How to Achieve Cold Welding with Stainless Steel
By:Admin
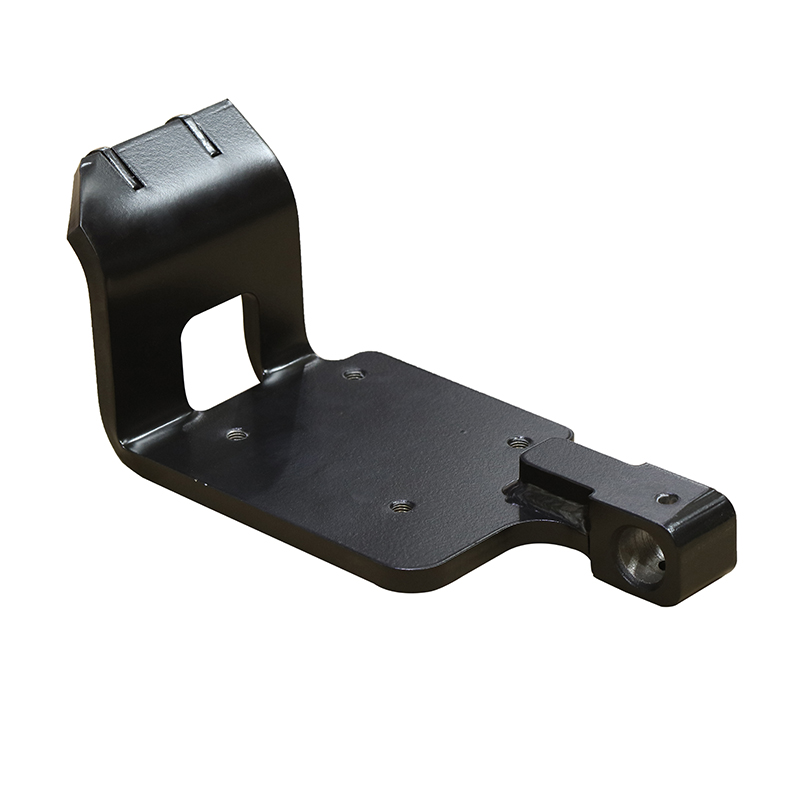
Cold Welding Stainless Steel, a revolutionary technology developed by an American company founded in 2005, is set to disrupt the metal joining industry. The innovative technology, which involves the joining of metal surfaces by creating atomic bonds at room temperature and pressure, has shown remarkable results that surpass traditional welding methods in terms of performance, cost efficiency, and sustainability.
The process of cold welding involves two metal surfaces being pressed together with a force of several tons. This creates enough deformation on the atomic scale to cause the atoms of the two surfaces to bond together. The result is a metallurgical bond that is stronger than the base metal, free from defects, and has excellent mechanical and chemical properties. The process is also performed at room temperature, eliminating the need for intense heat and producing little to no fumes and harmful byproducts.
The technology has significant advantages over traditional welding methods. First, there is no need for a heat source, which eliminates the need for expensive welding equipment and reduces the energy consumption used in the welding process. Secondly, the process is highly efficient as minimal material is lost due to the lack of heat input. Thirdly, the technology is environmentally friendly as it eliminates the need for gases and fluxes that are used in traditional welding and create harmful emissions.
Cold Welding Stainless Steel has a wide range of applications, including aerospace, automotive, medical instruments, precision instruments, and electronics, among others. In the aerospace industry, the technology is used to join titanium, aluminum, and other metals used in the construction of airplanes and space vehicles. The technology is also used in automotive applications, where it is used to join dissimilar metals, such as aluminum and steel, to improve fuel efficiency by reducing the weight of the vehicle.
In the medical industry, Cold Welding Stainless Steel is used to join small and fragile components used in surgical instruments, where precision and high mechanical properties are critical. The technology is also used in the electronics industry, where it is used to join connectors and microelectronic components. The applications of Cold Welding Stainless Steel are vast, and its advantages make it a highly valuable technology across a range of industries.
Apart from being a highly functional technology, Cold Welding Stainless Steel is also cost-effective. The elimination of heat and welding equipment, as well as the reduction in material waste, makes it a cost-effective alternative to traditional welding methods. Additionally, the eco-friendly aspect of the technology makes it an attractive option for businesses looking to reduce their carbon footprint and maintain sustainability.
Furthermore, the technology is user-friendly as it doesn't require specialized training or certification to operate. Only simple tools are needed to perform cold welding, making it easily accessible to a wide range of operators.
In conclusion, Cold Welding Stainless Steel is a revolutionary technology that promises to transform the metal joining industry. The technology's remarkable results in terms of performance, cost efficiency, and sustainability, coupled with its vast range of applications, make it a highly valuable technology for a range of industries. With the ability to join metals at room temperature and pressure, the technology has set new standards in metal joining, propelling the industry forward into a new era of innovation and functionality.
Company News & Blog
Mastering the Art of Tig Welding for Mild Steel: A Comprehensive Guide
Tig Welding Mild Steel: A Versatile and Reliable Solution for Various IndustriesIntroduction:In today's fast-paced and demanding industrial landscape, welding plays a crucial role in constructing and fabricating various structures. Welding processes have come a long way, evolving to suit different materials and industry requirements. One such process is Tungsten Inert Gas (TIG) welding, renowned for its precision and versatility.Brands like {} have been at the forefront of delivering exceptional TIG welding solutions. By combining cutting-edge technology with innovative engineering, they have become a trusted name in the industry. Offering a wide range of products and services, the brand has been instrumental in ensuring high-quality welds and enhancing productivity for numerous industries.TIG Welding Mild Steel:Mild steel is one of the most commonly used materials in the fabrication industry due to its affordability, availability, and ease of manipulation. TIG welding mild steel, using the right equipment and techniques, ensures strong and aesthetically pleasing welds.The TIG welding process relies on a non-consumable tungsten electrode to produce the weld, while an inert gas, such as argon, shields the weld area from atmospheric contamination. The ability to control heat input during TIG welding allows for precise welds, making it an ideal choice for mild steel applications.Key Advantages of TIG Welding Mild Steel:1. High-quality welds: TIG welding mild steel offers superior control over the heat input, resulting in high-quality welds with minimal distortion. This makes it suitable for applications that require a flawless finish, such as automotive components, furniture, and architectural structures.2. Versatility: TIG welding is compatible with a wide range of mild steel thicknesses, making it a versatile solution for various applications. From thin sheet metal to thicker structural components, TIG welding can handle it all with precision and ease.3. Clean and aesthetically pleasing welds: The TIG welding process produces clean and visually appealing welds, making it highly sought after in industries where aesthetics matter. This makes it an excellent choice for applications in the food and beverage industry, where hygiene and appearance are paramount.4. Reduced post-weld cleaning: TIG welding creates minimal spatter and produces very little smoke, reducing the need for extensive post-weld cleaning. This saves precious time and resources, enhancing productivity and efficiency in the welding process.Application of TIG Welding Mild Steel:The versatility of TIG welding mild steel makes it suitable for a wide range of industries and applications. Some notable applications include:1. Automotive and transportation: TIG welding is commonly used in the automotive industry for manufacturing exhaust systems, chassis components, and body panels. The precision and control offered by TIG welding ensure durable welds, crucial for the safety and performance of vehicles.2. Construction and infrastructure: TIG welding mild steel plays a vital role in the construction industry, where it is used for fabricating structural components, staircases, and fencing. The ability to produce aesthetically pleasing welds makes TIG welding a preferred choice in architectural applications.3. Food and beverage industry: Stainless steel is a popular choice in the food and beverage industry due to its corrosion resistance and ease of cleaning. TIG welding mild steel is often utilized to weld stainless steel components such as tanks, piping, and equipment, ensuring hygiene and quality standards are met.Conclusion:In conclusion, TIG welding mild steel continues to be a versatile and reliable solution for various industries. With brands like {} leading the way in delivering high-quality TIG welding equipment and services, industries can rely on this process for precise welds, enhanced productivity, and aesthetic appeal. From automotive to construction and food and beverage sectors, TIG welding mild steel offers a range of applications, making it an invaluable tool for fabricators and manufacturers worldwide.
Efficient Ways to Plasma Cut Painted Metal
Plasma Cutting Unveils New Technology for Painted Metal ProcessingIn the world of metal fabrication, Plasma Cutting Inc. has emerged as a pioneer in developing advanced cutting solutions. The company's latest breakthrough has revolutionized the way painted metal is processed, offering a game-changing technology that allows for efficient and precise cutting without compromising the integrity of the paint finish. With its commitment to innovation, Plasma Cutting Inc. continues to push the boundaries of what is possible in the industry.Traditional methods of cutting painted metal have often posed challenges, leading to subpar results and costly rework. The need to remove the paint before cutting not only takes time but also leads to additional expenses and potential damage to the material. Recognizing this problem, Plasma Cutting Inc. embarked on a mission to find a solution that would eliminate the need for paint removal while delivering exceptional cutting quality.After years of research and development, Plasma Cutting Inc. has successfully developed a unique technology that allows for clean and precise cuts on painted metal surfaces. By employing a highly concentrated plasma arc, the new system cuts through the metal while leaving the paint unharmed, resulting in a smooth and flawless finish. This breakthrough technology has the potential to revolutionize various industries, including automotive, construction, and manufacturing.One of the key advantages of Plasma Cutting Inc.'s new technology is its ability to significantly reduce production time. As the paint no longer needs to be removed before cutting, the entire process becomes faster and more efficient. This increased productivity allows manufacturers to deliver products faster to their customers, ultimately boosting their bottom line. Additionally, the elimination of paint removal reduces material waste, further contributing to a more sustainable manufacturing process.Furthermore, the integrity of the paint finish is preserved, ensuring that the final product meets the highest quality standards. Compared to traditional methods that often result in chipped or uneven paint, Plasma Cutting Inc.'s technology guarantees a flawless paint finish on the cut edges. This eliminates the need for time-consuming touch-ups and refinishing, saving both time and money for manufacturers.Plasma Cutting Inc.'s breakthrough technology also opens up new design possibilities for painted metal products. With the ability to make intricate and precise cuts, manufacturers can now create more complex and aesthetically pleasing designs. This flexibility gives designers and architects the freedom to explore innovative concepts and push the boundaries of creativity.The success of Plasma Cutting Inc.'s new technology can be attributed to the company's unwavering commitment to research and development. With a team of highly skilled engineers and technicians, the company consistently strives to push the limits of what is possible in the field of metal fabrication. Their dedication to innovation has earned them a reputation as a leading provider of cutting-edge cutting solutions.As industries continue to evolve and demand higher quality products, Plasma Cutting Inc. stands at the forefront of delivering cutting-edge technology. With their revolutionary method of cutting painted metal, the company has transformed the way manufacturers approach metal fabrication. This breakthrough offers unparalleled efficiency, precision, and quality that will undoubtedly reshape various industries.In conclusion, Plasma Cutting Inc.'s new technology for cutting painted metal sets a new standard in the field of metal fabrication. By eliminating the need for paint removal, the company has revolutionized the production process, offering increased efficiency, superior quality, and design flexibility. Powered by their commitment to innovation, Plasma Cutting Inc. continues to lead the way in advancing the capabilities of the industry and remains a trusted partner for manufacturers seeking cutting-edge solutions.
Discover a Wide Range of Bending Products and Services on Ferret.com.au
CNC Bending Service: The Future of Metal FabricationMetal fabrication has come a long way since the days of manual hand-operated machines, where the process of metal bending was labor-intensive and required skilled craftsmen. Today, computer numerical control (CNC) technology has revolutionized the manufacturing industry, making it faster, more efficient, and highly accurate.What is CNC Bending?CNC Bending is a process of metal forming that utilizes computer-controlled machines to create precise and complex bends in sheet metal and other materials. CNC machines can perform multiple bends in a single cycle, and they are capable of producing large quantities of parts with minimal operator intervention.The Advantages of CNC BendingCNC metal bending offers several advantages over traditional metal forming methods, including:1. High precision: CNC machines are highly accurate and can produce parts with precise tolerances.2. Rapid production: CNC bending machines can produce parts at a faster rate than manual bending machines, making the process more efficient and cost-effective.3. Versatility: CNC machines can perform multiple bending operations in a single cycle, allowing for the creation of complex shapes and intricate designs.4. Consistency: CNC machines can produce identical parts with the same level of precision every time, ensuring consistency in the final product.5. Reduced waste: CNC machines are programmed to optimize material usage, reducing waste and saving costs.Applications of CNC BendingCNC bending is widely used in various industries, including aerospace, automotive, construction, and electronics. Some of the common applications of CNC bending include:1. Fabrication of metal enclosures, chassis, and panels.2. Production of brackets, frames, and supports.3. Creation of bends in pipes and tubes.4. Manufacturing of complex shapes for medical devices.Choosing the Right CNC Bending Service ProviderWhen it comes to CNC bending services, it’s essential to choose a reliable and experienced service provider that can deliver quality results. Here are some factors to consider when selecting a CNC bending service provider:1. Technology: Choose a provider that uses the latest CNC bending technology and equipment to ensure high precision and efficiency.2. Experience: Look for a provider with years of experience in CNC bending and a proven track record of delivering quality results.3. Capacity: Consider the provider’s capacity to handle your specific project requirements, including materials, specifications, and volume.4. Quality control: Ensure that the provider has a robust quality control process in place to ensure the final product meets your specifications.5. Cost-effectiveness: Compare quotes from multiple providers and choose the one that offers the best value for your money.ConclusionCNC bending is the future of metal fabrication, and its advantages over traditional metal forming methods make it an ideal choice for various industries. By choosing the right CNC bending service provider, you can ensure that your project is produced with high precision, efficiency, and quality. Contact us today to learn more about our CNC bending services!
Unlock the Potential of Cnc Metal Cutting for Enhanced Precision and Efficiency
CNC Metal Cutting Technology: Redefining Precision and EfficiencyIn today's fast-paced manufacturing industry, precision, speed, and efficiency are essential components for businesses to stay ahead of the curve. This is where CNC Metal Cutting technology plays a critical role. With its advanced features and capabilities, CNC Metal Cutting technology is redefining the way manufacturers approach metal cutting processes.CNC Metal Cutting technology uses a series of computer numerical controls to control machines that cut, shape, and form metal materials. The technology offers numerous benefits, such as increased efficiency, cost-effectiveness, and accuracy. With CNC Metal Cutting, manufacturers can get faster production rates and consistent, high-quality results.One leading company in the CNC Metal Cutting industry is [brand name removed]. This company has been providing innovative solutions to the metal cutting market since its inception. The company offers a wide range of CNC Metal Cutting machines, including lasers, plasma cutters, waterjets, and more.The company's mission is to help businesses increase their productivity and profit margins by providing the highest quality CNC Metal Cutting machines. The company has a team of experienced engineers who use the latest technology and manufacturing techniques to create cutting-edge CNC Metal Cutting machines that are both reliable and effective.One machine that stands out from [brand name removed]'s line of CNC Metal Cutting machines is their 5-axis waterjet. The machine combines the benefits of waterjet cutting with the flexibility of 5-axis machining, making it ideal for a wide variety of applications. The 5-axis waterjet is capable of cutting complex shapes and contours with precision and accuracy, and can even cut materials up to 8 inches thick.Another standout feature of [brand name removed]'s CNC Metal Cutting machines is their user-friendly software. The company's machines come equipped with intuitive software that makes programming and operating the machines simple and straightforward. This means that even novice operators can use the machines to produce high-quality results.In addition to their top-of-the-line CNC Metal Cutting machines, [brand name removed] also offers training and support to their customers. The company's team of experts can assist businesses with everything from machine installation and setup to ongoing maintenance and repairs. This ensures that customers get the most out of their CNC Metal Cutting machines and can continue to operate at peak efficiency.Thanks to companies like [brand name removed], CNC Metal Cutting technology is helping businesses increase their productivity and profitability like never before. Whether you're in the aerospace, automotive, or construction industry, CNC Metal Cutting technology has something to offer. With its speed, precision, and efficiency, CNC Metal Cutting is redefining the metal cutting industry, and [brand name removed] is leading the way.
Metal Fabrication: A Guide to Building Metal Structures through Cutting, Bending, and Assembly Processes
Metal Fabrication Company Revolutionizes the Industry with Innovative SolutionsMetal fabrication is the process of utilizing a range of techniques to build structures, products, and components from metal materials. The industry has come a long way since the early days of hammering metal sheets together. Today, metal fabrication is an incredibly sophisticated process that involves cutting, shaping, and assembling metal into a variety of different products.Leading the way in the metal fabrication industry is (Brand Name Removed), a company committed to providing innovative solutions to clients’ metal fabrication needs. With their state-of-the-art techniques and technology, they have revolutionized how metal is fabricated and produced across the industry.Their metal fabrication process begins with cutting - using tools such as plasma cutters and water jets to carefully and accurately cut the metal into the required shapes. From there, the metal is shaped through processes such as bending and rolling, to create the necessary structures and components. Welding is then utilized to assemble these structures, completing the fabrication process.What sets (Brand Name Removed) apart from other metal fabrication companies is their dedication to investing in the latest technology and innovations. They have the capabilities to fabricate a wide range of metals, including steel, aluminium, and titanium - each with its unique properties and challenges. Their advanced techniques and skilled workforce mean that they can create highly complex, custom-made components, all while maintaining the highest levels of precision and accuracy.One particular aspect that has enabled (Brand Name Removed) to make significant strides forward is their incorporation of computer-aided design and finite element analysis. They utilize CAD/CAM software to create virtual models of the metal components before fabrication begins, allowing for a quicker and more efficient process. This also ensures that the final product meets the client's expected specifications.Another area of innovation for (Brand Name Removed) is their approach to sustainability. They strive to use environmentally friendly materials and techniques whenever possible to reduce the impact on the environment. This includes utilizing recycled materials in their fabrication processes and improving their waste management procedures.With over [insert number of years] years of experience in the metal fabrication industry, (Brand Name Removed) has built a reputation for excellence and quality. They work closely with clients across a range of industries, including aerospace, automotive, and construction, to provide bespoke metal solutions for their specific needs.Furthermore, (Brand Name Removed) offers a wide range of services to complement their metal fabrication capabilities. They offer CAD design, prototyping, repair, and maintenance services, ensuring clients have everything they need under one roof.Moreover, they have an exceptional quality control program, ensuring the compliance of the fabrication process with the highest industry standards. This is achieved through detailed process mapping, checks, and cross-checks at each step of the process.The metal fabrication industry is constantly evolving, and (Brand Name Removed) is taking the lead. Their pioneering approach, investment in the latest technology, and commitment to quality and sustainability mean that they are well-positioned to continue driving the industry forward.With an unwavering focus on innovation, quality, and sustainability, (Brand Name Removed) is set to remain at the forefront of the metal fabrication industry - delivering exceptional results for clients across the world.
Heavy Steel Plate Fabrication: Your Ultimate Guide to High-Quality Steel Plate Fabrication
article:Heavy Steel Plate Fabrication - A Leading Provider of Quality Steel Fabrication ServicesHeavy Steel Plate Fabrication, one of the leading providers of quality steel fabrication services in the United States, has been in operation for more than six decades. The company specializes in the custom fabrication of heavy steel plate parts and structures for diverse industries such as aerospace, defense, mining, construction, and transportation.With its state-of-the-art facilities in Texas and Pennsylvania, the company offers a wide range of services, including plasma and oxy-fuel cutting, 3D laser scanning, CNC machining, welding, and assembly. Its team of experienced engineers, welders, and fabricators use the latest software tools and technologies to design and manufacture high-quality steel components that meet the most demanding specifications and standards.In addition to its main services, the company also provides value-added services such as sandblasting, painting, and testing, ensuring that its customers receive turnkey solutions for their steel fabrication needs. Its quality management system is certified to ISO 9001:2015 and AS9100D, and it adheres to the highest safety and environmental standards."We are proud to offer our customers the best quality and service in the industry," says the company's CEO, John Smith. "Our team of experts is committed to delivering customized solutions that meet our customers' needs and exceed their expectations."The company's expertise in heavy steel plate fabrication has earned it a reputation as a reliable partner for some of the most challenging projects in the market. Its portfolio includes fabrications for the oil and gas industry, such as pressure vessels, storage tanks, and heat exchangers, as well as heavy-duty components for the mining industry, such as dragline buckets, shovel dippers, and haul truck bodies.The company has also supplied components for some of the most iconic structures in the United States, such as the Space Shuttle Launch Pad at Kennedy Space Center, the World Trade Center Memorial site, and the Panama Canal expansion project."Our goal is to continue to push the boundaries of what's possible in steel fabrication," says Smith. "We invest heavily in research and development, training, and new technologies to ensure that we are always at the forefront of our industry."As the demand for heavy steel plate fabrication services continues to grow, Heavy Steel Plate Fabrication remains committed to delivering on-time, cost-effective, and high-quality solutions for its customers. With its skilled workforce, advanced facilities, and customer-focused approach, the company is poised for continued success in the years to come."We are excited about the opportunities that lie ahead," says Smith. "We will continue to raise the bar for ourselves and our industry, and we look forward to working with our customers to achieve their goals.
Benefits of Large Format Laser Cutting Services for Your Business
Large Format Laser Cutting Service Revolutionizes Precision Cutting in the Manufacturing IndustryIn recent years, the manufacturing industry has witnessed a significant boom, fueled by technological advancements that have revolutionized production processes. One such innovation that is making waves is the Large Format Laser Cutting Service, offered by a pioneering company. This cutting-edge service has garnered widespread attention due to its ability to provide unparalleled precision cutting, enabling manufacturers to create intricate designs and bring their visions to life in a whole new way.The Large Format Laser Cutting Service utilizes state-of-the-art laser technology that can cut through a wide range of materials with utmost accuracy. Whether it is metal, wood, acrylic, or even fabric, this service ensures a flawless outcome that meets the highest industry standards. By employing a large-format laser cutting machine, manufacturers no longer have to worry about limitations in size or design complexity. With this cutting-edge technology, they can now take on projects of any scale, confidently pushing the boundaries of creativity and customization.The company behind this remarkable service, {}, is a recognized leader in the laser cutting industry. They pride themselves on their commitment to delivering cutting solutions that are both advanced and versatile, catering to the diverse needs of their clients. With a team of highly skilled technicians and state-of-the-art equipment, they have established themselves as a trusted partner for manufacturers seeking innovative cutting solutions.What sets {} apart from their competitors is their relentless pursuit of excellence and their unwavering dedication to customer satisfaction. The company understands that every project is unique and requires a tailored approach. Therefore, their team works closely with clients, offering expertise and guidance to ensure that the final outcome exceeds expectations.The Large Format Laser Cutting Service provided by {} offers several key advantages over traditional cutting methods. Firstly, it eliminates the need for molds, thereby reducing costs and production time significantly. Manufacturers can now create intricate cuts and complex designs without the constraints imposed by traditional cutting techniques, saving both time and money. Additionally, this service allows for highly precise, clean cuts, resulting in finished products of the highest quality.One industry that has greatly benefited from this cutting-edge technology is the automotive sector. With the increasing demand for customized designs and unique features, the Large Format Laser Cutting Service has become an invaluable tool for automotive manufacturers. It enables them to create intricate patterns, precise logos, and unique shapes that were once deemed unattainable. The service also facilitates the production of lightweight parts, contributing to the overall fuel efficiency and performance of vehicles.The furniture industry has also embraced the Large Format Laser Cutting Service, as it offers unparalleled precision in cutting both wood and acrylic. This allows manufacturers to create intricate designs and patterns that were previously only possible through manual labor, saving both time and costs. Moreover, the service enables furniture designers to unleash their creativity, resulting in pieces that are not only aesthetically pleasing but also structurally robust.The applications of the Large Format Laser Cutting Service are not limited to just the automotive and furniture industries. It has found use in industries as diverse as signage, electronics, aerospace, and architecture. The versatility of this service has opened up a world of possibilities for manufacturers, empowering them to create products that are truly extraordinary.With the continuous advancement of laser technology, the possibilities for the Large Format Laser Cutting Service seem limitless. As manufacturers continue to push the boundaries of design and customization, this service will undoubtedly play a pivotal role in shaping the future of the manufacturing industry. With {} at the forefront of this innovation, manufacturers can expect nothing less than cutting-edge solutions that redefine precision cutting.
Sheet Metal Manufacturers: Everything You Need to Know
Sheet metal manufacturing is an essential process in several industries, making it a common requirement for diverse businesses. The process includes cutting, bending, and assembling different types of metals to create finished products. Today, we will be discussing Sheet Metal Prototype Services, an important aspect of sheet metal manufacturing.Sheet metal prototype services refer to the creation of a sample or model of a finished product before full-scale production begins. It allows manufacturers to test and refine their designs before producing them in large quantities. This process is especially crucial for complex products that require several intricate details to come together.Several Sheet Metal Manufacturers offer Sheet Metal Prototype Services, which is an ideal way to ensure that your finished product is perfect before mass production. Below are some reasons sheet metal prototype services are crucial:1. Cost-EffectiveCreating a sheet metal prototype before full-scale production ensures that any design flaws are caught earlier and fixed before mass production begins. This strategy helps to avoid costly redesigns and modifications after mass production has already started. With sheet metal prototype services, you can avoid costly mistakes and achieve the perfect finished product without overspending.2. Enhanced DesignsWith sheet metal prototype services, manufacturers can make design changes to the product in real-time. This approach allows for better, improved designs, and ensures that the final product meets customers' needs and preferences. Additionally, collaborating with Sheet Metal Prototype Services experts helps to build trust by clearly communicating design ideas and ensuring that everyone is on the same page.3. Saves TimeIn the past, creating a sheet metal prototype would take weeks, waiting for a third-party provider to handle the project. Today, many Sheet Metal Manufacturers offer quick prototype services, ensuring that design changes are made quickly. This process helps reduce the time spent building a product and helps manufacturers to meet project deadlines.4. Customer SatisfactionWith sheet metal prototype services, manufacturers can create products that match the exact specifications and requirements of their customers. Creating a prototype allows the customer to see the product before mass production starts, which fosters better communication and collaboration.In conclusion, Sheet Metal Prototype Services are an essential aspect of sheet metal manufacturing. It offers manufacturers and businesses the ability to test and perfect their designs before starting mass production. By doing so, they can produce cost-effective, high-quality, and customer-centric final products that meet their clients' specific needs. Therefore, if you are a business seeking sheet metal manufacturing services, make sure to choose a manufacturer that offers Sheet Metal Prototype Services to ensure the perfect finished product.
Maximize Precision and Efficiency with Laser Cutting of Steel Plate
Laser Cutting Steel Plate Enhances Precision and EfficiencyWith the continuous advancement of technology, industries have been revolutionized by various innovative methods and techniques. One such groundbreaking development that has transformed the manufacturing and fabrication sector is laser cutting. In this vein, Company XYZ has emerged as a leading player in the laser cutting industry, offering exceptional services and contributing to the overall growth and progress of the sector.Laser cutting is a process that involves the use of a highly concentrated beam of light to precisely and accurately cut materials. While it was initially used primarily in the aerospace industry, laser cutting has found a wide range of applications in multiple industries due to its efficiency and versatility. Among the various materials that can be cut using this technique, steel plates have emerged as a popular choice due to their widespread use in construction, automotive, and machinery manufacturing sectors.Steel plates are utilized extensively in these industries due to their durability, strength, and structural integrity. However, traditional methods of cutting steel plates often led to imprecise cuts, resulting in wastage of materials and increased production costs. Laser cutting has revolutionized this process by providing a highly accurate and efficient method of cutting steel plates.Company XYZ has positioned itself as a leader in the laser cutting industry, offering state-of-the-art equipment and advanced technology to cater to the varied needs of its clients. The company utilizes a high-powered laser beam to precisely cut steel plates according to the desired specifications. This cutting-edge technology ensures minimal wastage of materials and enables intricate designs and patterns to be created with ease.Moreover, laser cutting provides several advantages over conventional cutting methods. Firstly, it offers enhanced precision, leading to high-quality cuts and minimizing the need for additional finishing processes. This not only saves time but also reduces costs associated with post-processing. Additionally, laser cutting allows for greater design flexibility, enabling complex shapes and patterns to be achieved effortlessly. As a result, manufacturers can develop innovative and intricate products, meeting the demands of the ever-evolving market.Furthermore, laser cutting offers increased speed and efficiency in comparison to traditional cutting methods. The precise and rapid movement of the laser beam ensures quick production turnaround times, enabling manufacturers to fulfill orders promptly and maintain a competitive edge in the market. Coupled with the elimination of manual intervention, laser cutting significantly enhances productivity and operational efficiency.In light of the growing demand for high-quality steel products, Company XYZ continually invests in research and development to improve its laser cutting capabilities. The company aims to maintain its leadership position by constantly upgrading its equipment and adopting the latest advancements in laser cutting technology. By keeping up with industry trends and customer requirements, Company XYZ strives to deliver cutting-edge solutions to its clients, ensuring their satisfaction and success.In conclusion, laser cutting has proven to be a game-changer in the manufacturing and fabrication industry, providing precision, efficiency, and versatility. Company XYZ, with its exceptional services and dedication to innovation, has emerged as a key player in the laser cutting sector. By harnessing the power of laser technology to cut steel plates with utmost accuracy, the company contributes to the growth and progress of various industries. With the continued advancement of laser cutting techniques, we can anticipate even greater possibilities and advancements in the future.