Innovative Laser Cutting and Bending Services for Your Manufacturing Needs
By:Admin
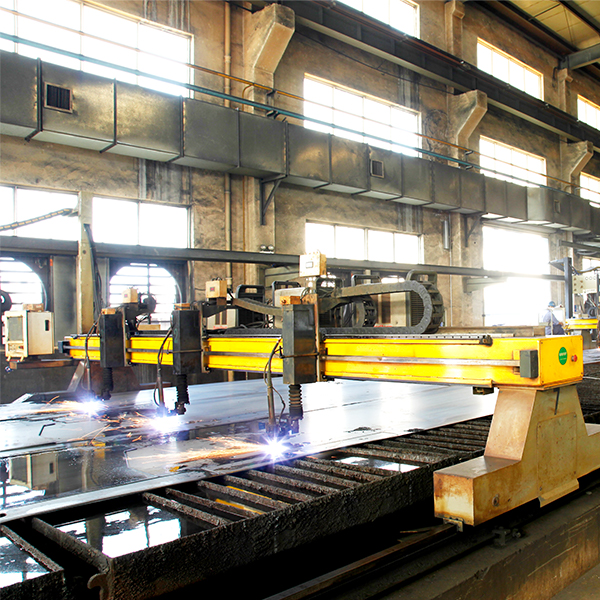
In this regard, {} stands out as a leading provider of laser cutting and bending services. With state-of-the-art machinery and a team of skilled professionals, {} has built a reputation for delivering superior quality and accuracy in their services. The company has been at the forefront of innovation in the industry and has continuously invested in the latest technology to meet the evolving needs of its customers.
One of the key advantages of laser cutting is its ability to cut through a variety of materials with high precision and speed. This makes it an ideal choice for industries that require intricate designs and complex shapes. Additionally, laser cutting produces minimal waste and results in cleaner edges, making it a cost-effective and sustainable solution for manufacturing processes.
On the other hand, bending is a crucial process in sheet metal fabrication that allows for the creation of different shapes and structures. With the use of advanced press brake machinery, {} is able to provide accurate and consistent bending services, ensuring that the final products meet the desired specifications and quality standards.
With the combination of laser cutting and bending services, {} offers a comprehensive solution for its clients' manufacturing needs. Whether it's creating components for machinery, customizing parts for automotive applications, or producing intricate designs for architectural purposes, the company has the expertise and capabilities to deliver high-quality results.
In addition to its cutting-edge technology and skilled workforce, {} prides itself on its commitment to customer satisfaction. The company works closely with its clients to understand their specific requirements and provide tailor-made solutions that meet their expectations. With a focus on transparency, reliability, and on-time delivery, {} has established long-lasting partnerships with its clients, earning their trust and loyalty.
Furthermore, {} places a strong emphasis on quality control and has stringent processes in place to ensure that the products meet the highest standards. From initial design and engineering to manufacturing and finishing, the company performs rigorous quality checks at every stage of the production process to guarantee precision and accuracy.
Beyond its technical capabilities, {} is also dedicated to fostering a culture of continuous improvement and innovation. The company invests in research and development to explore new techniques and technologies that can further enhance its services. By staying ahead of industry trends and embracing new advancements, {} remains at the forefront of the laser cutting and bending sector.
As the manufacturing landscape continues to evolve, {} is poised to meet the increasing demand for high-quality laser cutting and bending services. With its cutting-edge technology, skilled workforce, and customer-centric approach, the company is well-positioned to drive innovation and excellence in the industry. Whether it's delivering complex components with tight tolerances or producing customized solutions for unique applications, {} is committed to being the preferred partner for all laser cutting and bending needs.
Company News & Blog
Key Information on Choosing the Right Welding Electrode for Your Project
Title: Revolutionary Welding Electrode Innovates the Industry - Improving Efficiency and QualityIntroduction:In the ever-evolving world of welding technology, companies are continuously seeking new advancements to enhance efficiency and quality. In line with this demand, {Company Name}, a renowned industry leader, has introduced an innovative welding electrode that promises to revolutionize the field. This welding electrode, which boasts incredible capabilities, is set to transform welding processes, streamline operations, and deliver exceptional results like never before.Company Overview:{Company Name}, a well-established welding solutions provider, has a rich history of delivering cutting-edge products. With a commitment to quality and continuous innovation, the company has become a trusted partner for various industries, including automotive, construction, oil and gas, and manufacturing. Their team of skilled engineers and technicians work diligently to develop advanced welding technologies that address industry challenges and meet customer needs.Revolutionary Welding Electrode:The latest offering from {Company Name}, which we shall refer to as the "Advanced Welding Electrode," is the result of years of research and development. This innovative product is designed to enhance welding operations by improving efficiency, productivity, versatility, and overall welding quality.Improved Efficiency and Productivity:The Advanced Welding Electrode incorporates state-of-the-art features that significantly improve efficiency and productivity. Its enhanced coating formulation ensures smooth and steady arc stability, resulting in reduced spatter and welding defects. This attribute greatly decreases post-welding clean-up time, allowing welders to operate more efficiently and complete projects in a shorter duration.Moreover, the electrode's excellent heat dissipation properties minimize the risk of overheating, reducing downtime due to material damage and equipment failure. This feature, combined with its exceptional tie-in wetting ability, ensures seamless fusion between metals, maximizing welding productivity and minimizing waste.Enhanced Versatility and Adaptability:{Company Name}'s Advanced Welding Electrode offers superior adaptability to a wide range of welding scenarios. It is suitable for various metals, including carbon steel, stainless steel, and non-ferrous alloys. This versatile electrode performs exceptionally well in all welding positions, allowing welders to work with ease and confidence while maintaining high-quality standards.Additionally, the electrode's unique self-releasing slag formula improves welder visibility during the welding process. This enhancement promotes precise control and accuracy, resulting in meticulously welded joints, especially in complex and intricate welding projects.Uncompromised Welding Quality:The focus on welding quality is evident in every aspect of the Advanced Welding Electrode. Its remarkable arc stability, combined with minimal spatter and excellent slag control, ensures clean and smooth welds with minimal defects. This remarkable weld integrity is further reinforced by the electrode's ability to eliminate undesirable elements like sulfur and phosphorus, guaranteeing welds of exceptional quality and longevity.Moreover, {Company Name} has implemented rigorous quality control processes to guarantee consistent electrode performance. The company subjects each electrode batch to comprehensive testing, including tensile strength, elongation, and impact toughness assessments. This dedication to quality assurance provides customers with utmost confidence in the product's reliability and performance.Conclusion:{Company Name}'s introduction of the Advanced Welding Electrode is poised to create a significant impact in the welding industry. With its advanced features, enhanced efficiency and productivity, versatility, and unwavering commitment to welding quality, this revolutionary electrode presents unmatched benefits for welders across various industries.As {Company Name} continues to innovate and provide cutting-edge solutions, the Advanced Welding Electrode is a testament to their dedication towards empowering welders and revolutionizing the welding industry. The progressive strides made by {Company Name} demonstrate their commitment to meeting the evolving needs of the market while ensuring sustainable success for their customers.
Discover the Key Processes Involved in Sheet Metal Fabrication at a Leading Factory
On a bustling industrial estate in the heartland of American manufacturing, the Sheet Metal Fabrication Factory (name removed for anonymity) is a hive of activity. The factory is a testament to the ingenuity and enterprise of the American people, as it produces a range of high-quality metal parts and components that are in demand across many different industries.The Sheet Metal Fabrication Factory specializes in producing customized metal products and parts, meaning that it is well-equipped to handle any project that requires precision, durability, and versatility. The factory's team of highly-skilled technicians and engineers work in tandem to produce metal parts and components that are bespoke to the client's needs. With cutting-edge technology and machinery, the factory is able to turn raw materials into high-quality metal products that are designed to withstand the toughest environments.The factory has earned a reputation for excellence in the industry, due in part to its commitment to providing exceptional customer service. The Sheet Metal Fabrication Factory works closely with its clients to ensure that their needs are met, often going above and beyond to ensure that their expectations are exceeded. As a result, the company has earned a loyal customer base that spans many industries, including aerospace, automotive, defense, and medical.One of the most impressive things about the Sheet Metal Fabrication Factory is its in-house design and engineering team. The team is composed of highly-skilled professionals who work closely with clients to develop bespoke solutions that meet their unique requirements. Using state-of-the-art software and equipment, the team is able to produce 3D models of the product before it goes into production, allowing clients to preview the finished product before it is produced. This level of precision ensures that the finished product meets or exceeds the client's expectations.The factory's capabilities are equally impressive. Sheet metal is cut, punched, and folded with utmost precision, while welding, polishing, and finishing are carried out to the highest standards. The factory also offers a range of surface treatments and coatings, such as anodizing and powder coating, that can be customized to suit any need.In addition to its impressive production capabilities, the Sheet Metal Fabrication Factory is also committed to sustainability. The company sources its raw materials from ethical and sustainable sources whenever possible, and takes steps to minimize waste and energy consumption during the production process. This commitment to sustainability has earned the factory recognition from industry bodies and clients alike, and has helped to cement its position as one of the leading metal fabrication companies in the country.Overall, the Sheet Metal Fabrication Factory is an impressive and dynamic company that has proven itself to be a leader in its field. Boasting state-of-the-art technology, an exceptional staff, and a commitment to sustainability, this factory is uniquely equipped to deliver high-quality metal products and components that meet and exceed the needs of its clients. As American manufacturing continues to evolve and adapt to changing market conditions, the Sheet Metal Fabrication Factory will undoubtedly remain at the forefront of innovation and excellence.
Steps to Obtain a Metal Fabrication License in NSW
Metal fabrication is an important process in many industries that involves shaping and creating metal structures that are used in various applications. If you wish to operate a metal fabrication business in NSW, you need to obtain a metal fabrication license from the NSW Fair Trading department.The metal fabrication works can range from simple welding and sheet metal fabrication to complex engineering design and fabrication of intricate metal structures. With a metal fabrication license in hand, you can start your business and cater to various clients in need of custom metal fabrication for their specific applications.To obtain a metal fabrication license in NSW, you must first meet the eligibility criteria set by the NSW Fair Trading department. These criteria are designed to ensure that the applicants have necessary knowledge and experience to provide high-quality metal fabrication works.The eligibility criteria include:1. Completion of a Certificate III in Engineering - Fabrication Trade.2. Three years of experience in the metal fabrication industry.3. A completed SafeWork NSW General Construction Induction Training course.4. Submission of the required paperwork, including application and fee payment.Once you meet the eligibility criteria, you can apply for a metal fabrication license by submitting your application and providing all the necessary information. The NSW Fair Trading will review your application and may ask for additional information if required.After the review, if your application is approved, you will receive your metal fabrication license, and you can start operating your business in NSW.The metal fabrication works in NSW are regulated by the relevant state and federal laws, including the Work Health and Safety Act and the Building Code of Australia. You must comply with all these laws and regulations to ensure your business operates safely and legally.Apart from the legal requirements, there are also some best practices that you should follow as a metal fabricator. These practices include using high-quality materials, ensuring proper design and engineering, and using safe and effective fabrication methods.Metal fabrication works involve various techniques and tools such as CNC machines, laser cutters, and welding equipment. You must have the necessary skills and knowledge to operate these tools safely and effectively.In conclusion, a metal fabrication license is a necessary requirement for anyone who wishes to operate a metal fabrication business in NSW. By obtaining this license, you can offer high-quality metal fabrication works to your clients and ensure compliance with relevant laws and regulations. Follow the eligibility criteria, regulations, and best practices to ensure your business operates efficiently and safely.
How Laser Cutting is Revolutionizing Manufacturing Processes
Laser Plate Cutting: The Future of Precision ManufacturingIn our increasingly tech-savvy world, precision and accuracy have become more important than ever before. As such, precision manufacturing has taken center stage, with companies constantly seeking new and innovative ways to create perfect, intricate, and detailed products. One such innovation is laser plate cutting, a process that uses lasers to make precise cuts in a variety of materials. In this blog, we'll dive into the world of laser plate cutting and explore why it's the future of precision manufacturing.What is Laser Plate Cutting?Laser plate cutting is a process that uses a high-powered laser to cut through a variety of materials, including steel, aluminum, and other metals. The laser beam is directed at the material, creating a highly focused point of heat that melts or vaporizes the material in a precise and controlled manner. This process results in clean, sharp, and accurate cuts that are free of burrs or other imperfections.How Does Laser Plate Cutting Work?To understand how laser plate cutting works, it's helpful to understand how a laser works in the first place. A laser (which stands for Light Amplification by Stimulated Emission of Radiation) emits a highly concentrated beam of light that is focused on a small area. This beam is made up of photons, which are particles of light. When the photons hit a material, they transfer energy to it, causing it to heat up and melt or vaporize.In laser plate cutting, the laser beam is directed onto a plate of material using a series of mirrors and lenses. The laser can be adjusted to various settings, including power and speed, to ensure the most precise cut possible. The process can be automated using computer-controlled systems, which allows for even greater precision and speed.Benefits of Laser Plate CuttingSo why is laser plate cutting the future of precision manufacturing? There are several key benefits to the process that set it apart from other types of cutting:1. Precision and accuracy: Laser plate cutting allows for incredibly precise cuts that are free of burrs or other imperfections.2. Speed: Laser cutting is faster than many other cutting methods, which means that products can be created more quickly.3. Versatility: Laser cutting can be used on a wide range of materials, including metals, plastics, and even glass.4. Cost-effectiveness: Although laser plate cutting requires expensive equipment, it can ultimately save money in the long run by reducing waste and the need for additional finishing processes.Applications of Laser Plate CuttingLaser plate cutting has a wide range of applications across many industries. Here are just a few examples:1. Aerospace: Laser cutting is used to create precise components for aircraft engines, landing gear, and other systems.2. Automotive: Laser cutting is used to create parts for cars and trucks, including body panels, suspension components, and exhaust systems.3. Medical: Laser cutting is used to create surgical tools, implants, and other medical equipment that requires precision and accuracy.4. Technology: Laser cutting is used to create components for consumer electronics, such as smartphones and tablets.ConclusionIn conclusion, laser plate cutting is the future of precision manufacturing. With its ability to create precise, accurate cuts on a wide range of materials, laser cutting has become an essential tool for many industries. As technology continues to advance, we can expect to see even greater innovations in laser cutting, making it an even more important part of the manufacturing process. So if you're looking for the most precise and accurate cuts for your next project, consider laser plate cutting.
Efficient Ways to Plasma Cut Painted Metal
Plasma Cutting Unveils New Technology for Painted Metal ProcessingIn the world of metal fabrication, Plasma Cutting Inc. has emerged as a pioneer in developing advanced cutting solutions. The company's latest breakthrough has revolutionized the way painted metal is processed, offering a game-changing technology that allows for efficient and precise cutting without compromising the integrity of the paint finish. With its commitment to innovation, Plasma Cutting Inc. continues to push the boundaries of what is possible in the industry.Traditional methods of cutting painted metal have often posed challenges, leading to subpar results and costly rework. The need to remove the paint before cutting not only takes time but also leads to additional expenses and potential damage to the material. Recognizing this problem, Plasma Cutting Inc. embarked on a mission to find a solution that would eliminate the need for paint removal while delivering exceptional cutting quality.After years of research and development, Plasma Cutting Inc. has successfully developed a unique technology that allows for clean and precise cuts on painted metal surfaces. By employing a highly concentrated plasma arc, the new system cuts through the metal while leaving the paint unharmed, resulting in a smooth and flawless finish. This breakthrough technology has the potential to revolutionize various industries, including automotive, construction, and manufacturing.One of the key advantages of Plasma Cutting Inc.'s new technology is its ability to significantly reduce production time. As the paint no longer needs to be removed before cutting, the entire process becomes faster and more efficient. This increased productivity allows manufacturers to deliver products faster to their customers, ultimately boosting their bottom line. Additionally, the elimination of paint removal reduces material waste, further contributing to a more sustainable manufacturing process.Furthermore, the integrity of the paint finish is preserved, ensuring that the final product meets the highest quality standards. Compared to traditional methods that often result in chipped or uneven paint, Plasma Cutting Inc.'s technology guarantees a flawless paint finish on the cut edges. This eliminates the need for time-consuming touch-ups and refinishing, saving both time and money for manufacturers.Plasma Cutting Inc.'s breakthrough technology also opens up new design possibilities for painted metal products. With the ability to make intricate and precise cuts, manufacturers can now create more complex and aesthetically pleasing designs. This flexibility gives designers and architects the freedom to explore innovative concepts and push the boundaries of creativity.The success of Plasma Cutting Inc.'s new technology can be attributed to the company's unwavering commitment to research and development. With a team of highly skilled engineers and technicians, the company consistently strives to push the limits of what is possible in the field of metal fabrication. Their dedication to innovation has earned them a reputation as a leading provider of cutting-edge cutting solutions.As industries continue to evolve and demand higher quality products, Plasma Cutting Inc. stands at the forefront of delivering cutting-edge technology. With their revolutionary method of cutting painted metal, the company has transformed the way manufacturers approach metal fabrication. This breakthrough offers unparalleled efficiency, precision, and quality that will undoubtedly reshape various industries.In conclusion, Plasma Cutting Inc.'s new technology for cutting painted metal sets a new standard in the field of metal fabrication. By eliminating the need for paint removal, the company has revolutionized the production process, offering increased efficiency, superior quality, and design flexibility. Powered by their commitment to innovation, Plasma Cutting Inc. continues to lead the way in advancing the capabilities of the industry and remains a trusted partner for manufacturers seeking cutting-edge solutions.
Discover the Evolution of Butt Welding: A Comprehensive Insight into Steel Welding Techniques
Title: Revolutionizing Steel Butt Welding: A Company IntroductionIntroduction:In the world of industrial manufacturing, steel butt welding plays a vital role in creating strong and reliable joint connections. However, the traditional methods of steel butt welding often come with their fair share of challenges, such as inconsistencies in joint quality, increased labor costs, and a lack of efficiency. But now, a revolutionary solution has emerged that promises to transform the steel welding industry. In this news article, we will dive into the company{} and its groundbreaking advancements in steel butt welding.Company Background:{} is a leading innovator in the field of industrial manufacturing, specializing in advanced techniques and technologies for steel welding. With a rich history dating back to its establishment in [year], the company has continuously strived to push the boundaries of traditional welding methods. Through extensive research and development, {} has successfully developed a state-of-the-art solution for steel butt welding that addresses many of the long-standing challenges faced by the industry.Revolutionary Advancements in Steel Butt Welding:The innovative technology developed by {} aims to revolutionize the way steel butt welding is performed. By combining cutting-edge equipment with advanced process control, this groundbreaking method offers several key benefits over traditional approaches. Let's explore some of the noteworthy advancements:1. Enhanced Joint Quality: {}'s steel butt welding technique ensures consistent and high-quality joint connections, thereby minimizing the risk of weld failures. With a focus on precision and accuracy, the company's technology eliminates common discontinuities and imperfections often associated with traditional welding methods.2. Increased Efficiency: The new steel butt welding method drastically improves efficiency, resulting in significant time and cost savings for manufacturers. By streamlining the welding process and reducing the need for manual intervention, {} enables faster production cycles while maintaining strict adherence to quality standards.3. Reduced Labor Costs: Traditional welding methods involve labor-intensive processes, requiring skilled welders to carry out intricate tasks. However, {}'s technology automates several stages of the welding process, reducing the dependency on skilled labor and optimizing workforce utilization. This, in turn, helps reduce labor costs without compromising on the quality of welded joints.4. Seamless Integration: One of the major advantages of {}'s steel butt welding solution is its compatibility with existing manufacturing infrastructure. The technology seamlessly integrates into a wide range of production setups, allowing manufacturers to adopt this revolutionary method without significant modifications or equipment replacements.5. Environmental Sustainability: Recognizing the increasing need for eco-friendly practices, {}'s steel butt welding solution focuses on minimizing environmental impact. By optimizing energy consumption and reducing waste generation, the company's technology promotes sustainable manufacturing processes while maintaining or exceeding industry standards.Conclusion:{}'s revolutionary advancements in steel butt welding are poised to redefine the industrial manufacturing landscape. By addressing the challenges of joint quality, efficiency, labor costs, compatibility, and sustainability, the company has successfully positioned itself as a frontrunner in the field. As manufacturers worldwide strive for improved welding solutions, {} provides an innovative and reliable option that promises long-term benefits for all stakeholders involved. With {}.
Leveraging the Power of CNC Laser Services for Your Business's Needs
CNC Laser Service Launches Cutting-Edge Laser Technology to Meet the Needs of Modern BusinessesThe world of manufacturing and industrial production is constantly evolving, and businesses that want to stay ahead of the curve need to stay up to date with the latest technology. That's why CNC Laser Service (name removed) has recently launched their latest laser cutting system, designed to meet the needs of today's businesses.At CNC Laser Service, we have been providing high-quality laser cutting solutions to our customers for over twenty years. During that time, we have built a reputation for excellence, innovation, and customer service, and we are committed to continuing to meet the evolving needs of our clients.Our latest laser cutting system is a testament to that commitment, incorporating the latest technology and design features to deliver precision cutting solutions that are unmatched in the industry. With CNC Laser Service's state-of-the-art system, businesses can quickly and easily create custom parts, prototypes, and products with the highest level of accuracy and efficiency.One of the key benefits of CNC Laser Service's new laser cutting system is its speed. The system can produce parts and products at a significantly faster pace than traditional cutting methods, which means businesses can bring their products to market much more quickly. This speed also allows for faster changes and modifications to products, which is essential in today's fast-paced business environment.The precision of our system is another crucial attribute. Our laser cutting technology allows us to make cuts with an accuracy of 0.001 of an inch, which means we can create parts and products that are incredibly precise, with no room for error. This level of precision not only ensures the final product is of the highest quality, but it also minimizes waste and reduces costs associated with errors or rework.Another feature that sets CNC Laser Service's cutting-edge laser technology apart from traditional manufacturing solutions is its flexibility. Our system can work with a wide range of materials, including metals, plastics, and even delicate materials such as fabrics and ceramics. This versatility means we can tailor our processes to meet the unique needs of each of our clients, covering a wide range of industries.CNC Laser Service's laser machine also offers a high level of customization, allowing us to create parts and products with unique shapes, sizes, and textures. This customization is a vital feature for businesses that need to create parts that are tailored to specific needs, such as the medical or aerospace industries.Finally, our system's automation capabilities allow us to streamline our processes and reduce the need for manual labor, which translates to lower costs and faster turnaround times for our clients. Our laser cutting system allows us to quickly and easily produce large quantities of parts, making it an ideal solution for businesses with high-volume manufacturing needs.At CNC Laser Service, we are incredibly proud of our latest laser cutting system and the benefits it offers our clients. With its speed, precision, flexibility, customization, and automation capabilities, our technology is poised to take businesses to the next level of manufacturing excellence.Whether you're in the automotive, medical, aerospace, defense, or any other industry, CNC Laser Service's laser cutting system has the capability to meet your unique needs. We invite you to contact us today to learn more about our cutting-edge technology and discover how we can help you take your business to the next level of success.
Mastering the Art of Tig Welding for Mild Steel: A Comprehensive Guide
Tig Welding Mild Steel: A Versatile and Reliable Solution for Various IndustriesIntroduction:In today's fast-paced and demanding industrial landscape, welding plays a crucial role in constructing and fabricating various structures. Welding processes have come a long way, evolving to suit different materials and industry requirements. One such process is Tungsten Inert Gas (TIG) welding, renowned for its precision and versatility.Brands like {} have been at the forefront of delivering exceptional TIG welding solutions. By combining cutting-edge technology with innovative engineering, they have become a trusted name in the industry. Offering a wide range of products and services, the brand has been instrumental in ensuring high-quality welds and enhancing productivity for numerous industries.TIG Welding Mild Steel:Mild steel is one of the most commonly used materials in the fabrication industry due to its affordability, availability, and ease of manipulation. TIG welding mild steel, using the right equipment and techniques, ensures strong and aesthetically pleasing welds.The TIG welding process relies on a non-consumable tungsten electrode to produce the weld, while an inert gas, such as argon, shields the weld area from atmospheric contamination. The ability to control heat input during TIG welding allows for precise welds, making it an ideal choice for mild steel applications.Key Advantages of TIG Welding Mild Steel:1. High-quality welds: TIG welding mild steel offers superior control over the heat input, resulting in high-quality welds with minimal distortion. This makes it suitable for applications that require a flawless finish, such as automotive components, furniture, and architectural structures.2. Versatility: TIG welding is compatible with a wide range of mild steel thicknesses, making it a versatile solution for various applications. From thin sheet metal to thicker structural components, TIG welding can handle it all with precision and ease.3. Clean and aesthetically pleasing welds: The TIG welding process produces clean and visually appealing welds, making it highly sought after in industries where aesthetics matter. This makes it an excellent choice for applications in the food and beverage industry, where hygiene and appearance are paramount.4. Reduced post-weld cleaning: TIG welding creates minimal spatter and produces very little smoke, reducing the need for extensive post-weld cleaning. This saves precious time and resources, enhancing productivity and efficiency in the welding process.Application of TIG Welding Mild Steel:The versatility of TIG welding mild steel makes it suitable for a wide range of industries and applications. Some notable applications include:1. Automotive and transportation: TIG welding is commonly used in the automotive industry for manufacturing exhaust systems, chassis components, and body panels. The precision and control offered by TIG welding ensure durable welds, crucial for the safety and performance of vehicles.2. Construction and infrastructure: TIG welding mild steel plays a vital role in the construction industry, where it is used for fabricating structural components, staircases, and fencing. The ability to produce aesthetically pleasing welds makes TIG welding a preferred choice in architectural applications.3. Food and beverage industry: Stainless steel is a popular choice in the food and beverage industry due to its corrosion resistance and ease of cleaning. TIG welding mild steel is often utilized to weld stainless steel components such as tanks, piping, and equipment, ensuring hygiene and quality standards are met.Conclusion:In conclusion, TIG welding mild steel continues to be a versatile and reliable solution for various industries. With brands like {} leading the way in delivering high-quality TIG welding equipment and services, industries can rely on this process for precise welds, enhanced productivity, and aesthetic appeal. From automotive to construction and food and beverage sectors, TIG welding mild steel offers a range of applications, making it an invaluable tool for fabricators and manufacturers worldwide.
Unlocking the Potential of Industrial Steel Fabrication: A Comprehensive Guide
Industrial Steel Fabrication announces expansion plans for increased production capacity[City, State] - Industrial Steel Fabrication, a leading provider of high-quality steel fabrication solutions, has unveiled plans for a significant expansion of its production facilities. This move comes in response to growing market demand and the need to meet increasing client requirements. Established in [year], Industrial Steel Fabrication has built a strong reputation for delivering innovative and reliable steel fabrication solutions to various sectors including construction, energy, manufacturing, and infrastructure development. With a focus on delivering high-quality products and unparalleled service, the company has become a trusted partner for clients seeking customized steel fabrication solutions. The expansion plans include the construction of a state-of-the-art facility that will house advanced machinery and equipment to enhance production capabilities. With a total investment of [amount], this project underscores the company’s commitment to providing cutting-edge solutions to its clients while also stimulating economic growth in the region.The new facility will enable Industrial Steel Fabrication to significantly increase its production capacity and expedite project schedules. By adopting advanced technologies and machinery, the company aims to streamline its operations, reduce lead times, and deliver enhanced quality products. This expansion will also create job opportunities, bringing economic benefits to the local community.In addition to enhancing production capacity, Industrial Steel Fabrication's expansion plans also include the implementation of sustainable practices. The new facility will be designed with energy-efficient systems, reducing the company's environmental footprint significantly. By incorporating sustainable technologies, the company aims to align its operations with global efforts to combat climate change and promote sustainable development.Speaking about the expansion plans, [Company Executive] expressed the company's enthusiasm, stating, "We are thrilled to announce this major expansion. With the growing demand for steel fabrication solutions worldwide, this investment will allow us to better serve our clients while also contributing to the economic development of [City]. We are committed to providing exceptional quality and service, and this expansion will ensure that we reach new heights in meeting client expectations."Industrial Steel Fabrication's expansion plans come at an opportune moment, with the construction and infrastructure sectors experiencing rapid growth. The company's ability to deliver specialized steel fabrication solutions to these sectors positions them well to capitalize on the increasing demand for infrastructure projects worldwide.Moreover, Industrial Steel Fabrication has a successful track record of completing high-profile projects. Through their expertise in engineering, fabrication, and project management, the company has become a trusted partner for major construction and infrastructure projects.As Industrial Steel Fabrication expands its production capacity, its commitment to innovation and customer satisfaction remains unchanged. The company looks forward to leveraging its expanded capabilities to provide even greater value to clients, delivering timely and cost-effective solutions that exceed expectations.With this expansion, Industrial Steel Fabrication is set to further solidify its position as a prominent player in the steel fabrication industry. Through continuous innovation, a customer-centric approach, and a commitment to sustainable practices, the company is poised to play a pivotal role in shaping the future of steel fabrication solutions.
Advanced Methods for Precision Cutting: Laser vs. Waterjet
Laser And Waterjet Cutting Technology Innovations Revolutionize Manufacturing IndustryThe manufacturing industry is constantly evolving as new technologies and innovations are introduced. Laser and waterjet cutting have been at the forefront of these advancements, providing companies with the ability to precisely cut a wide range of materials, including metal, plastic, and composites. By combining these cutting technologies with state-of-the-art machinery and software, companies like {} are revolutionizing the manufacturing industry.{} is a leader in the manufacturing industry, specializing in precision cutting and fabrication services. With a commitment to quality, innovation, and customer satisfaction, {} has become a trusted partner for companies in a variety of industries, including aerospace, automotive, and medical device manufacturing.Laser cutting technology has become a preferred method for precision cutting in the manufacturing industry. By using a high-powered laser, materials can be cut with extreme accuracy, resulting in clean edges and minimal material waste. This technology is especially valuable for companies that require intricate and complex designs, as it can produce detailed cuts that would be challenging to achieve with traditional cutting methods.In addition to laser cutting, {} has also implemented waterjet cutting technology into their manufacturing processes. Waterjet cutting utilizes a high-pressure stream of water mixed with an abrasive substance to cut through materials with precision and ease. This technology is advantageous for cutting materials that are sensitive to heat, such as certain metals and composites, as it does not produce a heat-affected zone during the cutting process.By integrating both laser and waterjet cutting technologies, {} has been able to expand their capabilities and offer a more comprehensive range of cutting services to their customers. This combination of technologies allows {} to accommodate a wider variety of materials and project specifications, giving them a competitive edge in the manufacturing industry.One of the key benefits of laser and waterjet cutting technology is its versatility. {} has the ability to cut a wide range of materials, including stainless steel, aluminum, titanium, plastics, and even exotic metals. This versatility makes laser and waterjet cutting a valuable asset for companies that require custom parts and components for their products.Furthermore, laser and waterjet cutting technology can accommodate various thicknesses of materials, from thin sheets to thick plates. This flexibility allows {} to take on a diverse range of projects, from intricate and delicate cuts to heavy-duty fabrication work. With the ability to cater to a wide spectrum of cutting needs, {} has solidified its position as a go-to solution provider for companies seeking high-quality cutting and fabrication services.The implementation of laser and waterjet cutting technology has also contributed to improved efficiency and cost-effectiveness in the manufacturing process. By using these advanced cutting methods, {} is able to reduce material waste, minimize the need for additional finishing processes, and achieve faster production times. This efficiency not only benefits {} as a company but also provides their customers with cost savings and quicker turnaround times for their projects.As the manufacturing industry continues to evolve, the demand for innovative cutting technologies will only grow. The combination of laser and waterjet cutting has proven to be a game-changer for companies like {}, allowing them to elevate their capabilities and provide high-quality cutting solutions to their customers. With a steadfast commitment to excellence and a focus on continuous improvement, {} is poised to remain at the forefront of the manufacturing industry, driving advancements in precision cutting and fabrication services.