Mastering the Art of Tig Welding on Cast Stainless Steel - Expert Guide
By:Admin
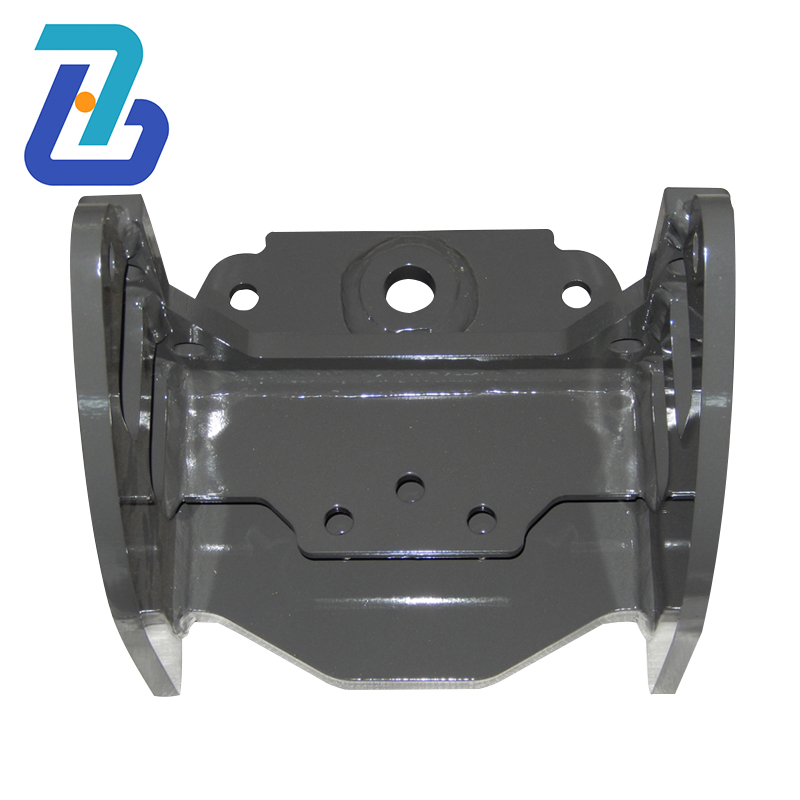
Introduction:
In today's rapidly advancing manufacturing industry, companies are continually striving to enhance their welding techniques to meet the growing demands of their customers. One such company, renowned for its innovation in the field of cast stainless steel welding, is {Name of Company}. Through a combination of cutting-edge technology and a strong commitment to research and development, they have recently achieved significant progress in Tig welding techniques for cast stainless steel. This article will delve into the latest advancements made by the company and their potential implications for the industry.
1. Background on Cast Stainless Steel:
Cast stainless steel is widely used in various industries, including automotive, aerospace, energy, and construction, primarily due to its exceptional corrosion resistance and high strength properties. However, welding cast stainless steel poses several challenges due to its unique metallurgical structure and inherent susceptibility to cracks and defects during the welding process. To overcome these challenges, {Name of Company} has dedicated significant resources to develop innovative welding techniques.
2. Innovations in Tig Welding for Cast Stainless Steel:
Tig welding, also known as Gas Tungsten Arc Welding (GTAW), has long been recognized as a reliable and efficient welding method for stainless steel alloys. However, when it comes to welding cast stainless steel, the process becomes much more intricate. {Name of Company} has made substantial breakthroughs in Tig welding, focusing specifically on cast stainless steel, resulting in enhanced weld quality and overall productivity.
a. Improved Pre-welding Preparation: To minimize defects during welding, {Name of Company} has introduced meticulous pre-welding preparation techniques, including thorough cleaning and surface conditioning of the cast stainless steel. By removing impurities and ensuring proper joint fit-up, the likelihood of defects such as porosity and cracking is significantly reduced.
b. Enhanced Heat Control: Achieving optimal heat input during the welding process is critical to prevent distortion, eliminate residual stresses, and maintain mechanical properties. {Name of Company} has developed advanced heat control systems, including rapid temperature monitoring and adaptive welding parameters, resulting in precise heat distribution and minimizing the risk of stress-related failures.
c. Filler Material Selection: {Name of Company} has extensively researched and tested various filler materials to match the specific metallurgical properties of cast stainless steel. This includes the development of new filler alloys with improved tensile strength, crack resistance, and corrosion resistance. The optimized selection of filler material greatly contributes to the durability and longevity of the welded joint.
d. Post-Weld Heat Treatment: Recognizing the importance of post-weld heat treatment for cast stainless steel, {Name of Company} has implemented innovative procedures to relieve residual stresses and improve the overall microstructure of the welded joint. Precisely controlled heat treatment cycles have proven to enhance the mechanical properties of the welded components, ensuring superior performance and longevity.
3. Implications for the Industry:
The advancements made by {Name of Company} in Tig welding techniques for cast stainless steel have significant implications for the manufacturing industry:
a. Improved Product Quality: The enhanced welding techniques result in higher-quality welds, with reduced defects and improved mechanical properties. This directly translates into superior-quality finished products for various industries reliant on cast stainless steel components.
b. Increased Productivity: The precise heat control and filler material selection contribute to increased productivity and overall manufacturing efficiency. With fewer defects and reduced post-welding process requirements, {Name of Company}'s advancements enable faster turnaround times and reduced costs.
c. Longevity and Reliability: Welded joints incorporating the advanced Tig welding techniques by {Name of Company} exhibit enhanced durability and improved resistance to corrosion, fatigue, and stress-related failures. This ensures the longevity and reliability of products in demanding environments, such as automotive and energy sectors.
Conclusion:
Through their relentless pursuit of innovation and dedication to delivering unmatched quality, {Name of Company} has revolutionized Tig welding techniques for cast stainless steel. Their advancements in pre-welding preparation, heat control, filler material selection, and post-weld heat treatment have led to superior weld quality, increased productivity, and enhanced product longevity. As the manufacturing industry continues to rely on cast stainless steel components, these advancements will undoubtedly play a pivotal role in shaping the future of Tig welding in this sector.
Company News & Blog
Laser Cut Cutting: A Revolutionary Technique for Precision Designs
Laser Cut Cutting Revolutionizes Manufacturing ProcessesIn today's rapidly evolving world, technology continues to redefine the way we live and work. One such innovation that has transformed traditional manufacturing processes is laser cut cutting. With its precision and efficiency, laser cut cutting has revolutionized industries and companies around the globe.Laser cut cutting, as the name suggests, involves the use of a high-powered laser beam to precisely cut or engrave various materials, including metal, plastic, wood, and even fabric. The laser beam is directed onto the surface of the material, creating a localized heat zone that vaporizes or melts the material, resulting in a clean and accurate cut.The advantages of laser cut cutting are manifold. Firstly, it offers unparalleled precision and accuracy. Laser technology allows for incredibly fine cuts and intricate detailing that would be impossible to achieve using traditional cutting methods. This level of precision has opened up endless possibilities for design and fabrication in various industries, including automotive, aerospace, electronics, and jewelry.Furthermore, laser cut cutting is an incredibly fast and efficient process. The laser beam operates at high speeds, allowing for rapid cutting and increased productivity. Additionally, laser cutting does not require any physical contact with the material, eliminating the risk of mechanical damage or contamination. This aspect makes it particularly valuable for fragile materials or intricate designs.Another key advantage of laser cut cutting is its versatility. The laser beam can be guided by computer-controlled software, enabling it to cut and engrave intricate patterns, shapes, and even 3D designs. This versatility allows for customization and personalization in product manufacturing, catering to individual customer preferences and demands.One company that has harnessed the power of laser cut cutting for their manufacturing processes is {}. Established in {}, the company has become a leading player in the industry, offering a wide range of laser cutting services to a diverse customer base.Specializing in the fabrication of metal products, {} has integrated laser cut cutting into every aspect of their manufacturing operations. With state-of-the-art laser cutting machines and highly skilled technicians, the company has consistently delivered high-quality products to their clients, meeting the most demanding specifications.The implementation of laser cut cutting has not only enhanced the precision and efficiency of {}'s manufacturing processes but has also improved their overall customer experience. With the ability to easily customize designs and quickly produce prototypes, the company has been able to accommodate unique customer requests and deliver innovative solutions.Moreover, {}'s commitment to sustainable practices is further reinforced by laser cut cutting. As a non-contact process, laser cutting generates minimal waste and uses significantly less energy compared to traditional methods. This reduction in material waste and energy consumption aligns with the company's mission to minimize its environmental footprint and promote sustainability within the industry.Looking ahead, laser cut cutting is poised to continue shaping the future of manufacturing. As technology advances and becomes more accessible, more industries will adopt laser cutting techniques to streamline their production processes and remain competitive in the global market.In conclusion, laser cut cutting has revolutionized manufacturing by offering precision, efficiency, versatility, and customization. Companies like {} have embraced this technology, leveraging its advantages to deliver high-quality products and enhance customer satisfaction. With its endless possibilities and continual advancements, laser cut cutting is undeniably the future of manufacturing.
Expert Die Cutting Services Available in Your Local Area - Get Matched with Top Engineers
Die cutting is an essential process in the manufacturing of various products across different industries. It allows mass production of items with precision and efficiency. Die cutting can be done using different methods, including laser die cutting, which offers high accuracy and speed.Laser die cutting services involve the use of a laser beam to cut materials with precision. The process involves creating a 2D computer-aided design (CAD) file of the desired shape or pattern to be cut on the material. The CAD file is then loaded on a computer program that communicates with the laser die cutting machine.The laser beam is directed onto the material, creating a high-intensity heat spot that melts or vaporizes the material at the cutting line. The laser cuts the material along the programmed cutting path, resulting in perfect and precise cuts without any physical contact from the cutting tool.Laser die cutting services are suitable for cutting various materials, including plastics, textiles, paper, wood, rubber, and metals. Laser die cutting is highly precise, and the cuts are burr-free, making it ideal for cutting intricate designs. Additionally, the process is fast, efficient, and cost-effective, making it a preferred method for mass production.Laser die cutting services have various advantages, including:1. Precision: Laser die cutting offers high accuracy, resulting in perfect cuts, even for complex designs.2. Flexibility: The laser cutting technology can cut different materials with varying thicknesses and shapes, making it a versatile option for many industries.3. Speed: Laser cutting services are highly efficient and can offer faster cutting speeds than traditional die cutting methods.4. Automation: The entire laser die cutting process can be automated, reducing the need for manual intervention and minimizing the risk of human error.5. Cost-effective: Laser cutting services offer excellent value for money, especially in mass production, where the process is repeatable and consistent.When looking for laser cutting services, it is crucial to consider various factors, including the quality of the equipment, the experience of the service provider, and the cost. Additionally, it is essential to choose a service provider that can handle your order volume and delivery timelines.In conclusion, laser die cutting services offer a precise and efficient method of cutting materials for various industries. The process is fast, versatile, and cost-effective, making it a preferred option for mass production. When looking for laser cutting services, ensure you partner with a reputable service provider that can deliver quality work within the set timelines.
How to Weld Stainless Steel to Mild Steel: A Comprehensive Guide
Headline: Welding Stainless Steel to Mild Steel: An Innovative Solution by {Company Name}Introduction:{Company Name}, a leading expert in metal fabrication and engineering solutions, has introduced a groundbreaking technique for welding stainless steel to mild steel. With their extensive experience and commitment to innovation, the company has successfully developed a solution that addresses the challenges associated with joining dissimilar metals.Body:1. Understanding the Need for Welding Stainless Steel to Mild Steel: Welding stainless steel to mild steel has been a significant challenge in various industries such as automotive, construction, and manufacturing. Both stainless steel and mild steel offer unique attributes and advantages, but their dissimilarities in terms of composition and physical properties make joining them a complex task. However, the combination of these two metals is often desirable to strike a balance between strength, corrosion resistance, and cost-effectiveness.2. The Innovative Solution: {Company Name} has invested substantial resources in research and development to devise an effective technique for welding stainless steel to mild steel. This pioneering approach involves using advanced filler metals and welding processes that ensure a robust and durable bond between the dissimilar materials.3. Comprehensive Material Analysis: Before combining stainless steel and mild steel, {Company Name} conducts a detailed analysis of both metals to determine the most suitable welding method. Factors such as composition, mechanical properties, and intended application are thoroughly assessed to optimize the welding process.4. Advanced Filler Metals: One of the key elements in successfully welding stainless steel to mild steel is the selection of appropriate filler metals. {Company Name} utilizes state-of-the-art filler metals that have been specifically designed for joining dissimilar metals. These specialized fillers possess excellent wetting and spreading characteristics, ensuring a strong bond and minimizing the risk of material failure.5. Tailored Welding Processes: {Company Name}'s team of skilled welders utilizes tailored welding processes to ensure optimal results when combining stainless steel and mild steel. Whether it be TIG (Tungsten Inert Gas) welding, MIG (Metal Inert Gas) welding, or other advanced techniques, the company's experts possess the expertise to choose the most suitable method for each unique welding project.6. Quality Control: {Company Name} is committed to delivering exceptional quality in every welding project. Stringent quality control measures are implemented throughout the welding process, including thorough inspections, non-destructive testing, and adherence to internationally recognized standards. This ensures that the welded stainless steel to mild steel joints meet or exceed industry requirements.7. Advantages and Applications: The innovative welding solution offered by {Company Name} presents numerous advantages to industries requiring the combination of stainless steel and mild steel. These advantages include enhanced strength, improved corrosion resistance, cost-effectiveness, and greater design flexibility. Such benefits make this technique ideal for applications in automotive manufacturing, construction, shipbuilding, and various other sectors.Conclusion:{Company Name}'s groundbreaking technique for welding stainless steel to mild steel opens a new realm of possibilities for industries seeking to combine the advantages of these two dissimilar metals. With their expertise, advanced filler metals, and tailored welding processes, the company ensures robust bonds, exceptional quality, and unmatched customer satisfaction. This innovative solution serves as a testament to {Company Name}'s commitment to pushing the boundaries of metal fabrication and engineering.
Top Tips for Architectural Sheet Metal Fabrication
Architectural Sheet Metal Fabrication Company Introduces Innovative Solutions for Modern Buildings[City, Date] – As the demand for innovative and sustainable building designs continues to rise, Architectural Sheet Metal Fabrication company, established in [year], has emerged as a leading provider of custom metal products for the modern construction industry. With a keen focus on design, efficiency, and durability, the company has gained a reputation for delivering high-quality solutions that enhance the aesthetics and functionality of contemporary buildings.Architectural Sheet Metal Fabrication prides itself on being at the forefront of the architectural industry, constantly pushing boundaries and exploring new possibilities. By leveraging their extensive expertise and state-of-the-art facilities, the company has successfully completed numerous projects, ranging from commercial skyscrapers to residential complexes and cultural institutions.One of the core strengths of Architectural Sheet Metal Fabrication lies in their ability to create bespoke metal products that meet the unique requirements of each project. The company possesses an in-house design team consisting of highly skilled architects, engineers, and metal fabricators who work closely with clients to understand their vision and translate it into reality. Using advanced computer-aided design (CAD) software, they can visualize the final product and ensure that it perfectly aligns with the client's specifications.In addition to their cutting-edge design capabilities, the company utilizes the latest fabrication techniques and equipment to transform raw metal materials into exquisite architectural elements. Their state-of-the-art facility is equipped with advanced machinery, including laser cutters, CNC routers, and robotic welding systems, enabling precise and efficient production. This ensures that each component is manufactured to the highest standards, surpassing industry expectations in terms of quality and durability.Architectural Sheet Metal Fabrication's commitment to sustainability is another aspect that sets them apart. Recognizing the importance of environmentally conscious construction practices, the company employs eco-friendly materials and energy-efficient processes throughout their operations. By using recycled metals and implementing sustainable manufacturing techniques, they contribute to the reduction of carbon emissions and the preservation of natural resources. This dedication to sustainability has earned them several accolades and certifications, solidifying their position as a responsible and forward-thinking industry leader.Moreover, Architectural Sheet Metal Fabrication continually strives to stay updated with the latest industry trends and technologies. They actively invest in research and development to introduce innovative solutions that cater to the evolving needs of architects and contractors. By staying at the forefront of technological advancements, the company has successfully executed complex projects that demand intricate metalwork and sophisticated designs.Furthermore, Architectural Sheet Metal Fabrication maintains strong partnerships with renowned architects, contractors, and developers, promoting collaboration and fostering a creative environment. By working closely with industry professionals, they are able to leverage their combined expertise to tackle the most challenging projects. This collaborative approach also ensures that the final product not only meets the client's vision but also exceeds their expectations, resulting in superior architectural metal solutions.Today, Architectural Sheet Metal Fabrication stands as a trusted brand in the architectural community, renowned for its dedication to quality, innovation, and sustainability. Their portfolio of successful projects continues to grow, showcasing their ability to deliver on even the most ambitious and complex design concepts.As the architectural industry continues to evolve, Architectural Sheet Metal Fabrication remains committed to providing cutting-edge metal solutions that redefine the possibilities of contemporary building designs. With their expertise, technological prowess, and commitment to sustainability, the company is poised to make a lasting impact on the architectural landscape.
Demand for High-Quality Elbow Fittings Increases in Construction Industry
In the world of plumbing and construction, stainless steel is an essential material that has earned its reputation for its durability, strength, and resistance to corrosion. One of the primary components of plumbing systems that use stainless steel pipes is the stainless steel elbow, which is indispensable in redirecting the flow of fluids through the system.One of the leading manufacturers of stainless steel elbows in the industry is [Company name], a company that has cemented its place as a reliable and innovative manufacturer of plumbing fittings. The company has been in operation for over {number of years} years and has earned a reputation for maintaining the highest standards of quality in all its products.[Company name] manufactures various types of stainless steel elbows that are designed, developed, and manufactured to meet the diverse needs of the plumbing and construction industries. The company uses state-of-the-art technology, coupled with high-quality raw materials, to create durable and functional stainless steel elbows that are ideal for a wide range of applications.One of the standout features of [Company name]'s stainless steel elbows is their ability to withstand high-pressure environments. This is because the company uses high-grade stainless steel that has been engineered to maintain its structural integrity even under intense pressure. As a result, their products are ideal for use in systems that deal with corrosive fluids, high-temperature environments, and other challenging conditions.Additionally, [Company name]'s stainless steel elbows exhibit excellent resistance to a wide range of chemicals, ensuring that they can be used in an array of plumbing applications. This feature makes their products a popular choice for use in industries such as pharmaceuticals, food and beverage, and chemical production, among others.[Company name]'s team of skilled and experienced professionals is committed to ensuring that their products meet the highest standards of quality and safety. The company adheres to stringent quality control measures, from sourcing raw materials to the finished product's final inspection, to ensure that their stainless steel elbows are of the highest quality possible.The company's customer-centric approach has earned them a loyal customer base, with clients singling out their exceptional customer service experience. [Company name] provides comprehensive support to its customers, from initial product recommendations to after-sales support.In summary, [Company name] is a leading manufacturer of high-quality stainless steel elbows that are engineered to meet the highest standards of quality, durability, and functionality. Their products are ideal for use in a wide range of plumbing applications and are designed to withstand harsh environments, high-pressure systems, and corrosive fluids. By maintaining excellent customer service standards, [Company name] has earned its place as a trusted and reliable plumbing fittings manufacturer in the industry.
Watch the Best Sheet Metal Fabrication Videos Online
Title: Unveiling the Craft: Exploring the World of Metal FabricationIntroduction (Approximately 100 words):Metal fabrication, an essential manufacturing process that shapes raw metal sheets into intricate and functional structures, plays a vital role in various industries. From automotive parts to machinery components, the applications of metal fabrication are boundless. In this blog post, we delve into the intriguing world of metal fabrication, shedding light on the processes, techniques, and advantages that make it an indispensable aspect of modern manufacturing. Join us as we unravel the secrets behind the creation of awe-inspiring metal structures and explore the possibilities offered by a reliable Metal Fabrication Factory.1. The Art of Sheet Metal Fabrication (Approximately 200 words):Sheet metal fabrication, also known as metalworking, is a highly intricate process that involves converting raw metal sheets into products of various shapes and sizes. Through a combination of cutting, bending, and shaping techniques, skilled fabricators transform plain metal sheets into detailed structures that serve a multitude of purposes.At a Metal Fabrication Factory, advanced machinery and equipment are utilized to achieve precise results while ensuring efficiency. CNC laser cutting machines, for instance, provide accurate and consistent cuts, while hydraulic presses enable intricate bending and forming of metals. Welding and surface finishing processes are also essential to enhance the aesthetic appeal and durability of the fabricated metal structures.2. Industries Served by Metal Fabrication (Approximately 200 words):Metal fabrication caters to an extensive range of industries and sectors. From construction and architecture to transportation and manufacturing, the applications are limitless. For example, in the construction industry, architectural metalwork such as staircases, handrails, and structural components are fabricated to ensure functionality, strength, and aesthetic appeal.The automotive industry heavily relies on metal fabrication to manufacture critical components like chassis, exhaust systems, and suspension parts. Metal fabrication is also crucial in the production of electrical enclosures, HVAC systems, and machinery components that are utilized in various manufacturing plants.3. The Advantages of Metal Fabrication (Approximately 200 words):Metal fabrication offers numerous advantages that make it the go-to manufacturing process for countless industries. First and foremost is the versatility it provides. Metal can be shaped into intricate designs and structures, making it suitable for both functional and aesthetic purposes. Additionally, metals are inherently strong and durable, ensuring the longevity of fabricated products.Moreover, metal fabrication allows for quick prototyping and customization. By utilizing computer-aided design (CAD) software, fabricators can create detailed digital designs, optimize them for precision, and then produce multiple replicas with ease.Furthermore, metal fabrication is a cost-effective solution as it eliminates the need for intricate assembly processes that add to the overall expenses. By integrating multiple manufacturing steps into one streamlined process, metal fabrication increases efficiency and reduces production time.4. Choosing a Metal Fabrication Factory (Approximately 200 words):When selecting a metal fabrication factory, various factors must be considered to ensure high-quality results. Look for a facility equipped with state-of-the-art machinery and cutting-edge technology that can meet your specific project requirements. Cross-check the factory's capabilities, such as laser cutting, bending, welding, and finishing, to ensure they align with your needs.Certifications and industry credentials are also important indicators of the fabricator's reliability and expertise. Prioritize a factory that adheres to international standards to guarantee exceptional quality and compliance with regulatory norms.Additionally, consider the factory's experience in your specific industry. A well-established fabricator with a portfolio of successful projects in your desired sector is more likely to understand the unique challenges and deliver tailored solutions.Conclusion (Approximately 100 words):Metal fabrication remains an essential pillar of modern manufacturing, enabling the creation of intricate and durable structures in diverse industries. The artistry and skill behind metal fabrication, combined with advanced machinery and technology, make it a captivating subject to explore. By partnering with a trustworthy Metal Fabrication Factory, businesses can unlock the potential of this versatile process, leveraging its advantages to bring their innovative ideas to life. So, whether you require custom architectural metalwork or need precise automotive components, metal fabrication is the key to turning your visions into reality.
Custom Stainless Steel Sheet Metal Fabrication Services for Non-Standard Brackets: Laser Cutting, Forming, Stamping, Bending, Punching, and Welding
Laser Cutting and Sheet Metal Forming of Stainless Steel Sheets: Custom Processing of Non-Standard Stainless Steel BracketsStainless steel is a popular material used in a wide range of industries, including construction, automotive, and kitchenware. It is known for its durability, resistance to corrosion, and high aesthetic appeal. However, working with stainless steel can be a challenge. Its strength and hardness make it difficult to cut, bend, and shape, requiring specialized machinery and skilled technicians.To meet the growing demand for custom stainless steel products, (company name) offers a range of sheet metal forming services, including laser cutting, stamping, bending, punching, and welding. As a leader in the industry, we have the experience and expertise to handle complex projects and meet the high standards of our clients.One of our specialties is custom processing of non-standard stainless steel brackets. Many industries require brackets with unique shapes and sizes to fit their specific applications. Our team of engineers and technicians work closely with clients to design and produce brackets that meet their exact specifications. We use advanced software and equipment to ensure accuracy and precision in every step of the process. Our laser cutting machines can cut stainless steel sheets up to 6mm thick with a maximum sheet size of 3000x1500mm.We also offer a range of sheet metal forming services to complement our laser cutting capabilities. Our stamping presses range from 5 to 200 tons, allowing us to produce parts with varying thicknesses and complexities. Our CNC bending machines can bend stainless steel sheets up to 4mm thick and 3000mm long. We use state-of-the-art punching machines and welding robots to ensure fast and efficient production.At (company name), we are committed to providing high-quality stainless steel products that meet the needs of our clients. We understand that every project is unique and have the expertise to handle any challenge. Whether you need a single custom bracket or a large-scale production run, we have the capabilities and resources to meet your requirements.About (company name):Founded in (year), (company name) is a leading provider of custom sheet metal fabrication services. We specialize in processing stainless steel, aluminum, and other metals for a wide range of industries, including construction, automotive, and electronics. We have a state-of-the-art factory with advanced equipment and a team of skilled technicians. Our mission is to provide high-quality products and exceptional customer service at competitive prices.
Discover the Key Processes Involved in Sheet Metal Fabrication at a Leading Factory
On a bustling industrial estate in the heartland of American manufacturing, the Sheet Metal Fabrication Factory (name removed for anonymity) is a hive of activity. The factory is a testament to the ingenuity and enterprise of the American people, as it produces a range of high-quality metal parts and components that are in demand across many different industries.The Sheet Metal Fabrication Factory specializes in producing customized metal products and parts, meaning that it is well-equipped to handle any project that requires precision, durability, and versatility. The factory's team of highly-skilled technicians and engineers work in tandem to produce metal parts and components that are bespoke to the client's needs. With cutting-edge technology and machinery, the factory is able to turn raw materials into high-quality metal products that are designed to withstand the toughest environments.The factory has earned a reputation for excellence in the industry, due in part to its commitment to providing exceptional customer service. The Sheet Metal Fabrication Factory works closely with its clients to ensure that their needs are met, often going above and beyond to ensure that their expectations are exceeded. As a result, the company has earned a loyal customer base that spans many industries, including aerospace, automotive, defense, and medical.One of the most impressive things about the Sheet Metal Fabrication Factory is its in-house design and engineering team. The team is composed of highly-skilled professionals who work closely with clients to develop bespoke solutions that meet their unique requirements. Using state-of-the-art software and equipment, the team is able to produce 3D models of the product before it goes into production, allowing clients to preview the finished product before it is produced. This level of precision ensures that the finished product meets or exceeds the client's expectations.The factory's capabilities are equally impressive. Sheet metal is cut, punched, and folded with utmost precision, while welding, polishing, and finishing are carried out to the highest standards. The factory also offers a range of surface treatments and coatings, such as anodizing and powder coating, that can be customized to suit any need.In addition to its impressive production capabilities, the Sheet Metal Fabrication Factory is also committed to sustainability. The company sources its raw materials from ethical and sustainable sources whenever possible, and takes steps to minimize waste and energy consumption during the production process. This commitment to sustainability has earned the factory recognition from industry bodies and clients alike, and has helped to cement its position as one of the leading metal fabrication companies in the country.Overall, the Sheet Metal Fabrication Factory is an impressive and dynamic company that has proven itself to be a leader in its field. Boasting state-of-the-art technology, an exceptional staff, and a commitment to sustainability, this factory is uniquely equipped to deliver high-quality metal products and components that meet and exceed the needs of its clients. As American manufacturing continues to evolve and adapt to changing market conditions, the Sheet Metal Fabrication Factory will undoubtedly remain at the forefront of innovation and excellence.
Unveiling the Latest Innovations in Metal Fabrications: Stay Updated with the Latest Developments
All Metal Fabrications: Revolutionizing the Metal Manufacturing IndustryIn the dynamic world of metal manufacturing, where precision, efficiency, and innovation hold the key to success, one company has consistently been setting new benchmarks - All Metal Fabrications (AMF). For over two decades, AMF has been at the forefront of revolutionizing the industry with their state-of-the-art fabrication services and pioneering techniques.Founded in 1999, AMF quickly established itself as a trusted name in the metal fabrication sector. Headquartered in [Location], their mission has always been to provide unparalleled quality and customer satisfaction. With a diverse range of services, from prototype development to large-scale manufacturing, AMF caters to businesses across various industries, including automotive, aerospace, architecture, and construction.One of the hallmarks of AMF's success has been their relentless pursuit of innovation. With a team of highly skilled engineers and technicians, AMF consistently pushes the boundaries of what is possible in metal fabrication. By investing in advanced technology, such as computer-aided design and cutting-edge machinery, AMF ensures that their clients receive products of the highest caliber.By leveraging their expertise in sheet metal fabrication, AMF has developed a reputation for delivering precision-engineered components and assemblies. Whether it's intricate parts for the automotive sector or architectural elements that demand meticulous detailing, AMF's commitment to accuracy is second to none. Their ability to handle complex projects with utmost precision has earned them accolades from clients worldwide.AMF's dedication to quality has also resulted in various certifications and industry recognition. With ISO 9001 and AS 9100 certifications, the company follows international quality management standards, ensuring that each product meets the highest industry standards. Customers can rely on AMF's commitment to consistency, quality, and on-time delivery.Moreover, AMF prides itself on its ability to offer tailored solutions to meet individual customer needs. By collaborating closely with clients throughout the fabrication process, AMF ensures that every project is executed with precision and efficiency. From conceptualization to the final product, their team works meticulously, paying attention to every detail to provide a seamless experience for their clients.In addition to their core fabrication services, AMF also offers value-added services such as finishing, assembly, and packaging. By providing a comprehensive range of services under one roof, the company streamlines production processes, reduces lead times, and offers cost-effective solutions. This approach has made them a preferred partner for businesses looking for a one-stop solution for their metal fabrication requirements.While AMF's commitment to quality and innovation is evident in their current operations, they also have their sights set on the future. With an eye towards sustainability, AMF is continuously exploring ways to reduce their environmental impact. By incorporating green practices into their manufacturing processes and sourcing materials responsibly, AMF aims to contribute to a greener, more sustainable metal fabrication industry.As AMF continues to grow, they remain dedicated to their founding principles of excellence, integrity, and customer-centricity. With a stellar track record and a steadfast commitment to innovation, AMF is well positioned to lead the metal fabrication industry into a new era. With every fabrication project they undertake, AMF aims to redefine what is possible in this ever-evolving sector.In conclusion, All Metal Fabrications has emerged as a trailblazer in the metal fabrication industry, setting new standards of excellence through their commitment to innovation, precision, and customer satisfaction. With their cutting-edge technology, tailored solutions, and green initiatives, AMF continues to be at the forefront of revolutionizing the way metal is fabricated and manufactured.
Optimize Production Efficiency with Sheet Metal Laser Cutting Service
article:Sheet Metal Laser Cutting ServiceSheet Metal Laser Cutting Service, the latest addition to the manufacturing industry, has drastically revolutionized the way metal products are fabricated, and it has become one of the most preferred and reliable methods for cutting and shaping metal. With the advancement in technology, laser cutting has become an affordable and efficient way for businesses to cut and shape their products. The process involves directing a concentrated beam of light at a metal surface, melting or vaporizing the material and leaving a precise, clean cut.The laser cutting technology has been in use since the 1970s, but the process has only recently gained popularity in the manufacturing industry. Prior to this, traditional methods such as sawing, drilling, and punching were used to cut and shape metal. However, these methods caused a lot of wear and tear on the material, leaving rough edges and requiring more finishing work after the cut. Laser cutting has revolutionized the industry by providing businesses with a precision cutting and shaping technique.Sheet Metal Laser Cutting Service is a company that has taken this technology to the next level, with its years of experience and a team of skilled professionals. The company is located in an industrial park in a metropolitan city, equipped with modern, state-of-the-art facilities that allow them to execute orders accurately and efficiently. Sheet Metal Laser Cutting Service takes pride in delivering high-quality metal fabrication services, and they have been successful in providing reliability and affordability to their clients.Sheet Metal Laser Cutting Service offers a wide range of services, including laser cutting of various metals such as aluminum, steel, and stainless steel. The company specializes in customized designs and shapes, and their laser-cut metal products range from metals for transportation, agricultural parts, electronic enclosures, to decorative accents, and customized parts. The precision of the laser cutting process enables the company to produce intricate shapes and designs that are difficult to achieve with traditional manufacturing techniques. They have a team of skilled designers and engineers who work closely with their clients, ensuring that their clients receive the perfect metal product they require.Moreover, Sheet Metal Laser Cutting Service uses the latest technology and equipment to ensure that their clients receive top-notch quality metal products. They have high-powered lasers that are capable of cutting metals of up to 1-inch thickness. The company also has a variety of software programs that enable them to customize and optimize cutting designs, resulting in minimal wastage of materials.The company has an elaborate quality assurance process that ensures they deliver high-quality metal products to their clients. They have strict quality standards in place, with every material goes through a rigorous inspection process to confirm that it meets the client's exact specifications. The company is also committed to ensuring that it delivers products within the specified timeline, and they have a fast turnaround time for orders, ensuring that their clients receive their products promptly.With the commitment to delivering high-quality metal products, reliability, and affordability, Sheet Metal Laser Cutting Service has become one of the preferred choices for businesses in various industries. They have a team of skilled professionals who work tirelessly to ensure the best services for their clients. The company has successfully maintained client satisfaction through the high quality of its metal products and prompt delivery services. In addition, Sheet Metal Laser Cutting Service has competitive pricing, ensuring that their services are affordable for all businesses.In conclusion, Sheet Metal Laser Cutting Service offers high-quality metal fabrication services that have revolutionized the manufacturing industry. With the latest technologies and equipment, the company has a competitive edge in the market and is renowned for timely delivery, reliability, and affordability. The company has set high standards in the industry and has established itself as a reliable service provider. It's an ideal place to seek out for all your metal fabrication requirements.