New technique for eco-friendly microstructure etching on complex-shaped components
By:Admin
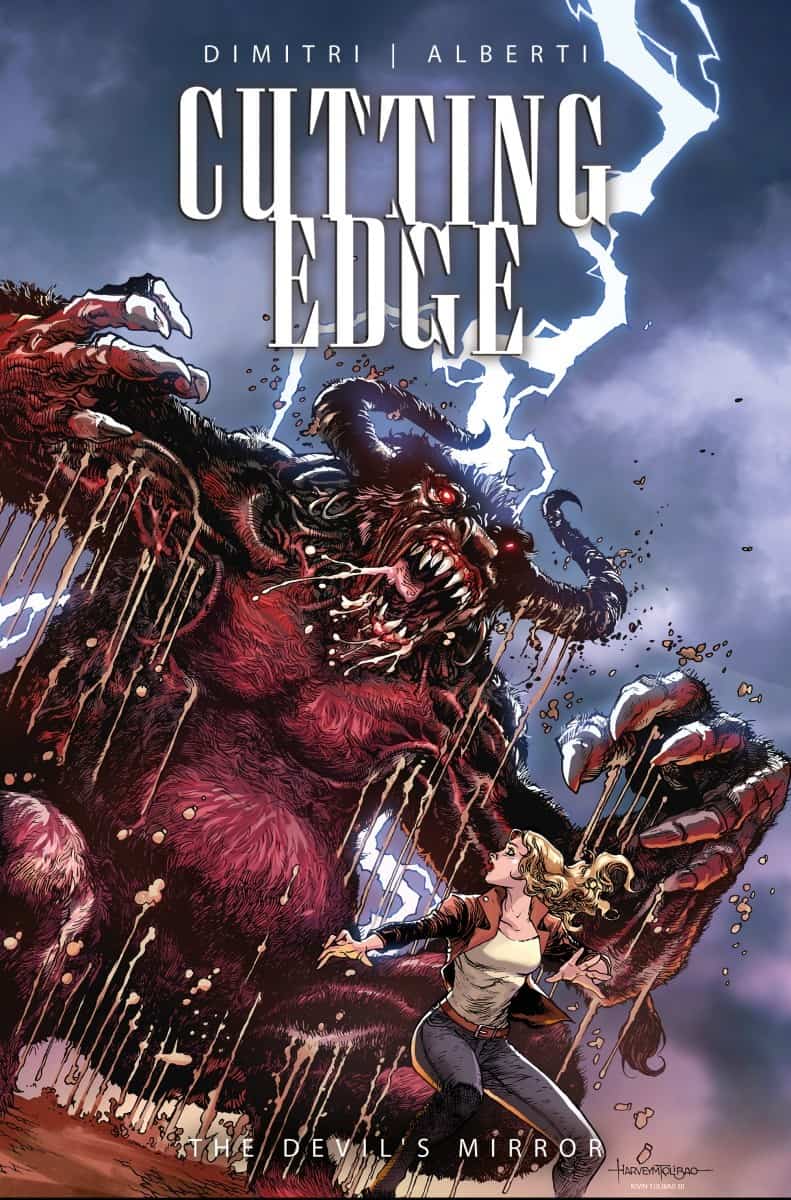
The development of a new laser cutting technique by German researchers promises to revolutionize the way we etch microstructures into complex-shaped surfaces. This new method is expected to be more environmentally friendly and efficient than traditional etching methods, which use chemicals to remove surface material.
The technique involves using a laser beam to burn micrometre-fine patterns into free-form surfaces, creating fine microstructures that were previously impossible to achieve with traditional etching methods. In addition to being more precise, this laser cutting technique is believed to be cheaper and more sustainable than its predecessors, making it a more accessible solution for a wider range of applications.
One area where this technique is expected to have a significant impact is in the development and production of prototypes. With the Prototype Laser Cutting Technique, it will be easier and more efficient to create fine microstructures on complex-shaped components, which are essential for prototyping. This is an important step in the development of products, as prototypes allow companies to test and refine their products before mass production.
The development of this laser cutting technique is a major step towards improving efficiency and sustainability in various industries. It has the potential to revolutionize the manufacturing process by making it more accessible and cost-effective. In addition to being used in prototyping, this technique will be useful for a variety of other applications, including the production of electronics, medical devices, and other precision components.
In conclusion, this new Prototype Laser Cutting Technique is a game-changer in the world of microstructure etching. It offers a more environmentally-friendly, efficient, and cost-effective solution than traditional etching methods. With potential applications in a wide range of industries, this laser cutting technique has the potential to revolutionize the way we create precision components and prototypes.
Company News & Blog
Professional Welding Services: MIG and TIG Welding for Aluminum and Steel - Hourly Rates Available
How to Spot Weld Galvanized Steel: A Comprehensive Guide
Spot Weld Galvanized Steel: A Breakthrough in Welding TechnologyIn recent years, advancements in manufacturing technology have brought about significant improvements in various industrial sectors. These improvements aim to enhance both the quality and efficiency of production processes. One such breakthrough has been achieved by a leading company in the industry, yet for confidentiality reasons, we will refer to it as Company X.Company X, a renowned player in the fabrication industry, has come up with an innovative solution to spot weld galvanized steel. This groundbreaking technology has the potential to revolutionize the welding industry and provide numerous benefits to businesses across various sectors.Spot welding, a widely used technique in the manufacturing sector, involves joining two metal surfaces together using heat and pressure. Galvanized steel, a material commonly used in the automotive and construction industries, poses unique challenges during spot welding due to its zinc coating. Traditionally, the zinc coating caused electrode degradation and created an inferior weld, resulting in compromised structural integrity.Recognizing the limitations of traditional spot welding techniques, Company X has developed an advanced method that overcomes these challenges. By leveraging their expertise in materials science and cutting-edge research, Company X has successfully engineered a solution to spot weld galvanized steel with exceptional precision and durability.The key behind this breakthrough lies in the development of a specialized welding electrode. This electrode is designed to withstand the adverse effects of the zinc coating, ensuring a reliable and robust weld every time. Additionally, Company X's innovative electrode design optimizes the distribution of heat and pressure, resulting in a stronger bond between the metal surfaces.This groundbreaking technology not only guarantees high-quality welds but also offers several other advantages. Firstly, it significantly reduces production costs by eliminating the need for extra surface preparation steps such as zinc coating removal. The new method also streamlines the manufacturing process by simplifying the spot welding operation, thereby increasing productivity.Moreover, the improved structural integrity achieved through this breakthrough welding technology ensures enhanced safety and durability in the finished products. Applications in the automotive and construction sectors are particularly promising, as the spot welding of galvanized steel is a common requirement in these industries.Company X's commitment to innovation and continuous improvement has been instrumental in their success. Their state-of-the-art research and development facilities enable them to stay at the forefront of technological advancements in the welding industry. By investing in cutting-edge equipment and collaborating with industry experts, Company X has solidified its position as a leading provider of spot welding solutions worldwide.With the introduction of this breakthrough technology, Company X intends to expand its market share and further strengthen its reputation as an industry frontrunner. By offering a superior alternative to traditional spot welding methods, Company X is poised to capture the attention of manufacturers seeking higher-quality and cost-effective welding solutions.Furthermore, the rapid adoption of this innovative welding technique has the potential to revolutionize the industry as a whole. Other manufacturers are likely to follow suit, enhancing the overall quality and efficiency of spot welding galvanized steel products globally.In conclusion, Company X's groundbreaking breakthrough in spot welding galvanized steel has paved the way for a new era in manufacturing. With their innovative electrode design and unparalleled expertise, they have successfully overcome the challenges posed by the zinc coating, revolutionizing the welding industry. The introduction of this technology promises increased productivity, reduced production costs, and enhanced product quality. As other manufacturers catch on to the advancements made by Company X, we can expect significant transformations in the way galvanized steel is spot welded, opening doors to a more reliable and efficient future.
Professional Tube Bending and Rolling Services for Various Materials
Aluminum Bending Services Meet Growing Demands for Customized FabricationIn response to the increasing demand for specialized fabrication solutions, industry-leading tube bending and rolling experts have expanded their services to include aluminum bending. As aluminum continues to gain popularity in a wide range of industries, these specialized services offer a cost-effective and efficient solution for creating custom-designed products and structures.MetzFab, a renowned provider of tube bending and rolling services, has recently expanded its capabilities to include aluminum bending. With their expertise and state-of-the-art equipment, MetzFab is now capable of working with a variety of materials, including steel, stainless steel, and aluminum.Aluminum has become a sought-after material for its exceptional versatility, strength, and lightweight properties. It is widely used across a range of industries, including aerospace, automotive, construction, and marine, to name just a few. By offering aluminum bending services, MetzFab is dedicated to meeting the ever-growing demands of these industries and providing them with customized fabrication solutions.MetzFab's aluminum bending services utilize advanced bending machinery and techniques to create precise and complex shapes. The company's skilled technicians are experienced in handling the unique properties of aluminum, ensuring high-quality results and minimizing material waste. Whether it's a simple bend or a complex multi-plane shape, MetzFab's aluminum bending services can meet the needs of any project.One of the key advantages of aluminum bending services is the cost-effectiveness it offers compared to traditional fabrication methods. With the ability to create intricate shapes and designs, aluminum bending reduces the need for additional parts and assembly, resulting in significant cost savings. Additionally, aluminum's lightweight nature reduces transportation costs and makes it easier to handle during installation.MetzFab's aluminum bending services also offer exceptional durability and corrosion resistance. Aluminum naturally forms a protective oxide layer, making it highly resistant to rust and corrosion. This makes it an ideal choice for outdoor applications and industries that require high strength and longevity. With their precise bending techniques, the company ensures that the integrity of the aluminum is maintained, providing customers with long-lasting and reliable products.The versatility of aluminum bending extends to a wide range of applications. In the aerospace industry, aluminum's lightweight properties are crucial for reducing fuel consumption and increasing aircraft efficiency. MetzFab's aluminum bending services can create intricate shapes for aircraft frames, fuselages, and other components, ensuring optimal performance and safety.In the automotive sector, aluminum bending enables the production of lightweight and fuel-efficient vehicles. By reducing the weight of car bodies and structures, manufacturers can improve fuel economy without compromising safety. MetzFab's aluminum bending services can contribute to this industry's goal of sustainability and environmental responsibility.In the construction and architectural industries, aluminum bending allows for the creation of unique and aesthetically pleasing structures. From curved facades to custom-designed staircases, aluminum bending provides architects and designers with unparalleled creative possibilities. MetzFab's expertise in aluminum bending ensures that these structures are not only visually appealing but also structurally sound.MetzFab's expansion into aluminum bending services highlights their commitment to meeting the changing needs of various industries. With their expertise, state-of-the-art equipment, and dedication to quality, they are well-positioned to provide customized fabrication solutions that meet and exceed customer expectations. Whether it's steel, stainless steel, or aluminum, MetzFab's tube bending and rolling services are a reliable choice for all materials.
Techniques for Welding Thin Sheets of Stainless Steel
Welding Thin Stainless Steel: Tips and Tricks for Perfect WeldsStainless steel is a popular choice of material for many applications due to its corrosion resistance, durability, and aesthetic appeal. However, welding thin sheets of stainless steel can be a challenging task, requiring careful preparation, skill, and the right equipment. In this blog post, we will provide some tips and tricks for welding thin stainless steel, including the use of advanced welding techniques and tools to achieve the perfect weld.PreparationBefore you begin welding thin stainless steel sheets, it is essential to prepare the workpiece properly. First, ensure that the surfaces to be welded are clean and free of any contaminants that may affect the quality of the weld. Use a degreaser or solvent to remove any oil, dirt, grease or oxide layers that may be present on the surface. You can also use a wire brush or grinder to remove the oxide layer and create a clean surface for welding.Next, ensure that the edges of the workpieces are aligned properly, with an even gap of around 1-2mm between them. A precise fit is essential for achieving a good weld, so take the time to check and recheck the alignment before beginning the welding process.TechniquesSeveral advanced welding techniques can be used to weld thin sheets of stainless steel, including TIG (Tungsten Inert Gas) welding and laser welding. TIG welding is a popular choice for welding thin stainless steel sheets because it offers precise control over the welding process, a high-quality finish, and the ability to weld various types of stainless steel.With TIG welding, the torch is held by the welder, and the other line feeds behind the weld using parts of pie plates and other forms of bendy stuff to dam the argon behind the weld. This technique ensures that the weld is protected by an argon gas shield, preventing the weld from being contaminated by oxygen and other atmospheric gases.Another option for welding thin stainless steel is laser welding. Laser welding uses a high-energy laser beam to join the workpieces, resulting in a precise, high-quality weld. Laser welding is particularly useful for welding complex shapes and contours, and it is ideal for welding thin sheets of stainless steel, where precision is essential.ToolsTo achieve the perfect weld on thin stainless steel, it is essential to have the right tools. Some of the key tools you will need for welding thin sheets of stainless steel include a TIG welding machine, a suitable electrode, filler wire, and an argon gas cylinder.A high-quality TIG welding machine is essential for achieving precise control over the welding process, enabling you to adjust the weld speed, current, and voltage for optimal results. The right electrode and filler wire are also critical, as they dictate the quality and strength of the weld.ConclusionWelding thin sheets of stainless steel requires careful preparation, skill, and the right equipment. By following the tips and tricks outlined in this blog post, including proper preparation, advanced welding techniques, and the use of quality tools, you can achieve perfect welds every time. Whether you choose TIG welding or laser welding, remember to take your time, stay focused, and enjoy the impressive results that you can achieve with thin steel.
Top Steel Fabrication Ideas on Pinterest: Get Inspired!
Steel fabrication is a crucial process in the construction industry that involves the creation of steel structures from raw materials. The process incorporates a range of techniques, including cutting, bending, welding, and assembling, to create everything from simple structures to complex designs. Steel fabrication is vital in the construction of buildings, bridges, and vehicles, and it is an essential aspect of modern construction.Steel fabrication has been in use for centuries and is a trusted and durable material for accomplishing a range of construction jobs. With advancements in technology, today's steel fabricators can produce intricate designs with precision. The use of sophisticated equipment, such as computer-aided design and drafting software, has been instrumental in improving the accuracy of steel fabrication. Steel fabrication has evolved over the years, and the process has become faster, more efficient, and cost-effective.Today, steel fabrication is done in various ways, depending on the application. It can be done through manual techniques that rely on the skill of the fabricator or through automated processes that use machines. Both techniques have their advantages, and it is up to the fabricator to determine which method is best for their project.The steel fabrication process involves several stages, starting with the design process. During the design phase, the fabricator creates the blueprints and determines the materials needed for the job, including the type of steel, the thickness, and the shape. The designer takes into account the project's requirements and considers the scope of the work to ensure that the steel structures meet the specifications.Next comes the cutting stage, where the steel is cut according to the specifications outlined in the blueprint. Different methods are used to cut steel, including plasma, laser, and waterjet cutting. Once the steel is cut, it is then prepared for bending and shaping.The bending stage is crucial as it determines the shape of the steel structure. The fabricator uses a hydraulic press brake to bend the steel pieces to the required angle. Once the steel is bent and shaped, it is then assembled and welded together.Welding is an essential process in steel fabrication as it joins the steel sections together, creating a sturdy and durable structure. The fabricator uses different types of welding techniques, including MIG, TIG, and Stick welding, to create high-quality welds. The welding process can also involve surface preparation, such as cleaning and sandblasting, to ensure optimal welding conditions.The final stage of steel fabrication involves finishing touches. This includes painting, polishing, or galvanizing the steel structures to protect them from rust and corrosion.In conclusion, steel fabrication is a crucial process in the construction industry that involves creating steel structures from raw materials. The process involves several stages, including design, cutting, bending, welding, and assembly, and requires a high level of skill and precision. With advancements in technology, steel fabrication has become faster, more efficient, and cost-effective, making it an essential aspect of modern construction. Steel fabrication is a durable and trusted material for accomplishing a range of construction jobs and is essential for the construction of buildings, bridges, and vehicles. If you are looking for a reputable steel fabrication company, it is important to do your research and find one that has the expertise, experience, and equipment needed to complete your project to your specifications. Make sure to choose a company that uses high-quality materials, has skilled professionals, and has a proven track record of successfully completed projects.
Sheet Metal Fabrication Services in the USA at Competitive Prices
Sheet Metal Fabrication Shop: Providing Quality Sheets for Your Manufacturing NeedsIn today's manufacturing industry, sheet metal fabrication is an integral part of producing finished products. From appliances, automotive parts, to custom enclosures, sheet metal is the backbone of every product that requires strength, durability, and precision.To meet the demands of this competitive market, industries turn to sheet metal fabrication shops to provide high-quality sheets and services. These shops specialize in the production, designing, and finishing of sheet metal products that meet the unique requirements of every client.Sheet metal fabrication shops play a crucial role in the manufacturing industry. Here's why:Fabrication CapabilitiesSheet metal fabrication shops have advanced technology and a team of skilled professionals that can handle even the most complex sheet metal projects. They use computer-aided design (CAD) and computer-aided manufacturing (CAM) to create precise and accurate designs that can be easily edited and modified. With their cutting-edge machines and techniques, they can create any shape, size, or design you require.High-Volume Precision ServicesSheet metal fabrication shops pride themselves on providing high-volume precision services. They ensure that every piece of sheet metal they produce meets the exact specifications set by the client. They use a variety of tools and techniques, such as CNC machining, stamping, laser cutting, and welding, to produce sheet metal products that are durable, safe, and meet all industry standards.Fast Delivery OptionsThe fast-paced manufacturing industry demands quick turnaround times. Sheet metal fabrication shops understand the importance of delivering finished products on time, every time. They prioritize meeting deadlines and have streamlined processes to ensure that each project is delivered promptly without compromising quality.Competitive PricingSheet metal fabrication shops offer competitive pricing for their products and services. With their advanced technology and streamlined processes, they can provide cost-effective solutions to meet every client's needs while maintaining the highest quality standards.In conclusion, sheet metal fabrication shops play an essential role in the manufacturing industry. They take pride in providing high-quality sheet metal products that meet the specific needs of their clients. They have the experience, expertise, and technology to handle any sheet metal project, big or small, and deliver it on time and within budget with competitive pricing. If you require sheet metal products, turn to a reputable sheet metal fabrication shop to ensure that your products are safe, durable, and of the highest quality.
Highly Efficient Precision Laser Cutter for Metals: Cut Steel, Aluminum, Copper, and Titanium With Ease Using Advanced Fiber Laser Technology - Mechanical Kingdom
Precision Laser Cutting: Unlocking New Possibilities with SS Laser CuttingWhen it comes to precision cutting, Ss stainless steel is one of the most challenging materials to work with. But with the rise of advanced laser cutting technology, what was once considered difficult has now become achievable with ease. One such technology is the Fy4050b Precision Laser Cutter from Feiyue Laser.The Fy4050b Precision Laser Cutter is a top-of-the-line CNC cutting machine that can handle a variety of materials, including stainless steel plates, aluminum, copper, titanium sheets, and jewelry metal. What sets this machine apart is its fixed optical path design, which provides a maintenance-free optical path and low operating cost while delivering high processing efficiency and cutting quality. Equipped with an international advanced fiber laser, the Fy4050b machine is capable of cutting through thick metal sheets with precision and accuracy, providing you with clean and smooth edges that require minimal post-processing. This makes it ideal for a range of applications, from industrial to jewelry making.The cutting head of the Fy4050b machine uses the LASERMECH optical fiber cutting head imported from the United States. It's also fitted with a capacitive sensor, which provides high sensing accuracy, sensitive response, and stable and reliable performance. This means you get a quality cut every time, regardless of the shape or size of the material.The CNC system of the Fy4050b machine is specially designed for laser cutting. It uses an imported non-contact height tracking system that's sensitive and accurate, and is not affected by the shape of the material. This helps to eliminate potential errors during the cutting process, ensuring that you get precise and clean cuts every time. Overall, the Fy4050b Precision Laser Cutter is a valuable investment for anyone looking to get into laser cutting. It's affordable, versatile, and reliable, making it a great choice for businesses and hobbyists alike. With its exceptional cutting quality and high processing efficiency, this machine is sure to unlock new possibilities in your metal cutting projects.In conclusion, choosing the right laser cutter is crucial, especially when it comes to working with tough materials like Ss stainless steel. With the Fy4050b Precision Laser Cutter from Feiyue Laser, you're assured of a quality machine that can handle all your metal cutting needs with ease, precision, and efficiency. This cutting-edge technology is transforming the metal-cutting industry, making it easier and more affordable to achieve precision cuts than ever before. So, invest in the Fy4050b Precision Laser Cutter today and take your metal cutting projects to a whole new level!
How Laser Cutting is Revolutionizing Manufacturing Processes
Laser Plate Cutting: The Future of Precision ManufacturingIn our increasingly tech-savvy world, precision and accuracy have become more important than ever before. As such, precision manufacturing has taken center stage, with companies constantly seeking new and innovative ways to create perfect, intricate, and detailed products. One such innovation is laser plate cutting, a process that uses lasers to make precise cuts in a variety of materials. In this blog, we'll dive into the world of laser plate cutting and explore why it's the future of precision manufacturing.What is Laser Plate Cutting?Laser plate cutting is a process that uses a high-powered laser to cut through a variety of materials, including steel, aluminum, and other metals. The laser beam is directed at the material, creating a highly focused point of heat that melts or vaporizes the material in a precise and controlled manner. This process results in clean, sharp, and accurate cuts that are free of burrs or other imperfections.How Does Laser Plate Cutting Work?To understand how laser plate cutting works, it's helpful to understand how a laser works in the first place. A laser (which stands for Light Amplification by Stimulated Emission of Radiation) emits a highly concentrated beam of light that is focused on a small area. This beam is made up of photons, which are particles of light. When the photons hit a material, they transfer energy to it, causing it to heat up and melt or vaporize.In laser plate cutting, the laser beam is directed onto a plate of material using a series of mirrors and lenses. The laser can be adjusted to various settings, including power and speed, to ensure the most precise cut possible. The process can be automated using computer-controlled systems, which allows for even greater precision and speed.Benefits of Laser Plate CuttingSo why is laser plate cutting the future of precision manufacturing? There are several key benefits to the process that set it apart from other types of cutting:1. Precision and accuracy: Laser plate cutting allows for incredibly precise cuts that are free of burrs or other imperfections.2. Speed: Laser cutting is faster than many other cutting methods, which means that products can be created more quickly.3. Versatility: Laser cutting can be used on a wide range of materials, including metals, plastics, and even glass.4. Cost-effectiveness: Although laser plate cutting requires expensive equipment, it can ultimately save money in the long run by reducing waste and the need for additional finishing processes.Applications of Laser Plate CuttingLaser plate cutting has a wide range of applications across many industries. Here are just a few examples:1. Aerospace: Laser cutting is used to create precise components for aircraft engines, landing gear, and other systems.2. Automotive: Laser cutting is used to create parts for cars and trucks, including body panels, suspension components, and exhaust systems.3. Medical: Laser cutting is used to create surgical tools, implants, and other medical equipment that requires precision and accuracy.4. Technology: Laser cutting is used to create components for consumer electronics, such as smartphones and tablets.ConclusionIn conclusion, laser plate cutting is the future of precision manufacturing. With its ability to create precise, accurate cuts on a wide range of materials, laser cutting has become an essential tool for many industries. As technology continues to advance, we can expect to see even greater innovations in laser cutting, making it an even more important part of the manufacturing process. So if you're looking for the most precise and accurate cuts for your next project, consider laser plate cutting.