Quality Metal Forming Services for Your Business Needs
By:Admin
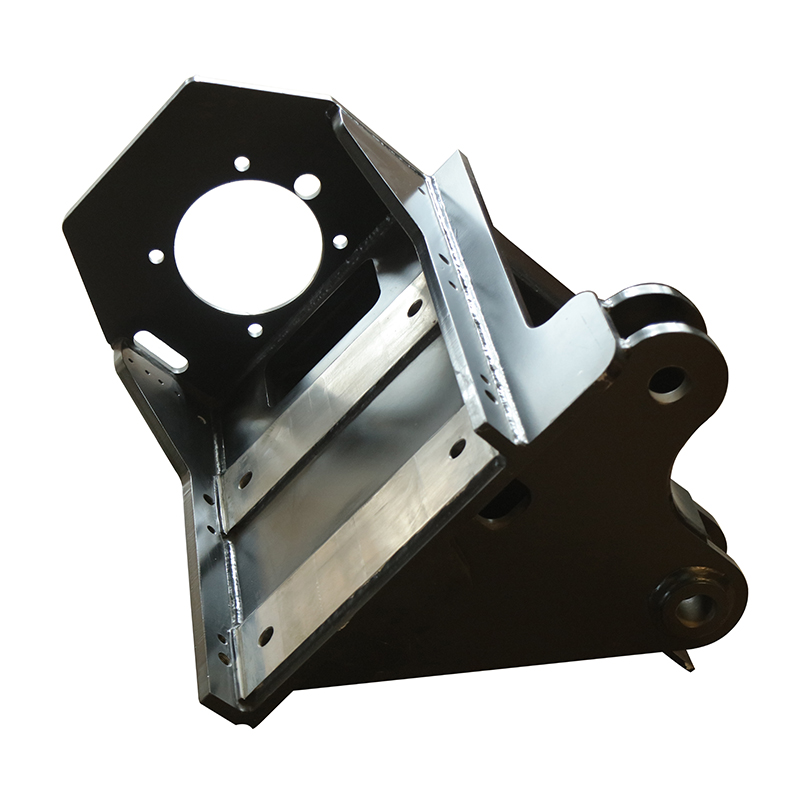
{Company Introduction} is pleased to announce the expansion of its metal forming services to meet the growing demand from various industries. With a reputation for high-quality and precision metal forming solutions, the company has positioned itself as a leader in the industry.
The expansion of metal forming services comes as a response to the increasing demand for custom metal components across a wide range of industries, including automotive, aerospace, electronics, and more. {Company Introduction} aims to provide its customers with a comprehensive range of metal forming solutions to meet their unique needs and requirements.
The company's metal forming services include a variety of processes such as stamping, bending, rolling, and more. {Company Introduction} has invested in state-of-the-art equipment and technology to ensure that it can deliver precise and efficient metal forming solutions to its customers.
The expansion of the company's metal forming services will allow it to take on larger and more complex projects, providing customers with a one-stop shop for all their metal forming needs. Whether it's a small batch of custom metal components or a large-scale production run, {Company Introduction} has the capabilities and expertise to handle it all.
In addition to expanding its metal forming services, {Company Introduction} has also increased its team of experienced engineers and technicians to ensure that it can continue to deliver exceptional results to its customers. The company's team is dedicated to providing innovative solutions and excellent customer service to ensure that every project is completed to the highest standards.
{Company Introduction} is also committed to maintaining the highest standards of quality and precision in its metal forming services. The company adheres to strict quality control measures throughout the entire metal forming process, from design and engineering to manufacturing and inspection. This commitment to quality ensures that customers receive metal components that meet their exact specifications and requirements.
Furthermore, {Company Introduction} is dedicated to sustainability and environmentally friendly practices. The company utilizes advanced manufacturing processes that minimize waste and reduce its environmental impact. By investing in sustainable metal forming solutions, the company is able to meet the needs of its customers while also contributing to a greener and more sustainable future.
With the expansion of its metal forming services, {Company Introduction} is poised to continue its growth and success in the industry. The company looks forward to serving both new and existing customers with its comprehensive range of metal forming solutions, providing them with the high-quality components they need to succeed in their respective industries.
The expansion of metal forming services at {Company Introduction} comes at a time of significant growth in the industry, and the company is well-positioned to meet the increasing demand for custom metal components. With its commitment to quality, precision, and innovation, {Company Introduction} is set to remain a leader in the metal forming industry for years to come.
Company News & Blog
Fiber Laser Engraving Service: Enhancing Precision and Efficiency for Your Engraving Needs
Discover the Benefits of Plasma Cutting Stainless Steel with Nitrogen
Plasma Cutting Stainless Steel With Nitrogen: [Company Name] Introduces Advanced Technology[City, Country] – [Date] – [Company Name], a leading provider of advanced metal cutting and fabrication solutions, has introduced a state-of-the-art plasma cutting technology that allows for the precise and efficient cutting of stainless steel using nitrogen. This revolutionary technology promises to revolutionize the metal fabrication industry by offering a more precise, clean, and cost-effective solution for cutting stainless steel.Plasma cutting is a popular method for cutting metal, but traditional plasma cutting is often limited in its ability to cut stainless steel with the precision and quality that is required by many industries. [Company Name]’s latest innovation, however, utilizes nitrogen as the cutting gas, allowing for a significantly improved cut quality and reduced dross formation on stainless steel.The use of nitrogen as the cutting gas in plasma cutting is not a new concept, but [Company Name] has taken it to the next level by developing a cutting system that is specifically optimized for stainless steel. This system is capable of cutting stainless steel up to [thickness] with unparalleled speed and precision, making it ideal for a wide range of applications in industries such as aerospace, automotive, and general fabrication.In addition to the superior cut quality and reduced dross formation, the use of nitrogen as the cutting gas offers several other benefits. For example, it reduces the risk of oxidation on the cut edges, resulting in a clean and oxide-free cut surface. This, in turn, minimizes the need for additional finishing processes, saving time and money for the end-user.Furthermore, the use of nitrogen as the cutting gas results in lower operating costs compared to traditional plasma cutting methods. Nitrogen is readily available and cost-effective, and its use in plasma cutting can lead to significant savings in gas consumption and consumable costs.[Company Name]’s plasma cutting technology is also environmentally friendly, as it produces fewer emissions and waste compared to traditional cutting methods. This aligns with the company’s commitment to sustainability and responsible manufacturing practices.As a leading provider of metal cutting and fabrication solutions, [Company Name] is dedicated to staying at the forefront of technological advancements in the industry. The introduction of the plasma cutting technology for stainless steel with nitrogen is a testament to the company’s commitment to innovation and its relentless pursuit of excellence.“We are thrilled to introduce this cutting-edge technology to the market,” said [Spokesperson], [Title] at [Company Name]. “With the increasing demand for high-quality stainless steel components in various industries, we are confident that our new plasma cutting system will meet and exceed the expectations of our customers. This technology represents a significant leap forward in the metal fabrication industry and we are excited to see the impact it will have on the market.”[Company Name] has a proven track record of delivering cutting-edge solutions to its customers, both locally and internationally. The company’s team of highly skilled engineers and technicians are dedicated to providing comprehensive support and service, ensuring that customers can fully leverage the capabilities of the new plasma cutting technology.The introduction of the plasma cutting technology is just the latest example of [Company Name]’s commitment to innovation and customer satisfaction. The company continues to invest in research and development to develop new and improved solutions that address the evolving needs of the metal fabrication industry.For more information about [Company Name] and its advanced plasma cutting technology for stainless steel, please visit [company website].About [Company Name]:[Company Name] is a leading provider of advanced metal cutting and fabrication solutions. With a focus on innovation, quality, and customer satisfaction, the company offers a comprehensive range of cutting technologies and services to meet the diverse needs of industries such as aerospace, automotive, and general fabrication. With a strong commitment to sustainability and responsible manufacturing practices, [Company Name] is dedicated to delivering cutting-edge solutions that drive customer success. For more information, please visit [company website].
Top 5 Benefits of Laser Cutting for Your Household Items
Laser Cutting Technology Revolutionizes Manufacturing IndustryLaser cutting technology has become a game changer in the manufacturing industry, offering a precise and efficient method for cutting a wide range of materials. This technology, combined with the expertise of innovative companies such as {}, is ushering in a new era of manufacturing processes that are faster, more accurate, and more cost-effective than ever before.With the advancement of laser cutting technology, manufacturers are able to achieve extremely precise cuts with minimal material waste. This is achieved through the use of high-powered lasers that are capable of cutting through a variety of materials, including metal, plastic, wood, and composites. In addition, the computerized control systems used in conjunction with the lasers allow for precise and complex shapes to be cut with ease.{} is at the forefront of utilizing this cutting-edge technology in their manufacturing processes. As a leading provider of metal products, they have integrated laser cutting technology into their operations to offer their customers unparalleled precision and quality. By investing in state-of-the-art laser cutting equipment, they are able to offer a wide range of customized cutting solutions for various industries, including automotive, aerospace, and architecture.One of the key benefits of laser cutting technology is its ability to produce high-quality cuts with minimal distortion. Traditional cutting methods often result in heat-affected zones and burrs, which can compromise the integrity of the material. With laser cutting, the focused beam of light generates minimal heat, resulting in clean and precise cuts without any distortion. This level of precision and quality is essential for industries that demand high standards for their products.In addition to its precision, laser cutting technology offers significant cost savings for manufacturers. The efficiency and speed of laser cutting processes reduce production times and labor costs, making it a cost-effective solution for companies looking to streamline their operations. Furthermore, the minimal material waste produced by laser cutting results in additional cost savings and environmental benefits.The versatility of laser cutting technology is another factor driving its widespread adoption in the manufacturing industry. With the ability to cut a wide range of materials and produce complex shapes, laser cutting is a versatile solution for various manufacturing needs. This flexibility allows manufacturers to create customized products and components that meet the specific requirements of their customers.As the demand for high-quality, precision-engineered products continues to grow, the role of laser cutting technology in the manufacturing industry is poised to expand even further. The ability to produce intricate and complex designs with precision and efficiency makes laser cutting an indispensable tool for manufacturers across a wide range of industries.The adoption of laser cutting technology by companies such as {} is a testament to its transformative impact on the manufacturing industry. By leveraging this advanced technology, {} is able to deliver superior quality products to their customers while driving operational efficiency and cost savings.In conclusion, laser cutting technology has revolutionized the manufacturing industry by offering a precise, efficient, and cost-effective solution for cutting a wide range of materials. Through the expertise and innovation of companies like {}, this technology is reshaping the way products are manufactured, setting new standards for precision and quality. As the industry continues to embrace the benefits of laser cutting, the future looks bright for manufacturing processes that are faster, more accurate, and more cost-effective than ever before.
The process of welding steel to stainless steel explained
Steel To Stainless Steel Welding Process: A Breakthrough Solution by Acme CorporationAcme Corporation is proud to introduce an innovative solution for welding steel to stainless steel. This breakthrough process has been developed by our team of experts and is set to revolutionize the welding industry.Welding steel to stainless steel has posed many challenges in the past. The differences in the properties of these two materials make the welding process complex and often result in weak welds. However, the new welding process developed by Acme Corporation overcomes these challenges and provides a strong and durable bond between steel and stainless steel.The key to this breakthrough solution lies in our advanced welding techniques and the use of state-of-the-art equipment. Our team has spent extensive time and resources in research and development to optimize the welding parameters and ensure the highest quality of welds. As a result, we have successfully created a welding process that produces strong and reliable bonds between steel and stainless steel.One of the main advantages of our new welding process is its versatility. Whether it's for industrial applications, automotive components, or household appliances, the ability to weld steel to stainless steel opens up a wide range of opportunities for manufacturers. This breakthrough solution will allow companies to create products that are not only strong and durable, but also have a sleek and modern aesthetic.In addition to the strength and durability of the welds, our new process also ensures a smooth and clean finish. This is particularly important for applications where the appearance of the welded joint is crucial. With our solution, manufacturers can achieve seamless and visually appealing welds, adding value to their end products.Furthermore, the new welding process is also more cost-effective compared to traditional methods. By reducing the need for additional materials and minimizing the time required for post-welding treatments, manufacturers can enjoy significant cost savings while maintaining the highest quality standards.Acme Corporation is committed to providing cutting-edge solutions to meet the evolving needs of the industry. Our new welding process for steel to stainless steel is a testament to our dedication to innovation and excellence. We are excited to bring this breakthrough solution to the market and are confident that it will make a significant impact on the welding industry.With this new advancement, Acme Corporation continues to solidify its position as a leader in the welding technology sector. Our commitment to research and development, combined with our passion for pushing the boundaries of what is possible, sets us apart from the competition.As we look ahead, we are already exploring the potential of applying our new welding process to other materials and combinations. Our goal is to continue to innovate and provide solutions that address the most pressing needs of the industry.In conclusion, Acme Corporation is proud to announce the launch of our groundbreaking welding process for steel to stainless steel. Our new solution offers unmatched strength, durability, and aesthetic appeal, while also providing cost savings for manufacturers. We believe that this advancement will set new standards for welding technology and open up endless possibilities for product development.The future of welding steel to stainless steel has arrived, and it's being led by Acme Corporation. We invite manufacturers and industry professionals to explore the potential of our new welding process and experience the difference it can make in their products.
Professional Steel Welding Services for Your Project Needs
Steel Welding Service, a leading provider of welding and fabrication services, is pleased to announce the launch of their newest location in the heart of the industrial district. With over 20 years of experience in the welding industry, Steel Welding Service has established itself as a trusted partner for businesses in need of high-quality welding and fabrication solutions.The new facility is equipped with state-of-the-art machinery and a team of highly skilled welders and fabricators, allowing Steel Welding Service to meet the increasing demand for their services in the area. The company's commitment to excellence and customer satisfaction has been a driving force behind their expansion, and the new location will enable them to better serve their growing client base."We are thrilled to open our newest location in the industrial district," said the CEO of Steel Welding Service. "This expansion is a testament to our dedication to providing top-notch welding and fabrication services to our clients. We are excited to bring our expertise and craftsmanship to the businesses in this area and look forward to fostering new partnerships."Steel Welding Service offers a wide range of welding and fabrication services, including MIG welding, TIG welding, stainless steel fabrication, aluminum fabrication, custom metal fabrication, and more. Their team of experts is capable of handling projects of all sizes, from small prototypes to large-scale industrial applications. By combining cutting-edge technology with traditional craftsmanship, Steel Welding Service ensures that each project is completed with precision and according to the highest standards of quality.In addition to their welding and fabrication capabilities, Steel Welding Service also offers on-site welding and fabrication services, allowing clients to receive their services directly at their location. This convenience has been instrumental in their success, as it enables businesses to minimize downtime and improve efficiency by having their welding and fabrication needs met on-site.The company's dedication to exceptional customer service and satisfaction has earned them a stellar reputation in the industry. Steel Welding Service has built long-lasting relationships with their clients by consistently delivering superior results and exceeding expectations. Their commitment to quality and reliability has set them apart as a leader in the welding and fabrication space.With the opening of their new location, Steel Welding Service is poised to further elevate their position as a trusted provider of welding and fabrication solutions. The company's expansion represents a significant milestone in their growth, and they are eager to extend their services to more businesses in the industrial district and beyond.As they continue to expand, Steel Welding Service remains focused on upholding their core values of integrity, professionalism, and excellence. Their team is dedicated to staying at the forefront of industry advancements and delivering innovative solutions that meet the evolving needs of their clients. With their new location, Steel Welding Service is well-equipped to continue exceeding expectations and setting new standards for welding and fabrication services.For businesses in need of top-quality welding and fabrication services, Steel Welding Service stands as a reliable and capable partner. Their commitment to excellence, combined with their extensive experience and expertise, makes them the go-to choice for businesses looking for superior welding and fabrication solutions. As they embark on this new chapter of growth, Steel Welding Service is fully prepared to meet the increasing demand for their services and provide unmatched craftsmanship to their clients.
Essential Tips for Mig Welding Stainless Steel to Mild Steel
The process of welding stainless steel to mild steel using the MIG welding technique has become increasingly popular in the manufacturing and construction industries. This innovative method allows for the joining of dissimilar metals, providing a strong, durable bond that is essential for a wide range of applications.{Company Name} is a leading provider of welding solutions, specializing in MIG welding equipment and accessories. With a strong commitment to quality and innovation, {Company Name} has been at the forefront of developing cutting-edge technologies that cater to the evolving needs of the welding industry.The process of MIG welding stainless steel to mild steel involves the use of a filler material that is compatible with both metals. This filler material is fed through the MIG welding torch, which generates an electric arc to heat and melt the metals, creating a strong bond as the filler material cools and solidifies.One of the primary advantages of MIG welding stainless steel to mild steel is the ability to create a joint that is highly resistant to corrosion and oxidation. This is particularly important in applications where the welded joint is exposed to harsh environmental conditions, such as in the manufacturing of chemical processing equipment or outdoor structures. The resulting weld is also highly durable, with excellent strength and ductility properties, making it suitable for a wide range of load-bearing applications.{Company Name} has developed a range of MIG welding equipment and consumables specifically designed for welding stainless steel to mild steel. These include specialized welding torches, shielding gases, and filler materials that are optimized for achieving high-quality welds with minimal heat input, reducing the risk of distortion and warping in the welded components.In addition to its technical expertise, {Company Name} provides comprehensive training and support services for welders and fabricators looking to adopt the MIG welding process for joining stainless steel to mild steel. This includes on-site training programs, technical support, and access to a network of certified welding professionals who can provide guidance and assistance in achieving the desired weld quality and performance.The ability to MIG weld stainless steel to mild steel opens up new possibilities for manufacturing and construction projects, allowing for the seamless integration of different materials to meet specific design and performance requirements. This is particularly relevant in industries such as aerospace, automotive, and marine engineering, where the demand for lightweight, corrosion-resistant materials is driving the need for advanced welding solutions.{Company Name} is dedicated to pushing the boundaries of what is possible in the field of welding, and its commitment to research and development has led to numerous breakthroughs in MIG welding technology. By offering a comprehensive range of solutions for welding stainless steel to mild steel, {Company Name} is empowering welders and fabricators to take on new challenges and achieve exceptional results in their craft.As the demand for MIG welding stainless steel to mild steel continues to grow, {Company Name} is well-positioned to lead the way with its innovative products, technical expertise, and unwavering commitment to customer satisfaction. With a strong track record of delivering superior welding solutions, {Company Name} is poised to remain a trusted partner for welders and fabricators seeking to elevate their capabilities and achieve outstanding results in their work.
Techniques for Welding Thin Sheets of Stainless Steel
Welding Thin Stainless Steel: Tips and Tricks for Perfect WeldsStainless steel is a popular choice of material for many applications due to its corrosion resistance, durability, and aesthetic appeal. However, welding thin sheets of stainless steel can be a challenging task, requiring careful preparation, skill, and the right equipment. In this blog post, we will provide some tips and tricks for welding thin stainless steel, including the use of advanced welding techniques and tools to achieve the perfect weld.PreparationBefore you begin welding thin stainless steel sheets, it is essential to prepare the workpiece properly. First, ensure that the surfaces to be welded are clean and free of any contaminants that may affect the quality of the weld. Use a degreaser or solvent to remove any oil, dirt, grease or oxide layers that may be present on the surface. You can also use a wire brush or grinder to remove the oxide layer and create a clean surface for welding.Next, ensure that the edges of the workpieces are aligned properly, with an even gap of around 1-2mm between them. A precise fit is essential for achieving a good weld, so take the time to check and recheck the alignment before beginning the welding process.TechniquesSeveral advanced welding techniques can be used to weld thin sheets of stainless steel, including TIG (Tungsten Inert Gas) welding and laser welding. TIG welding is a popular choice for welding thin stainless steel sheets because it offers precise control over the welding process, a high-quality finish, and the ability to weld various types of stainless steel.With TIG welding, the torch is held by the welder, and the other line feeds behind the weld using parts of pie plates and other forms of bendy stuff to dam the argon behind the weld. This technique ensures that the weld is protected by an argon gas shield, preventing the weld from being contaminated by oxygen and other atmospheric gases.Another option for welding thin stainless steel is laser welding. Laser welding uses a high-energy laser beam to join the workpieces, resulting in a precise, high-quality weld. Laser welding is particularly useful for welding complex shapes and contours, and it is ideal for welding thin sheets of stainless steel, where precision is essential.ToolsTo achieve the perfect weld on thin stainless steel, it is essential to have the right tools. Some of the key tools you will need for welding thin sheets of stainless steel include a TIG welding machine, a suitable electrode, filler wire, and an argon gas cylinder.A high-quality TIG welding machine is essential for achieving precise control over the welding process, enabling you to adjust the weld speed, current, and voltage for optimal results. The right electrode and filler wire are also critical, as they dictate the quality and strength of the weld.ConclusionWelding thin sheets of stainless steel requires careful preparation, skill, and the right equipment. By following the tips and tricks outlined in this blog post, including proper preparation, advanced welding techniques, and the use of quality tools, you can achieve perfect welds every time. Whether you choose TIG welding or laser welding, remember to take your time, stay focused, and enjoy the impressive results that you can achieve with thin steel.
New technique for eco-friendly microstructure etching on complex-shaped components
Technique, Microstructures, Environmentally-Friendly, Free-Form Surfaces, Traditional Etching Methods, Efficiency, SustainabilityThe development of a new laser cutting technique by German researchers promises to revolutionize the way we etch microstructures into complex-shaped surfaces. This new method is expected to be more environmentally friendly and efficient than traditional etching methods, which use chemicals to remove surface material.The technique involves using a laser beam to burn micrometre-fine patterns into free-form surfaces, creating fine microstructures that were previously impossible to achieve with traditional etching methods. In addition to being more precise, this laser cutting technique is believed to be cheaper and more sustainable than its predecessors, making it a more accessible solution for a wider range of applications.One area where this technique is expected to have a significant impact is in the development and production of prototypes. With the Prototype Laser Cutting Technique, it will be easier and more efficient to create fine microstructures on complex-shaped components, which are essential for prototyping. This is an important step in the development of products, as prototypes allow companies to test and refine their products before mass production.The development of this laser cutting technique is a major step towards improving efficiency and sustainability in various industries. It has the potential to revolutionize the manufacturing process by making it more accessible and cost-effective. In addition to being used in prototyping, this technique will be useful for a variety of other applications, including the production of electronics, medical devices, and other precision components.In conclusion, this new Prototype Laser Cutting Technique is a game-changer in the world of microstructure etching. It offers a more environmentally-friendly, efficient, and cost-effective solution than traditional etching methods. With potential applications in a wide range of industries, this laser cutting technique has the potential to revolutionize the way we create precision components and prototypes.
High-Quality Laser Cutting and Bending Services for Your Needs
Laser Cutting And Bending ServicesIn the world of manufacturing and production, precision and accuracy are key. That's why companies are constantly on the lookout for the latest technologies and services to help them achieve their goals. One such service that has been gaining popularity in recent years is laser cutting and bending. This advanced technology allows for precise and intricate cuts and bends, making it ideal for a wide range of industries.Laser cutting and bending services offer a number of benefits over traditional cutting and bending methods. For one, they allow for greater precision and accuracy, resulting in higher quality finished products. Additionally, laser cutting and bending is a faster and more efficient process, which can lead to cost savings for companies in the long run.One company that has been at the forefront of providing top-notch laser cutting and bending services is {}. With their state-of-the-art equipment and highly skilled technicians, they have been able to meet the needs of a wide range of clients from various industries.{} is proud to offer a comprehensive range of laser cutting and bending services to their clients. They utilize the latest technology and equipment, including high-powered lasers and advanced bending machines, to ensure that each project is completed with the utmost precision and efficiency. Whether it's a simple cut or a complex bend, their team has the expertise to get the job done right.One of the key advantages of choosing {} for laser cutting and bending services is their commitment to quality. They understand the importance of delivering accurate and reliable results, and they go above and beyond to ensure that every project meets the highest standards. This dedication to quality has earned them a stellar reputation in the industry and has made them the go-to choice for many companies in need of advanced cutting and bending services.In addition to their commitment to quality, {} also prides itself on providing exceptional customer service. They work closely with each client to understand their specific needs and requirements, and they go the extra mile to ensure that every project is completed to their satisfaction. From start to finish, their team is dedicated to providing a seamless and stress-free experience for their clients.Another key aspect of {}'s laser cutting and bending services is their versatility. They have the capability to work with a wide range of materials, including steel, aluminum, and more. This flexibility allows them to take on projects of varying complexity, from simple cuts to intricate bends and shapes. No matter the material or the scope of the project, {} has the expertise and resources to deliver outstanding results.As the demand for laser cutting and bending services continues to grow, {} remains committed to staying at the forefront of the industry. They invest in the latest technology and techniques to ensure that they can continue to meet the evolving needs of their clients. With their dedication to quality, exceptional customer service, and unmatched expertise, {} is well-positioned to remain a leader in the laser cutting and bending services sector for years to come.In conclusion, laser cutting and bending services have become an invaluable resource for companies in a wide range of industries. From their precision and efficiency to their versatility and reliability, these advanced services offer a number of benefits over traditional cutting and bending methods. And with companies like {} leading the way, the future of laser cutting and bending looks brighter than ever.
US Manufacturer Launches High-Quality Precision Metal Fabrication Services" can be rewritten as "New High-Quality Precision Metal Fabrication Services Now Available in the US.
Precision Fabrications, a leading manufacturing company, is making headlines with its cutting-edge technologies and innovative solutions in the industry. With a strong commitment to quality and customer satisfaction, Precision Fabrications continues to excel in delivering exceptional products and services to its clients worldwide.Established several decades ago, Precision Fabrications has evolved into a global powerhouse in the manufacturing sector. Specializing in the production of precision components and fabricated metal products, the company has garnered a reputation for its expertise, reliability, and attention to detail. With state-of-the-art facilities and a highly skilled workforce, Precision Fabrications is well-equipped to meet the ever-growing demands of its diverse clientele.One of the key strengths of Precision Fabrications lies in its extensive range of capabilities. The company possesses a wide variety of machining and fabrication equipment, allowing it to produce intricate components with utmost precision. From CNC machining and turning to welding and assembly, Precision Fabrications offers comprehensive solutions tailored to meet the unique needs of each client. By combining advanced manufacturing techniques with rigorous quality control measures, the company ensures that every product leaving its facility is of the highest standard.Precision Fabrications serves clients across diverse sectors, including aerospace, automotive, medical, and energy. By catering to such diverse industries, the company has gained invaluable experience in navigating complex manufacturing challenges and delivering solutions that exceed expectations. Its commitment to continuous improvement and investment in research and development have enabled Precision Fabrications to stay ahead of the curve, offering cutting-edge technologies and innovative solutions that keep its clients at the forefront of their respective industries.In addition to its technical expertise, Precision Fabrications places great emphasis on building strong and lasting relationships with its clients. The company recognizes that open communication and collaboration are crucial to ensuring successful partnerships. By actively engaging with clients from project inception to completion, Precision Fabrications is able to fully understand their needs and develop customized solutions that address their specific requirements. This client-focused approach has earned the company a solid reputation for its reliability and ability to deliver on time and within budget.Precision Fabrications also prides itself on its commitment to sustainability and environmental responsibility. The company actively seeks ways to minimize its ecological footprint through efficient use of resources, waste reduction, and recycling initiatives. By implementing eco-friendly practices throughout its operations, Precision Fabrications not only contributes to a greener planet but also demonstrates its commitment to corporate social responsibility.Looking towards the future, Precision Fabrications remains driven by a strong vision to be at the forefront of technological advancements in the manufacturing industry. The company continues to invest in research and development, exploring emerging technologies such as additive manufacturing and automation to further enhance its capabilities. By embracing innovation and staying ahead of industry trends, Precision Fabrications aims to provide its clients with cutting-edge solutions that drive their success in an ever-evolving global market.In conclusion, Precision Fabrications is a leading manufacturing company that has established itself as a trusted partner for clients worldwide. With its commitment to quality, technical expertise, and customer satisfaction, the company continues to deliver exceptional products and services across diverse industries. As it remains dedicated to innovation and sustainability, Precision Fabrications is poised to shape the future of the manufacturing sector, setting new industry standards and raising the bar for excellence.