Top Tips for Precision CNC Metal Cutting
By:Admin
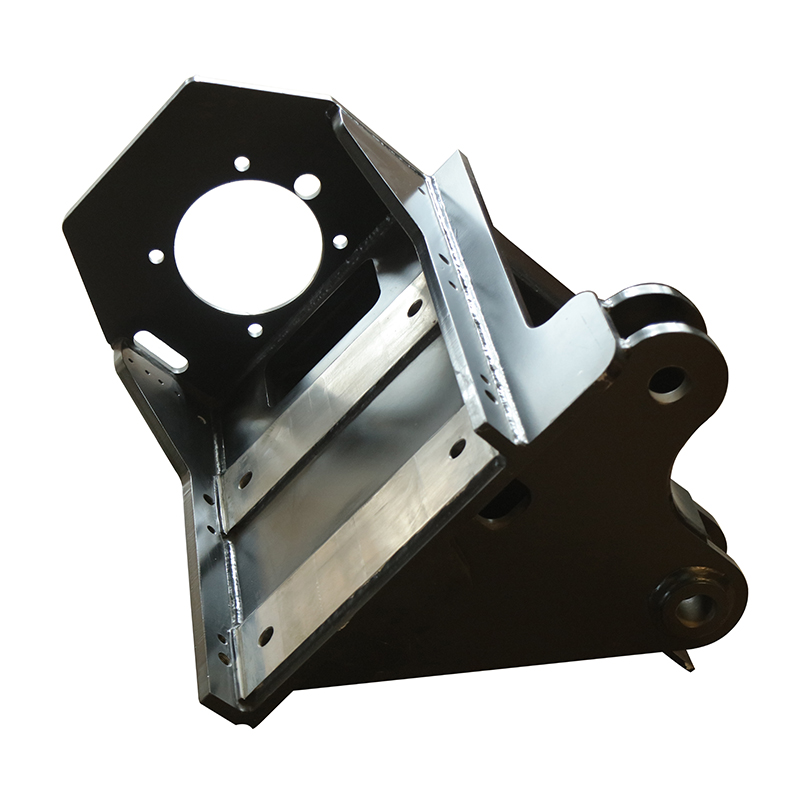
In today's fast-paced manufacturing industry, precision and efficiency are key factors in success. With the advent of CNC metal cutting technology, manufacturers are now able to produce high-quality and complex metal components with ease and accuracy. This technology has revolutionized the way metal parts are fabricated, offering a wide range of benefits for companies looking to enhance their productivity and performance.
CNC metal cutting, also known as computer numerical control metal cutting, is a modern manufacturing process that utilizes computer-controlled machines to accurately and efficiently cut and shape metal materials. This technology allows for precise and repeatable machining operations, resulting in high-quality metal components with tight tolerances and smooth finishes. By utilizing advanced computer-aided design (CAD) and computer-aided manufacturing (CAM) software, manufacturers can create detailed and intricate metal parts that meet the exact specifications of their customers.
For [], the integration of CNC metal cutting technology has been a game-changer in their manufacturing operations. With an extensive background in metal fabrication, they have embraced CNC metal cutting as a way to stay ahead of the competition and meet the growing demands of their customers. By investing in state-of-the-art CNC machines and training their staff on the latest cutting techniques, [] has been able to expand their capabilities and offer a wider range of metal cutting services to their clients.
One of the key advantages of CNC metal cutting technology is its ability to streamline the production process and reduce production time. Traditional metal cutting methods, such as manual milling and turning, are time-consuming and often prone to human error. With CNC metal cutting, the entire process is automated and controlled by the computer, leading to faster and more efficient machining operations. This not only results in quicker turnaround times for customers but also allows manufacturers to take on more complex and challenging projects.
In addition to improved efficiency, CNC metal cutting technology also enables manufacturers to achieve higher levels of precision and accuracy. The computer-controlled machines are capable of performing intricate cuts and shaping operations with minimal error, ensuring that each metal component meets the exact specifications of the design. This level of precision is essential for industries that require tight tolerances and complex geometries, such as aerospace, automotive, and medical device manufacturing.
Furthermore, CNC metal cutting technology offers a high degree of versatility, allowing manufacturers to work with a wide range of metal materials, including stainless steel, aluminum, titanium, and exotic alloys. This flexibility enables companies like [] to cater to diverse industry needs and provide custom metal cutting solutions for various applications. Whether it's prototyping a new product or mass-producing metal components, CNC metal cutting technology offers the ability to handle a wide spectrum of projects with ease.
With the ongoing advancements in CNC metal cutting technology, the future looks promising for the manufacturing industry. As demand for high-quality metal components continues to grow, companies that embrace this cutting-edge technology will be well-positioned to thrive in an increasingly competitive marketplace. [] is a prime example of a company that has leveraged CNC metal cutting to elevate its manufacturing capabilities and deliver exceptional results to its customers.
As CNC metal cutting technology becomes more accessible and cost-effective, it's expected that more manufacturers will adopt this innovative approach to metal fabrication. With its unmatched precision, efficiency, and versatility, CNC metal cutting has truly revolutionized the way metal parts are produced, setting a new standard for excellence in the manufacturing industry. As the industry continues to evolve, companies like [] will be at the forefront of this technological revolution, driving innovation and delivering superior metal cutting solutions to their clients.
Company News & Blog
Unlock the Potential of Cnc Metal Cutting for Enhanced Precision and Efficiency
CNC Metal Cutting Technology: Redefining Precision and EfficiencyIn today's fast-paced manufacturing industry, precision, speed, and efficiency are essential components for businesses to stay ahead of the curve. This is where CNC Metal Cutting technology plays a critical role. With its advanced features and capabilities, CNC Metal Cutting technology is redefining the way manufacturers approach metal cutting processes.CNC Metal Cutting technology uses a series of computer numerical controls to control machines that cut, shape, and form metal materials. The technology offers numerous benefits, such as increased efficiency, cost-effectiveness, and accuracy. With CNC Metal Cutting, manufacturers can get faster production rates and consistent, high-quality results.One leading company in the CNC Metal Cutting industry is [brand name removed]. This company has been providing innovative solutions to the metal cutting market since its inception. The company offers a wide range of CNC Metal Cutting machines, including lasers, plasma cutters, waterjets, and more.The company's mission is to help businesses increase their productivity and profit margins by providing the highest quality CNC Metal Cutting machines. The company has a team of experienced engineers who use the latest technology and manufacturing techniques to create cutting-edge CNC Metal Cutting machines that are both reliable and effective.One machine that stands out from [brand name removed]'s line of CNC Metal Cutting machines is their 5-axis waterjet. The machine combines the benefits of waterjet cutting with the flexibility of 5-axis machining, making it ideal for a wide variety of applications. The 5-axis waterjet is capable of cutting complex shapes and contours with precision and accuracy, and can even cut materials up to 8 inches thick.Another standout feature of [brand name removed]'s CNC Metal Cutting machines is their user-friendly software. The company's machines come equipped with intuitive software that makes programming and operating the machines simple and straightforward. This means that even novice operators can use the machines to produce high-quality results.In addition to their top-of-the-line CNC Metal Cutting machines, [brand name removed] also offers training and support to their customers. The company's team of experts can assist businesses with everything from machine installation and setup to ongoing maintenance and repairs. This ensures that customers get the most out of their CNC Metal Cutting machines and can continue to operate at peak efficiency.Thanks to companies like [brand name removed], CNC Metal Cutting technology is helping businesses increase their productivity and profitability like never before. Whether you're in the aerospace, automotive, or construction industry, CNC Metal Cutting technology has something to offer. With its speed, precision, and efficiency, CNC Metal Cutting is redefining the metal cutting industry, and [brand name removed] is leading the way.
How to Weld Stainless Steel to Mild Steel: A Comprehensive Guide
Headline: Welding Stainless Steel to Mild Steel: An Innovative Solution by {Company Name}Introduction:{Company Name}, a leading expert in metal fabrication and engineering solutions, has introduced a groundbreaking technique for welding stainless steel to mild steel. With their extensive experience and commitment to innovation, the company has successfully developed a solution that addresses the challenges associated with joining dissimilar metals.Body:1. Understanding the Need for Welding Stainless Steel to Mild Steel: Welding stainless steel to mild steel has been a significant challenge in various industries such as automotive, construction, and manufacturing. Both stainless steel and mild steel offer unique attributes and advantages, but their dissimilarities in terms of composition and physical properties make joining them a complex task. However, the combination of these two metals is often desirable to strike a balance between strength, corrosion resistance, and cost-effectiveness.2. The Innovative Solution: {Company Name} has invested substantial resources in research and development to devise an effective technique for welding stainless steel to mild steel. This pioneering approach involves using advanced filler metals and welding processes that ensure a robust and durable bond between the dissimilar materials.3. Comprehensive Material Analysis: Before combining stainless steel and mild steel, {Company Name} conducts a detailed analysis of both metals to determine the most suitable welding method. Factors such as composition, mechanical properties, and intended application are thoroughly assessed to optimize the welding process.4. Advanced Filler Metals: One of the key elements in successfully welding stainless steel to mild steel is the selection of appropriate filler metals. {Company Name} utilizes state-of-the-art filler metals that have been specifically designed for joining dissimilar metals. These specialized fillers possess excellent wetting and spreading characteristics, ensuring a strong bond and minimizing the risk of material failure.5. Tailored Welding Processes: {Company Name}'s team of skilled welders utilizes tailored welding processes to ensure optimal results when combining stainless steel and mild steel. Whether it be TIG (Tungsten Inert Gas) welding, MIG (Metal Inert Gas) welding, or other advanced techniques, the company's experts possess the expertise to choose the most suitable method for each unique welding project.6. Quality Control: {Company Name} is committed to delivering exceptional quality in every welding project. Stringent quality control measures are implemented throughout the welding process, including thorough inspections, non-destructive testing, and adherence to internationally recognized standards. This ensures that the welded stainless steel to mild steel joints meet or exceed industry requirements.7. Advantages and Applications: The innovative welding solution offered by {Company Name} presents numerous advantages to industries requiring the combination of stainless steel and mild steel. These advantages include enhanced strength, improved corrosion resistance, cost-effectiveness, and greater design flexibility. Such benefits make this technique ideal for applications in automotive manufacturing, construction, shipbuilding, and various other sectors.Conclusion:{Company Name}'s groundbreaking technique for welding stainless steel to mild steel opens a new realm of possibilities for industries seeking to combine the advantages of these two dissimilar metals. With their expertise, advanced filler metals, and tailored welding processes, the company ensures robust bonds, exceptional quality, and unmatched customer satisfaction. This innovative solution serves as a testament to {Company Name}'s commitment to pushing the boundaries of metal fabrication and engineering.
High-Quality Laser Cutting and Bending Services for Your Needs
Laser Cutting And Bending ServicesIn the world of manufacturing and production, precision and accuracy are key. That's why companies are constantly on the lookout for the latest technologies and services to help them achieve their goals. One such service that has been gaining popularity in recent years is laser cutting and bending. This advanced technology allows for precise and intricate cuts and bends, making it ideal for a wide range of industries.Laser cutting and bending services offer a number of benefits over traditional cutting and bending methods. For one, they allow for greater precision and accuracy, resulting in higher quality finished products. Additionally, laser cutting and bending is a faster and more efficient process, which can lead to cost savings for companies in the long run.One company that has been at the forefront of providing top-notch laser cutting and bending services is {}. With their state-of-the-art equipment and highly skilled technicians, they have been able to meet the needs of a wide range of clients from various industries.{} is proud to offer a comprehensive range of laser cutting and bending services to their clients. They utilize the latest technology and equipment, including high-powered lasers and advanced bending machines, to ensure that each project is completed with the utmost precision and efficiency. Whether it's a simple cut or a complex bend, their team has the expertise to get the job done right.One of the key advantages of choosing {} for laser cutting and bending services is their commitment to quality. They understand the importance of delivering accurate and reliable results, and they go above and beyond to ensure that every project meets the highest standards. This dedication to quality has earned them a stellar reputation in the industry and has made them the go-to choice for many companies in need of advanced cutting and bending services.In addition to their commitment to quality, {} also prides itself on providing exceptional customer service. They work closely with each client to understand their specific needs and requirements, and they go the extra mile to ensure that every project is completed to their satisfaction. From start to finish, their team is dedicated to providing a seamless and stress-free experience for their clients.Another key aspect of {}'s laser cutting and bending services is their versatility. They have the capability to work with a wide range of materials, including steel, aluminum, and more. This flexibility allows them to take on projects of varying complexity, from simple cuts to intricate bends and shapes. No matter the material or the scope of the project, {} has the expertise and resources to deliver outstanding results.As the demand for laser cutting and bending services continues to grow, {} remains committed to staying at the forefront of the industry. They invest in the latest technology and techniques to ensure that they can continue to meet the evolving needs of their clients. With their dedication to quality, exceptional customer service, and unmatched expertise, {} is well-positioned to remain a leader in the laser cutting and bending services sector for years to come.In conclusion, laser cutting and bending services have become an invaluable resource for companies in a wide range of industries. From their precision and efficiency to their versatility and reliability, these advanced services offer a number of benefits over traditional cutting and bending methods. And with companies like {} leading the way, the future of laser cutting and bending looks brighter than ever.
Professional Welding Services: MIG and TIG Welding for Aluminum and Steel - Hourly Rates Available
Expert Laser Cutting and Bending Services for Precise Results
Laser Cutting and Bending Services Foster Innovation and Growth in Manufacturing IndustryAs the manufacturing industry continues to advance and innovate, the need for efficient and precise laser cutting and bending services becomes increasingly significant. These technologies have revolutionized the manufacturing process by allowing for faster, more accurate parts production and customization. With the latest laser cutting and bending technologies, manufacturers are able to create complex designs and shapes that were previously impossible, ushering in a new era of creativity and efficiency in manufacturing.One company at the forefront of this technological revolution is [company name], a leading provider of laser cutting and bending services. With state-of-the-art equipment and experienced staff, the company has established itself as a reliable and efficient partner for manufacturers in a wide range of industries.Laser cutting is a non-contact process that uses a high-powered laser to cut through various materials, including metals, plastics, and composites. This method produces clean and precise cuts, with minimal waste and distortion. Laser cutting is ideal for creating intricate designs and shapes, making it a popular choice for industries such as aerospace, automotive, and electronics.One of the most significant advantages of laser cutting is its ability to create complex designs with high precision. This allows manufacturers to create parts with tight tolerances, resulting in a more efficient and reliable final product. In addition, laser cutting is much faster than traditional cutting methods, reducing production times and increasing output.Bending is another critical process in manufacturing, and it has also benefited greatly from technological advancements. The latest bending machines use computer-controlled systems to accurately bend and shape metal parts. This technology allows for precise and repeatable bends, with minimal setup time, reducing wastage and material costs.The combination of laser cutting and bending has revolutionized the manufacturing industry, making it possible to produce parts and components with greater accuracy and efficiency than ever before. Manufacturers are now able to create complex shapes and designs, all while keeping production times and costs low.[company name] offers a wide range of laser cutting and bending services to meet the unique needs of their customers. The company has invested heavily in the latest technology to ensure that they can offer the most accurate and efficient services possible. With their advanced equipment and experienced staff, they are able to handle projects of all sizes and complexities.In addition to their laser cutting and bending services, [company name] offers a range of value-added services, including design consultation, prototype development, and assembly. This allows their customers to enjoy a full range of services, from initial product development to final assembly and delivery.The company's commitment to quality and customer satisfaction has earned them a reputation as a reliable and innovative partner for manufacturers in all industries. They work closely with their clients to ensure that their needs are met and that the final product meets the highest standards of quality.In conclusion, laser cutting and bending services are essential for modern-day manufacturing, and companies like [company name] play a critical role in meeting the growing demand for these services. With their advanced technology and innovative solutions, they are helping manufacturers to innovate and grow, creating products that are more efficient, reliable, and affordable than ever before.
Ultimate Guide to Steel Profile Cutting
Steel Profile Cutting, a subsidiary of (company name), is making waves in the steel cutting industry with its innovative technologies and commitment to delivering high-quality products to its customers. With a strong focus on precision and efficiency, Steel Profile Cutting has become a leader in the field, serving a wide range of industries including construction, automotive, and manufacturing.One of the keys to Steel Profile Cutting’s success is its state-of-the-art equipment, including the latest in CNC plasma and oxy-fuel cutting machines. These machines allow for highly accurate and clean cuts, ensuring that the finished products meet the highest standards of quality. In addition, the company’s team of skilled technicians is dedicated to providing personalized service to each customer, ensuring that their specific needs are met with precision and attention to detail.In addition to its cutting-edge technology, Steel Profile Cutting prides itself on its commitment to sustainability and environmental responsibility. The company utilizes advanced recycling processes to minimize waste and reduce its carbon footprint, making it a trusted partner for environmentally conscious businesses. By prioritizing sustainability, Steel Profile Cutting is not only meeting the demands of its customers, but also contributing to a more sustainable future for the steel industry as a whole.Despite its success and growth, Steel Profile Cutting remains dedicated to its core values of integrity, honesty, and customer satisfaction. The company’s team understands the importance of building strong relationships with its clients, and goes above and beyond to ensure that every project is completed to the highest standard. This commitment to excellence has earned Steel Profile Cutting a reputation as a trusted and reliable partner in the steel cutting industry.One recent project that showcases Steel Profile Cutting’s capabilities is the fabrication of custom steel profiles for a major construction project. The client, a leading construction company, required a high volume of precision-cut steel profiles to be used in the construction of a new commercial building. Steel Profile Cutting was able to meet the client’s specifications with accuracy and efficiency, delivering the finished products ahead of schedule and exceeding the client’s expectations.In addition to its commercial projects, Steel Profile Cutting also serves individual customers with custom cutting services for a wide range of applications. Whether it’s a small DIY project or a large-scale industrial application, the company is committed to providing the same level of quality and precision to every client, regardless of the size of the project. This dedication to customer satisfaction has earned Steel Profile Cutting a loyal and satisfied customer base, further solidifying its position as a leader in the industry.Looking ahead, Steel Profile Cutting is poised for continued growth and success, with plans to expand its capabilities and reach new markets. By staying at the forefront of technological advancements and continuously improving its processes, the company aims to remain a top choice for customers in need of high-quality steel cutting solutions. With its unwavering commitment to excellence and customer satisfaction, Steel Profile Cutting is set to continue making a significant impact in the steel cutting industry for years to come.
Mastering the Art of Tig Welding on Cast Stainless Steel - Expert Guide
Title: Advancements in Tig Welding Techniques for Cast Stainless SteelIntroduction:In today's rapidly advancing manufacturing industry, companies are continually striving to enhance their welding techniques to meet the growing demands of their customers. One such company, renowned for its innovation in the field of cast stainless steel welding, is {Name of Company}. Through a combination of cutting-edge technology and a strong commitment to research and development, they have recently achieved significant progress in Tig welding techniques for cast stainless steel. This article will delve into the latest advancements made by the company and their potential implications for the industry.1. Background on Cast Stainless Steel:Cast stainless steel is widely used in various industries, including automotive, aerospace, energy, and construction, primarily due to its exceptional corrosion resistance and high strength properties. However, welding cast stainless steel poses several challenges due to its unique metallurgical structure and inherent susceptibility to cracks and defects during the welding process. To overcome these challenges, {Name of Company} has dedicated significant resources to develop innovative welding techniques.2. Innovations in Tig Welding for Cast Stainless Steel:Tig welding, also known as Gas Tungsten Arc Welding (GTAW), has long been recognized as a reliable and efficient welding method for stainless steel alloys. However, when it comes to welding cast stainless steel, the process becomes much more intricate. {Name of Company} has made substantial breakthroughs in Tig welding, focusing specifically on cast stainless steel, resulting in enhanced weld quality and overall productivity.a. Improved Pre-welding Preparation: To minimize defects during welding, {Name of Company} has introduced meticulous pre-welding preparation techniques, including thorough cleaning and surface conditioning of the cast stainless steel. By removing impurities and ensuring proper joint fit-up, the likelihood of defects such as porosity and cracking is significantly reduced.b. Enhanced Heat Control: Achieving optimal heat input during the welding process is critical to prevent distortion, eliminate residual stresses, and maintain mechanical properties. {Name of Company} has developed advanced heat control systems, including rapid temperature monitoring and adaptive welding parameters, resulting in precise heat distribution and minimizing the risk of stress-related failures.c. Filler Material Selection: {Name of Company} has extensively researched and tested various filler materials to match the specific metallurgical properties of cast stainless steel. This includes the development of new filler alloys with improved tensile strength, crack resistance, and corrosion resistance. The optimized selection of filler material greatly contributes to the durability and longevity of the welded joint.d. Post-Weld Heat Treatment: Recognizing the importance of post-weld heat treatment for cast stainless steel, {Name of Company} has implemented innovative procedures to relieve residual stresses and improve the overall microstructure of the welded joint. Precisely controlled heat treatment cycles have proven to enhance the mechanical properties of the welded components, ensuring superior performance and longevity.3. Implications for the Industry:The advancements made by {Name of Company} in Tig welding techniques for cast stainless steel have significant implications for the manufacturing industry:a. Improved Product Quality: The enhanced welding techniques result in higher-quality welds, with reduced defects and improved mechanical properties. This directly translates into superior-quality finished products for various industries reliant on cast stainless steel components.b. Increased Productivity: The precise heat control and filler material selection contribute to increased productivity and overall manufacturing efficiency. With fewer defects and reduced post-welding process requirements, {Name of Company}'s advancements enable faster turnaround times and reduced costs.c. Longevity and Reliability: Welded joints incorporating the advanced Tig welding techniques by {Name of Company} exhibit enhanced durability and improved resistance to corrosion, fatigue, and stress-related failures. This ensures the longevity and reliability of products in demanding environments, such as automotive and energy sectors.Conclusion:Through their relentless pursuit of innovation and dedication to delivering unmatched quality, {Name of Company} has revolutionized Tig welding techniques for cast stainless steel. Their advancements in pre-welding preparation, heat control, filler material selection, and post-weld heat treatment have led to superior weld quality, increased productivity, and enhanced product longevity. As the manufacturing industry continues to rely on cast stainless steel components, these advancements will undoubtedly play a pivotal role in shaping the future of Tig welding in this sector.
Top Tips for Precision CNC Metal Cutting
CNC Metal Cutting Technology Revolutionizes Manufacturing at []In today's fast-paced manufacturing industry, precision and efficiency are key factors in success. With the advent of CNC metal cutting technology, manufacturers are now able to produce high-quality and complex metal components with ease and accuracy. This technology has revolutionized the way metal parts are fabricated, offering a wide range of benefits for companies looking to enhance their productivity and performance.CNC metal cutting, also known as computer numerical control metal cutting, is a modern manufacturing process that utilizes computer-controlled machines to accurately and efficiently cut and shape metal materials. This technology allows for precise and repeatable machining operations, resulting in high-quality metal components with tight tolerances and smooth finishes. By utilizing advanced computer-aided design (CAD) and computer-aided manufacturing (CAM) software, manufacturers can create detailed and intricate metal parts that meet the exact specifications of their customers.For [], the integration of CNC metal cutting technology has been a game-changer in their manufacturing operations. With an extensive background in metal fabrication, they have embraced CNC metal cutting as a way to stay ahead of the competition and meet the growing demands of their customers. By investing in state-of-the-art CNC machines and training their staff on the latest cutting techniques, [] has been able to expand their capabilities and offer a wider range of metal cutting services to their clients.One of the key advantages of CNC metal cutting technology is its ability to streamline the production process and reduce production time. Traditional metal cutting methods, such as manual milling and turning, are time-consuming and often prone to human error. With CNC metal cutting, the entire process is automated and controlled by the computer, leading to faster and more efficient machining operations. This not only results in quicker turnaround times for customers but also allows manufacturers to take on more complex and challenging projects.In addition to improved efficiency, CNC metal cutting technology also enables manufacturers to achieve higher levels of precision and accuracy. The computer-controlled machines are capable of performing intricate cuts and shaping operations with minimal error, ensuring that each metal component meets the exact specifications of the design. This level of precision is essential for industries that require tight tolerances and complex geometries, such as aerospace, automotive, and medical device manufacturing.Furthermore, CNC metal cutting technology offers a high degree of versatility, allowing manufacturers to work with a wide range of metal materials, including stainless steel, aluminum, titanium, and exotic alloys. This flexibility enables companies like [] to cater to diverse industry needs and provide custom metal cutting solutions for various applications. Whether it's prototyping a new product or mass-producing metal components, CNC metal cutting technology offers the ability to handle a wide spectrum of projects with ease.With the ongoing advancements in CNC metal cutting technology, the future looks promising for the manufacturing industry. As demand for high-quality metal components continues to grow, companies that embrace this cutting-edge technology will be well-positioned to thrive in an increasingly competitive marketplace. [] is a prime example of a company that has leveraged CNC metal cutting to elevate its manufacturing capabilities and deliver exceptional results to its customers.As CNC metal cutting technology becomes more accessible and cost-effective, it's expected that more manufacturers will adopt this innovative approach to metal fabrication. With its unmatched precision, efficiency, and versatility, CNC metal cutting has truly revolutionized the way metal parts are produced, setting a new standard for excellence in the manufacturing industry. As the industry continues to evolve, companies like [] will be at the forefront of this technological revolution, driving innovation and delivering superior metal cutting solutions to their clients.
Leveraging the Power of CNC Laser Services for Your Business's Needs
CNC Laser Service Launches Cutting-Edge Laser Technology to Meet the Needs of Modern BusinessesThe world of manufacturing and industrial production is constantly evolving, and businesses that want to stay ahead of the curve need to stay up to date with the latest technology. That's why CNC Laser Service (name removed) has recently launched their latest laser cutting system, designed to meet the needs of today's businesses.At CNC Laser Service, we have been providing high-quality laser cutting solutions to our customers for over twenty years. During that time, we have built a reputation for excellence, innovation, and customer service, and we are committed to continuing to meet the evolving needs of our clients.Our latest laser cutting system is a testament to that commitment, incorporating the latest technology and design features to deliver precision cutting solutions that are unmatched in the industry. With CNC Laser Service's state-of-the-art system, businesses can quickly and easily create custom parts, prototypes, and products with the highest level of accuracy and efficiency.One of the key benefits of CNC Laser Service's new laser cutting system is its speed. The system can produce parts and products at a significantly faster pace than traditional cutting methods, which means businesses can bring their products to market much more quickly. This speed also allows for faster changes and modifications to products, which is essential in today's fast-paced business environment.The precision of our system is another crucial attribute. Our laser cutting technology allows us to make cuts with an accuracy of 0.001 of an inch, which means we can create parts and products that are incredibly precise, with no room for error. This level of precision not only ensures the final product is of the highest quality, but it also minimizes waste and reduces costs associated with errors or rework.Another feature that sets CNC Laser Service's cutting-edge laser technology apart from traditional manufacturing solutions is its flexibility. Our system can work with a wide range of materials, including metals, plastics, and even delicate materials such as fabrics and ceramics. This versatility means we can tailor our processes to meet the unique needs of each of our clients, covering a wide range of industries.CNC Laser Service's laser machine also offers a high level of customization, allowing us to create parts and products with unique shapes, sizes, and textures. This customization is a vital feature for businesses that need to create parts that are tailored to specific needs, such as the medical or aerospace industries.Finally, our system's automation capabilities allow us to streamline our processes and reduce the need for manual labor, which translates to lower costs and faster turnaround times for our clients. Our laser cutting system allows us to quickly and easily produce large quantities of parts, making it an ideal solution for businesses with high-volume manufacturing needs.At CNC Laser Service, we are incredibly proud of our latest laser cutting system and the benefits it offers our clients. With its speed, precision, flexibility, customization, and automation capabilities, our technology is poised to take businesses to the next level of manufacturing excellence.Whether you're in the automotive, medical, aerospace, defense, or any other industry, CNC Laser Service's laser cutting system has the capability to meet your unique needs. We invite you to contact us today to learn more about our cutting-edge technology and discover how we can help you take your business to the next level of success.
Sheet Metal Bending Services: Custom Solutions for Your Needs
Custom Sheet Metal Bending: A Look Into the Process, Capabilities, and BenefitsSheet metal bending is a vital manufacturing process that allows for the creation of custom parts and components for a wide range of industries. From automotive and aerospace to construction and electronics, custom sheet metal bending plays a crucial role in producing high-quality, precision-engineered parts.{Company Name} is a leading provider of custom sheet metal bending services, offering a comprehensive range of capabilities to meet the unique needs of their customers. With state-of-the-art equipment, skilled technicians, and a commitment to excellence, {Company Name} has established itself as a trusted partner for businesses looking to source high-quality sheet metal components.The process of custom sheet metal bending involves using specialized machinery to shape flat metal sheets into specific geometries, angles, and forms. This process requires precision and expertise to ensure that the final product meets the exact specifications provided by the customer.{Company Name} utilizes a variety of bending techniques, including press braking, roll bending, and stretch forming, to accommodate a wide range of material types and thicknesses. Whether it's aluminum, stainless steel, carbon steel, or copper, {Company Name} has the capabilities to bend and form a diverse array of sheet metal materials.In addition to their technical proficiency, {Company Name} takes pride in their ability to work closely with customers to understand their unique needs and provide tailored solutions. Their team of engineers and technicians collaborate with clients to develop designs, prototypes, and production plans that align with their specific requirements.The benefits of custom sheet metal bending are numerous, and they can have a significant impact on the performance, durability, and overall quality of the final product. By leveraging custom sheet metal bending services, businesses can achieve:1. Precision and accuracy: With the ability to bend metal sheets to exact specifications, custom sheet metal bending allows for the production of parts with high precision and accuracy, ensuring a perfect fit and function.2. Strength and durability: Bending metal sheets can enhance their strength and durability, making them suitable for heavy-duty applications where structural integrity is critical.3. Cost-effectiveness: Custom sheet metal bending can reduce the need for multiple components and assembly, leading to cost savings and improved efficiency in manufacturing processes.4. Customization and versatility: The ability to create custom bent parts opens up opportunities for unique designs and solutions that may not be achievable with standardized components.{Company Name} is committed to delivering these benefits to their customers, offering a combination of advanced technology, skilled craftsmanship, and a dedication to quality. Their facility is equipped with a range of CNC press brakes, roll formers, and other bending equipment, enabling them to produce complex, high-precision parts with ease.The company's expertise extends beyond just bending metal sheets – they also provide additional services such as welding, cutting, and finishing to deliver fully integrated solutions for their clients. From small-batch prototyping to large-scale production runs, {Company Name} has the capacity and capability to handle diverse project requirements.Customer satisfaction is at the core of {Company Name}'s business philosophy, and they strive to exceed expectations by delivering reliable, high-quality products on time. Their commitment to continuous improvement and innovation ensures that they stay at the forefront of industry trends and technological advancements, providing customers with the best possible solutions for their sheet metal bending needs.With a track record of success in serving clients across various industries, {Company Name} has earned a reputation as a trusted and dependable partner for custom sheet metal bending. Their focus on quality, precision, and customer service sets them apart in the market, making them a go-to resource for businesses seeking top-notch sheet metal components.As the demand for custom sheet metal bending continues to grow, {Company Name} remains dedicated to meeting the evolving needs of their customers. By investing in cutting-edge equipment, expanding their capabilities, and fostering a culture of excellence, they are poised to remain a leader in the industry for years to come.