Top Small Metal Fabrication Techniques for Custom Projects
By:Admin
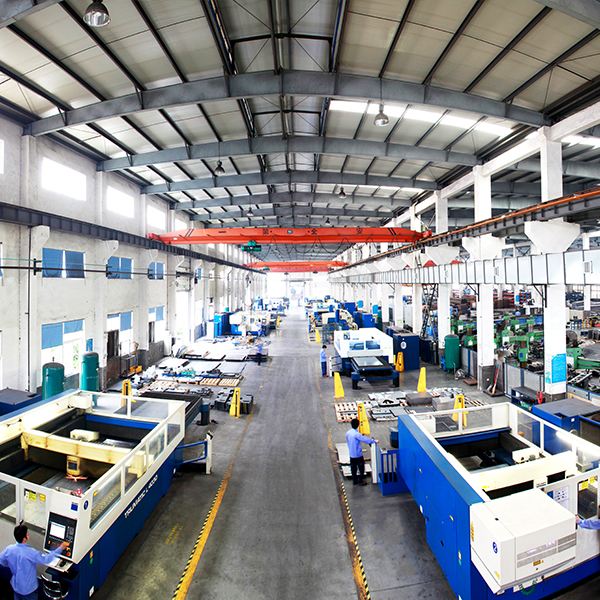
Small Metal Fabrication, a leading provider of high-quality metal fabrication services, has announced the opening of their new state-of-the-art facility in [location], marking a significant milestone for the company. The expansion comes as a response to increasing demand for their services and reflects the company's commitment to providing the best possible solutions for their customers.
With over [number] years of experience in the industry, Small Metal Fabrication has established itself as a trusted name in the metal fabrication sector. The company specializes in providing a wide range of metal fabrication services, including custom metal fabrication, welding, machining, and assembly. Their team of skilled professionals is dedicated to delivering precision-engineered products that meet the highest standards of quality and durability.
The new facility is equipped with the latest cutting-edge technology and machinery, enabling Small Metal Fabrication to further enhance their capabilities and increase production capacity. This investment in new infrastructure demonstrates the company's dedication to staying ahead of the curve and meeting the evolving needs of their customers. Additionally, the upgraded facility will allow the company to take on larger and more complex projects, positioning them for continued growth and success in the industry.
"We are thrilled to announce the opening of our new facility, which represents a significant step forward for Small Metal Fabrication," said [Name], [position] of Small Metal Fabrication. "This expansion is a testament to our ongoing commitment to delivering superior metal fabrication solutions to our customers. With our enhanced capabilities, we are well-positioned to serve a broader range of industries and take on even more challenging projects."
Small Metal Fabrication's new facility also reflects their dedication to sustainability and environmental responsibility. The company has incorporated eco-friendly practices and technologies into the design and operation of the facility, minimizing their environmental impact while maximizing operational efficiency.
In addition to the physical expansion, Small Metal Fabrication has also made strategic investments in training and development for their team members. By providing ongoing education and professional development opportunities, the company aims to ensure that their staff are equipped with the latest skills and knowledge to deliver exceptional results for their customers.
The launch of the new facility has already generated excitement within the industry, with many existing and potential customers eager to see how Small Metal Fabrication's expanded capabilities can benefit their businesses. The company is well-positioned to attract new clients and establish themselves as a leader in the metal fabrication sector.
As Small Metal Fabrication continues to grow and expand, they remain committed to their core values of quality, innovation, and customer satisfaction. The company's dedication to delivering superior metal fabrication solutions, combined with their investment in cutting-edge technology and infrastructure, positions them for continued success in the years to come.
About Small Metal Fabrication:
Small Metal Fabrication is a leading provider of high-quality metal fabrication services, specializing in custom metal fabrication, welding, machining, and assembly. With over [number] years of experience in the industry, the company is dedicated to delivering precision-engineered products that meet the highest standards of quality and durability. Small Metal Fabrication's new state-of-the-art facility reflects their commitment to staying ahead of the curve and meeting the evolving needs of their customers. For more information, visit [website].
Company News & Blog
Quality Laser Cutting Services in Your Local Area
Local Laser Cutting Services Local Laser Cutting Services is a prominent provider of laser cutting solutions in the local area. With a team of highly skilled professionals and state-of-the-art equipment, they offer a wide range of services to meet the diverse needs of their clients. From precision cutting to engraving, they have the capabilities to handle a variety of projects with precision and efficiency.The company takes great pride in their commitment to quality and customer satisfaction. They work closely with their clients to understand their specific requirements and deliver custom solutions that exceed expectations. Whether it's a small prototype or a large production run, Local Laser Cutting Services has the expertise and resources to deliver outstanding results.One of the key advantages of working with Local Laser Cutting Services is their quick turnaround times. They understand the importance of meeting deadlines and strive to complete projects in a timely manner without compromising on quality. This has earned them a stellar reputation in the industry and a loyal client base that continues to trust them with their laser cutting needs.In addition to their cutting-edge technology, Local Laser Cutting Services also emphasizes the importance of sustainability and environmental responsibility. They have implemented eco-friendly practices throughout their operations to minimize their impact on the environment. This has not only helped them reduce waste and energy consumption but has also positioned them as a responsible and forward-thinking service provider.Local Laser Cutting Services is also committed to staying at the forefront of technological advancements in the industry. They continuously invest in the latest equipment and training for their team to ensure that they offer the most advanced and innovative solutions to their clients. This commitment to staying ahead of the curve has enabled them to tackle complex projects and deliver exceptional results.Furthermore, Local Laser Cutting Services is dedicated to fostering a collaborative and inclusive work environment. They prioritize the professional development and well-being of their team members, which has resulted in a motivated and skilled workforce. This, in turn, directly contributes to the high quality and reliability of the services they provide to their clients.In the news, it was announced that Local Laser Cutting Services has expanded their capabilities with the addition of a new state-of-the-art laser cutting machine. This machine boasts increased precision and speed, allowing the company to take on even more complex projects and deliver faster turnaround times. The investment in this new equipment reflects Local Laser Cutting Services' ongoing commitment to providing the best possible service to their clients.In response to the news, the CEO of Local Laser Cutting Services expressed their excitement about the expansion. "We are thrilled to announce the addition of our new cutting-edge laser machine. This investment represents our dedication to offering the highest quality and most advanced laser cutting solutions to our clients. With this new equipment, we are confident that we can continue to exceed the expectations of our customers and take on even more challenging projects."The company's clients have also expressed their enthusiasm about the news, praising Local Laser Cutting Services for their continuous pursuit of excellence. One client stated, "We have been working with Local Laser Cutting Services for several years, and we are consistently impressed with the quality of their work. The addition of the new laser machine only further solidifies our trust in their capabilities, and we look forward to continuing our partnership with them."Overall, Local Laser Cutting Services continues to be a leading provider of laser cutting solutions in the local area. With their unwavering commitment to quality, sustainability, and innovation, they have positioned themselves as a trusted partner for businesses seeking reliable and top-of-the-line laser cutting services. As they continue to expand and invest in their capabilities, it is clear that Local Laser Cutting Services is dedicated to setting new standards in the industry and delivering exceptional results for their clients.
Tips for Welding Stainless Steel for a Restaurant Steamer Tank Exposed to Heat
Welding stainless steel can be a challenging task, especially when it comes to repairing equipment that is constantly exposed to heat, such as a steamer tank in a restaurant. If you have been struggling to fix your stainless steel steamer tank and are getting frustrated with recurring leaks, it might be time to reconsider your repair techniques.One common mistake that people make when attempting to repair stainless steel is using adhesives like JB Weld. While JB Weld is known for its strength and versatility, it is not the ideal solution for repairing stainless steel. Adhesives like JB Weld lack the durability and temperature resistance required for withstanding the extreme conditions that stainless steel equipment in a restaurant setting endures.To effectively repair your stainless steel steamer tank, you need to consider welding as a more reliable solution. Welding provides a strong and permanent bond by joining separate metal pieces together using heat and pressure. When it comes to welding stainless steel, there are several techniques you can employ, such as TIG (Tungsten Inert Gas) welding, MIG (Metal Inert Gas) welding, and spot welding. However, TIG welding is often recommended for stainless steel due to its ability to provide precise and high-quality welds.Before attempting to weld your stainless steel steamer tank, it is crucial to prepare the surface properly. Stainless steel welding requires a clean and contamination-free surface, so make sure to remove any dirt, rust, or previous failed repair attempts. You can use a grinder or sanding tools to clean the surface and ensure a smooth and consistent finish.Once the surface is prepared, it is time to start the welding process. TIG welding stainless steel involves using a tungsten electrode to create an electric arc that generates extreme heat. This heat melts the stainless steel surface, allowing the filler material to be added to create a strong weld joint. It is important to choose the appropriate filler material that matches the stainless steel grade you are working with. Additionally, it is recommended to utilize a shielding gas such as argon or helium to protect the weld area from oxidation and prevent contamination.When welding the stainless steel steamer tank, ensure that you have the proper safety equipment, such as a welding helmet, gloves, and protective clothing. Safety should always be a priority when working with welding equipment and high temperatures.In order to prevent future leaks, it is crucial to pay attention to the welding technique and ensure a solid weld. Proper cleaning and preparation of the surface, precise heat control, and correct filler material selection are key factors in achieving a successful weld. It is also important to thoroughly inspect the weld joint after completing the repair to ensure its integrity.In conclusion, when it comes to repairing a stainless steel steamer tank in a restaurant setting, relying on adhesives like JB Weld may not provide a long-lasting solution. Welding stainless steel using techniques like TIG welding is a more reliable option. By properly preparing the surface, selecting the appropriate filler material, and employing proper welding techniques, you can achieve a strong and leak-free repair. Remember to prioritize safety during the welding process and conduct thorough inspections to ensure the quality of the weld.
Essential Tips for Mig Welding Stainless Steel to Mild Steel
The process of welding stainless steel to mild steel using the MIG welding technique has become increasingly popular in the manufacturing and construction industries. This innovative method allows for the joining of dissimilar metals, providing a strong, durable bond that is essential for a wide range of applications.{Company Name} is a leading provider of welding solutions, specializing in MIG welding equipment and accessories. With a strong commitment to quality and innovation, {Company Name} has been at the forefront of developing cutting-edge technologies that cater to the evolving needs of the welding industry.The process of MIG welding stainless steel to mild steel involves the use of a filler material that is compatible with both metals. This filler material is fed through the MIG welding torch, which generates an electric arc to heat and melt the metals, creating a strong bond as the filler material cools and solidifies.One of the primary advantages of MIG welding stainless steel to mild steel is the ability to create a joint that is highly resistant to corrosion and oxidation. This is particularly important in applications where the welded joint is exposed to harsh environmental conditions, such as in the manufacturing of chemical processing equipment or outdoor structures. The resulting weld is also highly durable, with excellent strength and ductility properties, making it suitable for a wide range of load-bearing applications.{Company Name} has developed a range of MIG welding equipment and consumables specifically designed for welding stainless steel to mild steel. These include specialized welding torches, shielding gases, and filler materials that are optimized for achieving high-quality welds with minimal heat input, reducing the risk of distortion and warping in the welded components.In addition to its technical expertise, {Company Name} provides comprehensive training and support services for welders and fabricators looking to adopt the MIG welding process for joining stainless steel to mild steel. This includes on-site training programs, technical support, and access to a network of certified welding professionals who can provide guidance and assistance in achieving the desired weld quality and performance.The ability to MIG weld stainless steel to mild steel opens up new possibilities for manufacturing and construction projects, allowing for the seamless integration of different materials to meet specific design and performance requirements. This is particularly relevant in industries such as aerospace, automotive, and marine engineering, where the demand for lightweight, corrosion-resistant materials is driving the need for advanced welding solutions.{Company Name} is dedicated to pushing the boundaries of what is possible in the field of welding, and its commitment to research and development has led to numerous breakthroughs in MIG welding technology. By offering a comprehensive range of solutions for welding stainless steel to mild steel, {Company Name} is empowering welders and fabricators to take on new challenges and achieve exceptional results in their craft.As the demand for MIG welding stainless steel to mild steel continues to grow, {Company Name} is well-positioned to lead the way with its innovative products, technical expertise, and unwavering commitment to customer satisfaction. With a strong track record of delivering superior welding solutions, {Company Name} is poised to remain a trusted partner for welders and fabricators seeking to elevate their capabilities and achieve outstanding results in their work.
Top Tips for Small Metal Fabrication
Small Metal Fabrication, a leading enterprise in the field of metal fabrication, has announced its expansion plans for the upcoming year. The company, known for its dedication to quality and innovation, is set to open a new manufacturing facility that will enable them to increase production capacity and meet growing demand from a diverse range of industries.Established in [year], Small Metal Fabrication has built a strong reputation for delivering high-quality metal fabrication solutions to a wide array of clients. Specializing in [specific type of metal fabrication], the company has established itself as a reliable and trusted partner for businesses looking for precision-engineered metal components.The new manufacturing facility, strategically located in [location], will feature state-of-the-art equipment and technology that will enable Small Metal Fabrication to offer an even wider range of services to its clients. This expansion comes as a response to the increasing demand for the company's products and services, and is a testament to Small Metal Fabrication's commitment to providing the best possible solutions to its customers."We are thrilled to announce the expansion of our manufacturing capabilities with the opening of our new facility," said [Name], CEO of Small Metal Fabrication. "This investment is a reflection of our dedication to meeting the evolving needs of our customers and the industries we serve. With this new facility, we will be able to increase our production capacity and offer a broader range of services, further cementing our position as a leader in the metal fabrication industry."The new facility will not only enable Small Metal Fabrication to increase its production capacity, but also to streamline its operations and improve efficiency. This will allow the company to better serve its clients, reduce lead times, and ensure that they continue to receive the high-quality products and services that Small Metal Fabrication is known for.In addition to the new facility, Small Metal Fabrication is also investing in the latest technologies and processes that will further enhance its capabilities. This includes the adoption of advanced CAD/CAM software, CNC machining equipment, and quality control systems, all of which will enable the company to deliver the precise and cost-effective solutions that its clients demand."We understand the importance of staying at the forefront of technological advancements in our industry," said [Name]. "By investing in the latest equipment and processes, we are not only ensuring that we can meet the needs of our clients today, but also in the future. Our commitment to innovation and quality is unwavering, and we are excited to see the positive impact that these investments will have on our ability to serve our customers."With the expansion of its manufacturing capabilities and the adoption of cutting-edge technologies, Small Metal Fabrication is well-positioned to continue its growth and success in the metal fabrication industry. The company's dedication to quality, innovation, and customer satisfaction has allowed it to build strong and lasting relationships with its clients, and this new investment will only serve to further solidify its position as a leader in the field.As Small Metal Fabrication prepares to open its new manufacturing facility, the company is also looking to expand its team of skilled professionals. With the increased demand for its products and services, Small Metal Fabrication is seeking talented individuals who are passionate about metal fabrication and committed to delivering excellence. For those looking to join a dynamic and growing company, Small Metal Fabrication offers exciting opportunities for career development and advancement.The expansion of Small Metal Fabrication's manufacturing capabilities is a testament to the company's commitment to meeting the needs of its clients and delivering the highest quality solutions. With the opening of the new facility and the adoption of advanced technologies, Small Metal Fabrication is poised to continue its leadership in the metal fabrication industry for years to come.
Welding Tips for Galvanized Sheet Metal: What You Should Know
Welding Galvanized Sheet Metal Safely and Effectively: A Look at the Innovative Practices of {}Welding galvanized sheet metal is a complex process that requires precision, skill, and advanced techniques. For many years, companies have struggled with the challenges of welding galvanized steel due to the potential health hazards associated with the zinc coating. However, with the innovative practices and state-of-the-art technology of {}, welding galvanized sheet metal has never been safer or more effective.{} is a leading company in the field of metal fabrication, specializing in welding and forming galvanized sheet metal for a wide range of applications. With over 20 years of experience in the industry, {} has established itself as a pioneer in developing and implementing advanced welding techniques for galvanized steel.One of the key challenges in welding galvanized sheet metal is the release of toxic fumes and gases from the zinc coating when it is exposed to high temperatures. Traditionally, this has made the welding process hazardous for the welder and those in the immediate vicinity. However, {} has made significant strides in developing welding procedures and equipment that minimize the release of harmful substances.One of the innovative methods employed by {} is the use of advanced ventilation systems and fume extraction equipment in their welding facilities. These systems effectively capture and remove the toxic fumes and gases that are generated during the welding process, ensuring a safe and healthy work environment for their employees.In addition to the focus on worker safety, {} has also developed advanced welding techniques that optimize the quality and strength of the welds on galvanized sheet metal. Through extensive research and development, the company has refined its welding procedures to ensure that the zinc coating is preserved and the integrity of the metal is maintained throughout the welding process.Furthermore, {} has invested in state-of-the-art welding equipment that is specifically designed for welding galvanized steel. This includes specialized welding machines and tools that are capable of delivering precise and consistent welds, even on the inherently challenging surface of galvanized sheet metal.To complement their technical expertise, {} also has a team of highly skilled and experienced welders who have been extensively trained in the art of welding galvanized sheet metal. These professionals possess a deep understanding of the unique characteristics of galvanized steel and are equipped with the knowledge and skills to overcome the challenges associated with welding this type of material.With a strong focus on innovation and continuous improvement, {} is leading the way in the industry by setting new standards for the safe and effective welding of galvanized sheet metal. Their commitment to excellence and dedication to advancing welding practices has earned them a reputation as a trusted and reliable partner for companies seeking high-quality welded products made from galvanized steel.In conclusion, the innovative practices and advanced technology employed by {} have revolutionized the welding of galvanized sheet metal, making it safer and more effective than ever before. With a steadfast commitment to worker safety, quality, and innovation, {} continues to set the bar high for the industry, ensuring that their customers receive the best possible welding services for their galvanized steel products.
- The Ultimate Guide to Sheet Metal Fabrication: Tips and Techniques
Sheet metal fabrication is a crucial process used in a wide variety of industries, including automotive, aerospace, construction, and manufacturing. This process involves the cutting, bending, and assembling of sheet metal to create a wide range of products and components. From simple brackets and enclosures to complex machine parts and aerospace components, sheet metal fabrication is essential for producing high-quality, precision-engineered parts.With the advancement of technology and the increasing demand for custom and high-quality sheet metal products, the sheet metal fabrication industry has seen significant growth in recent years. Companies are constantly striving to improve their processes and capabilities to meet the evolving needs of their customers. One such company that has been at the forefront of this industry is {}.{} is a leading provider of sheet metal fabrication services, offering a comprehensive range of capabilities, including laser cutting, CNC punching, bending, welding, and assembly. With state-of-the-art facilities and a team of highly skilled engineers and technicians, {} has the expertise and resources to handle projects of any size and complexity. From prototyping and small-batch production to large-scale manufacturing, {} is committed to delivering the highest quality products and services to its customers.One of the key factors that sets {} apart from its competitors is its focus on precision and quality. The company utilizes the latest manufacturing techniques and equipment to ensure that every product meets the strictest standards of accuracy and quality. From design and engineering to production and finishing, {}’s team is dedicated to delivering products that exceed customer expectations.In addition to its commitment to quality, {} also places a strong emphasis on innovation and continuous improvement. The company invests heavily in research and development to stay ahead of the latest industry trends and technologies. This proactive approach allows {} to offer cutting-edge solutions to its customers, helping them stay competitive in their respective markets.Recently, {} announced the acquisition of new, state-of-the-art equipment to further enhance its sheet metal fabrication capabilities. This investment includes the addition of advanced laser cutting machines and CNC punching equipment, which will significantly improve the company’s production capacity and efficiency. By incorporating the latest technology into its operations, {} aims to better serve its customers and meet the growing demand for high-quality, precision-engineered sheet metal products.The new equipment will also enable {} to expand its range of services and take on more complex and challenging projects. With the ability to work with a wider variety of materials and thicknesses, the company will be able to offer even more options to its customers, further solidifying its position as a leading provider of sheet metal fabrication services.In addition to expanding its capabilities, {} is also dedicated to maintaining its commitment to sustainability and environmental responsibility. The company adheres to strict environmental standards and takes proactive measures to minimize its environmental impact. By optimizing its manufacturing processes and reducing waste, {} strives to operate in an eco-friendly manner, contributing to a more sustainable future.As the demand for custom, high-quality sheet metal products continues to grow, companies like {} are playing a crucial role in meeting this demand. With their focus on precision, quality, innovation, and sustainability, they are setting new standards for the sheet metal fabrication industry. Through their investments in technology and their dedication to customer satisfaction, {} is well-positioned to remain a leader in the industry for years to come.
Mastering the Art of Tig Welding for Mild Steel: A Comprehensive Guide
Tig Welding Mild Steel: A Versatile and Reliable Solution for Various IndustriesIntroduction:In today's fast-paced and demanding industrial landscape, welding plays a crucial role in constructing and fabricating various structures. Welding processes have come a long way, evolving to suit different materials and industry requirements. One such process is Tungsten Inert Gas (TIG) welding, renowned for its precision and versatility.Brands like {} have been at the forefront of delivering exceptional TIG welding solutions. By combining cutting-edge technology with innovative engineering, they have become a trusted name in the industry. Offering a wide range of products and services, the brand has been instrumental in ensuring high-quality welds and enhancing productivity for numerous industries.TIG Welding Mild Steel:Mild steel is one of the most commonly used materials in the fabrication industry due to its affordability, availability, and ease of manipulation. TIG welding mild steel, using the right equipment and techniques, ensures strong and aesthetically pleasing welds.The TIG welding process relies on a non-consumable tungsten electrode to produce the weld, while an inert gas, such as argon, shields the weld area from atmospheric contamination. The ability to control heat input during TIG welding allows for precise welds, making it an ideal choice for mild steel applications.Key Advantages of TIG Welding Mild Steel:1. High-quality welds: TIG welding mild steel offers superior control over the heat input, resulting in high-quality welds with minimal distortion. This makes it suitable for applications that require a flawless finish, such as automotive components, furniture, and architectural structures.2. Versatility: TIG welding is compatible with a wide range of mild steel thicknesses, making it a versatile solution for various applications. From thin sheet metal to thicker structural components, TIG welding can handle it all with precision and ease.3. Clean and aesthetically pleasing welds: The TIG welding process produces clean and visually appealing welds, making it highly sought after in industries where aesthetics matter. This makes it an excellent choice for applications in the food and beverage industry, where hygiene and appearance are paramount.4. Reduced post-weld cleaning: TIG welding creates minimal spatter and produces very little smoke, reducing the need for extensive post-weld cleaning. This saves precious time and resources, enhancing productivity and efficiency in the welding process.Application of TIG Welding Mild Steel:The versatility of TIG welding mild steel makes it suitable for a wide range of industries and applications. Some notable applications include:1. Automotive and transportation: TIG welding is commonly used in the automotive industry for manufacturing exhaust systems, chassis components, and body panels. The precision and control offered by TIG welding ensure durable welds, crucial for the safety and performance of vehicles.2. Construction and infrastructure: TIG welding mild steel plays a vital role in the construction industry, where it is used for fabricating structural components, staircases, and fencing. The ability to produce aesthetically pleasing welds makes TIG welding a preferred choice in architectural applications.3. Food and beverage industry: Stainless steel is a popular choice in the food and beverage industry due to its corrosion resistance and ease of cleaning. TIG welding mild steel is often utilized to weld stainless steel components such as tanks, piping, and equipment, ensuring hygiene and quality standards are met.Conclusion:In conclusion, TIG welding mild steel continues to be a versatile and reliable solution for various industries. With brands like {} leading the way in delivering high-quality TIG welding equipment and services, industries can rely on this process for precise welds, enhanced productivity, and aesthetic appeal. From automotive to construction and food and beverage sectors, TIG welding mild steel offers a range of applications, making it an invaluable tool for fabricators and manufacturers worldwide.
Top Tips for Precision CNC Metal Cutting
CNC Metal Cutting Technology Revolutionizes Manufacturing at []In today's fast-paced manufacturing industry, precision and efficiency are key factors in success. With the advent of CNC metal cutting technology, manufacturers are now able to produce high-quality and complex metal components with ease and accuracy. This technology has revolutionized the way metal parts are fabricated, offering a wide range of benefits for companies looking to enhance their productivity and performance.CNC metal cutting, also known as computer numerical control metal cutting, is a modern manufacturing process that utilizes computer-controlled machines to accurately and efficiently cut and shape metal materials. This technology allows for precise and repeatable machining operations, resulting in high-quality metal components with tight tolerances and smooth finishes. By utilizing advanced computer-aided design (CAD) and computer-aided manufacturing (CAM) software, manufacturers can create detailed and intricate metal parts that meet the exact specifications of their customers.For [], the integration of CNC metal cutting technology has been a game-changer in their manufacturing operations. With an extensive background in metal fabrication, they have embraced CNC metal cutting as a way to stay ahead of the competition and meet the growing demands of their customers. By investing in state-of-the-art CNC machines and training their staff on the latest cutting techniques, [] has been able to expand their capabilities and offer a wider range of metal cutting services to their clients.One of the key advantages of CNC metal cutting technology is its ability to streamline the production process and reduce production time. Traditional metal cutting methods, such as manual milling and turning, are time-consuming and often prone to human error. With CNC metal cutting, the entire process is automated and controlled by the computer, leading to faster and more efficient machining operations. This not only results in quicker turnaround times for customers but also allows manufacturers to take on more complex and challenging projects.In addition to improved efficiency, CNC metal cutting technology also enables manufacturers to achieve higher levels of precision and accuracy. The computer-controlled machines are capable of performing intricate cuts and shaping operations with minimal error, ensuring that each metal component meets the exact specifications of the design. This level of precision is essential for industries that require tight tolerances and complex geometries, such as aerospace, automotive, and medical device manufacturing.Furthermore, CNC metal cutting technology offers a high degree of versatility, allowing manufacturers to work with a wide range of metal materials, including stainless steel, aluminum, titanium, and exotic alloys. This flexibility enables companies like [] to cater to diverse industry needs and provide custom metal cutting solutions for various applications. Whether it's prototyping a new product or mass-producing metal components, CNC metal cutting technology offers the ability to handle a wide spectrum of projects with ease.With the ongoing advancements in CNC metal cutting technology, the future looks promising for the manufacturing industry. As demand for high-quality metal components continues to grow, companies that embrace this cutting-edge technology will be well-positioned to thrive in an increasingly competitive marketplace. [] is a prime example of a company that has leveraged CNC metal cutting to elevate its manufacturing capabilities and deliver exceptional results to its customers.As CNC metal cutting technology becomes more accessible and cost-effective, it's expected that more manufacturers will adopt this innovative approach to metal fabrication. With its unmatched precision, efficiency, and versatility, CNC metal cutting has truly revolutionized the way metal parts are produced, setting a new standard for excellence in the manufacturing industry. As the industry continues to evolve, companies like [] will be at the forefront of this technological revolution, driving innovation and delivering superior metal cutting solutions to their clients.
Expert Custom Metal Bending Services for Precision Fabrication
Custom Metal Bending is a leading company in the metal bending industry, providing high-quality metal bending solutions for a wide range of industries. The company has been in operation for over 20 years and has built a strong reputation for its dedication to precision, quality, and customer satisfaction.The company specializes in custom metal bending, offering a wide range of services including tube bending, pipe bending, and sheet metal bending. With state-of-the-art equipment and a team of highly skilled technicians, Custom Metal Bending is able to handle complex and challenging bending projects with precision and efficiency.One of the key strengths of Custom Metal Bending is its ability to work with a variety of materials, including steel, aluminum, and stainless steel. This versatility allows the company to meet the diverse needs of its customers, who come from industries such as automotive, aerospace, construction, and manufacturing.In addition to its core metal bending services, Custom Metal Bending also offers value-added solutions such as welding, fabrication, and finishing. This comprehensive approach allows the company to be a one-stop-shop for its customers, providing a seamless and efficient experience from start to finish.Custom Metal Bending takes pride in its commitment to quality and accuracy. The company employs strict quality control measures throughout the production process to ensure that each finished product meets the highest standards. This attention to detail has earned Custom Metal Bending a loyal customer base and a reputation for excellence in the industry.Furthermore, Custom Metal Bending is dedicated to staying at the forefront of technological advancements in the metal bending field. The company continually invests in new equipment and training for its staff to ensure that it can offer the most advanced and innovative solutions to its customers. This forward-thinking approach has allowed Custom Metal Bending to lead the way in the industry and remain a trusted partner for its clients.Another key aspect of Custom Metal Bending's success is its commitment to customer satisfaction. The company places a strong emphasis on building long-term relationships with its clients, understanding their unique needs, and delivering tailored solutions that exceed expectations. This customer-centric approach has helped Custom Metal Bending earn the trust and confidence of its clients, many of whom have been with the company for years.In addition to its dedication to quality and customer satisfaction, Custom Metal Bending is also committed to environmental responsibility. The company adheres to strict environmental regulations and implements sustainable practices in its operations. This commitment to sustainability not only benefits the environment but also reflects Custom Metal Bending's integrity and social responsibility as a corporate citizen.Looking ahead, Custom Metal Bending is poised for continued success and growth in the metal bending industry. With its unwavering focus on quality, innovation, and customer satisfaction, the company is well-positioned to meet the evolving needs of its clients and continue to be a leader in the industry.In conclusion, Custom Metal Bending is a trusted partner for businesses in need of high-quality and reliable metal bending solutions. With its dedication to precision, quality, and customer satisfaction, the company has established itself as a leader in the industry and is well-equipped to meet the diverse needs of its clients. As Custom Metal Bending continues to invest in technology, talent, and sustainable practices, it is set to maintain its position as a top choice for custom metal bending services.
Professional Metal Fabrication Services for Quality Results
Metal Fabrication Works, a leading provider of metal fabrication services, offers a wide range of solutions to meet the needs of various industries. The company specializes in the fabrication of metal products such as enclosures, frames, and machinery components for diverse industries including automotive, aerospace, and construction.With over 20 years of experience in the industry, Metal Fabrication Works has established a solid reputation for delivering high-quality products and exceptional customer service. The company's state-of-the-art facilities and team of skilled professionals enable them to handle complex fabrication projects with precision and efficiency. From design and engineering to manufacturing and finishing, Metal Fabrication Works is committed to providing cost-effective and reliable solutions to their clients.One of the key factors that sets Metal Fabrication Works apart from their competitors is their ability to offer customized solutions tailored to the specific needs of their clients. Whether it's a one-off prototype or a large-scale production run, the company has the capabilities to deliver products that meet the highest standards of quality and performance.Metal Fabrication Works' commitment to excellence is evident in their dedication to continuous improvement and investment in the latest technologies. By staying ahead of industry trends and advancements, the company is able to offer cutting-edge fabrication solutions that are both innovative and efficient.In addition to their technical expertise, Metal Fabrication Works places a strong emphasis on customer satisfaction. The company works closely with their clients to understand their needs and expectations, and strives to exceed them at every opportunity. Whether it's providing regular progress updates or offering post-production support, Metal Fabrication Works is dedicated to building long-lasting relationships with their clients based on trust and reliability.Metal Fabrication Works' diverse portfolio of projects speaks to their versatility and adaptability. From small-scale custom fabrications to large-scale production runs, the company has the capacity to handle projects of all sizes and complexities. Their commitment to quality and customer satisfaction has earned them the trust of clients from various industries, making them a preferred partner for metal fabrication needs.Metal Fabrication Works also takes pride in their commitment to environmental sustainability. The company adheres to strict environmental standards and practices responsible waste management to minimize their environmental impact. By incorporating sustainable practices into their operations, Metal Fabrication Works is able to contribute to a cleaner and greener future for the industry and the community.The company's dedication to excellence, innovation, and sustainability has positioned Metal Fabrication Works as a leader in the metal fabrication industry. With a strong track record of delivering superior products and outstanding service, the company continues to set the standard for quality and reliability in the industry.As Metal Fabrication Works looks to the future, they remain committed to upholding their values and exceeding the expectations of their clients. By staying at the forefront of technological advancements and industry best practices, the company is poised to continue providing cutting-edge metal fabrication solutions for years to come. With a steadfast commitment to excellence and customer satisfaction, Metal Fabrication Works is a trusted partner for all metal fabrication needs.