Guide to Welding Steel to Stainless Steel: Tips and Techniques
By:Admin
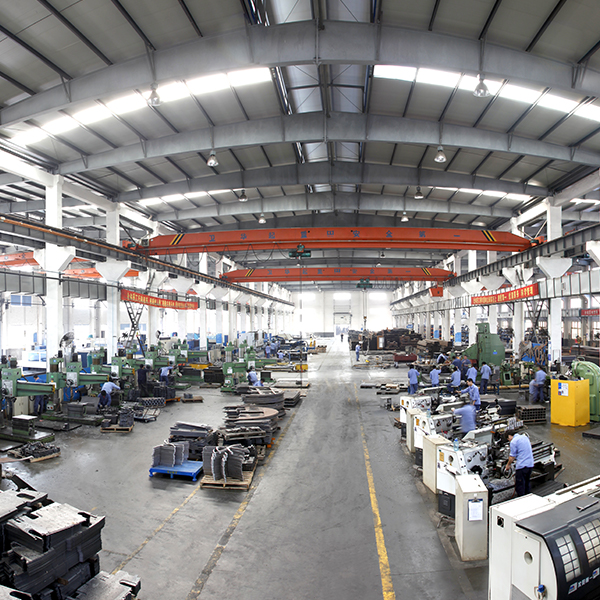
In today's rapidly evolving manufacturing industry, the demand for high-quality, durable products continues to grow. As a result, there is an increased need for advanced welding techniques that can join different types of metals together with precision and strength. One company that is at the forefront of this industry is {}.
{} is a leading manufacturing company that specializes in producing a wide range of industrial products using state-of-the-art technologies and innovative techniques. With a strong focus on quality and innovation, the company has been a key player in the industry for several years.
Recently, {} reached a significant milestone with the successful development of a new welding technique that allows for the seamless joining of steel to stainless steel. This breakthrough has the potential to revolutionize the manufacturing industry by opening up new possibilities for the production of high-performance, corrosion-resistant products.
The traditional methods of welding steel to stainless steel have often been challenging, as the two metals have different properties and require careful handling to ensure a strong and durable bond. However, {}'s new welding technique has overcome these challenges by leveraging the latest advancements in welding technology.
The company's team of skilled engineers and technicians worked tirelessly to develop and perfect this innovative welding process. By utilizing advanced welding equipment and proprietary techniques, they were able to achieve a flawless weld that exhibits exceptional strength and integrity.
The successful implementation of this new welding technique has paved the way for {} to expand its product offerings and cater to a wider range of industrial applications. With the ability to create seamless joints between steel and stainless steel, the company can now produce a diverse array of products, including machinery parts, automotive components, and architectural elements.
In addition to the practical applications of this new welding technique, {} is also committed to upholding the highest standards of quality and safety. The company ensures that all its welding processes adhere to industry regulations and best practices, thereby guaranteeing the reliability and performance of its products.
Furthermore, {} is dedicated to sustainability and environmental responsibility in its manufacturing operations. The company strives to minimize waste and reduce its carbon footprint by implementing efficient production processes and utilizing eco-friendly materials.
As {} continues to pioneer advancements in welding technology and manufacturing excellence, it remains committed to serving its customers with the utmost dedication and integrity. The company's unwavering pursuit of innovation and quality has earned it a reputation as a trusted partner for businesses across various industries.
Looking ahead, {} is poised to further expand its capabilities and offerings, leveraging its expertise in welding and manufacturing to meet the evolving needs of the market. With a relentless commitment to excellence, the company is well-positioned to continue setting new benchmarks in the industry and delivering exceptional value to its customers.
In conclusion, the successful development of a new welding technique for joining steel to stainless steel represents a significant achievement for {}. This breakthrough not only demonstrates the company's technical prowess and innovation but also signifies its commitment to pushing the boundaries of what is possible in the manufacturing industry. As {} continues to lead the way in welding technology, it is poised to make a lasting impact on the industry and drive the creation of high-quality, durable products for years to come.
Company News & Blog
Mastering the Art of Tig Welding for Mild Steel: A Comprehensive Guide
Tig Welding Mild Steel: A Versatile and Reliable Solution for Various IndustriesIntroduction:In today's fast-paced and demanding industrial landscape, welding plays a crucial role in constructing and fabricating various structures. Welding processes have come a long way, evolving to suit different materials and industry requirements. One such process is Tungsten Inert Gas (TIG) welding, renowned for its precision and versatility.Brands like {} have been at the forefront of delivering exceptional TIG welding solutions. By combining cutting-edge technology with innovative engineering, they have become a trusted name in the industry. Offering a wide range of products and services, the brand has been instrumental in ensuring high-quality welds and enhancing productivity for numerous industries.TIG Welding Mild Steel:Mild steel is one of the most commonly used materials in the fabrication industry due to its affordability, availability, and ease of manipulation. TIG welding mild steel, using the right equipment and techniques, ensures strong and aesthetically pleasing welds.The TIG welding process relies on a non-consumable tungsten electrode to produce the weld, while an inert gas, such as argon, shields the weld area from atmospheric contamination. The ability to control heat input during TIG welding allows for precise welds, making it an ideal choice for mild steel applications.Key Advantages of TIG Welding Mild Steel:1. High-quality welds: TIG welding mild steel offers superior control over the heat input, resulting in high-quality welds with minimal distortion. This makes it suitable for applications that require a flawless finish, such as automotive components, furniture, and architectural structures.2. Versatility: TIG welding is compatible with a wide range of mild steel thicknesses, making it a versatile solution for various applications. From thin sheet metal to thicker structural components, TIG welding can handle it all with precision and ease.3. Clean and aesthetically pleasing welds: The TIG welding process produces clean and visually appealing welds, making it highly sought after in industries where aesthetics matter. This makes it an excellent choice for applications in the food and beverage industry, where hygiene and appearance are paramount.4. Reduced post-weld cleaning: TIG welding creates minimal spatter and produces very little smoke, reducing the need for extensive post-weld cleaning. This saves precious time and resources, enhancing productivity and efficiency in the welding process.Application of TIG Welding Mild Steel:The versatility of TIG welding mild steel makes it suitable for a wide range of industries and applications. Some notable applications include:1. Automotive and transportation: TIG welding is commonly used in the automotive industry for manufacturing exhaust systems, chassis components, and body panels. The precision and control offered by TIG welding ensure durable welds, crucial for the safety and performance of vehicles.2. Construction and infrastructure: TIG welding mild steel plays a vital role in the construction industry, where it is used for fabricating structural components, staircases, and fencing. The ability to produce aesthetically pleasing welds makes TIG welding a preferred choice in architectural applications.3. Food and beverage industry: Stainless steel is a popular choice in the food and beverage industry due to its corrosion resistance and ease of cleaning. TIG welding mild steel is often utilized to weld stainless steel components such as tanks, piping, and equipment, ensuring hygiene and quality standards are met.Conclusion:In conclusion, TIG welding mild steel continues to be a versatile and reliable solution for various industries. With brands like {} leading the way in delivering high-quality TIG welding equipment and services, industries can rely on this process for precise welds, enhanced productivity, and aesthetic appeal. From automotive to construction and food and beverage sectors, TIG welding mild steel offers a range of applications, making it an invaluable tool for fabricators and manufacturers worldwide.
High-Quality Steel and Fabrication Services for Commercial and Residential Projects
Steel And Fabrication Company Celebrates 20 Years of Excellence in Fabrication and Manufacturing[Company Name] is a leading steel and fabrication company that has been providing top-notch services in the fabrication and manufacturing industry for the past 20 years. The company has a proven track record of delivering high-quality products and exceptional customer service, making them a trusted and reliable partner for businesses across various industries.Founded in 2001, [Company Name] has steadily grown to become a powerhouse in the fabrication and manufacturing sector. With a state-of-the-art facility and a team of highly skilled and experienced professionals, the company has the capabilities to handle projects of all sizes and complexities. From custom steel fabrication to heavy equipment manufacturing, [Company Name] offers a wide range of services to cater to the diverse needs of its clients.Over the years, [Company Name] has built a solid reputation for consistently delivering superior products and services. The company is committed to upholding the highest standards of quality and precision in its work, ensuring that every project is completed to perfection. From concept to completion, [Company Name] works closely with its clients to understand their unique requirements and provide tailor-made solutions that exceed expectations.One of the key factors that sets [Company Name] apart from its competitors is its dedication to innovation and continuous improvement. The company invests heavily in cutting-edge technology and machinery to enhance its capabilities and stay ahead of industry trends. This commitment to innovation has enabled [Company Name] to tackle complex projects with efficiency and effectiveness, earning the trust and loyalty of its clients.In addition to its technical expertise, [Company Name] also prides itself on its unwavering commitment to safety and environmental sustainability. The company adheres to strict safety protocols and best practices to ensure the well-being of its employees and the preservation of the environment. By prioritizing safety and sustainability, [Company Name] demonstrates its responsibility as a corporate citizen and a steward of the community.As [Company Name] celebrates its 20th anniversary, the company looks back on its journey with a sense of pride and accomplishment. Over the years, [Company Name] has successfully completed a wide array of projects across different industries, from construction and infrastructure to oil and gas. The company's versatility and expertise have earned it a stellar reputation in the fabrication and manufacturing sector, positioning it as a preferred partner for leading businesses.Looking ahead, [Company Name] is poised for continued success and growth in the years to come. The company remains committed to delivering best-in-class products and services, upholding its core values of quality, integrity, and reliability. With a focus on innovation and customer satisfaction, [Company Name] is well-equipped to meet the evolving needs of the market and set new benchmarks for excellence in the fabrication and manufacturing industry.In conclusion, [Company Name] has emerged as a force to be reckoned with in the fabrication and manufacturing sector, and its 20th anniversary is a testament to its unwavering dedication and success. As the company continues to thrive and expand its horizons, it remains a trusted partner for businesses seeking top-quality solutions in steel fabrication and manufacturing. Congratulations to [Company Name] on this remarkable milestone, and here's to many more years of excellence and achievement.
Top 5 Custom Metal Cutting Techniques for Precision Results
Custom Metal Cutting Company Delivers Innovative Solutions for Precision ManufacturingCustom Metal Cutting Company is proud to announce the launch of their new state-of-the-art facility, offering custom precision metal cutting services for a wide range of industries. With over 20 years of experience in the industry, Custom Metal Cutting Company is dedicated to providing high-quality, cost-effective solutions that meet the unique needs of their clients.Specializing in precision metal cutting, the company utilizes advanced CNC machinery and cutting-edge technologies to deliver precise, accurate results. Their team of highly skilled engineers and technicians are committed to providing innovative solutions that exceed industry standards and customer expectations."We are thrilled to introduce our new facility, equipped with the latest technology and capabilities to meet the growing demand for precision metal cutting services," said the CEO of Custom Metal Cutting Company. "Our goal is to provide our customers with the highest quality products and superior customer service, while maintaining competitive pricing and lead times."Custom Metal Cutting Company offers a wide range of metal cutting services, including laser cutting, plasma cutting, waterjet cutting, and EDM wire cutting. Their capabilities allow for the cutting of various materials, including steel, aluminum, stainless steel, and titanium, among others. In addition to their cutting services, the company also provides value-added services such as deburring, tapping, and drilling to ensure that the final product meets the exact specifications of their clients.The company serves a diverse customer base, including the aerospace, automotive, medical, and defense industries, among others. Their commitment to quality, precision, and innovation has earned them a reputation as a trusted partner in the manufacturing and fabrication industry.With a relentless focus on continuous improvement and investing in the latest technologies, Custom Metal Cutting Company is positioned to meet the evolving needs of their customers and the industry as a whole. Their dedication to innovation and excellence has allowed them to stay ahead of the competition and maintain a strong presence in the market.In addition to their commitment to quality and technology, Custom Metal Cutting Company places a strong emphasis on environmental sustainability and corporate social responsibility. They adhere to the highest standards of environmental compliance and work to minimize their impact on the environment through responsible waste management and energy-efficient practices.As part of their commitment to their clients, the company offers personalized consultation and engineering support to help customers optimize their designs for manufacturability and cost-effectiveness. Their team of experts works closely with clients to understand their specific needs and provide tailored solutions that meet their unique requirements.The launch of their new facility marks an important milestone for Custom Metal Cutting Company, as they continue to expand their capabilities and position themselves as a leader in the precision metal cutting industry. With a relentless commitment to innovation, quality, and customer satisfaction, the company is well-equipped to address the evolving needs of their clients and deliver superior solutions for precision manufacturing.
How Laser Cutting is Revolutionizing Manufacturing Processes
Laser Plate Cutting: The Future of Precision ManufacturingIn our increasingly tech-savvy world, precision and accuracy have become more important than ever before. As such, precision manufacturing has taken center stage, with companies constantly seeking new and innovative ways to create perfect, intricate, and detailed products. One such innovation is laser plate cutting, a process that uses lasers to make precise cuts in a variety of materials. In this blog, we'll dive into the world of laser plate cutting and explore why it's the future of precision manufacturing.What is Laser Plate Cutting?Laser plate cutting is a process that uses a high-powered laser to cut through a variety of materials, including steel, aluminum, and other metals. The laser beam is directed at the material, creating a highly focused point of heat that melts or vaporizes the material in a precise and controlled manner. This process results in clean, sharp, and accurate cuts that are free of burrs or other imperfections.How Does Laser Plate Cutting Work?To understand how laser plate cutting works, it's helpful to understand how a laser works in the first place. A laser (which stands for Light Amplification by Stimulated Emission of Radiation) emits a highly concentrated beam of light that is focused on a small area. This beam is made up of photons, which are particles of light. When the photons hit a material, they transfer energy to it, causing it to heat up and melt or vaporize.In laser plate cutting, the laser beam is directed onto a plate of material using a series of mirrors and lenses. The laser can be adjusted to various settings, including power and speed, to ensure the most precise cut possible. The process can be automated using computer-controlled systems, which allows for even greater precision and speed.Benefits of Laser Plate CuttingSo why is laser plate cutting the future of precision manufacturing? There are several key benefits to the process that set it apart from other types of cutting:1. Precision and accuracy: Laser plate cutting allows for incredibly precise cuts that are free of burrs or other imperfections.2. Speed: Laser cutting is faster than many other cutting methods, which means that products can be created more quickly.3. Versatility: Laser cutting can be used on a wide range of materials, including metals, plastics, and even glass.4. Cost-effectiveness: Although laser plate cutting requires expensive equipment, it can ultimately save money in the long run by reducing waste and the need for additional finishing processes.Applications of Laser Plate CuttingLaser plate cutting has a wide range of applications across many industries. Here are just a few examples:1. Aerospace: Laser cutting is used to create precise components for aircraft engines, landing gear, and other systems.2. Automotive: Laser cutting is used to create parts for cars and trucks, including body panels, suspension components, and exhaust systems.3. Medical: Laser cutting is used to create surgical tools, implants, and other medical equipment that requires precision and accuracy.4. Technology: Laser cutting is used to create components for consumer electronics, such as smartphones and tablets.ConclusionIn conclusion, laser plate cutting is the future of precision manufacturing. With its ability to create precise, accurate cuts on a wide range of materials, laser cutting has become an essential tool for many industries. As technology continues to advance, we can expect to see even greater innovations in laser cutting, making it an even more important part of the manufacturing process. So if you're looking for the most precise and accurate cuts for your next project, consider laser plate cutting.
Key Tips for Structural Steel Welding to Ensure Strong and Reliable Connections
Structural Steel Welding: A Crucial Process in ConstructionIntroduction:Structural steel welding plays a critical role in the construction industry, ensuring the durability and stability of buildings, bridges, and other infrastructure projects. By joining pieces of steel together using specialized welding techniques, construction professionals can create strong and reliable structures capable of withstanding a range of challenging conditions.Steel is one of the most commonly used materials in construction due to its exceptional strength and durability. However, to harness its full potential, steel requires welding to create a solid and integrated structure. Many construction companies have utilized advanced welding processes and technologies to ensure the highest level of quality and safety in steel structures being built.The Importance of Structural Steel Welding:Structural steel welding is vital for several reasons. Firstly, it ensures the integrity of the structure by effectively joining steel beams, columns, and plates. Welding provides a secure connection that allows the load-bearing capacity of the steel to be maximized, making it an essential component in the construction industry.Additionally, welding enables architects and engineers to design complex and innovative structures. It allows for the creation of artistic and unique designs that may not be achievable with other construction materials. The flexibility and versatility of welding make it possible to construct intricate steel shapes, giving architects the freedom to explore their creativity while maintaining structural integrity.Moreover, structural steel welding ensures the longevity of a building or infrastructure project. By creating a solid bond between steel components, welding minimizes the risk of structural failure, enhancing the durability and lifespan of the structure. This is particularly crucial in high-demand sectors such as bridges, where welding plays a significant role in maintaining safety standards and preventing catastrophic accidents.Advanced Welding Technologies:In recent years, significant advancements have been made in welding techniques and technologies. These advancements have brought immense benefits to the construction industry, allowing for more efficient and precise welding processes.One notable technological development is the introduction of automated welding systems. These systems utilize robotics and computer-controlled machinery to perform welding tasks with higher precision and consistency. Automated welding not only reduces labor costs but also minimizes human error, resulting in stronger and more reliable welds.Furthermore, the emergence of laser welding has revolutionized the field of structural steel welding. Laser welding offers several advantages such as faster welding speeds, reduced heat input, and improved weld quality. It enables construction companies to achieve high-quality welds in less time, enhancing productivity without compromising on safety or durability.Safety and Quality Assurance:When it comes to structural steel welding, safety and quality assurance are paramount. Construction companies must adhere to strict industry standards and regulations to ensure the integrity of the welds and, ultimately, the entire structure.Inspection and quality assurance processes play a crucial role in verifying the quality of welds. Non-destructive testing methods, such as ultrasonic testing and X-ray inspection, are commonly employed to detect any potential defects in the welded joints. By identifying these defects early on, necessary repairs and modifications can be made, guaranteeing the reliability and safety of the structure.Moreover, certified welders with specialized training and skills are essential for executing structural steel welding. These professionals understand the complexities of different welding techniques and materials, ensuring that the welds meet the required strength and durability standards.Conclusion:Structural steel welding is an indispensable process in the construction industry, providing strength, durability, and safety to structures of all kinds. The advancements in welding technologies have significantly contributed to enhanced efficiency, precision, and overall project quality. However, it is crucial that construction companies prioritize safety and quality assurance through thorough inspection and employing certified welders. By doing so, they can ensure the longevity and reliability of the structures they build.
Discover the Benefits of Custom Fabrication and Welding Services
Custom Fabrication And Welding recently announced their expansion in the fabrication and welding industry, offering a wide range of services to meet the diverse needs of their clients. With their state-of-the-art equipment and highly skilled team, the company has positioned themselves as a leader in the industry, capable of providing customized solutions for a variety of projects.The company specializes in custom fabrication and welding, offering services such as metal cutting, bending, shaping, and welding. They have the capability to work with a variety of materials, including steel, aluminum, and stainless steel, and are able to create custom designs based on their clients' specifications.One of the key factors that sets Custom Fabrication And Welding apart from their competitors is their dedication to providing superior quality work. The company takes great pride in their craftsmanship, ensuring that each project is completed to the highest standards of excellence. They have implemented strict quality control measures to guarantee the durability and reliability of their products, making them a trusted name in the industry.In addition to their commitment to quality, Custom Fabrication And Welding is also known for their exceptional customer service. They work closely with their clients throughout the entire process, from the initial consultation to the final delivery of the project. Their team of experts is always available to address any questions or concerns, and they strive to exceed their clients' expectations with every project.This dedication to excellence has earned Custom Fabrication And Welding a strong reputation within the industry, and they have built long-lasting relationships with many satisfied clients. Their ability to deliver innovative solutions and meet tight deadlines has made them a preferred choice for businesses in need of custom fabrication and welding services.With their recent expansion, Custom Fabrication And Welding is now equipped to take on even larger and more complex projects. They have invested in advanced technology and equipment to further enhance their capabilities, allowing them to tackle a wider range of fabrication and welding requirements. This expansion will enable the company to continue meeting the evolving needs of their clients and maintain their position as a leading provider in the industry.The team at Custom Fabrication And Welding is excited about the opportunities that this expansion brings, and they are eager to take on new challenges and deliver exceptional results for their clients. They are confident that their expanded capabilities will allow them to continue exceeding expectations and solidify their position as a preferred partner for custom fabrication and welding solutions.As they move forward with their expansion, Custom Fabrication And Welding remains committed to their core values of quality, integrity, and customer satisfaction. They are dedicated to upholding the highest standards of professionalism and excellence in all aspects of their work, and they are poised to continue making a positive impact in the fabrication and welding industry.For businesses in need of custom fabrication and welding services, Custom Fabrication And Welding is a trusted partner that can deliver top-notch solutions tailored to their specific needs. With their extensive experience, advanced capabilities, and unwavering commitment to quality, the company is well-equipped to handle a wide range of projects and deliver exceptional results.
Discover the Best Bevel Angle for Plasma Cutting
Plasma Cutting Bevel Angle Technology: Revolutionizing the Metal Fabrication IndustryIn the world of metal fabrication, precision and efficiency are paramount. As demand for high-quality metal products continues to rise, companies are constantly searching for new technologies to streamline their processes and improve their end products. One such technology that is revolutionizing the industry is Plasma Cutting Bevel Angle.Plasma cutting is a process that uses a high-velocity jet of ionized gas to cut through electrically conductive materials. It is widely used in metal fabrication for its speed and precision. However, traditional plasma cutting methods are limited in the types of cuts they can produce, often requiring secondary processing to achieve beveled edges.This is where Plasma Cutting Bevel Angle technology comes in. By integrating advanced software and hardware capabilities, this cutting-edge technology allows for the production of beveled edges directly from the plasma cutting process, eliminating the need for secondary processing and significantly reducing production time and cost.One company at the forefront of this technology is {}. With a long history of innovation in the metal fabrication industry, {} has been a pioneer in the development and implementation of Plasma Cutting Bevel Angle technology. By combining their expertise in plasma cutting with state-of-the-art software and hardware solutions, they have been able to offer their clients a level of precision and efficiency that was previously unattainable.The key to the success of Plasma Cutting Bevel Angle technology lies in its ability to dynamically adjust the cutting angle in real time, allowing for the production of beveled edges with a high degree of accuracy. This not only saves time and money for metal fabricators, but also opens up new possibilities for the types of products that can be created.For example, in the automotive industry, where precision is crucial, Plasma Cutting Bevel Angle technology has enabled the production of complex components with beveled edges that would have been difficult or impossible to achieve with traditional plasma cutting methods. This has led to improved performance and aesthetics in the final products, giving companies a competitive edge in the market.In addition to its impact on the automotive industry, Plasma Cutting Bevel Angle technology has also found applications in aerospace, shipbuilding, and structural steel fabrication, among others. Its versatility and precision make it a valuable tool for any metal fabrication project, regardless of size or complexity.Furthermore, with the rise of digital manufacturing and the adoption of Industry 4.0 principles, Plasma Cutting Bevel Angle technology is poised to play a key role in the future of metal fabrication. Its integration with digital design and robotic systems offers new possibilities for automation and optimization of production processes, ultimately leading to higher quality products and faster time to market.As the demand for high-quality metal products continues to grow, the importance of advanced technologies like Plasma Cutting Bevel Angle cannot be overstated. With its ability to streamline production processes, improve product quality, and reduce costs, it is set to become a standard feature in the metal fabrication industry.In conclusion, Plasma Cutting Bevel Angle technology is revolutionizing the metal fabrication industry by offering a level of precision and efficiency that was previously unattainable. With its ability to produce beveled edges directly from the plasma cutting process, it is saving time and money for metal fabricators and opening up new possibilities for product design and manufacturing. As a pioneer in this technology, {} is leading the way in bringing this innovation to the market, setting new standards for the industry as a whole.
Top 5 Custom Metal Fabrication Services to Enhance Your Business
Custom Metal Fabrication Services has been providing top-quality metal fabrication services for over a decade. The company has carved a niche for itself in the industry thanks to its commitment to producing the highest-quality products for its clients, while staying up-to-date with the latest technologies and techniques.The company offers a wide range of custom metal fabrication services to businesses across various industries, including aerospace, automotive, food and beverage, and more. The team comprises highly-skilled and experienced fabricators that are passionate about delivering exceptional results."We are proud to offer our clients a wide range of custom metal fabrication services, each tailored to meet their specific needs," said a company representative. "We are committed to ensuring that our clients get the best possible results, and we are relentless in our pursuit of excellence."Custom Metal Fabrication Services utilizes the latest technologies and materials to produce products that meet the highest-quality standards. They specialize in working with a variety of materials, including carbon steel, aluminum, stainless steel, and more.The company offers a range of services that includes designing, prototyping, manufacturing, finishing, and installation. They work closely with their clients throughout the entire process, ensuring that their unique needs are met and that their expectations are exceeded.At Custom Metal Fabrication Services, quality is of utmost importance. The company has a comprehensive quality control process in place, which ensures that every product that leaves their facility meets the required quality standards. Every project is carefully monitored and tested to ensure that it meets the client's specific requirements.The company's commitment to quality has earned them a reputation as a trusted provider of custom metal fabrication services. Clients can always count on them to deliver exceptional results on time and within budget.In addition to providing high-quality metal fabrication services, Custom Metal Fabrication Services is also committed to providing exceptional customer service. Their team is always available to assist clients throughout the entire process, from the initial consultation to the final installation."We understand that our clients have unique needs, and we are always willing to go above and beyond to ensure that those needs are met," said the company representative. "Our team is passionate about what we do, and we are committed to delivering outstanding results and exceptional customer service, every time."Custom Metal Fabrication Services has invested heavily in the latest technologies and equipment to ensure that they stay ahead of the curve in the metal fabrication industry. They are constantly exploring new ways to improve their processes and techniques to deliver the best possible results for their clients.Whether it's a small or large project, Custom Metal Fabrication Services is equipped to handle it. They have the resources, skills, and experience necessary to take on any project, from simple designs to complex custom fabrications.In conclusion, Custom Metal Fabrication Services is a premier provider of custom metal fabrication services. Their commitment to quality, exceptional customer service, and staying up-to-date with the latest technologies and techniques has earned them a reputation as a trusted provider in the industry. Businesses looking for top-quality metal fabrication services can count on Custom Metal Fabrication Services to deliver the results they need.
Professional Tube Bending and Rolling Services for Various Materials
Aluminum Bending Services Meet Growing Demands for Customized FabricationIn response to the increasing demand for specialized fabrication solutions, industry-leading tube bending and rolling experts have expanded their services to include aluminum bending. As aluminum continues to gain popularity in a wide range of industries, these specialized services offer a cost-effective and efficient solution for creating custom-designed products and structures.MetzFab, a renowned provider of tube bending and rolling services, has recently expanded its capabilities to include aluminum bending. With their expertise and state-of-the-art equipment, MetzFab is now capable of working with a variety of materials, including steel, stainless steel, and aluminum.Aluminum has become a sought-after material for its exceptional versatility, strength, and lightweight properties. It is widely used across a range of industries, including aerospace, automotive, construction, and marine, to name just a few. By offering aluminum bending services, MetzFab is dedicated to meeting the ever-growing demands of these industries and providing them with customized fabrication solutions.MetzFab's aluminum bending services utilize advanced bending machinery and techniques to create precise and complex shapes. The company's skilled technicians are experienced in handling the unique properties of aluminum, ensuring high-quality results and minimizing material waste. Whether it's a simple bend or a complex multi-plane shape, MetzFab's aluminum bending services can meet the needs of any project.One of the key advantages of aluminum bending services is the cost-effectiveness it offers compared to traditional fabrication methods. With the ability to create intricate shapes and designs, aluminum bending reduces the need for additional parts and assembly, resulting in significant cost savings. Additionally, aluminum's lightweight nature reduces transportation costs and makes it easier to handle during installation.MetzFab's aluminum bending services also offer exceptional durability and corrosion resistance. Aluminum naturally forms a protective oxide layer, making it highly resistant to rust and corrosion. This makes it an ideal choice for outdoor applications and industries that require high strength and longevity. With their precise bending techniques, the company ensures that the integrity of the aluminum is maintained, providing customers with long-lasting and reliable products.The versatility of aluminum bending extends to a wide range of applications. In the aerospace industry, aluminum's lightweight properties are crucial for reducing fuel consumption and increasing aircraft efficiency. MetzFab's aluminum bending services can create intricate shapes for aircraft frames, fuselages, and other components, ensuring optimal performance and safety.In the automotive sector, aluminum bending enables the production of lightweight and fuel-efficient vehicles. By reducing the weight of car bodies and structures, manufacturers can improve fuel economy without compromising safety. MetzFab's aluminum bending services can contribute to this industry's goal of sustainability and environmental responsibility.In the construction and architectural industries, aluminum bending allows for the creation of unique and aesthetically pleasing structures. From curved facades to custom-designed staircases, aluminum bending provides architects and designers with unparalleled creative possibilities. MetzFab's expertise in aluminum bending ensures that these structures are not only visually appealing but also structurally sound.MetzFab's expansion into aluminum bending services highlights their commitment to meeting the changing needs of various industries. With their expertise, state-of-the-art equipment, and dedication to quality, they are well-positioned to provide customized fabrication solutions that meet and exceed customer expectations. Whether it's steel, stainless steel, or aluminum, MetzFab's tube bending and rolling services are a reliable choice for all materials.
How to Plasma Cut Stainless Steel Using Nitrogen Gas
Plasma Cutting Stainless Steel With Nitrogen: A New Era of Precision ManufacturingManufacturing precision components has always been a challenging task, requiring highly specialized equipment and skilled workers. To meet market demands, manufacturing companies are constantly seeking new and innovative methods to improve production efficiency and maintain the highest standards of quality. One such method is plasma cutting with nitrogen, a cutting-edge technology that has revolutionized the way in which stainless steel components are manufactured. Here, we explore the latest developments in the field of plasma cutting with nitrogen, its advantages, and the companies that are leading the way.What is Plasma Cutting with Nitrogen?Plasma cutting is a technique used to cut materials, such as metals, using a high-temperature plasma arc. It works by passing an electrical current through a gas, such as oxygen or nitrogen, to generate a plasma arc that can melt through metal. By manipulating the arc's intensity and jet's velocity, the operator can control the quality of the cut and ensure a fine finish. Plasma cutting is widely used in metal fabrication as it allows the creation of intricate shapes and designs in a variety of materials, including stainless steel.Specifically, plasma cutting with nitrogen is a process that uses pure nitrogen gas as the cutting medium. Compared to plasma cutting with oxygen, nitrogen provides a cleaner cut and minimizes the risk of oxidation or discoloration of the cut edge. Because nitrogen is an inert gas, it also creates a safer working environment for operators and reduces the risk of fire.Advantages of Plasma Cutting with NitrogenThe benefits of cutting stainless steel with plasma and nitrogen are numerous. Firstly, the process can handle stainless steel's high reflective nature and thicker gauge metals. Secondly, the method can boost productivity while reducing waste by limiting aspects like kerf width and dross production. The cleaner cuts and minimal bevel make for faster removal of excess material and the ability to reduce labor-intensive grinding and cleaning. Cutting with nitrogen produces minimal thermal distortion, ensuring the final parts maintain tight tolerances.The process is also highly flexible, allowing workers to cut shapes or designs on a customer's request with relative ease. With this technique, the cutting's quality, accuracy, and finish are impeccable every single time. And since nitrogen is a non-reactive gas, the risk of oxidization, warping, or disfigurement of the metal is eliminated. This reduces the chances of rework, saving both time and money.Companies Making Strides In Plasma Cutting With NitrogenOne of the enterprises making significant strides in plasma cutting with nitrogen is {Unnamed company}. Founded in {year}, this young company has established itself as a leading player in the precision manufacturing industry. With the mission of providing the highest quality metal cutting services, the company has invested in the latest equipment and technology to stay ahead of the curve.To that end, the company has adopted plasma cutting techniques with nitrogen to achieve unparalleled precision and quality in its metal fabrication processes. Equipped with a state-of-the-art CNC machine, the company can cut intricate shapes and designs into stainless steel with remarkable accuracy and speed. With such precision, the company can fulfill custom orders on a tight schedule while maintaining exceptional quality.{Unnamed company} is also renowned for investing in its people. They employ a team of highly skilled technicians who remain dedicated to the company's philosophy by delivering high-quality products and services to customers. Committed to innovation, they seek to leverage the latest techniques and technology to enhance their services, continually pushing the boundaries of what's possible.Final ThoughtsWithout a doubt, plasma cutting with nitrogen is an innovative manufacturing process that has revolutionized the world of metal cutting. Stainless steel, a notoriously difficult material to cut, has become easier to manage and meet the precision demands. Thanks to this method's accuracy, speed, and superior quality finishes, manufacturers are now capable of delivering precision components that are beyond excellence. As for {Unnamed company}, this forward-thinking enterprise is leading the way in this manufacturing process, continually seeking to refine its services for the benefit of its customers. When it comes to plasma cutting with nitrogen, there’s no doubt that the future remains bright.