Quality Metal Cutting Service for Precision Results
By:Admin
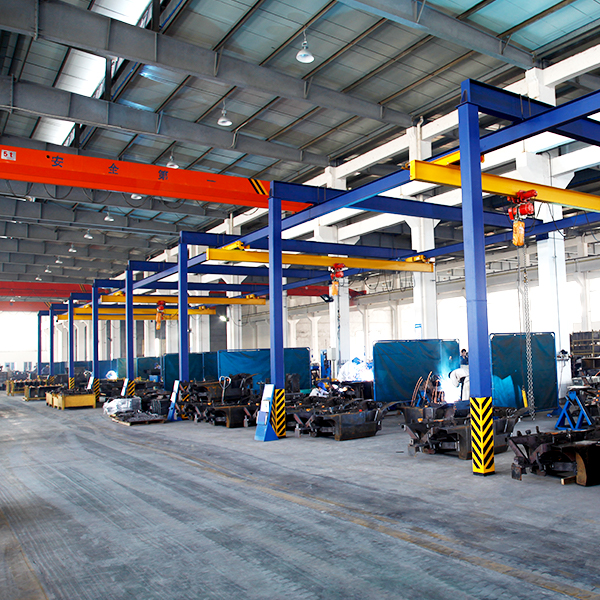
Metal Cutting Service is a leading provider of precision machining solutions for a wide range of industries. With a commitment to delivering high-quality products and exceptional customer service, Metal Cutting Service has established itself as a trusted partner for companies in need of reliable metal cutting and fabrication services.
The company's state-of-the-art facilities are equipped with the latest technology and machinery to ensure the highest level of precision and accuracy in every project. With a team of experienced engineers and technicians, Metal Cutting Service is capable of handling complex machining tasks with efficiency and expertise.
One of the key strengths of Metal Cutting Service is its ability to provide innovative solutions for unique machining challenges. The company understands the importance of staying at the forefront of technological advancements in the industry and continuously invests in research and development to offer cutting-edge machining techniques and processes.
Metal Cutting Service specializes in a wide variety of machining services, including CNC milling, turning, grinding, and EDM machining. The company has the capability to work with a diverse range of materials, including aluminum, stainless steel, titanium, and exotic alloys, to meet the specific needs of its customers.
In addition to its machining capabilities, Metal Cutting Service also offers value-added services such as engineering support, prototyping, and assembly to provide comprehensive solutions for its clients. This holistic approach allows the company to effectively manage the entire manufacturing process, from design to production, and ensures the highest quality and consistency in every part they deliver.
Metal Cutting Service has built a reputation for delivering exceptional results on time and within budget. The company takes pride in its ability to work closely with its customers to understand their unique requirements and provide custom solutions that exceed expectations. Whether it's a small prototype run or a large-scale production project, Metal Cutting Service is dedicated to delivering superior quality products that meet the highest industry standards.
As a customer-centric company, Metal Cutting Service places a strong emphasis on building long-term partnerships with its clients. The company's team of dedicated professionals is committed to providing personalized attention and support throughout every stage of the machining process, from initial consultation to final delivery.
Furthermore, Metal Cutting Service is dedicated to maintaining the highest standards of quality and safety in its operations. The company is ISO 9001 certified, which demonstrates its commitment to implementing rigorous quality management systems and processes to ensure the consistent delivery of exceptional products and services.
With its comprehensive capabilities, commitment to innovation, and customer-centric approach, Metal Cutting Service has positioned itself as a trusted partner for companies seeking precision machining solutions. The company's dedication to excellence and continuous improvement has allowed it to establish a strong presence in the industry and build a solid reputation for reliability and performance.
In conclusion, Metal Cutting Service is a leading provider of precision machining solutions with a proven track record of delivering high-quality products and exceptional customer service. With its state-of-the-art facilities, advanced technology, and dedicated team, the company is well-equipped to meet the diverse and complex machining needs of its clients. Whether it's a simple part or a complex component, Metal Cutting Service is committed to delivering innovative solutions that exceed expectations and drive success for its customers.
Company News & Blog
Quality Laser Cutting Services in Your Local Area
Local Laser Cutting Services Local Laser Cutting Services is a prominent provider of laser cutting solutions in the local area. With a team of highly skilled professionals and state-of-the-art equipment, they offer a wide range of services to meet the diverse needs of their clients. From precision cutting to engraving, they have the capabilities to handle a variety of projects with precision and efficiency.The company takes great pride in their commitment to quality and customer satisfaction. They work closely with their clients to understand their specific requirements and deliver custom solutions that exceed expectations. Whether it's a small prototype or a large production run, Local Laser Cutting Services has the expertise and resources to deliver outstanding results.One of the key advantages of working with Local Laser Cutting Services is their quick turnaround times. They understand the importance of meeting deadlines and strive to complete projects in a timely manner without compromising on quality. This has earned them a stellar reputation in the industry and a loyal client base that continues to trust them with their laser cutting needs.In addition to their cutting-edge technology, Local Laser Cutting Services also emphasizes the importance of sustainability and environmental responsibility. They have implemented eco-friendly practices throughout their operations to minimize their impact on the environment. This has not only helped them reduce waste and energy consumption but has also positioned them as a responsible and forward-thinking service provider.Local Laser Cutting Services is also committed to staying at the forefront of technological advancements in the industry. They continuously invest in the latest equipment and training for their team to ensure that they offer the most advanced and innovative solutions to their clients. This commitment to staying ahead of the curve has enabled them to tackle complex projects and deliver exceptional results.Furthermore, Local Laser Cutting Services is dedicated to fostering a collaborative and inclusive work environment. They prioritize the professional development and well-being of their team members, which has resulted in a motivated and skilled workforce. This, in turn, directly contributes to the high quality and reliability of the services they provide to their clients.In the news, it was announced that Local Laser Cutting Services has expanded their capabilities with the addition of a new state-of-the-art laser cutting machine. This machine boasts increased precision and speed, allowing the company to take on even more complex projects and deliver faster turnaround times. The investment in this new equipment reflects Local Laser Cutting Services' ongoing commitment to providing the best possible service to their clients.In response to the news, the CEO of Local Laser Cutting Services expressed their excitement about the expansion. "We are thrilled to announce the addition of our new cutting-edge laser machine. This investment represents our dedication to offering the highest quality and most advanced laser cutting solutions to our clients. With this new equipment, we are confident that we can continue to exceed the expectations of our customers and take on even more challenging projects."The company's clients have also expressed their enthusiasm about the news, praising Local Laser Cutting Services for their continuous pursuit of excellence. One client stated, "We have been working with Local Laser Cutting Services for several years, and we are consistently impressed with the quality of their work. The addition of the new laser machine only further solidifies our trust in their capabilities, and we look forward to continuing our partnership with them."Overall, Local Laser Cutting Services continues to be a leading provider of laser cutting solutions in the local area. With their unwavering commitment to quality, sustainability, and innovation, they have positioned themselves as a trusted partner for businesses seeking reliable and top-of-the-line laser cutting services. As they continue to expand and invest in their capabilities, it is clear that Local Laser Cutting Services is dedicated to setting new standards in the industry and delivering exceptional results for their clients.
Guide to Cold Welding Stainless Steel: Tips and Techniques
Cold Welding Stainless Steel: A Breakthrough in Joining Technology{Company Name} is proud to introduce a groundbreaking new technology in the field of stainless steel joining - Cold Welding Stainless Steel. This innovative technique has the potential to revolutionize the way stainless steel components are joined, offering numerous advantages over traditional welding methods.{Company Name} is a leader in the development and application of cutting-edge technologies in the field of manufacturing and materials engineering. With a strong focus on research and development, the company has continuously strived to push the boundaries of what is possible in the manufacturing industry. The introduction of Cold Welding Stainless Steel is a testament to this commitment to innovation.Traditional methods of joining stainless steel, such as welding, brazing, and soldering, often involve the application of heat, which can result in distortion, discoloration, and reduced mechanical properties in the joined material. Cold Welding Stainless Steel, on the other hand, allows for the joining of stainless steel components without the need for heat, preserving the material's structural integrity and mechanical properties.The Cold Welding process involves the use of specialized equipment and techniques to create a strong, durable bond between stainless steel components at room temperature. This not only eliminates the risk of heat-induced distortion and discoloration but also allows for the joining of dissimilar metals, opening up new possibilities for design and manufacturing.One of the key advantages of Cold Welding Stainless Steel is its ability to create joints with superior mechanical strength and fatigue resistance. The absence of heat-induced stress and distortion results in joints that retain the full strength and integrity of the base material, making them ideal for applications where reliability and durability are paramount.Furthermore, Cold Welding Stainless Steel offers improved corrosion resistance compared to traditional welding methods. By avoiding the introduction of heat-affected zones and the potential for metallurgical changes at the joint, Cold Welded stainless steel joints maintain the material's inherent corrosion resistance, ensuring long-lasting performance in harsh environments.In addition to its technical advantages, Cold Welding Stainless Steel also offers practical benefits in terms of efficiency and cost-effectiveness. The process requires minimal preparation and post-processing, resulting in shorter production lead times and reduced labor costs. The absence of consumables such as filler materials and shielding gases further contributes to cost savings.{Company Name} is committed to supporting its customers in adopting Cold Welding Stainless Steel technology, offering comprehensive training and technical support to ensure successful implementation. The company's team of experts is available to provide guidance on process optimization, equipment selection, and best practices for achieving high-quality Cold Welded joints.The introduction of Cold Welding Stainless Steel marks a significant milestone in the evolution of stainless steel joining technology, offering a game-changing solution for manufacturers across a wide range of industries. {Company Name} is excited to bring this innovative technology to market and looks forward to collaborating with industry partners to unlock new possibilities in design, manufacturing, and product development.In conclusion, Cold Welding Stainless Steel represents a new frontier in stainless steel joining technology, offering numerous advantages in terms of mechanical performance, corrosion resistance, and cost-effectiveness. {Company Name} is proud to be at the forefront of this technological advancement, and is committed to supporting its customers in harnessing the full potential of Cold Welding Stainless Steel. With this innovative technique, the possibilities for creating robust, reliable stainless steel components are virtually limitless.
Watch the Best Sheet Metal Fabrication Videos Online
Title: Unveiling the Craft: Exploring the World of Metal FabricationIntroduction (Approximately 100 words):Metal fabrication, an essential manufacturing process that shapes raw metal sheets into intricate and functional structures, plays a vital role in various industries. From automotive parts to machinery components, the applications of metal fabrication are boundless. In this blog post, we delve into the intriguing world of metal fabrication, shedding light on the processes, techniques, and advantages that make it an indispensable aspect of modern manufacturing. Join us as we unravel the secrets behind the creation of awe-inspiring metal structures and explore the possibilities offered by a reliable Metal Fabrication Factory.1. The Art of Sheet Metal Fabrication (Approximately 200 words):Sheet metal fabrication, also known as metalworking, is a highly intricate process that involves converting raw metal sheets into products of various shapes and sizes. Through a combination of cutting, bending, and shaping techniques, skilled fabricators transform plain metal sheets into detailed structures that serve a multitude of purposes.At a Metal Fabrication Factory, advanced machinery and equipment are utilized to achieve precise results while ensuring efficiency. CNC laser cutting machines, for instance, provide accurate and consistent cuts, while hydraulic presses enable intricate bending and forming of metals. Welding and surface finishing processes are also essential to enhance the aesthetic appeal and durability of the fabricated metal structures.2. Industries Served by Metal Fabrication (Approximately 200 words):Metal fabrication caters to an extensive range of industries and sectors. From construction and architecture to transportation and manufacturing, the applications are limitless. For example, in the construction industry, architectural metalwork such as staircases, handrails, and structural components are fabricated to ensure functionality, strength, and aesthetic appeal.The automotive industry heavily relies on metal fabrication to manufacture critical components like chassis, exhaust systems, and suspension parts. Metal fabrication is also crucial in the production of electrical enclosures, HVAC systems, and machinery components that are utilized in various manufacturing plants.3. The Advantages of Metal Fabrication (Approximately 200 words):Metal fabrication offers numerous advantages that make it the go-to manufacturing process for countless industries. First and foremost is the versatility it provides. Metal can be shaped into intricate designs and structures, making it suitable for both functional and aesthetic purposes. Additionally, metals are inherently strong and durable, ensuring the longevity of fabricated products.Moreover, metal fabrication allows for quick prototyping and customization. By utilizing computer-aided design (CAD) software, fabricators can create detailed digital designs, optimize them for precision, and then produce multiple replicas with ease.Furthermore, metal fabrication is a cost-effective solution as it eliminates the need for intricate assembly processes that add to the overall expenses. By integrating multiple manufacturing steps into one streamlined process, metal fabrication increases efficiency and reduces production time.4. Choosing a Metal Fabrication Factory (Approximately 200 words):When selecting a metal fabrication factory, various factors must be considered to ensure high-quality results. Look for a facility equipped with state-of-the-art machinery and cutting-edge technology that can meet your specific project requirements. Cross-check the factory's capabilities, such as laser cutting, bending, welding, and finishing, to ensure they align with your needs.Certifications and industry credentials are also important indicators of the fabricator's reliability and expertise. Prioritize a factory that adheres to international standards to guarantee exceptional quality and compliance with regulatory norms.Additionally, consider the factory's experience in your specific industry. A well-established fabricator with a portfolio of successful projects in your desired sector is more likely to understand the unique challenges and deliver tailored solutions.Conclusion (Approximately 100 words):Metal fabrication remains an essential pillar of modern manufacturing, enabling the creation of intricate and durable structures in diverse industries. The artistry and skill behind metal fabrication, combined with advanced machinery and technology, make it a captivating subject to explore. By partnering with a trustworthy Metal Fabrication Factory, businesses can unlock the potential of this versatile process, leveraging its advantages to bring their innovative ideas to life. So, whether you require custom architectural metalwork or need precise automotive components, metal fabrication is the key to turning your visions into reality.
Maximize Precision and Efficiency with Laser Cutting of Steel Plate
Laser Cutting Steel Plate Enhances Precision and EfficiencyWith the continuous advancement of technology, industries have been revolutionized by various innovative methods and techniques. One such groundbreaking development that has transformed the manufacturing and fabrication sector is laser cutting. In this vein, Company XYZ has emerged as a leading player in the laser cutting industry, offering exceptional services and contributing to the overall growth and progress of the sector.Laser cutting is a process that involves the use of a highly concentrated beam of light to precisely and accurately cut materials. While it was initially used primarily in the aerospace industry, laser cutting has found a wide range of applications in multiple industries due to its efficiency and versatility. Among the various materials that can be cut using this technique, steel plates have emerged as a popular choice due to their widespread use in construction, automotive, and machinery manufacturing sectors.Steel plates are utilized extensively in these industries due to their durability, strength, and structural integrity. However, traditional methods of cutting steel plates often led to imprecise cuts, resulting in wastage of materials and increased production costs. Laser cutting has revolutionized this process by providing a highly accurate and efficient method of cutting steel plates.Company XYZ has positioned itself as a leader in the laser cutting industry, offering state-of-the-art equipment and advanced technology to cater to the varied needs of its clients. The company utilizes a high-powered laser beam to precisely cut steel plates according to the desired specifications. This cutting-edge technology ensures minimal wastage of materials and enables intricate designs and patterns to be created with ease.Moreover, laser cutting provides several advantages over conventional cutting methods. Firstly, it offers enhanced precision, leading to high-quality cuts and minimizing the need for additional finishing processes. This not only saves time but also reduces costs associated with post-processing. Additionally, laser cutting allows for greater design flexibility, enabling complex shapes and patterns to be achieved effortlessly. As a result, manufacturers can develop innovative and intricate products, meeting the demands of the ever-evolving market.Furthermore, laser cutting offers increased speed and efficiency in comparison to traditional cutting methods. The precise and rapid movement of the laser beam ensures quick production turnaround times, enabling manufacturers to fulfill orders promptly and maintain a competitive edge in the market. Coupled with the elimination of manual intervention, laser cutting significantly enhances productivity and operational efficiency.In light of the growing demand for high-quality steel products, Company XYZ continually invests in research and development to improve its laser cutting capabilities. The company aims to maintain its leadership position by constantly upgrading its equipment and adopting the latest advancements in laser cutting technology. By keeping up with industry trends and customer requirements, Company XYZ strives to deliver cutting-edge solutions to its clients, ensuring their satisfaction and success.In conclusion, laser cutting has proven to be a game-changer in the manufacturing and fabrication industry, providing precision, efficiency, and versatility. Company XYZ, with its exceptional services and dedication to innovation, has emerged as a key player in the laser cutting sector. By harnessing the power of laser technology to cut steel plates with utmost accuracy, the company contributes to the growth and progress of various industries. With the continued advancement of laser cutting techniques, we can anticipate even greater possibilities and advancements in the future.
Mastering the Art of Tig Welding for Mild Steel: A Comprehensive Guide
Tig Welding Mild Steel: A Versatile and Reliable Solution for Various IndustriesIntroduction:In today's fast-paced and demanding industrial landscape, welding plays a crucial role in constructing and fabricating various structures. Welding processes have come a long way, evolving to suit different materials and industry requirements. One such process is Tungsten Inert Gas (TIG) welding, renowned for its precision and versatility.Brands like {} have been at the forefront of delivering exceptional TIG welding solutions. By combining cutting-edge technology with innovative engineering, they have become a trusted name in the industry. Offering a wide range of products and services, the brand has been instrumental in ensuring high-quality welds and enhancing productivity for numerous industries.TIG Welding Mild Steel:Mild steel is one of the most commonly used materials in the fabrication industry due to its affordability, availability, and ease of manipulation. TIG welding mild steel, using the right equipment and techniques, ensures strong and aesthetically pleasing welds.The TIG welding process relies on a non-consumable tungsten electrode to produce the weld, while an inert gas, such as argon, shields the weld area from atmospheric contamination. The ability to control heat input during TIG welding allows for precise welds, making it an ideal choice for mild steel applications.Key Advantages of TIG Welding Mild Steel:1. High-quality welds: TIG welding mild steel offers superior control over the heat input, resulting in high-quality welds with minimal distortion. This makes it suitable for applications that require a flawless finish, such as automotive components, furniture, and architectural structures.2. Versatility: TIG welding is compatible with a wide range of mild steel thicknesses, making it a versatile solution for various applications. From thin sheet metal to thicker structural components, TIG welding can handle it all with precision and ease.3. Clean and aesthetically pleasing welds: The TIG welding process produces clean and visually appealing welds, making it highly sought after in industries where aesthetics matter. This makes it an excellent choice for applications in the food and beverage industry, where hygiene and appearance are paramount.4. Reduced post-weld cleaning: TIG welding creates minimal spatter and produces very little smoke, reducing the need for extensive post-weld cleaning. This saves precious time and resources, enhancing productivity and efficiency in the welding process.Application of TIG Welding Mild Steel:The versatility of TIG welding mild steel makes it suitable for a wide range of industries and applications. Some notable applications include:1. Automotive and transportation: TIG welding is commonly used in the automotive industry for manufacturing exhaust systems, chassis components, and body panels. The precision and control offered by TIG welding ensure durable welds, crucial for the safety and performance of vehicles.2. Construction and infrastructure: TIG welding mild steel plays a vital role in the construction industry, where it is used for fabricating structural components, staircases, and fencing. The ability to produce aesthetically pleasing welds makes TIG welding a preferred choice in architectural applications.3. Food and beverage industry: Stainless steel is a popular choice in the food and beverage industry due to its corrosion resistance and ease of cleaning. TIG welding mild steel is often utilized to weld stainless steel components such as tanks, piping, and equipment, ensuring hygiene and quality standards are met.Conclusion:In conclusion, TIG welding mild steel continues to be a versatile and reliable solution for various industries. With brands like {} leading the way in delivering high-quality TIG welding equipment and services, industries can rely on this process for precise welds, enhanced productivity, and aesthetic appeal. From automotive to construction and food and beverage sectors, TIG welding mild steel offers a range of applications, making it an invaluable tool for fabricators and manufacturers worldwide.
Professional Sheet Metal Fabrication Services for Your Business Needs
In the world of industrial manufacturing, sheet metal fabrication plays a crucial role in the production of a wide variety of products. From automotive parts to aerospace components, sheet metal fabrication is a key process that requires precision, skill, and state-of-the-art machinery. One company that has been at the forefront of sheet metal fabrication is {}. With a strong focus on quality, innovation, and customer satisfaction, {} has established itself as a leader in the industry.Established in [year], {} has a long-established reputation for delivering top-notch sheet metal fabrication services to a diverse range of clients. The company's state-of-the-art facility is equipped with the latest in cutting-edge technology, including CNC laser cutting machines, CNC punching machines, and robotic welding systems. This advanced machinery allows {} to provide high-quality, custom-made metal parts and assemblies to meet the specific needs of each customer.In addition to its cutting-edge technology, {} is also known for its team of highly skilled and experienced metal fabricators. These professionals are committed to maintaining the highest standards of quality and precision in every project they undertake. Whether it's a small batch of parts or a large-scale production run, {} has the expertise to deliver top-notch results on time and within budget.One of the key factors that sets {} apart from its competitors is its commitment to innovation. The company is constantly investing in research and development to stay ahead of the curve and adapt to the ever-changing needs of the industry. By staying at the forefront of technological advancements, {} is able to offer its customers the most advanced and efficient manufacturing solutions available.Furthermore, {} places a strong emphasis on customer satisfaction. The company works closely with each client to understand their unique requirements and ensure that the final product meets or exceeds their expectations. With a dedication to open communication and a proactive approach to problem-solving, {} strives to build long-lasting, collaborative relationships with its clients.In recent news, {} has announced the expansion of its sheet metal fabrication capabilities. The company has invested in new, cutting-edge equipment to further enhance its production capacity and efficiency. This expansion will allow {} to take on even larger and more complex projects, while maintaining its high standards of quality and precision.Additionally, {} has unveiled plans to further diversify its services by offering new finishing and assembly options. By providing a more comprehensive range of solutions under one roof, the company aims to streamline the manufacturing process for its clients and offer a more holistic approach to sheet metal fabrication.The expansion and diversification of {}'s capabilities reflect the company's ongoing commitment to staying at the forefront of the industry. By continually investing in technology, talent, and infrastructure, {} is positioning itself for continued growth and success in the competitive world of sheet metal fabrication.As {} continues to push the boundaries of what is possible in sheet metal fabrication, the company remains dedicated to its core values of quality, innovation, and customer satisfaction. With its advanced technology, skilled team, and customer-centric approach, {} is poised to continue leading the way in the industry for years to come.
The Process of Steel Butt Welding: A Complete Guide
Steel Butt Welding, a leading welding technology company specializing in the manufacturing of high-quality welding equipment, is making waves in the industry with its innovative and advanced welding solutions. With a strong emphasis on research and development, the company has been able to create cutting-edge welding technologies that are not only efficient but also cost-effective.The company, with its headquarters located in the heart of the industrial sector, has been at the forefront of providing welding solutions to a wide range of industries, including automotive, aerospace, construction, and more. With a team of highly skilled and experienced professionals, Steel Butt Welding has been able to develop a diverse range of welding equipment that meets the specific needs of its customers.One of the key factors that set Steel Butt Welding apart from its competitors is its commitment to quality. The company has implemented strict quality control measures to ensure that all its products meet the highest industry standards. This dedication to quality has earned Steel Butt Welding a stellar reputation among its customers, who have come to rely on the company for their welding needs.In addition to its focus on quality, Steel Butt Welding also places a strong emphasis on innovation. The company continuously invests in research and development to stay ahead of the curve and introduce new and improved welding solutions to the market. This commitment to innovation has enabled Steel Butt Welding to introduce state-of-the-art welding technologies that offer improved efficiency, productivity, and cost savings to its customers.Among the company's most notable achievements is the development of its butt welding equipment, which has gained significant attention in the industry. The butt welding process is a highly effective method of joining two pieces of metal together end-to-end. This method results in a strong and durable weld, making it ideal for industries that require high-quality and reliable welds.Steel Butt Welding's butt welding equipment is designed to deliver precision and consistency in the welding process, ensuring that the resulting weld is of the highest quality. The company's equipment is also known for its user-friendly design, making it easy for operators to set up and operate, further contributing to the efficiency and effectiveness of the welding process.Another notable aspect of Steel Butt Welding's butt welding equipment is its versatility. The equipment is designed to accommodate a wide range of materials and thicknesses, making it suitable for a variety of welding applications across different industries. This versatility has made Steel Butt Welding's equipment a popular choice among businesses looking for reliable and efficient welding solutions.Steel Butt Welding's commitment to providing top-of-the-line welding equipment, coupled with its dedication to customer satisfaction, has positioned the company as a trusted partner for businesses seeking welding solutions. The company's customer-centric approach has earned it a loyal customer base that values its reliable products and excellent service.Looking ahead, Steel Butt Welding is poised to continue its trajectory of success in the welding industry. The company is committed to further advancing its welding technologies and expanding its range of solutions to meet the evolving needs of its customers. With a focus on innovation, quality, and customer satisfaction, Steel Butt Welding is well-positioned to remain a leader in the welding industry for years to come.
Top Tips for Precision CNC Metal Cutting
CNC Metal Cutting Technology Revolutionizes Manufacturing at []In today's fast-paced manufacturing industry, precision and efficiency are key factors in success. With the advent of CNC metal cutting technology, manufacturers are now able to produce high-quality and complex metal components with ease and accuracy. This technology has revolutionized the way metal parts are fabricated, offering a wide range of benefits for companies looking to enhance their productivity and performance.CNC metal cutting, also known as computer numerical control metal cutting, is a modern manufacturing process that utilizes computer-controlled machines to accurately and efficiently cut and shape metal materials. This technology allows for precise and repeatable machining operations, resulting in high-quality metal components with tight tolerances and smooth finishes. By utilizing advanced computer-aided design (CAD) and computer-aided manufacturing (CAM) software, manufacturers can create detailed and intricate metal parts that meet the exact specifications of their customers.For [], the integration of CNC metal cutting technology has been a game-changer in their manufacturing operations. With an extensive background in metal fabrication, they have embraced CNC metal cutting as a way to stay ahead of the competition and meet the growing demands of their customers. By investing in state-of-the-art CNC machines and training their staff on the latest cutting techniques, [] has been able to expand their capabilities and offer a wider range of metal cutting services to their clients.One of the key advantages of CNC metal cutting technology is its ability to streamline the production process and reduce production time. Traditional metal cutting methods, such as manual milling and turning, are time-consuming and often prone to human error. With CNC metal cutting, the entire process is automated and controlled by the computer, leading to faster and more efficient machining operations. This not only results in quicker turnaround times for customers but also allows manufacturers to take on more complex and challenging projects.In addition to improved efficiency, CNC metal cutting technology also enables manufacturers to achieve higher levels of precision and accuracy. The computer-controlled machines are capable of performing intricate cuts and shaping operations with minimal error, ensuring that each metal component meets the exact specifications of the design. This level of precision is essential for industries that require tight tolerances and complex geometries, such as aerospace, automotive, and medical device manufacturing.Furthermore, CNC metal cutting technology offers a high degree of versatility, allowing manufacturers to work with a wide range of metal materials, including stainless steel, aluminum, titanium, and exotic alloys. This flexibility enables companies like [] to cater to diverse industry needs and provide custom metal cutting solutions for various applications. Whether it's prototyping a new product or mass-producing metal components, CNC metal cutting technology offers the ability to handle a wide spectrum of projects with ease.With the ongoing advancements in CNC metal cutting technology, the future looks promising for the manufacturing industry. As demand for high-quality metal components continues to grow, companies that embrace this cutting-edge technology will be well-positioned to thrive in an increasingly competitive marketplace. [] is a prime example of a company that has leveraged CNC metal cutting to elevate its manufacturing capabilities and deliver exceptional results to its customers.As CNC metal cutting technology becomes more accessible and cost-effective, it's expected that more manufacturers will adopt this innovative approach to metal fabrication. With its unmatched precision, efficiency, and versatility, CNC metal cutting has truly revolutionized the way metal parts are produced, setting a new standard for excellence in the manufacturing industry. As the industry continues to evolve, companies like [] will be at the forefront of this technological revolution, driving innovation and delivering superior metal cutting solutions to their clients.
Guide to Welding Mild Steel to Stainless Steel
[Title: Expanding Capabilities: Mild Steel To Stainless Steel Welding][Date][City, State] - [Company Name], a renowned leader in the welding industry, is delighted to announce the expansion of its capabilities to include mild steel to stainless steel welding. This recent advancement showcases the company's commitment to providing comprehensive solutions to its customers' diverse needs.Founded in [Year], [Company Name] has established itself as a reliable and innovative force within the welding industry. With a team of highly skilled professionals at their disposal, the company has consistently delivered top-notch welding services across various sectors. Keeping up with emerging trends and customer demands, [Company Name] has continuously invested in technological advancements to enhance their offerings.The addition of mild steel to stainless steel welding to their repertoire is a significant milestone for [Company Name]. This development equips the company to cater to a broader range of projects, meeting the needs of industries such as construction, automotive, infrastructure, and manufacturing. By expanding their welding capabilities, the company aims to strengthen its position as a one-stop solution provider for welding services.Mild steel to stainless steel welding poses unique challenges due to the differences in composition and properties of these metals. However, with their extensive expertise and state-of-the-art equipment, [Company Name] is poised to excel in this specialized welding technique. Their highly skilled welders undergo rigorous training to master the intricacies of joining mild steel and stainless steel, ensuring precise and durable welds that meet the highest industry standards.[Company Name]'s commitment to quality assurance remains unwavering. The company adheres to strict quality control protocols at every stage of the welding process, from initial inspection to final delivery. By maintaining stringent quality standards, [Company Name] obtains certifications and accreditations that attest to their professionalism and reliability. Clients can trust that their projects will be executed flawlessly, guaranteeing superior results.The expansion of [Company Name]'s welding capabilities opens up new avenues for collaboration with existing and potential clients. The company's increased flexibility allows them to take on challenging projects that involve mild steel to stainless steel welding. Whether it's fabricating custom components, repairing equipment, or constructing durable structures, [Company Name] has the expertise, resources, and technology to deliver exceptional results.Customers who choose [Company Name] for their mild steel to stainless steel welding requirements can expect a seamless experience from start to finish. The company places great emphasis on clear and effective communication, ensuring that clients' specifications and expectations are thoroughly understood and met. [Company Name]'s team of professionals works closely with each client, providing expert advice and guidance throughout the welding process.Furthermore, [Company Name] is dedicated to fostering long-term relationships based on trust, reliability, and excellent customer service. The company values feedback from clients and consistently seeks ways to improve their services. By prioritizing customer satisfaction, [Company Name] has built a loyal clientele that continues to entrust their welding needs to the company repeatedly.As [Company Name] expands its capabilities to include mild steel to stainless steel welding, they look forward to strengthening their position as an industry leader. The company remains committed to delivering outstanding results while consistently adapting to the evolving needs of the welding industry. With their expertise, technological advancements, and dedication to customer satisfaction, [Company Name] is poised to achieve new milestones in the welding sector.About [Company Name]:[Company Name] is a leading provider of welding services, known for its exceptional quality, reliability, and customer service. Founded in [Year], the company has been serving clients across various industries, including construction, automotive, infrastructure, and manufacturing. With a team of highly skilled professionals and state-of-the-art equipment, [Company Name] offers a comprehensive range of welding solutions, now including mild steel to stainless steel welding.For more information, please visit [website] or contact:[Company Name][Address][City, State][Phone][Email]
Welding 304 Stainless: Tips for Mig Welding
{Company Name} Excels in Mig Welding 304 Stainless Steel, Sets New Standards in Quality and Efficiency{City, Date} - {Company Name}, a leading stainless steel fabrication company, has once again raised the bar with its exceptional mig welding capabilities for 304 stainless steel. The company's unwavering commitment to quality and efficiency has made it a standout in the industry, setting new standards for stainless steel welding.Mig welding 304 stainless steel requires precision and expertise, and {Company Name} has proven time and again that they are up to the challenge. With a team of highly skilled welders and state-of-the-art equipment, the company is able to produce welds that are not only strong and durable, but also aesthetically pleasing.One of the key factors that sets {Company Name} apart is their attention to detail and commitment to perfection. Every weld is meticulously inspected to ensure that it meets the highest standards of quality. This level of dedication has earned {Company Name} a reputation for excellence in mig welding 304 stainless steel, and has made them the go-to choice for customers who demand the best.In addition to their exceptional welding capabilities, {Company Name} offers a wide range of stainless steel fabrication services. From custom designs to large-scale production, the company has the expertise and experience to handle any project, no matter the size or complexity. Their commitment to delivering superior results, on time and within budget, has made them a trusted partner for clients across various industries.With their cutting-edge technology and skilled workforce, {Company Name} has consistently pushed the boundaries of what is possible in stainless steel fabrication. Their mig welding capabilities for 304 stainless steel have not only met but exceeded industry standards, earning them accolades from clients and peers alike.In an industry where precision and quality are paramount, {Company Name} continues to stand out as a leader. Their unwavering dedication to excellence, coupled with their ability to consistently deliver outstanding results, has earned them a loyal and growing customer base.As {Company Name} continues to expand and innovate, they remain committed to upholding the highest standards of quality and integrity in everything they do. With an eye on the future, the company is poised to continue setting new benchmarks in the stainless steel fabrication industry and beyond. Their mig welding capabilities for 304 stainless steel are just one example of how they are pushing the boundaries of what is possible and redefining industry norms.{Company Name} is not just a stainless steel fabrication company; they are a team of dedicated professionals who are passionate about what they do. Their commitment to excellence, paired with their expertise and innovation, has allowed them to carve out a niche as an industry leader. With their unparalleled mig welding capabilities for 304 stainless steel, they have truly set new standards for quality and efficiency.In conclusion, {Company Name} has proven time and again that they are at the forefront of mig welding 304 stainless steel. Their unwavering commitment to quality, coupled with their dedication to perfection, has set new benchmarks in the industry. As the company continues to grow and innovate, they are sure to leave an indelible mark on the stainless steel fabrication industry.