Essential Tips for Mig Welding Stainless Steel to Mild Steel
By:Admin
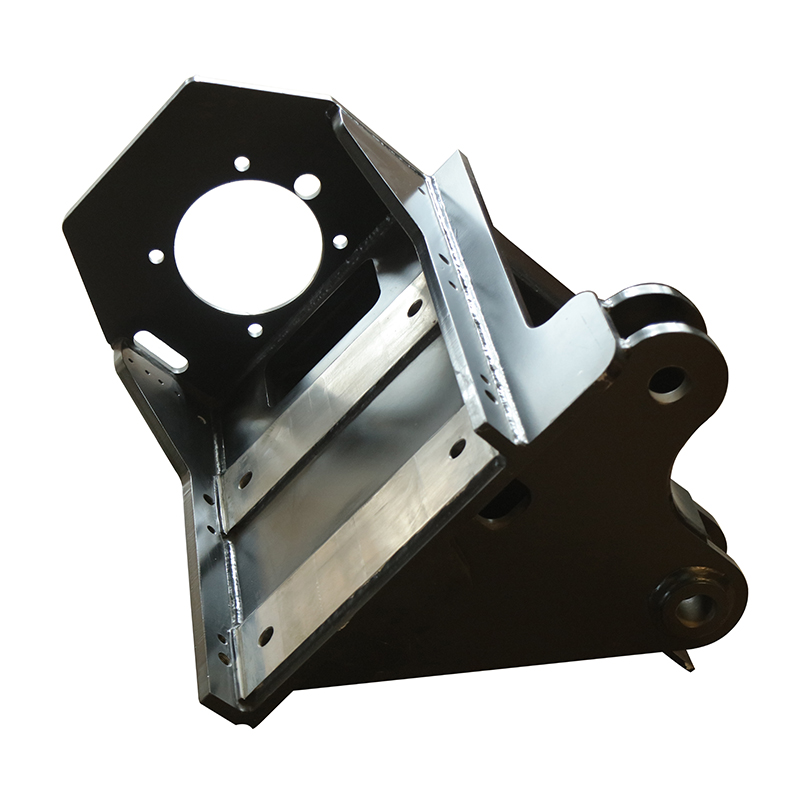
{Company Name} is a leading provider of welding solutions, specializing in MIG welding equipment and accessories. With a strong commitment to quality and innovation, {Company Name} has been at the forefront of developing cutting-edge technologies that cater to the evolving needs of the welding industry.
The process of MIG welding stainless steel to mild steel involves the use of a filler material that is compatible with both metals. This filler material is fed through the MIG welding torch, which generates an electric arc to heat and melt the metals, creating a strong bond as the filler material cools and solidifies.
One of the primary advantages of MIG welding stainless steel to mild steel is the ability to create a joint that is highly resistant to corrosion and oxidation. This is particularly important in applications where the welded joint is exposed to harsh environmental conditions, such as in the manufacturing of chemical processing equipment or outdoor structures. The resulting weld is also highly durable, with excellent strength and ductility properties, making it suitable for a wide range of load-bearing applications.
{Company Name} has developed a range of MIG welding equipment and consumables specifically designed for welding stainless steel to mild steel. These include specialized welding torches, shielding gases, and filler materials that are optimized for achieving high-quality welds with minimal heat input, reducing the risk of distortion and warping in the welded components.
In addition to its technical expertise, {Company Name} provides comprehensive training and support services for welders and fabricators looking to adopt the MIG welding process for joining stainless steel to mild steel. This includes on-site training programs, technical support, and access to a network of certified welding professionals who can provide guidance and assistance in achieving the desired weld quality and performance.
The ability to MIG weld stainless steel to mild steel opens up new possibilities for manufacturing and construction projects, allowing for the seamless integration of different materials to meet specific design and performance requirements. This is particularly relevant in industries such as aerospace, automotive, and marine engineering, where the demand for lightweight, corrosion-resistant materials is driving the need for advanced welding solutions.
{Company Name} is dedicated to pushing the boundaries of what is possible in the field of welding, and its commitment to research and development has led to numerous breakthroughs in MIG welding technology. By offering a comprehensive range of solutions for welding stainless steel to mild steel, {Company Name} is empowering welders and fabricators to take on new challenges and achieve exceptional results in their craft.
As the demand for MIG welding stainless steel to mild steel continues to grow, {Company Name} is well-positioned to lead the way with its innovative products, technical expertise, and unwavering commitment to customer satisfaction. With a strong track record of delivering superior welding solutions, {Company Name} is poised to remain a trusted partner for welders and fabricators seeking to elevate their capabilities and achieve outstanding results in their work.
Company News & Blog
Tig Welding Tips for Cast Stainless Steel: A Comprehensive Guide
Tig Welding Cast Stainless Steel - A Game Changer in the Manufacturing IndustryIn today's fast-paced manufacturing industry, the need for advanced welding techniques has become more crucial than ever before. This is where Tig welding cast stainless steel comes into play. Tig welding, also known as gas tungsten arc welding (GTAW), is a welding process that uses a non-consumable tungsten electrode to produce the weld. It is widely utilized in the fabrication of stainless steel products due to its precision and control over the welding process.One company at the forefront of this innovative welding technique is {Company}. With decades of experience in the welding industry, {Company} has established itself as a pioneer in the development and implementation of advanced welding technologies. Their expertise lies in providing high-quality welding solutions to various industries, including automotive, aerospace, and medical equipment manufacturing.Tig welding cast stainless steel has revolutionized the way stainless steel components are fabricated. Due to its ability to produce clean and precise welds, it has become the preferred method for welding complex and intricate stainless steel parts. The process involves using a filler material to join the cast stainless steel components, resulting in a strong and durable weld that meets the highest quality standards.{Company} has taken Tig welding cast stainless steel to new heights by investing in state-of-the-art equipment and training its team of expert welders to master this technique. They have also collaborated with industry leaders to develop advanced welding procedures and best practices to ensure the highest level of quality and performance.The benefits of Tig welding cast stainless steel are manifold. Not only does it produce aesthetically pleasing welds, but it also offers superior strength and corrosion resistance. This makes it an ideal choice for applications where the welded components are exposed to harsh operating conditions or corrosive environments.Furthermore, the precision and control offered by Tig welding make it suitable for welding thin gauge materials without causing distortion or warpage. This is particularly advantageous in the manufacturing of complex and intricate stainless steel components, where maintaining the original shape and dimensions is crucial.{Company}'s commitment to excellence and continuous improvement has positioned them as a leader in Tig welding cast stainless steel. By staying ahead of industry trends and technological advancements, they have been able to consistently deliver superior welding solutions to their clients, helping them achieve their manufacturing goals with the highest level of quality and precision.In addition to providing cutting-edge welding services, {Company} also offers comprehensive consultation and support to their clients. Their team of welding experts works closely with customers to understand their specific requirements and provide customized solutions that meet and exceed their expectations.The future of manufacturing lies in advanced welding techniques such as Tig welding cast stainless steel. As industries continue to demand higher quality and precision in their fabricated components, companies like {Company} are paving the way for a new era of welding excellence.In conclusion, Tig welding cast stainless steel has become a game changer in the manufacturing industry, enabling the fabrication of complex and intricate stainless steel components with unmatched precision and quality. {Company}'s dedication to mastering this advanced welding technique has solidified their position as a leader in the field, providing their clients with the highest level of welding excellence. As the manufacturing industry continues to evolve, the importance of innovative welding solutions like Tig welding cast stainless steel will only grow, and {Company} is at the forefront of this revolution.
Expert Metal Bending Services for Custom Projects
Custom Metal Bending, located in [location], is a leading provider of precision metal bending and fabrication services. With a strong focus on quality and customer satisfaction, Custom Metal Bending has been serving a wide range of industries including aerospace, automotive, construction, and more for over 20 years. The company's commitment to excellence and innovation has established them as a trusted partner for businesses seeking custom metal bending solutions.Custom Metal Bending offers a wide range of metal bending capabilities, including tube bending, pipe bending, and structural bending. Their state-of-the-art facility is equipped with the latest CNC bending machines and tools to ensure precision and accuracy in every project. From simple bends to complex shapes, the team at Custom Metal Bending has the expertise to deliver high-quality results for their clients.In addition to metal bending, Custom Metal Bending also provides a variety of fabrication services such as welding, cutting, and assembly. Their team of skilled craftsmen and engineers work closely with clients to understand their unique requirements and provide tailored solutions to meet their specific needs. Whether it's a prototype or a large-scale production run, Custom Metal Bending has the capabilities to handle projects of any size and complexity.One of the key differentiators of Custom Metal Bending is their commitment to continuous improvement and investment in technology. The company regularly invests in the latest machinery and software to stay ahead of the curve and provide their clients with the best possible solutions. This dedication to innovation has allowed Custom Metal Bending to expand their capabilities and take on increasingly challenging projects with confidence.Custom Metal Bending's dedication to quality and customer satisfaction is also reflected in their ISO 9001 certification. This internationally recognized standard for quality management ensures that the company adheres to rigorous quality control measures and consistently delivers products and services that meet or exceed customer expectations. With a focus on continuous improvement and customer feedback, Custom Metal Bending is continuously enhancing their processes and services to better serve their clients.The company's commitment to sustainability is another important aspect of their operations. Custom Metal Bending is committed to minimizing their environmental impact through responsible waste management and energy-efficient practices. They strive to source materials from suppliers with sustainable and ethical practices, and also work with clients to develop eco-friendly solutions whenever possible.As Custom Metal Bending looks towards the future, they remain committed to staying at the forefront of the industry by embracing new technologies and expanding their capabilities. With a strong track record of delivering high-quality results and a dedicated team of professionals, the company is well-positioned to continue serving the needs of their clients and the industry as a whole."We are proud of our reputation for excellence and our ability to deliver custom metal bending solutions that meet the unique needs of our clients," says [spokesperson], [job title] at Custom Metal Bending. "We are dedicated to maintaining the highest standards of quality and customer satisfaction, and look forward to continuing to serve our clients with innovative and reliable solutions."Whether it's a simple bend or a complex fabrication project, Custom Metal Bending has the expertise and capabilities to deliver exceptional results. With a strong commitment to quality, innovation, and customer satisfaction, the company continues to be a trusted partner for businesses seeking custom metal bending and fabrication services.
Leveraging the Power of CNC Laser Services for Your Business's Needs
CNC Laser Service Launches Cutting-Edge Laser Technology to Meet the Needs of Modern BusinessesThe world of manufacturing and industrial production is constantly evolving, and businesses that want to stay ahead of the curve need to stay up to date with the latest technology. That's why CNC Laser Service (name removed) has recently launched their latest laser cutting system, designed to meet the needs of today's businesses.At CNC Laser Service, we have been providing high-quality laser cutting solutions to our customers for over twenty years. During that time, we have built a reputation for excellence, innovation, and customer service, and we are committed to continuing to meet the evolving needs of our clients.Our latest laser cutting system is a testament to that commitment, incorporating the latest technology and design features to deliver precision cutting solutions that are unmatched in the industry. With CNC Laser Service's state-of-the-art system, businesses can quickly and easily create custom parts, prototypes, and products with the highest level of accuracy and efficiency.One of the key benefits of CNC Laser Service's new laser cutting system is its speed. The system can produce parts and products at a significantly faster pace than traditional cutting methods, which means businesses can bring their products to market much more quickly. This speed also allows for faster changes and modifications to products, which is essential in today's fast-paced business environment.The precision of our system is another crucial attribute. Our laser cutting technology allows us to make cuts with an accuracy of 0.001 of an inch, which means we can create parts and products that are incredibly precise, with no room for error. This level of precision not only ensures the final product is of the highest quality, but it also minimizes waste and reduces costs associated with errors or rework.Another feature that sets CNC Laser Service's cutting-edge laser technology apart from traditional manufacturing solutions is its flexibility. Our system can work with a wide range of materials, including metals, plastics, and even delicate materials such as fabrics and ceramics. This versatility means we can tailor our processes to meet the unique needs of each of our clients, covering a wide range of industries.CNC Laser Service's laser machine also offers a high level of customization, allowing us to create parts and products with unique shapes, sizes, and textures. This customization is a vital feature for businesses that need to create parts that are tailored to specific needs, such as the medical or aerospace industries.Finally, our system's automation capabilities allow us to streamline our processes and reduce the need for manual labor, which translates to lower costs and faster turnaround times for our clients. Our laser cutting system allows us to quickly and easily produce large quantities of parts, making it an ideal solution for businesses with high-volume manufacturing needs.At CNC Laser Service, we are incredibly proud of our latest laser cutting system and the benefits it offers our clients. With its speed, precision, flexibility, customization, and automation capabilities, our technology is poised to take businesses to the next level of manufacturing excellence.Whether you're in the automotive, medical, aerospace, defense, or any other industry, CNC Laser Service's laser cutting system has the capability to meet your unique needs. We invite you to contact us today to learn more about our cutting-edge technology and discover how we can help you take your business to the next level of success.
Techniques for Welding Thin Sheets of Stainless Steel
Welding Thin Stainless Steel: Tips and Tricks for Perfect WeldsStainless steel is a popular choice of material for many applications due to its corrosion resistance, durability, and aesthetic appeal. However, welding thin sheets of stainless steel can be a challenging task, requiring careful preparation, skill, and the right equipment. In this blog post, we will provide some tips and tricks for welding thin stainless steel, including the use of advanced welding techniques and tools to achieve the perfect weld.PreparationBefore you begin welding thin stainless steel sheets, it is essential to prepare the workpiece properly. First, ensure that the surfaces to be welded are clean and free of any contaminants that may affect the quality of the weld. Use a degreaser or solvent to remove any oil, dirt, grease or oxide layers that may be present on the surface. You can also use a wire brush or grinder to remove the oxide layer and create a clean surface for welding.Next, ensure that the edges of the workpieces are aligned properly, with an even gap of around 1-2mm between them. A precise fit is essential for achieving a good weld, so take the time to check and recheck the alignment before beginning the welding process.TechniquesSeveral advanced welding techniques can be used to weld thin sheets of stainless steel, including TIG (Tungsten Inert Gas) welding and laser welding. TIG welding is a popular choice for welding thin stainless steel sheets because it offers precise control over the welding process, a high-quality finish, and the ability to weld various types of stainless steel.With TIG welding, the torch is held by the welder, and the other line feeds behind the weld using parts of pie plates and other forms of bendy stuff to dam the argon behind the weld. This technique ensures that the weld is protected by an argon gas shield, preventing the weld from being contaminated by oxygen and other atmospheric gases.Another option for welding thin stainless steel is laser welding. Laser welding uses a high-energy laser beam to join the workpieces, resulting in a precise, high-quality weld. Laser welding is particularly useful for welding complex shapes and contours, and it is ideal for welding thin sheets of stainless steel, where precision is essential.ToolsTo achieve the perfect weld on thin stainless steel, it is essential to have the right tools. Some of the key tools you will need for welding thin sheets of stainless steel include a TIG welding machine, a suitable electrode, filler wire, and an argon gas cylinder.A high-quality TIG welding machine is essential for achieving precise control over the welding process, enabling you to adjust the weld speed, current, and voltage for optimal results. The right electrode and filler wire are also critical, as they dictate the quality and strength of the weld.ConclusionWelding thin sheets of stainless steel requires careful preparation, skill, and the right equipment. By following the tips and tricks outlined in this blog post, including proper preparation, advanced welding techniques, and the use of quality tools, you can achieve perfect welds every time. Whether you choose TIG welding or laser welding, remember to take your time, stay focused, and enjoy the impressive results that you can achieve with thin steel.
Discover the Benefits of Custom Fabrication and Welding Services
Custom Fabrication And Welding recently announced their expansion in the fabrication and welding industry, offering a wide range of services to meet the diverse needs of their clients. With their state-of-the-art equipment and highly skilled team, the company has positioned themselves as a leader in the industry, capable of providing customized solutions for a variety of projects.The company specializes in custom fabrication and welding, offering services such as metal cutting, bending, shaping, and welding. They have the capability to work with a variety of materials, including steel, aluminum, and stainless steel, and are able to create custom designs based on their clients' specifications.One of the key factors that sets Custom Fabrication And Welding apart from their competitors is their dedication to providing superior quality work. The company takes great pride in their craftsmanship, ensuring that each project is completed to the highest standards of excellence. They have implemented strict quality control measures to guarantee the durability and reliability of their products, making them a trusted name in the industry.In addition to their commitment to quality, Custom Fabrication And Welding is also known for their exceptional customer service. They work closely with their clients throughout the entire process, from the initial consultation to the final delivery of the project. Their team of experts is always available to address any questions or concerns, and they strive to exceed their clients' expectations with every project.This dedication to excellence has earned Custom Fabrication And Welding a strong reputation within the industry, and they have built long-lasting relationships with many satisfied clients. Their ability to deliver innovative solutions and meet tight deadlines has made them a preferred choice for businesses in need of custom fabrication and welding services.With their recent expansion, Custom Fabrication And Welding is now equipped to take on even larger and more complex projects. They have invested in advanced technology and equipment to further enhance their capabilities, allowing them to tackle a wider range of fabrication and welding requirements. This expansion will enable the company to continue meeting the evolving needs of their clients and maintain their position as a leading provider in the industry.The team at Custom Fabrication And Welding is excited about the opportunities that this expansion brings, and they are eager to take on new challenges and deliver exceptional results for their clients. They are confident that their expanded capabilities will allow them to continue exceeding expectations and solidify their position as a preferred partner for custom fabrication and welding solutions.As they move forward with their expansion, Custom Fabrication And Welding remains committed to their core values of quality, integrity, and customer satisfaction. They are dedicated to upholding the highest standards of professionalism and excellence in all aspects of their work, and they are poised to continue making a positive impact in the fabrication and welding industry.For businesses in need of custom fabrication and welding services, Custom Fabrication And Welding is a trusted partner that can deliver top-notch solutions tailored to their specific needs. With their extensive experience, advanced capabilities, and unwavering commitment to quality, the company is well-equipped to handle a wide range of projects and deliver exceptional results.
Local Laser Cutting Services: Find Top-Notch Precision Cutting Near You
Title: Revolutionary Laser Cutting Technology Shaping the Future of ManufacturingIntroduction:In the fast-paced world of manufacturing, the demand for precise and efficient cutting techniques is ever-present. Cutting-edge technology has emerged to meet this demand, and one such innovation is laser cutting. With its ability to achieve high levels of precision, speed, and flexibility, laser cutting has become an indispensable tool for numerous industries.Company Introduction (Company Name):Established as a pioneer in laser cutting services, our company has been at the forefront of this transformative technology for over two decades. With a diverse range of state-of-the-art laser cutting machines and a team of highly skilled professionals, we have earned a reputation as a trusted partner in the manufacturing industry.1. Laser Cutting: An OverviewLaser cutting is a process that employs a high-powered laser beam to cut through various materials, ranging from metals to plastics and even fabrics. This technology offers distinct advantages over traditional cutting methods, including reduced material wastage, higher precision, and increased operational efficiency. It has found widespread applications across industries such as automotive, aerospace, electronics, and signage.2. High Precision and AccuracyThe key feature that sets laser cutting apart is its exceptional precision and accuracy. The focused laser beam allows for intricate, fine cuts without damaging the surrounding material. This precision is crucial in industries where even the slightest deviation can be detrimental. By adhering to strict quality control protocols, our company ensures that every product meets the highest standards of accuracy.3. Material Versatility and FlexibilityLaser cutting is compatible with a wide range of materials. From metals like stainless steel and aluminum to acrylics, wood, and even ceramics, this process effortlessly navigates diverse materials, allowing for versatile applications. Our cutting-edge laser machines can tackle varying material thicknesses and deliver results with exceptional repeatability.4. Efficiency and ProductivityWhen compared to traditional cutting methods, laser cutting excels in terms of speed and efficiency. The non-contact process eliminates the need for physical force, reducing material damage and minimizing production downtime. The rapid cutting speeds and automated capabilities of our laser machines enable faster production cycles, translating into enhanced productivity and reduced overall costs.5. Design Flexibility and CustomizationDesign flexibility is a crucial aspect in today's highly competitive market. Laser cutting provides unparalleled freedom in creating intricate shapes, patterns, and designs. Whether it is complex geometries or personalized engravings, our company's laser cutting services empower manufacturers to bring their visions to life, catering to the evolving demands of the market.6. Sustainable and Environmentally FriendlyLaser cutting is an environmentally conscious choice due to its minimal waste generation and reduced energy consumption. Traditional cutting methods often result in significant material wastage, while laser cutting optimizes material usage, contributing to both cost savings and environmental preservation.Conclusion:As technology continues to advance, laser cutting has emerged as a game-changer in the manufacturing landscape. With its high precision, speed, and versatility, it has revolutionized the way industries approach cutting processes. The expertise and cutting-edge capabilities of our company undoubtedly make it a go-to choice for businesses seeking best-in-class laser cutting solutions, ensuring their products are crafted with utmost precision and efficiency.
How to Weld Stainless Steel to Regular Steel
Welding Stainless Steel to Steel - A Revolutionary Technique!Welding stainless steel to steel has never been an easy task. Professionals in the industry have been struggling with this challenge for decades. However, the good news is that {} has recently made a breakthrough in this area, with a new welding technique that promises to revolutionize the industry.As experts in the field of welding, {} has been working tirelessly to solve some of the most complex challenges facing the industry. One such challenge is the inability to weld stainless steel to steel, which has been a frustrating issue for many professionals.According to company sources, after years of research and experimentation, {} has developed a new welding technique that can successfully join stainless steel and steel together. This new method promises to expand the application of stainless steel, which will have a significant impact on various industries, including automotive, construction, aerospace, and more.This technique involves the use of specially formulated welding wire with built-in flux that is capable of removing impurities from the steel surface, ensuring a strong and durable bond. The process is quick, efficient, and cost-effective, which makes it a game-changer for the industry.In addition to the innovative welding technique, {} is also proud to offer a range of welding solutions for other challenging applications, including aluminum, copper, and other exotic materials. The company, which has been in the industry for over 20 years, has built a reputation as a reliable and trusted source of welding solutions.{} sources say that the company's team of experts is committed to providing the highest quality of products and services to their clients. They work closely with clients to understand their unique needs and offer customized solutions that meet their specific requirements.With a strong focus on research and development, {} is constantly on the lookout for new techniques and technologies that can improve the welding process. The company is known for its innovation and creativity, and its team of experts is always ready to take on new challenges.The news of this breakthrough welding technique is already making waves in the industry. Many professionals are eager to try out this new method and see its impact on their work.One of {}'s clients, a leading manufacturer of automotive parts, has already tested this new technique and reported excellent results. They were able to weld stainless steel and steel together without any issues, and the joints were strong and durable.The CEO of {} said in a statement, "We are thrilled to offer this new welding technique to our clients. It is a game-changer for the industry, and we are confident that it will make a significant impact on various industries. Our team has worked hard to develop this innovation, and we are excited to see its potential."He added, "We are committed to providing the highest quality of products and services to our clients, and this new technique is one of the many ways we are demonstrating that commitment."In conclusion, the breakthrough welding technique developed by {} promises to revolutionize the industry and expand the application of stainless steel. With a focus on innovation and creativity, {} is leading the way in the welding industry, and their commitment to providing the highest quality of products and services is unwavering. Professionals in the industry are excited to try out this new method and see its potential.
How to weld galvanised steel: tips and techniques
{Company Name}, a leading provider of welding services, has recently announced their specialized welding services for galvanized steel. With their extensive experience and state-of-the-art technology, {Company Name} is equipped to handle the challenges of welding to galvanized steel, providing high-quality and durable solutions for their customers.Galvanized steel is coated with a layer of zinc to protect it from corrosion, making it a popular choice for a wide range of applications, from construction to automotive industries. However, welding to galvanized steel presents unique challenges, as the zinc coating can release toxic fumes when heated, and can also cause weld spatter and porosity if not properly managed.{Company Name} has invested in advanced welding equipment and specialized training for their welders to ensure that they can effectively and safely weld to galvanized steel. Their team of experts is well-versed in the best practices for welding to galvanized steel, including proper ventilation and welding techniques to minimize the release of zinc fumes and ensure a strong weld."We understand the complexities of welding to galvanized steel, and we are committed to providing our customers with reliable and high-quality welding solutions," said {Spokesperson Name}, the CEO of {Company Name}. "With our expertise and dedication to safety, we can confidently tackle the challenges of welding to galvanized steel, delivering superior results for our clients."In addition to their expertise in welding to galvanized steel, {Company Name} offers a wide range of welding services, including MIG, TIG, and stick welding, as well as robotic welding for high-volume production. They serve a diverse customer base across various industries, including automotive, aerospace, construction, and manufacturing.{Company Name} is known for their commitment to quality, reliability, and customer satisfaction. They prioritize safety in all aspects of their work and adhere to the highest industry standards and regulations. Their team of skilled welders and technicians undergo rigorous training and certification to ensure that they can deliver exceptional results for their clients.With their focus on innovation and continuous improvement, {Company Name} stays at the forefront of the welding industry, incorporating the latest technologies and best practices into their services. They are dedicated to meeting the unique needs of each customer and providing tailored solutions that exceed expectations.As {Company Name} continues to expand their capabilities and offerings, they remain steadfast in their commitment to delivering excellence in welding services. Their specialized welding services for galvanized steel demonstrate their ability to take on complex challenges and deliver superior results, setting them apart as a trusted and reliable partner for all welding needs.For businesses and industries that require welding to galvanized steel, {Company Name} offers a proven track record of success, expertise, and dedication to safety. With their unparalleled capabilities and commitment to quality, {Company Name} is the go-to source for all welding needs, delivering reliable and high-quality solutions that stand the test of time.
Efficient Ways to Plasma Cut Painted Metal
Plasma Cutting Unveils New Technology for Painted Metal ProcessingIn the world of metal fabrication, Plasma Cutting Inc. has emerged as a pioneer in developing advanced cutting solutions. The company's latest breakthrough has revolutionized the way painted metal is processed, offering a game-changing technology that allows for efficient and precise cutting without compromising the integrity of the paint finish. With its commitment to innovation, Plasma Cutting Inc. continues to push the boundaries of what is possible in the industry.Traditional methods of cutting painted metal have often posed challenges, leading to subpar results and costly rework. The need to remove the paint before cutting not only takes time but also leads to additional expenses and potential damage to the material. Recognizing this problem, Plasma Cutting Inc. embarked on a mission to find a solution that would eliminate the need for paint removal while delivering exceptional cutting quality.After years of research and development, Plasma Cutting Inc. has successfully developed a unique technology that allows for clean and precise cuts on painted metal surfaces. By employing a highly concentrated plasma arc, the new system cuts through the metal while leaving the paint unharmed, resulting in a smooth and flawless finish. This breakthrough technology has the potential to revolutionize various industries, including automotive, construction, and manufacturing.One of the key advantages of Plasma Cutting Inc.'s new technology is its ability to significantly reduce production time. As the paint no longer needs to be removed before cutting, the entire process becomes faster and more efficient. This increased productivity allows manufacturers to deliver products faster to their customers, ultimately boosting their bottom line. Additionally, the elimination of paint removal reduces material waste, further contributing to a more sustainable manufacturing process.Furthermore, the integrity of the paint finish is preserved, ensuring that the final product meets the highest quality standards. Compared to traditional methods that often result in chipped or uneven paint, Plasma Cutting Inc.'s technology guarantees a flawless paint finish on the cut edges. This eliminates the need for time-consuming touch-ups and refinishing, saving both time and money for manufacturers.Plasma Cutting Inc.'s breakthrough technology also opens up new design possibilities for painted metal products. With the ability to make intricate and precise cuts, manufacturers can now create more complex and aesthetically pleasing designs. This flexibility gives designers and architects the freedom to explore innovative concepts and push the boundaries of creativity.The success of Plasma Cutting Inc.'s new technology can be attributed to the company's unwavering commitment to research and development. With a team of highly skilled engineers and technicians, the company consistently strives to push the limits of what is possible in the field of metal fabrication. Their dedication to innovation has earned them a reputation as a leading provider of cutting-edge cutting solutions.As industries continue to evolve and demand higher quality products, Plasma Cutting Inc. stands at the forefront of delivering cutting-edge technology. With their revolutionary method of cutting painted metal, the company has transformed the way manufacturers approach metal fabrication. This breakthrough offers unparalleled efficiency, precision, and quality that will undoubtedly reshape various industries.In conclusion, Plasma Cutting Inc.'s new technology for cutting painted metal sets a new standard in the field of metal fabrication. By eliminating the need for paint removal, the company has revolutionized the production process, offering increased efficiency, superior quality, and design flexibility. Powered by their commitment to innovation, Plasma Cutting Inc. continues to lead the way in advancing the capabilities of the industry and remains a trusted partner for manufacturers seeking cutting-edge solutions.