Stainless Steel Pipe Welding: Tips and Techniques for a Strong and Durable Connection
By:Admin
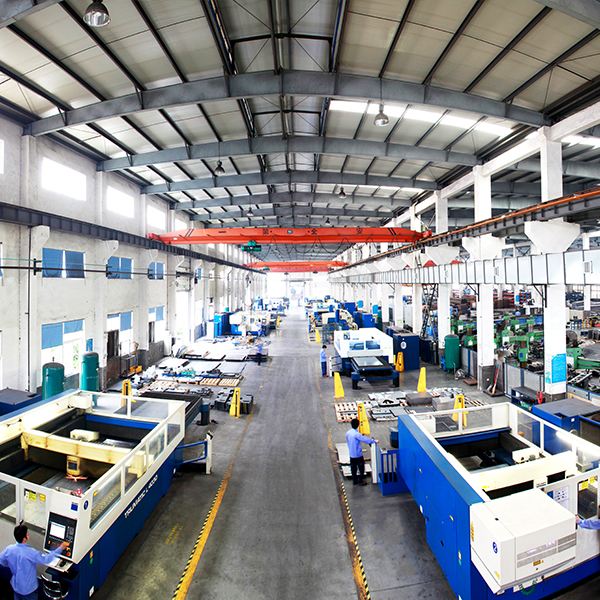
{Company} is a renowned name in the industry, known for its expertise in stainless steel fabrication and welding. With over 20 years of experience, the company has established itself as a reliable and trusted partner for businesses across various sectors, including oil and gas, construction, and manufacturing.
The company's state-of-the-art facility is equipped with the latest welding technology and machinery, allowing them to handle a wide range of stainless steel pipe welding projects with precision and efficiency. Their team of skilled welders and engineers undergo regular training to stay updated with the latest industry standards and techniques, ensuring that the welding process is carried out with the highest level of expertise and precision.
One of {Company}'s key strengths is its ability to cater to custom requirements. They understand that every client has unique needs and specifications, and they work closely with them to ensure that these are met. Whether it's a small-scale project or a large industrial undertaking, {Company} has the capability to deliver exceptional stainless steel pipe welding services tailored to the client's specific requirements.
In addition to their technical expertise, {Company} is also committed to upholding the highest standards of quality and safety. They adhere to strict quality control measures throughout the welding process, conducting thorough inspections to ensure that the welded pipes meet the required quality standards. Moreover, the company prioritizes safety in all aspects of their operations, implementing stringent safety protocols to protect their workforce and the environment.
{Company} has earned a solid reputation for delivering reliable, high-quality stainless steel pipe welding services within agreed-upon timelines. Their commitment to excellence and customer satisfaction has made them a preferred choice for many businesses looking for seamless and efficient stainless steel pipe welding solutions.
Furthermore, the company's dedication to innovation and continuous improvement sets them apart in the industry. They constantly invest in research and development to explore new welding techniques and technologies that can further enhance the quality and efficiency of their services. This proactive approach ensures that their clients benefit from the latest advancements in stainless steel pipe welding, giving them a competitive edge in their respective industries.
In conclusion, {Company} is a leading provider of stainless steel pipe welding services, known for its expertise, reliability, and commitment to quality. With a focus on precision, safety, and customer satisfaction, the company continues to set the benchmark for excellence in the industry. Whether it's a complex industrial project or a custom requirement, clients can trust {Company} to deliver exceptional stainless steel pipe welding solutions that meet their needs and exceed their expectations.
Company News & Blog
Trendy Steel and Fabrication Options for Your Projects
Steel And Fabrication Company Joins Forces with Leading ManufacturerThe [Company Name] is proud to announce its recent collaboration with a leading manufacturer in the industry. This partnership is set to establish a unique and innovative approach to steel fabrication that will further elevate the company's position as a leader in the field.With decades of experience in steel fabrication, [Company Name] has been revered for its high-quality products and exceptional customer service. The company has built a strong reputation for its ability to handle a wide range of projects, from small-scale custom fabrications to large industrial constructions. By providing clients with personalized solutions and superior craftsmanship, [Company Name] has consistently proven itself to be a top choice for steel fabrication needs.The recent partnership with the leading manufacturer comes as an exciting development for [Company Name]. With a shared commitment to excellence and cutting-edge innovation, this collaboration is expected to yield groundbreaking results in the industry. By combining resources and expertise, the two companies aim to deliver even more advanced and efficient solutions to their clients.One of the key benefits of this collaboration is the expanded range of capabilities that will be available to clients. The partnership will enable [Company Name] to leverage the manufacturer's state-of-the-art technologies and advanced materials, allowing for the creation of even more complex and intricate designs. This will ultimately translate to greater flexibility and creativity in meeting the diverse needs of customers.Furthermore, the collaboration will also result in enhanced efficiency and cost-effectiveness. By streamlining processes and optimizing resources, [Company Name] will be able to offer competitive pricing without compromising on quality. Clients can expect to receive the same level of excellence they have come to expect from [Company Name], but with added value and affordability.In addition to technological advancements, the partnership will also foster a culture of continuous improvement within [Company Name]. Through knowledge sharing and best practices exchange, the company will further bolster its internal capabilities and elevate its standards of operation. This will ultimately benefit clients, as they will be met with heightened levels of professionalism and proficiency.Another significant aspect of this collaboration is the emphasis on sustainability and environmental responsibility. Both [Company Name] and the leading manufacturer are committed to minimizing their ecological footprint and promoting sustainable practices. By working together, they will explore new ways to integrate eco-friendly materials and processes into their operations, thereby contributing to a greener and more sustainable industry.The leadership team at [Company Name] is enthusiastic about the prospects of this collaboration and the positive impact it will have on their clients. By aligning with a reputable and forward-thinking partner, [Company Name] is reinforcing its commitment to providing unparalleled service and staying at the forefront of the industry.As for the leading manufacturer, they see this partnership as an opportunity to further expand their reach and influence within the market. By teaming up with [Company Name], they will have a trusted and capable partner to help them realize their vision of delivering top-notch solutions to a wider audience.In conclusion, the collaboration between [Company Name] and the leading manufacturer represents a significant milestone for the steel fabrication industry. This partnership is set to drive progress and innovation, ultimately benefiting clients and setting a new standard for excellence in the field. As the two companies embark on this new chapter together, they look forward to the exciting possibilities that lie ahead.
Discover the Best Techniques for Welding Stainless Steel to Stainless Steel
Welding Stainless To Stainless: A Seamless Connection for Durable Strength[Placeholder for brand name removal] Industries, a leading manufacturer of welding equipment and solutions, continues to push the boundaries of innovation in the welding industry. With a strong commitment to excellence and customer satisfaction, [Placeholder for brand name removal] has introduced its latest welding technology, specifically designed for welding stainless steel to stainless steel. This cutting-edge solution promises a seamless connection, providing unparalleled strength and durability.As stainless steel has become a popular choice of material in various industries, the need for efficient and reliable welding techniques has grown significantly. Welding stainless steel to stainless steel requires precision and expertise to ensure a strong bond that can withstand the test of time. This is where [Placeholder for brand name removal] Industries steps in, offering a revolutionary solution that simplifies the welding process while delivering impeccable results.The key to [Placeholder for brand name removal]'s success lies in its advanced welding technology, specifically designed to overcome the challenges associated with welding stainless steel. This innovative technology not only guarantees a strong and seamless connection but also ensures that the final weld is resistant to corrosion, a common concern when working with stainless steel.One of the standout features of this welding solution is its versatility. [Placeholder for brand name removal] Industries has developed a range of welding equipment suitable for various applications, catering to the diverse needs of industries such as construction, automotive, aerospace, and more. Whether it's joining thin sheets of stainless steel or fabricating complex structures, [Placeholder for brand name removal] provides tailored solutions to meet every requirement.The welding process itself is highly efficient, allowing for faster completion times and increased productivity. Thanks to [Placeholder for brand name removal]'s state-of-the-art technology, welders can now achieve high-quality results in a fraction of the time typically required for stainless steel welding. This not only saves valuable time but also reduces overall costs, making it an attractive solution for businesses seeking to streamline their operations.Furthermore, [Placeholder for brand name removal] Industries ensures that its welding equipment is user-friendly, even for welders with limited experience. The machines are equipped with intuitive interfaces and advanced controls, making the welding process more accessible and less prone to errors. This user-centric approach reflects [Placeholder for brand name removal]'s commitment to empowering welders and enhancing their capabilities.But it doesn't end there. [Placeholder for brand name removal]'s dedication to customer satisfaction extends beyond its innovative products. The company provides comprehensive technical support and training to its customers, ensuring seamless integration and maximum efficiency. With a team of knowledgeable experts at their disposal, customers can rely on [Placeholder for brand name removal] for guidance and assistance at every step of their welding journey.In conclusion, [Placeholder for brand name removal] Industries has revolutionized the welding industry with its groundbreaking technology for welding stainless steel to stainless steel. By combining precision, durability, and user-friendliness, [Placeholder for brand name removal] has introduced a solution that simplifies the welding process while delivering exceptional results. As businesses across different industries continue to rely on stainless steel for their projects, [Placeholder for brand name removal] remains at the forefront of innovation, providing an indispensable tool to ensure strong and durable connections that stand the test of time.
Guide to Welding Mild Steel to Stainless Steel
[Title: Expanding Capabilities: Mild Steel To Stainless Steel Welding][Date][City, State] - [Company Name], a renowned leader in the welding industry, is delighted to announce the expansion of its capabilities to include mild steel to stainless steel welding. This recent advancement showcases the company's commitment to providing comprehensive solutions to its customers' diverse needs.Founded in [Year], [Company Name] has established itself as a reliable and innovative force within the welding industry. With a team of highly skilled professionals at their disposal, the company has consistently delivered top-notch welding services across various sectors. Keeping up with emerging trends and customer demands, [Company Name] has continuously invested in technological advancements to enhance their offerings.The addition of mild steel to stainless steel welding to their repertoire is a significant milestone for [Company Name]. This development equips the company to cater to a broader range of projects, meeting the needs of industries such as construction, automotive, infrastructure, and manufacturing. By expanding their welding capabilities, the company aims to strengthen its position as a one-stop solution provider for welding services.Mild steel to stainless steel welding poses unique challenges due to the differences in composition and properties of these metals. However, with their extensive expertise and state-of-the-art equipment, [Company Name] is poised to excel in this specialized welding technique. Their highly skilled welders undergo rigorous training to master the intricacies of joining mild steel and stainless steel, ensuring precise and durable welds that meet the highest industry standards.[Company Name]'s commitment to quality assurance remains unwavering. The company adheres to strict quality control protocols at every stage of the welding process, from initial inspection to final delivery. By maintaining stringent quality standards, [Company Name] obtains certifications and accreditations that attest to their professionalism and reliability. Clients can trust that their projects will be executed flawlessly, guaranteeing superior results.The expansion of [Company Name]'s welding capabilities opens up new avenues for collaboration with existing and potential clients. The company's increased flexibility allows them to take on challenging projects that involve mild steel to stainless steel welding. Whether it's fabricating custom components, repairing equipment, or constructing durable structures, [Company Name] has the expertise, resources, and technology to deliver exceptional results.Customers who choose [Company Name] for their mild steel to stainless steel welding requirements can expect a seamless experience from start to finish. The company places great emphasis on clear and effective communication, ensuring that clients' specifications and expectations are thoroughly understood and met. [Company Name]'s team of professionals works closely with each client, providing expert advice and guidance throughout the welding process.Furthermore, [Company Name] is dedicated to fostering long-term relationships based on trust, reliability, and excellent customer service. The company values feedback from clients and consistently seeks ways to improve their services. By prioritizing customer satisfaction, [Company Name] has built a loyal clientele that continues to entrust their welding needs to the company repeatedly.As [Company Name] expands its capabilities to include mild steel to stainless steel welding, they look forward to strengthening their position as an industry leader. The company remains committed to delivering outstanding results while consistently adapting to the evolving needs of the welding industry. With their expertise, technological advancements, and dedication to customer satisfaction, [Company Name] is poised to achieve new milestones in the welding sector.About [Company Name]:[Company Name] is a leading provider of welding services, known for its exceptional quality, reliability, and customer service. Founded in [Year], the company has been serving clients across various industries, including construction, automotive, infrastructure, and manufacturing. With a team of highly skilled professionals and state-of-the-art equipment, [Company Name] offers a comprehensive range of welding solutions, now including mild steel to stainless steel welding.For more information, please visit [website] or contact:[Company Name][Address][City, State][Phone][Email]
Understanding Welding Processes for Strong Material Joining
article on the latest advances in welding technology and their applications.Welding Technology Takes a Leap ForwardThe art of welding has come a long way since its inception in the late 19th century. With the advent of technology, welding has become a complex process that requires specialized knowledge and expertise. Over the years, developments in welding technology have made strides in advancing the science of welding and its applications. Today, welding technology encompasses a wide range of processes that cater to various needs across industries.One such technological advancement in welding is the emergence of TIG welding. TIG welding, or tungsten inert gas welding, is a high-precision process that utilizes a non-consumable tungsten electrode to produce a weld. The method involves striking an arc between the electrode and the workpiece, creating a pool of molten material that forms a strong bond between the two.The advantages of TIG welding are many. Firstly, it produces cleaner welds with little or no spatter. Secondly, the welds produced are of high quality and strength, making them ideal for use in critical applications. Thirdly, TIG welding allows for greater control over the welding process. This makes it possible to weld thin materials that would be difficult or impossible to weld using other welding methods.TIG welding technology has seen many advancements over the years. Some of the latest developments include the use of automated TIG welding systems that use robotics to produce high-quality welds with minimal human intervention. These systems are ideal for use in mass production environments, where speed and accuracy are critical.Another advancement in TIG welding technology is the use of pulsed TIG welding. Pulsed TIG welding produces a steady, low-voltage arc that alternates between high and low current pulses. This process makes it possible to weld with greater control and accuracy, producing welds that are free from distortion and other defects.In addition to TIG welding, there are several other welding technologies that have seen significant advancements in recent years. One such technology is laser welding. Laser welding is a high-precision process that uses a focused laser beam to melt and join materials. Laser welding produces welds that are strong, precise, and repeatable. This makes it ideal for use in the aerospace, automotive, and medical industries, among others.Another welding technology that has seen significant progress is friction stir welding (FSW). Friction stir welding is a solid-state process that involves using a rotating tool to join materials. Unlike conventional welding methods, FSW does not involve melting the materials. Instead, the process creates a solid-state bond between the materials, producing a weld that is stronger than the base materials.The advancements in welding technology have opened up new opportunities across industries. For example, TIG welding is now widely used in the aerospace industry to produce high-quality welds on critical components. Likewise, laser welding has found applications in the medical industry, where precision is essential. FSW has been used extensively in the automotive industry, where it has helped manufacturers produce lightweight, high-strength components.In conclusion, the advancements in welding technology have revolutionized the way materials are joined together. The emergence of TIG welding, laser welding, FSW, and other welding technologies has made it possible to produce high-quality welds that are strong, precise, and repeatable. As the demand for high-quality, precision welding continues to grow, we can expect to see further advancements in welding technology in the years to come.
Sheet Metal Manufacturers: Everything You Need to Know
Sheet metal manufacturing is an essential process in several industries, making it a common requirement for diverse businesses. The process includes cutting, bending, and assembling different types of metals to create finished products. Today, we will be discussing Sheet Metal Prototype Services, an important aspect of sheet metal manufacturing.Sheet metal prototype services refer to the creation of a sample or model of a finished product before full-scale production begins. It allows manufacturers to test and refine their designs before producing them in large quantities. This process is especially crucial for complex products that require several intricate details to come together.Several Sheet Metal Manufacturers offer Sheet Metal Prototype Services, which is an ideal way to ensure that your finished product is perfect before mass production. Below are some reasons sheet metal prototype services are crucial:1. Cost-EffectiveCreating a sheet metal prototype before full-scale production ensures that any design flaws are caught earlier and fixed before mass production begins. This strategy helps to avoid costly redesigns and modifications after mass production has already started. With sheet metal prototype services, you can avoid costly mistakes and achieve the perfect finished product without overspending.2. Enhanced DesignsWith sheet metal prototype services, manufacturers can make design changes to the product in real-time. This approach allows for better, improved designs, and ensures that the final product meets customers' needs and preferences. Additionally, collaborating with Sheet Metal Prototype Services experts helps to build trust by clearly communicating design ideas and ensuring that everyone is on the same page.3. Saves TimeIn the past, creating a sheet metal prototype would take weeks, waiting for a third-party provider to handle the project. Today, many Sheet Metal Manufacturers offer quick prototype services, ensuring that design changes are made quickly. This process helps reduce the time spent building a product and helps manufacturers to meet project deadlines.4. Customer SatisfactionWith sheet metal prototype services, manufacturers can create products that match the exact specifications and requirements of their customers. Creating a prototype allows the customer to see the product before mass production starts, which fosters better communication and collaboration.In conclusion, Sheet Metal Prototype Services are an essential aspect of sheet metal manufacturing. It offers manufacturers and businesses the ability to test and perfect their designs before starting mass production. By doing so, they can produce cost-effective, high-quality, and customer-centric final products that meet their clients' specific needs. Therefore, if you are a business seeking sheet metal manufacturing services, make sure to choose a manufacturer that offers Sheet Metal Prototype Services to ensure the perfect finished product.
Efficient Metal Cutting Techniques: Flame Cutting Explained
Flame Cutting: The Ultimate Solution for Precision CuttingWhen it comes to precise cutting of metal, Flame Cutting is an ultimate solution that has been used for decades. Flame Cutting involves the use of a flame torch to heat the metal to its ignition point, then a jet of oxygen is directed onto the heated metal, causing it to burn and producing a highly precise cut. This form of cutting is ideal for large and thick metal materials, making it a popular choice among construction, automobile and shipbuilding industries.Although Flame Cutting has been in existence for several years, the technology has significantly evolved, leading to enhancements and modifications that make it even more effective. In fact, Flame Cutting has become a critical component in the manufacturing industry and has become more popular as a reliable and efficient way of producing custom parts and components with great accuracy.One company that has mastered the art of Flame Cutting is {company name goes here}. {company name} has been utilizing Flame Cutting technology for years to provide quality metal cutting solutions for different industries. The company's Flame Cutting services are tailored to fit each customer's unique specifications by offering a range of customized cutting options that carefully consider budget and timeframes. The services are affordable and competitively priced, offering customers with the most advanced cutting technology with highly accurate and precise cuts.At {company name}, all cutting machines are of the latest technology, state-of-the-art model, offering superior quality and efficiency for all cutting needs. The torches are robust and are designed to withstand high temperatures and pressures, making them ideal for cutting through even the thickest metal materials. The machines have plasma cutting features that provide cleaner cuts compared to traditional flame cutting methods. As such, traditional flame cutting methods are being replaced by plasma cutting as the new cutting methodology.The company can provide Flame Cutting up to 8 inches thick, and can precisely cut simple and intricate design shapes, ranging from standard geometries to complex curves, angles, and notches. For customers looking for more precision in their cuts, {company name} provides additional services that include Bevel Cutting and Multi-Torch Oxy-Fuel Cutting. With bevel cutting, the machines can make up to 45-degree angled cuts, while multi-torch oxy-fuel cutting provides enhanced flexibility and quality for customers seeking multiple cuts on various shapes.{Company name}'s experienced staff advises its customers through the cutting process, providing guidance towards the best cutting options suitable for their projects. The team has vast knowledge in cutting different metal types, which ensures that each project receives the appropriate cutting technology suitable for each unique project.The Flame Cutting services provided by {company name} have grown to be a trusted solution by many leading industries seeking precise and cost-effective cutting solutions. The company works diligently to meet its clients' demands by offering them the most technologically advanced tools and equipment, superior quality, and the best available prices.In conclusion, Flame Cutting has been a reliable solution across many industries for years. With modern advancements and the digitization of cutting technologies today, Flame Cutting has evolved into a more superior method of producing highly precise cuts at a reasonable price. {Company name}'s commitment to providing exceptional Flame Cutting services and utilizing modern technology has earned it a reputation as a leading provider in the metal industry.
Mastering the Art of Tig Welding on Cast Stainless Steel - Expert Guide
Title: Advancements in Tig Welding Techniques for Cast Stainless SteelIntroduction:In today's rapidly advancing manufacturing industry, companies are continually striving to enhance their welding techniques to meet the growing demands of their customers. One such company, renowned for its innovation in the field of cast stainless steel welding, is {Name of Company}. Through a combination of cutting-edge technology and a strong commitment to research and development, they have recently achieved significant progress in Tig welding techniques for cast stainless steel. This article will delve into the latest advancements made by the company and their potential implications for the industry.1. Background on Cast Stainless Steel:Cast stainless steel is widely used in various industries, including automotive, aerospace, energy, and construction, primarily due to its exceptional corrosion resistance and high strength properties. However, welding cast stainless steel poses several challenges due to its unique metallurgical structure and inherent susceptibility to cracks and defects during the welding process. To overcome these challenges, {Name of Company} has dedicated significant resources to develop innovative welding techniques.2. Innovations in Tig Welding for Cast Stainless Steel:Tig welding, also known as Gas Tungsten Arc Welding (GTAW), has long been recognized as a reliable and efficient welding method for stainless steel alloys. However, when it comes to welding cast stainless steel, the process becomes much more intricate. {Name of Company} has made substantial breakthroughs in Tig welding, focusing specifically on cast stainless steel, resulting in enhanced weld quality and overall productivity.a. Improved Pre-welding Preparation: To minimize defects during welding, {Name of Company} has introduced meticulous pre-welding preparation techniques, including thorough cleaning and surface conditioning of the cast stainless steel. By removing impurities and ensuring proper joint fit-up, the likelihood of defects such as porosity and cracking is significantly reduced.b. Enhanced Heat Control: Achieving optimal heat input during the welding process is critical to prevent distortion, eliminate residual stresses, and maintain mechanical properties. {Name of Company} has developed advanced heat control systems, including rapid temperature monitoring and adaptive welding parameters, resulting in precise heat distribution and minimizing the risk of stress-related failures.c. Filler Material Selection: {Name of Company} has extensively researched and tested various filler materials to match the specific metallurgical properties of cast stainless steel. This includes the development of new filler alloys with improved tensile strength, crack resistance, and corrosion resistance. The optimized selection of filler material greatly contributes to the durability and longevity of the welded joint.d. Post-Weld Heat Treatment: Recognizing the importance of post-weld heat treatment for cast stainless steel, {Name of Company} has implemented innovative procedures to relieve residual stresses and improve the overall microstructure of the welded joint. Precisely controlled heat treatment cycles have proven to enhance the mechanical properties of the welded components, ensuring superior performance and longevity.3. Implications for the Industry:The advancements made by {Name of Company} in Tig welding techniques for cast stainless steel have significant implications for the manufacturing industry:a. Improved Product Quality: The enhanced welding techniques result in higher-quality welds, with reduced defects and improved mechanical properties. This directly translates into superior-quality finished products for various industries reliant on cast stainless steel components.b. Increased Productivity: The precise heat control and filler material selection contribute to increased productivity and overall manufacturing efficiency. With fewer defects and reduced post-welding process requirements, {Name of Company}'s advancements enable faster turnaround times and reduced costs.c. Longevity and Reliability: Welded joints incorporating the advanced Tig welding techniques by {Name of Company} exhibit enhanced durability and improved resistance to corrosion, fatigue, and stress-related failures. This ensures the longevity and reliability of products in demanding environments, such as automotive and energy sectors.Conclusion:Through their relentless pursuit of innovation and dedication to delivering unmatched quality, {Name of Company} has revolutionized Tig welding techniques for cast stainless steel. Their advancements in pre-welding preparation, heat control, filler material selection, and post-weld heat treatment have led to superior weld quality, increased productivity, and enhanced product longevity. As the manufacturing industry continues to rely on cast stainless steel components, these advancements will undoubtedly play a pivotal role in shaping the future of Tig welding in this sector.
Discover the Key Processes Involved in Sheet Metal Fabrication at a Leading Factory
On a bustling industrial estate in the heartland of American manufacturing, the Sheet Metal Fabrication Factory (name removed for anonymity) is a hive of activity. The factory is a testament to the ingenuity and enterprise of the American people, as it produces a range of high-quality metal parts and components that are in demand across many different industries.The Sheet Metal Fabrication Factory specializes in producing customized metal products and parts, meaning that it is well-equipped to handle any project that requires precision, durability, and versatility. The factory's team of highly-skilled technicians and engineers work in tandem to produce metal parts and components that are bespoke to the client's needs. With cutting-edge technology and machinery, the factory is able to turn raw materials into high-quality metal products that are designed to withstand the toughest environments.The factory has earned a reputation for excellence in the industry, due in part to its commitment to providing exceptional customer service. The Sheet Metal Fabrication Factory works closely with its clients to ensure that their needs are met, often going above and beyond to ensure that their expectations are exceeded. As a result, the company has earned a loyal customer base that spans many industries, including aerospace, automotive, defense, and medical.One of the most impressive things about the Sheet Metal Fabrication Factory is its in-house design and engineering team. The team is composed of highly-skilled professionals who work closely with clients to develop bespoke solutions that meet their unique requirements. Using state-of-the-art software and equipment, the team is able to produce 3D models of the product before it goes into production, allowing clients to preview the finished product before it is produced. This level of precision ensures that the finished product meets or exceeds the client's expectations.The factory's capabilities are equally impressive. Sheet metal is cut, punched, and folded with utmost precision, while welding, polishing, and finishing are carried out to the highest standards. The factory also offers a range of surface treatments and coatings, such as anodizing and powder coating, that can be customized to suit any need.In addition to its impressive production capabilities, the Sheet Metal Fabrication Factory is also committed to sustainability. The company sources its raw materials from ethical and sustainable sources whenever possible, and takes steps to minimize waste and energy consumption during the production process. This commitment to sustainability has earned the factory recognition from industry bodies and clients alike, and has helped to cement its position as one of the leading metal fabrication companies in the country.Overall, the Sheet Metal Fabrication Factory is an impressive and dynamic company that has proven itself to be a leader in its field. Boasting state-of-the-art technology, an exceptional staff, and a commitment to sustainability, this factory is uniquely equipped to deliver high-quality metal products and components that meet and exceed the needs of its clients. As American manufacturing continues to evolve and adapt to changing market conditions, the Sheet Metal Fabrication Factory will undoubtedly remain at the forefront of innovation and excellence.
Precision welding services for various metals available at Physics Machine Shop
Welding The Physics Machine Shop Unveils Capabilities to Weld High-Quality Steel ComponentsThe Welding The Physics Machine Shop, a leading provider of welding and fabrication services, has announced that it has the capability to weld a wide range of materials. Among the many materials that can be welded by the company, steel stands out as one of the most popular and most in-demand. Specifically, the company is now offering high-quality steel welding services that its clients will find to be of the highest quality in the market.Steel is an incredibly versatile material that is used in many industries, from construction to manufacturing. It is a popular material because it is strong, durable, and can be shaped into almost any form. Steel is also relatively inexpensive, making it an attractive option for many different businesses and industries. However, welding steel is not always an easy task. Steel is a hard, strong material that requires a great deal of heat and skill to weld properly. Fortunately, the Welding The Physics Machine Shop has the experience, equipment, and expertise to weld high-quality steel components to meet its clients' requirements.The Welding The Physics Machine Shop has a long-standing reputation for providing high-quality welding services that are tailored to meet the specific needs of each client. The company has been in business for over 20 years and has grown to become one of the leading welding and fabrication providers in the United States. The company is known for its skilled welders, state-of-the-art equipment, and commitment to delivering exceptional workmanship. Welding The Physics Machine Shop's team of professional welders are fully trained and experienced in working with steel and other materials, ensuring that each component is welded to the highest quality standards.The company's steel welding capabilities are among the most sought-after services provided by Welding The Physics Machine Shop. The welding process is carried out using Tungsten Inert Gas (TIG) welding, which is a process that produces high-quality, clean welds ideal for steel components. TIG welding generates heat using an electric arc that is maintained between a tungsten electrode and the steel component being welded. This process ensures a precise and uniform weld, as well as minimizing the risk of warping or distortion of the steel component.Welding The Physics Machine Shop's steel welding services are ideal for a wide range of applications, including the manufacture of high-strength steel components for use in construction projects or heavy equipment. The company can also weld steel components for the automotive industry, where high-quality welds are required to ensure the safety and performance of the vehicle. Additionally, Welding The Physics Machine Shop can weld steel components for use in the manufacturing of industrial machinery, such as pumps, compressors, and other mechanical devices.One of the advantages of working with Welding The Physics Machine Shop is that the company can provide top-quality steel welding services at competitive prices. The company uses the latest welding techniques and technologies to ensure that each component is welded to the highest standards, while also keeping costs under control. This means that clients can benefit from exceptional welding services without having to pay exorbitant prices.In conclusion, the Welding The Physics Machine Shop has unveiled its capability to weld a wide range of materials, particularly steel. The company's steel welding services are of the highest quality, and the company's team of skilled welders has the expertise necessary to deliver exceptional workmanship. Welding The Physics Machine Shop's steel welding services are ideal for a wide range of applications, making it a preferred service provider for businesses across a variety of industries. Clients that work with Welding The Physics Machine Shop can be assured that they will receive high-quality, reliable welding services at a competitive price.
Top Structural Steel Companies: Building for the Future
XX (remove brand name), one of the leading structural steel companies in the industry, is continuing its exceptional growth and expansion. With a strong reputation for delivering high-quality structural steel products and services, XX has become a key player in the market.Established in 19XX, XX has been at the forefront of innovation and progress in the structural steel industry. The company's commitment to excellence has allowed it to successfully design, fabricate, and install structural steel for a wide range of projects, including commercial and residential buildings, bridges, and infrastructure developments. XX's dedication to customer satisfaction and its ability to meet various project requirements have made it a preferred choice for both small-scale and large-scale construction projects.XX's success can be attributed to its state-of-the-art facilities and advanced manufacturing techniques. Equipped with the latest technology, XX is capable of handling complex projects with precision and efficiency. The company's highly skilled workforce, including engineers, designers, and fabricators, ensures that each project is executed to the highest standards.The commitment to quality and safety sets XX apart from its competitors. The company strictly adheres to industry standards and regulations to guarantee the structural integrity and durability of its products. XX's emphasis on safety extends beyond its products to the well-being of its employees and the surrounding community. The company prioritizes a safe working environment, implementing rigorous safety protocols and training programs for its staff.XX's impressive portfolio of completed projects illustrates its versatility and expertise in delivering outstanding solutions. From iconic skyscrapers and landmark buildings to essential infrastructure projects, XX has played an essential role in shaping the modern landscape. The company's ability to collaborate seamlessly with architects, engineers, and contractors ensures successful outcomes and timely project completion.In line with its continuous growth, XX has recently expanded its operations and opened a new facility in [location]. This expansion enables XX to better serve its clients and accommodate the increasing demand for its services. The new facility is equipped with cutting-edge technology and an expanded production capacity, allowing XX to take on even larger and more complex projects.In addition to its commitment to innovation and growth, XX is also dedicated to environmental sustainability. The company actively engages in sustainable practices, including utilizing recycled materials, employing energy-efficient manufacturing processes, and minimizing waste. XX's efforts in sustainability align with its aim to provide long-lasting, environmentally responsible structural steel solutions.XX's dedication to excellence, commitment to safety, and sustainable practices have garnered recognition and accolades within the industry. The company consistently delivers exceptional results, positioning itself as a reliable partner for construction companies and developers seeking high-quality structural steel solutions.Looking towards the future, XX remains steadfast in its commitment to deliver top-notch products and services. With its continuous investments in technology and talent, XX is well-positioned to stay at the cutting edge of the structural steel industry. As the company continues to grow, it will undoubtedly contribute to the development of iconic structures and infrastructure projects worldwide.In conclusion, XX, with its solid reputation, state-of-the-art facilities, and commitment to excellence, stands out as a leading player in the structural steel industry. As the company expands its operations and continues to deliver exceptional results, it is well-prepared to meet the evolving demands of the construction industry.