all sizes, from small prototypes to large-scale industrial applications. By combining cutting-edge technology with traditional craftsmanship, Steel Welding Service ensures that each project is completed with precision and according to the highest standards of quality.In addition to their welding and fabrication capabilities, Steel Welding Service also offers on-site welding and fabrication services, allowing clients to receive their services directly at their location. This convenience has been instrumental in their success, as it enables businesses to minimize downtime and improve efficiency by having their welding and fabrication needs met on-site.The company's dedication to exceptional customer service and satisfaction has earned them a stellar reputation in the industry. Steel Welding Service has built long-lasting relationships with their clients by consistently delivering superior results and exceeding expectations. Their commitment to quality and reliability has set them apart as a leader in the welding and fabrication space.With the opening of their new location, Steel Welding Service is poised to further elevate their position as a trusted provider of welding and fabrication solutions. The company's expansion represents a significant milestone in their growth, and they are eager to extend their services to more businesses in the industrial district and beyond.As they continue to expand, Steel Welding Service remains focused on upholding their core values of integrity, professionalism, and excellence. Their team is dedicated to staying at the forefront of industry advancements and delivering innovative solutions that meet the evolving needs of their clients. With their new location, Steel Welding Service is well-equipped to continue exceeding expectations and setting new standards for welding and fabrication services.For businesses in need of top-quality welding and fabrication services, Steel Welding Service stands as a reliable and capable partner. Their commitment to excellence, combined with their extensive experience and expertise, makes them the go-to choice for businesses looking for superior welding and fabrication solutions. As they embark on this new chapter of growth, Steel Welding Service is fully prepared to meet the increasing demand for their services and provide unmatched craftsmanship to their clients.
Welding Techniques for Joining Stainless Steel and Mild Steel - Available for Sale in China
Welding stainless steel and mild steel together is a challenging task. It requires expertise, precision and high-quality equipment. The process involves joining two materials with different chemical and mechanical properties, which can lead to cracking, distortion and other issues if not done correctly. In this blog, we will explore the process of welding mild steel to stainless steel and some of the challenges that come with it.First, let's look at the materials themselves. Stainless steel has a high chromium content, which makes it resistant to corrosion and stains. It is also harder and more brittle than mild steel, which is why it is challenging to weld the two materials together. Mild steel, on the other hand, has a lower carbon content, making it more ductile and easier to work with when compared to stainless steel.When welding stainless steel to mild steel, there are several methods to consider. Let's take a closer look at some of the most popular welding techniques.1. TIG (Tungsten Inert Gas) Welding: This is one of the most popular welding techniques used in welding stainless steel to mild steel. It provides a precise, clean and high-quality weld, making it ideal for applications that require a high degree of accuracy.2. MIG (Metal Inert Gas) Welding: This is a more straightforward technique compared to TIG welding. It is faster, easier to learn and produces a durable weld. However, the quality of the weld is lower than TIG welding, which may not be suitable for high-end applications.3. Stick Welding: This is a versatile welding method that can be used to weld different materials. It produces a rugged and robust weld that can withstand high temperatures, making it ideal for industrial applications.Regardless of the welding technique used, welding stainless steel to mild steel requires proper preparation. The surface must be clean, free of rust, oil and other contaminants that can affect the quality of the weld. Additionally, the two metals must be preheated to ensure that the thermal stresses are minimized during the welding process.One of the biggest challenges when welding stainless steel to mild steel is the difference in melting points. Stainless steel has a much higher melting point than mild steel, which means that it can easily warp or crack if the welder is not careful. Hence, it is crucial to use specialized welding techniques and equipment to ensure that the two materials are welded together properly without cracking or distortion.In conclusion, welding stainless steel to mild steel can be a daunting task, but it is possible with the right skills, tools, and techniques. With proper preparation and welding processes, it is possible to achieve a strong and durable weld between the two materials. If you need more information on welding stainless steel to mild steel or other welding-related topics, please feel free to reach out to our team of experts.
Welding Techniques for Steel Pipe in Construction and Manufacturing
Steel Pipe Welding: A Key Component in the Manufacturing ProcessSteel pipe welding is a crucial process in the manufacturing of various products, from industrial machinery to infrastructure components. The welding of steel pipes requires precision, expertise, and high-quality equipment to ensure the integrity and durability of the final product. With the advancement of technology and the increasing demand for high-quality steel products, the need for efficient and reliable steel pipe welding has never been greater.{} is a leading company in the field of steel pipe welding, with a long history and a strong reputation for delivering superior products and services. Founded in 1980, {} has been at the forefront of technological innovation in the steel industry. The company's state-of-the-art facilities and highly skilled workforce have made it a trusted partner for businesses across various industries.The process of steel pipe welding involves joining two steel pipes together using various welding techniques. The quality of the weld is crucial to the overall strength and integrity of the pipe, as any defects or inconsistencies can compromise the structural integrity of the final product. {}'s team of certified welders and engineers are experts in a wide range of welding techniques, including arc welding, gas tungsten arc welding, and gas metal arc welding, among others. This expertise allows {} to deliver precision welding that meets the highest industry standards.In addition to its expertise in welding techniques, {} utilizes cutting-edge equipment and technology to ensure the highest quality and efficiency in the welding process. The company's modern welding machines and robotic welding systems are capable of handling a wide range of pipe sizes and materials, allowing for flexibility and adaptability in the manufacturing process. This combination of expertise and technology positions {} as a leader in the field of steel pipe welding.One of the key advantages of {}'s steel pipe welding process is its ability to produce high-quality welds with minimal distortion and stress on the material. This results in a final product that is not only strong and durable but also aesthetically pleasing. The company's focus on precision and attention to detail ensures that its welded steel pipes meet or exceed the stringent requirements of its clients, whether they are in the automotive, aerospace, construction, or energy sectors.Moreover, {} is committed to upholding the highest standards of safety and environmental responsibility in its welding processes. The company's facilities adhere to strict safety protocols, and its welding operations are designed to minimize emissions and waste. This commitment to sustainability and safety not only benefits the environment but also ensures a safe and healthy working environment for the company's employees.As the demand for high-quality steel products continues to grow, the role of steel pipe welding in the manufacturing process will only become more critical. {}'s dedication to excellence and innovation in steel pipe welding positions it as a trusted partner for businesses seeking top-notch welding solutions. Whether it's for a large-scale infrastructure project or the production of precision machinery, {}'s expertise and state-of-the-art facilities make it a leader in the field of steel pipe welding.In conclusion, steel pipe welding is an essential component of the manufacturing process for a wide range of products. With its expertise, advanced technology, and commitment to quality and safety, {} is well-positioned to meet the growing demand for high-quality welded steel pipes. The company's dedication to excellence and innovation makes it a trusted partner for businesses across various industries, ensuring that their products meet the highest standards of quality and reliability.
Custom CNC Bending Service: Expert Metal Fabrication Solutions
We are delighted to introduce our company's latest addition to our services - CNC Bending. As a leading provider of metal fabrication solutions, we are constantly striving to enhance our capabilities and offer our customers a comprehensive range of services. With the addition of CNC Bending, we are able to provide even more efficient and precise metal bending solutions to meet the diverse needs of our clients.Our CNC Bending service utilizes state-of-the-art equipment and technology to achieve precise and accurate bends in a variety of materials, including steel, aluminum, and stainless steel. This cutting-edge technology allows us to bend complex shapes and designs with ease, ensuring that our customers receive the highest quality results for their projects.In addition to our advanced equipment, our team of skilled technicians are highly experienced in operating the CNC Bending process, ensuring that each bend is executed with precision and consistency. Whether it's a simple bend or a complex multi-bend part, our team is dedicated to delivering top-notch results that meet the exact specifications of our customers.With this new service, we are able to cater to a wide range of industries, including automotive, aerospace, construction, and manufacturing. Our CNC Bending capabilities allow us to accommodate small-scale projects as well as large-scale production runs, providing our clients with the flexibility and scalability they need for their metal fabrication needs.As a company committed to delivering excellence in metal fabrication, we take pride in offering a complete suite of services to our clients. From CNC machining to sheet metal fabrication, welding, and now CNC Bending, we are equipped to handle every aspect of our customer's metal fabrication needs.Our dedication to quality, precision, and customer satisfaction sets us apart as a leader in the industry. With the addition of CNC Bending to our services, we are confident that we will continue to exceed the expectations of our customers and serve as a trusted partner for all their metal fabrication needs.In conclusion, we are thrilled to announce the expansion of our services to include CNC Bending. With this new capability, we are well-positioned to provide our customers with a comprehensive range of metal fabrication solutions that are efficient, precise, and tailored to their specific needs. Whether it's a single prototype or a large production run, our team is ready to deliver exceptional results that meet the highest standards of quality and craftsmanship. We look forward to the opportunity to serve our customers with our new CNC Bending service and are excited about the possibilities it brings for our company and our clients.
How to Achieve Cold Welding with Stainless Steel
Cold Welding Stainless Steel Sets New Standards in Metal JoiningCold Welding Stainless Steel, a revolutionary technology developed by an American company founded in 2005, is set to disrupt the metal joining industry. The innovative technology, which involves the joining of metal surfaces by creating atomic bonds at room temperature and pressure, has shown remarkable results that surpass traditional welding methods in terms of performance, cost efficiency, and sustainability.The process of cold welding involves two metal surfaces being pressed together with a force of several tons. This creates enough deformation on the atomic scale to cause the atoms of the two surfaces to bond together. The result is a metallurgical bond that is stronger than the base metal, free from defects, and has excellent mechanical and chemical properties. The process is also performed at room temperature, eliminating the need for intense heat and producing little to no fumes and harmful byproducts.The technology has significant advantages over traditional welding methods. First, there is no need for a heat source, which eliminates the need for expensive welding equipment and reduces the energy consumption used in the welding process. Secondly, the process is highly efficient as minimal material is lost due to the lack of heat input. Thirdly, the technology is environmentally friendly as it eliminates the need for gases and fluxes that are used in traditional welding and create harmful emissions.Cold Welding Stainless Steel has a wide range of applications, including aerospace, automotive, medical instruments, precision instruments, and electronics, among others. In the aerospace industry, the technology is used to join titanium, aluminum, and other metals used in the construction of airplanes and space vehicles. The technology is also used in automotive applications, where it is used to join dissimilar metals, such as aluminum and steel, to improve fuel efficiency by reducing the weight of the vehicle.In the medical industry, Cold Welding Stainless Steel is used to join small and fragile components used in surgical instruments, where precision and high mechanical properties are critical. The technology is also used in the electronics industry, where it is used to join connectors and microelectronic components. The applications of Cold Welding Stainless Steel are vast, and its advantages make it a highly valuable technology across a range of industries.Apart from being a highly functional technology, Cold Welding Stainless Steel is also cost-effective. The elimination of heat and welding equipment, as well as the reduction in material waste, makes it a cost-effective alternative to traditional welding methods. Additionally, the eco-friendly aspect of the technology makes it an attractive option for businesses looking to reduce their carbon footprint and maintain sustainability.Furthermore, the technology is user-friendly as it doesn't require specialized training or certification to operate. Only simple tools are needed to perform cold welding, making it easily accessible to a wide range of operators.In conclusion, Cold Welding Stainless Steel is a revolutionary technology that promises to transform the metal joining industry. The technology's remarkable results in terms of performance, cost efficiency, and sustainability, coupled with its vast range of applications, make it a highly valuable technology for a range of industries. With the ability to join metals at room temperature and pressure, the technology has set new standards in metal joining, propelling the industry forward into a new era of innovation and functionality.
How to Weld Mild Steel to Stainless Steel: Tips and Techniques
In the fast-paced world of manufacturing, advancements in technology and materials are constantly pushing the boundaries of what is possible. One such advancement is the ability to weld mild steel to stainless steel, a process that was previously thought to be impossible due to the disparate properties of the two materials. However, through careful research and development, {company name} has successfully developed a method for welding these two materials together, opening up new possibilities for engineers and designers.{Company name} is a leading manufacturer of welding equipment and supplies, known for their innovative solutions and dedication to quality. Founded in 1980, {company name} has a long history of pushing the boundaries of what is possible in the welding industry. With a team of experienced engineers and technicians, they have consistently developed cutting-edge technologies that have revolutionized the way that welding is done.The process of welding mild steel to stainless steel has long been a challenge for manufacturers. Stainless steel is a high-alloy steel that contains at least 10.5% chromium, which gives it its characteristic resistance to corrosion and oxidation. On the other hand, mild steel is a low-carbon steel that is much easier to weld due to its lower carbon content. The challenge lies in the fact that these two materials have different melting points and react differently to heat, making it difficult to join them together seamlessly.However, {company name} has developed a proprietary welding process that allows for the successful joining of mild steel to stainless steel. This process involves the use of specialized welding equipment and techniques that have been carefully engineered to ensure a strong and durable bond between the two materials. This breakthrough has the potential to revolutionize the manufacturing industry, opening up new possibilities for the construction of a wide range of products that require the use of both mild steel and stainless steel.The ability to weld mild steel to stainless steel has a wide range of applications across various industries. For example, in the automotive industry, this breakthrough could lead to the development of lighter and more durable vehicles, as manufacturers would be able to use a combination of mild steel and stainless steel in their designs. In the construction industry, the ability to weld these two materials together could lead to the development of stronger and more corrosion-resistant building materials. Additionally, in the manufacturing of household appliances and consumer goods, this technology could lead to the creation of more durable and long-lasting products.{Company name} has already begun working with various industry partners to implement this new welding process into their manufacturing operations. They have also been conducting extensive testing and research to further refine and improve the process, ensuring that it meets the highest standards of quality and performance. With their track record of innovation and expertise in the welding industry, {company name} is well-positioned to lead the way in the adoption of this new technology.The successful development of this welding process is a testament to {company name}'s commitment to pushing the boundaries of what is possible in the welding industry. By overcoming the long-standing challenge of welding mild steel to stainless steel, they have opened up new possibilities for engineers and designers, and have the potential to revolutionize the manufacturing industry as a whole. As they continue to refine and improve this technology, {company name} is poised to have a significant impact on the future of welding and manufacturing. With their dedication to innovation and their track record of success, {company name} is sure to continue to lead the way in the development of cutting-edge welding technologies.
Advanced Methods for Precision Cutting: Laser vs. Waterjet
Laser And Waterjet Cutting Technology Innovations Revolutionize Manufacturing IndustryThe manufacturing industry is constantly evolving as new technologies and innovations are introduced. Laser and waterjet cutting have been at the forefront of these advancements, providing companies with the ability to precisely cut a wide range of materials, including metal, plastic, and composites. By combining these cutting technologies with state-of-the-art machinery and software, companies like {} are revolutionizing the manufacturing industry.{} is a leader in the manufacturing industry, specializing in precision cutting and fabrication services. With a commitment to quality, innovation, and customer satisfaction, {} has become a trusted partner for companies in a variety of industries, including aerospace, automotive, and medical device manufacturing.Laser cutting technology has become a preferred method for precision cutting in the manufacturing industry. By using a high-powered laser, materials can be cut with extreme accuracy, resulting in clean edges and minimal material waste. This technology is especially valuable for companies that require intricate and complex designs, as it can produce detailed cuts that would be challenging to achieve with traditional cutting methods.In addition to laser cutting, {} has also implemented waterjet cutting technology into their manufacturing processes. Waterjet cutting utilizes a high-pressure stream of water mixed with an abrasive substance to cut through materials with precision and ease. This technology is advantageous for cutting materials that are sensitive to heat, such as certain metals and composites, as it does not produce a heat-affected zone during the cutting process.By integrating both laser and waterjet cutting technologies, {} has been able to expand their capabilities and offer a more comprehensive range of cutting services to their customers. This combination of technologies allows {} to accommodate a wider variety of materials and project specifications, giving them a competitive edge in the manufacturing industry.One of the key benefits of laser and waterjet cutting technology is its versatility. {} has the ability to cut a wide range of materials, including stainless steel, aluminum, titanium, plastics, and even exotic metals. This versatility makes laser and waterjet cutting a valuable asset for companies that require custom parts and components for their products.Furthermore, laser and waterjet cutting technology can accommodate various thicknesses of materials, from thin sheets to thick plates. This flexibility allows {} to take on a diverse range of projects, from intricate and delicate cuts to heavy-duty fabrication work. With the ability to cater to a wide spectrum of cutting needs, {} has solidified its position as a go-to solution provider for companies seeking high-quality cutting and fabrication services.The implementation of laser and waterjet cutting technology has also contributed to improved efficiency and cost-effectiveness in the manufacturing process. By using these advanced cutting methods, {} is able to reduce material waste, minimize the need for additional finishing processes, and achieve faster production times. This efficiency not only benefits {} as a company but also provides their customers with cost savings and quicker turnaround times for their projects.As the manufacturing industry continues to evolve, the demand for innovative cutting technologies will only grow. The combination of laser and waterjet cutting has proven to be a game-changer for companies like {}, allowing them to elevate their capabilities and provide high-quality cutting solutions to their customers. With a steadfast commitment to excellence and a focus on continuous improvement, {} is poised to remain at the forefront of the manufacturing industry, driving advancements in precision cutting and fabrication services.