Top 5 Custom Metal Cutting Techniques for Precision Results
By:Admin
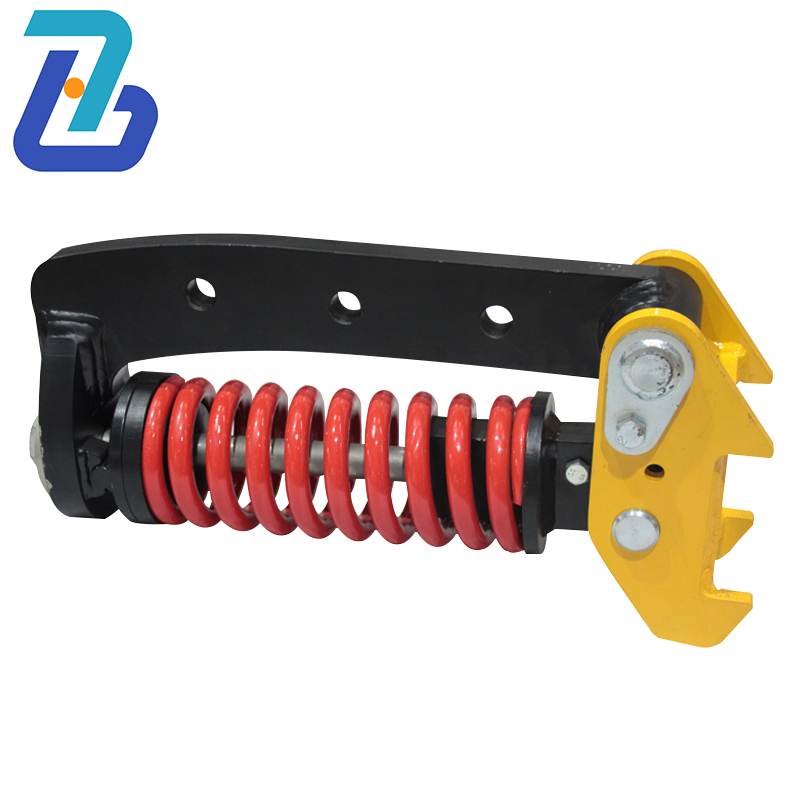
Custom Metal Cutting Company is proud to announce the launch of their new state-of-the-art facility, offering custom precision metal cutting services for a wide range of industries. With over 20 years of experience in the industry, Custom Metal Cutting Company is dedicated to providing high-quality, cost-effective solutions that meet the unique needs of their clients.
Specializing in precision metal cutting, the company utilizes advanced CNC machinery and cutting-edge technologies to deliver precise, accurate results. Their team of highly skilled engineers and technicians are committed to providing innovative solutions that exceed industry standards and customer expectations.
"We are thrilled to introduce our new facility, equipped with the latest technology and capabilities to meet the growing demand for precision metal cutting services," said the CEO of Custom Metal Cutting Company. "Our goal is to provide our customers with the highest quality products and superior customer service, while maintaining competitive pricing and lead times."
Custom Metal Cutting Company offers a wide range of metal cutting services, including laser cutting, plasma cutting, waterjet cutting, and EDM wire cutting. Their capabilities allow for the cutting of various materials, including steel, aluminum, stainless steel, and titanium, among others. In addition to their cutting services, the company also provides value-added services such as deburring, tapping, and drilling to ensure that the final product meets the exact specifications of their clients.
The company serves a diverse customer base, including the aerospace, automotive, medical, and defense industries, among others. Their commitment to quality, precision, and innovation has earned them a reputation as a trusted partner in the manufacturing and fabrication industry.
With a relentless focus on continuous improvement and investing in the latest technologies, Custom Metal Cutting Company is positioned to meet the evolving needs of their customers and the industry as a whole. Their dedication to innovation and excellence has allowed them to stay ahead of the competition and maintain a strong presence in the market.
In addition to their commitment to quality and technology, Custom Metal Cutting Company places a strong emphasis on environmental sustainability and corporate social responsibility. They adhere to the highest standards of environmental compliance and work to minimize their impact on the environment through responsible waste management and energy-efficient practices.
As part of their commitment to their clients, the company offers personalized consultation and engineering support to help customers optimize their designs for manufacturability and cost-effectiveness. Their team of experts works closely with clients to understand their specific needs and provide tailored solutions that meet their unique requirements.
The launch of their new facility marks an important milestone for Custom Metal Cutting Company, as they continue to expand their capabilities and position themselves as a leader in the precision metal cutting industry. With a relentless commitment to innovation, quality, and customer satisfaction, the company is well-equipped to address the evolving needs of their clients and deliver superior solutions for precision manufacturing.
Company News & Blog
US Manufacturer Launches High-Quality Precision Metal Fabrication Services" can be rewritten as "New High-Quality Precision Metal Fabrication Services Now Available in the US.
Precision Fabrications, a leading manufacturing company, is making headlines with its cutting-edge technologies and innovative solutions in the industry. With a strong commitment to quality and customer satisfaction, Precision Fabrications continues to excel in delivering exceptional products and services to its clients worldwide.Established several decades ago, Precision Fabrications has evolved into a global powerhouse in the manufacturing sector. Specializing in the production of precision components and fabricated metal products, the company has garnered a reputation for its expertise, reliability, and attention to detail. With state-of-the-art facilities and a highly skilled workforce, Precision Fabrications is well-equipped to meet the ever-growing demands of its diverse clientele.One of the key strengths of Precision Fabrications lies in its extensive range of capabilities. The company possesses a wide variety of machining and fabrication equipment, allowing it to produce intricate components with utmost precision. From CNC machining and turning to welding and assembly, Precision Fabrications offers comprehensive solutions tailored to meet the unique needs of each client. By combining advanced manufacturing techniques with rigorous quality control measures, the company ensures that every product leaving its facility is of the highest standard.Precision Fabrications serves clients across diverse sectors, including aerospace, automotive, medical, and energy. By catering to such diverse industries, the company has gained invaluable experience in navigating complex manufacturing challenges and delivering solutions that exceed expectations. Its commitment to continuous improvement and investment in research and development have enabled Precision Fabrications to stay ahead of the curve, offering cutting-edge technologies and innovative solutions that keep its clients at the forefront of their respective industries.In addition to its technical expertise, Precision Fabrications places great emphasis on building strong and lasting relationships with its clients. The company recognizes that open communication and collaboration are crucial to ensuring successful partnerships. By actively engaging with clients from project inception to completion, Precision Fabrications is able to fully understand their needs and develop customized solutions that address their specific requirements. This client-focused approach has earned the company a solid reputation for its reliability and ability to deliver on time and within budget.Precision Fabrications also prides itself on its commitment to sustainability and environmental responsibility. The company actively seeks ways to minimize its ecological footprint through efficient use of resources, waste reduction, and recycling initiatives. By implementing eco-friendly practices throughout its operations, Precision Fabrications not only contributes to a greener planet but also demonstrates its commitment to corporate social responsibility.Looking towards the future, Precision Fabrications remains driven by a strong vision to be at the forefront of technological advancements in the manufacturing industry. The company continues to invest in research and development, exploring emerging technologies such as additive manufacturing and automation to further enhance its capabilities. By embracing innovation and staying ahead of industry trends, Precision Fabrications aims to provide its clients with cutting-edge solutions that drive their success in an ever-evolving global market.In conclusion, Precision Fabrications is a leading manufacturing company that has established itself as a trusted partner for clients worldwide. With its commitment to quality, technical expertise, and customer satisfaction, the company continues to deliver exceptional products and services across diverse industries. As it remains dedicated to innovation and sustainability, Precision Fabrications is poised to shape the future of the manufacturing sector, setting new industry standards and raising the bar for excellence.
Top CNC Sheet Metal Cutting Techniques for Precision Results
CNC sheet metal cutting is a highly advanced and precise method of cutting metal sheets using computer numerical control technology. This technology allows for accurate and efficient cutting of metal sheets, making it ideal for a wide range of industries such as automotive, aerospace, construction, and manufacturing.With the increasing demand for high-quality sheet metal cutting, the need for advanced and automated cutting technologies has become imperative. This is where the innovative solutions offered by {} come into play.Established in 1998, {} has become a renowned name in the field of sheet metal cutting, thanks to its commitment to delivering cutting-edge solutions and exceptional customer service. The company's dedication to embracing the latest technological advancements has allowed it to stay ahead of the competition and consistently meet the evolving needs of its clients.{} offers a wide range of CNC sheet metal cutting services, including laser cutting, plasma cutting, and waterjet cutting. These services are tailored to meet the specific requirements of each client, ensuring that they receive the highest quality cuts with minimal material waste.The company's state-of-the-art facilities are equipped with the latest CNC machines, which are operated by highly skilled and experienced technicians. This ensures that every cut is precise, accurate, and of the highest quality.One of the key advantages of {} is its ability to handle both small-scale and large-scale projects with equal ease. Whether it's a small prototype or a mass production run, the company has the capacity and expertise to deliver exceptional results within tight deadlines.In addition to its cutting-edge technology and exceptional capabilities, {} is also committed to sustainability and environmental responsibility. The company implements eco-friendly practices in its operations, including the recycling of metal waste and the use of energy-efficient machinery.Furthermore, {} places a strong emphasis on customer satisfaction, striving to exceed client expectations in every project it undertakes. The company works closely with its clients to understand their unique requirements and provide tailored solutions that meet and exceed their expectations.The combination of cutting-edge technology, skilled workforce, commitment to sustainability, and customer-centric approach has made {} a trusted partner for companies across various industries.As the demand for high-quality sheet metal cutting continues to rise, {} remains at the forefront of the industry, constantly pushing the boundaries of what is possible with CNC sheet metal cutting technology. With its unwavering dedication to excellence, innovation, and customer satisfaction, the company is well-positioned to meet the evolving needs of its clients and maintain its leadership in the sheet metal cutting industry.
Reliable Metal Forming Services Revamp Manufacturing Processes for Enhanced Efficiency
Metal Forming Services, a renowned manufacturer in the metalworking industry, continues to revolutionize the sector with its cutting-edge technology and efficient solutions. With a dedicated team of experts and state-of-the-art facilities, the company has built a strong reputation for delivering high-quality products and exemplary customer service.Metal Forming Services is committed to meeting the growing demands of various industries, including automotive, aerospace, and construction. They offer a wide range of metal forming services, such as stamping, bending, and deep drawing. Their advanced equipment and skilled technicians allow them to tackle complex projects with precision and consistency.One of Metal Forming Services' key strengths lies in their ability to customize solutions that meet individual client specifications. They understand that every project is unique and requires a tailored approach. Through close collaboration with customers, they gather detailed requirements and provide innovative solutions that fulfill their specific needs.The company's commitment to cutting-edge technology has been instrumental in their success. They continuously invest in the latest equipment, allowing them to stay at the forefront of the industry. By embracing automation and digitalization, Metal Forming Services ensures increased efficiency, reduced lead times, and enhanced product quality.Moreover, Metal Forming Services prioritizes sustainability and adopts environmentally friendly practices throughout their operations. They understand the importance of minimizing their ecological footprint and strive to make a positive impact on the environment. From employing energy-efficient machinery to recycling waste materials, they are dedicated to promoting sustainability in the metalworking industry.As a customer-centric company, Metal Forming Services places great emphasis on delivering exceptional service. They value their relationships with clients and strive to exceed expectations at every opportunity. Their knowledgeable and friendly staff are always available to address any concerns and provide prompt assistance, making the customer experience seamless and enjoyable.To ensure consistent excellence, Metal Forming Services employs a rigorous quality control process. They adhere to stringent industry standards and implement stringent quality assurance measures. With a comprehensive inspection system in place, they guarantee that every product leaving their facility meets or exceeds the highest quality benchmarks.In addition to their commitment to quality, Metal Forming Services believes in fostering a culture of safety in the workplace. They prioritize the well-being of their employees and strictly adhere to safety protocols to minimize accidents and injuries. By providing a safe and secure working environment, they promote employee satisfaction and productivity.Metal Forming Services also prides itself on its continuous commitment to research and development. They understand the importance of staying ahead of technological advancements and industry trends. Through ongoing innovation and learning, they anticipate emerging needs and deliver solutions that cater to the evolving demands of their customers.As a market leader in the metalworking industry, Metal Forming Services continues to set the benchmark for excellence. Their unwavering dedication to customer satisfaction, technological innovation, and sustainable practices ensures that they remain at the forefront of the industry. With each project they undertake, they strive to create lasting partnerships and deliver unparalleled value to their clients.In summary, Metal Forming Services is a dynamic and forward-thinking manufacturer that offers a comprehensive range of metal forming services. With their state-of-the-art facilities, skilled workforce, and commitment to quality, the company consistently delivers exceptional solutions to a diverse clientele. Through their ongoing investment in technology and environmentally friendly practices, Metal Forming Services sets itself apart as an industry leader that is capable of meeting the ever-changing demands of modern manufacturing.
Top 5 Benefits of Laser Cutting for Your Household Items
Laser Cutting Technology Revolutionizes Manufacturing IndustryLaser cutting technology has become a game changer in the manufacturing industry, offering a precise and efficient method for cutting a wide range of materials. This technology, combined with the expertise of innovative companies such as {}, is ushering in a new era of manufacturing processes that are faster, more accurate, and more cost-effective than ever before.With the advancement of laser cutting technology, manufacturers are able to achieve extremely precise cuts with minimal material waste. This is achieved through the use of high-powered lasers that are capable of cutting through a variety of materials, including metal, plastic, wood, and composites. In addition, the computerized control systems used in conjunction with the lasers allow for precise and complex shapes to be cut with ease.{} is at the forefront of utilizing this cutting-edge technology in their manufacturing processes. As a leading provider of metal products, they have integrated laser cutting technology into their operations to offer their customers unparalleled precision and quality. By investing in state-of-the-art laser cutting equipment, they are able to offer a wide range of customized cutting solutions for various industries, including automotive, aerospace, and architecture.One of the key benefits of laser cutting technology is its ability to produce high-quality cuts with minimal distortion. Traditional cutting methods often result in heat-affected zones and burrs, which can compromise the integrity of the material. With laser cutting, the focused beam of light generates minimal heat, resulting in clean and precise cuts without any distortion. This level of precision and quality is essential for industries that demand high standards for their products.In addition to its precision, laser cutting technology offers significant cost savings for manufacturers. The efficiency and speed of laser cutting processes reduce production times and labor costs, making it a cost-effective solution for companies looking to streamline their operations. Furthermore, the minimal material waste produced by laser cutting results in additional cost savings and environmental benefits.The versatility of laser cutting technology is another factor driving its widespread adoption in the manufacturing industry. With the ability to cut a wide range of materials and produce complex shapes, laser cutting is a versatile solution for various manufacturing needs. This flexibility allows manufacturers to create customized products and components that meet the specific requirements of their customers.As the demand for high-quality, precision-engineered products continues to grow, the role of laser cutting technology in the manufacturing industry is poised to expand even further. The ability to produce intricate and complex designs with precision and efficiency makes laser cutting an indispensable tool for manufacturers across a wide range of industries.The adoption of laser cutting technology by companies such as {} is a testament to its transformative impact on the manufacturing industry. By leveraging this advanced technology, {} is able to deliver superior quality products to their customers while driving operational efficiency and cost savings.In conclusion, laser cutting technology has revolutionized the manufacturing industry by offering a precise, efficient, and cost-effective solution for cutting a wide range of materials. Through the expertise and innovation of companies like {}, this technology is reshaping the way products are manufactured, setting new standards for precision and quality. As the industry continues to embrace the benefits of laser cutting, the future looks bright for manufacturing processes that are faster, more accurate, and more cost-effective than ever before.
MIG Welding Tips for Working with Thin Steel
Mig Welding Thin Steel – A Game-Changer in the Welding IndustryWelding is a crucial process in the manufacturing and construction industry. It involves the process of fusing two pieces of metal to create a strong bond. Mig welding is one of the most popular welding techniques used today. It stands for Metal Inert Gas welding and is sometimes referred to as Gas Metal Arc welding (GMAW).Mig welding uses a consumable electrode wire consisting of a metal wire placed on a spool that continuously feeds through a welding gun. The process involves the wire coming into contact with the base metal, generating an electrical arc that melts the wire and the base metal together to form a strong bond. The process is efficient, and it can be used to weld various metals, including carbon steel, stainless steel, aluminum, nickel alloys, and copper.However, Mig welding thin steel has always been a challenge, mainly due to the risk of burn-through, weld distortion, and poor weld quality. These challenges have been at the forefront of the welding industry, and many companies have been searching for a solution to solve these issues. Fortunately, one company has developed a solution that has been a game-changer in the welding industry.The company, which prefers to remain anonymous, has developed a new technique that enhances Mig welding thin steel, delivering exceptional results with minimal risks of distortion and burn-through. The company’s innovation is designed for use in the automotive, aerospace, and construction industries.Their solution is a new welding wire designed explicitly for thin steel. The wire comprises a unique combination of materials designed to deliver superior results when welding thin steel. Its construction comprises a specific blend of wire, shield gas, and other advanced technologies that enhance the welding process.The new welding wire boasts several benefits, including a lower melting point and higher heat conductivity, making it easier to weld thin steel without burning through. Additionally, it enhances the arc stability hence reducing the risk of weld defects.For the automotive industry, the new welding wire has been a game-changer. Automakers face the challenge of building lighter, fuel-efficient cars, and the new welding wire has been instrumental in achieving that. Thin sheet metal is used to construct body panels, hoods, and trunks. The new welding wire has helped automakers overcome the challenges of welding these thin sheets, resulting in lighter vehicles, increased fuel efficiency, and reduced manufacturing costs.In the aerospace industry, the new welding wire has also come in handy. Aircraft manufacturers use thin steel in the construction of wings, tail sections, and fuselage. These thin sheets require careful handling during the welding process to avoid distortions and burn-through. The new welding wire has enhanced the welding process, enabling manufacturers to construct high-quality aircraft with minimal defects, reduced manufacturing costs, and faster production times.For the construction industry, the new welding wire has decreased the risks of welding thin structural pipes. The welding of pipes is essential for the construction of various structures, including buildings, bridges, and tunnels. With the new welding wire, manufacturers can weld thin steel pipes without the risk of burn-through and distortions, creating a safer and more efficient construction environment.In summary, the development of the new welding wire designed for Mig welding thin steel has been a game-changer in the welding industry. Its unique combination of materials has enhanced the welding process, reducing the risks of burn-through, weld defects, and distortions. The new welding wire has been instrumental in facilitating the production of lighter, fuel-efficient vehicles in the automotive industry, the production of high-quality aircraft in the aerospace industry, and safer and more efficient welding for the construction industry.The company that developed the new welding wire has continued to innovate, seeking new ways to improve the welding process further. Their achievement serves as a testament to the power of innovation and the endless possibilities it presents. The welding industry will continue to benefit from advancements in technology, and we can expect even more innovations in the future.
Essential Techniques for Welding Stainless Steel Pipes: A Comprehensive Guide
Stainless Steel Pipe Welding: Delivering Quality and Precision(Company Introduction)In a rapidly evolving industrial landscape, companies must constantly innovate to stay ahead of the competition. One such enterprise leading the charge is {{Company Name}}, a market leader in the stainless steel industry. With years of experience and a dedication to quality, they have revolutionized the world of stainless steel pipe welding.(Opening Paragraph)Stainless steel pipes play a crucial role in various industries, including oil and gas, construction, and manufacturing. Their ability to withstand extreme temperatures, pressure, and corrosion makes them an essential component in many applications. However, it is the welding process that truly determines the integrity and durability of these pipes.(Main Body - Paragraph 1)Recognizing the critical importance of stainless steel pipe welding, {{Company Name}} has invested heavily in state-of-the-art technology and equipment. Equipped with cutting-edge welding machines, they ensure the highest standards of quality and precision in every welded joint. The company also places significant emphasis on continuous training and development of its welding technicians, allowing them to maintain the highest level of expertise in the industry.(Main Body - Paragraph 2)Precision is a key factor in stainless steel pipe welding, as even the tiniest of flaws can compromise the integrity of the final product. {{Company Name}} utilizes advanced welding techniques, such as Tungsten Inert Gas (TIG) and Metal Inert Gas (MIG), to achieve flawless welds. Through meticulous control of the welding parameters, including voltage, current, and speed, they guarantee consistent and reliable welds, meeting the stringent requirements of various industries.(Main Body - Paragraph 3)Quality assurance is at the core of {{Company Name}}'s operations. Every welded joint undergoes rigorous testing and inspection to ensure conformity to international standards. Non-destructive testing techniques, such as ultrasonic testing and radiographic examination, are employed to detect any hidden flaws or defects. By adhering to these strict quality control measures, {{Company Name}} has earned an impeccable reputation for supplying stainless steel pipes of superior quality.(Main Body - Paragraph 4){{Company Name}} takes environmental responsibility seriously. Through the implementation of environmentally friendly welding processes, such as low-emission welding techniques, they reduce the carbon footprint associated with stainless steel pipe manufacturing. This commitment to sustainability not only benefits the environment but also demonstrates {{Company Name}}'s dedication to meeting the evolving needs of socially conscious industries.(Main Body - Paragraph 5)As the demand for stainless steel pipes continues to grow, {{Company Name}} remains at the forefront of innovation. Their research and development department is constantly exploring new materials, welding techniques, and technologies to further enhance the performance and longevity of their products. By staying ahead of the curve, they ensure that their customers always receive the most cutting-edge solutions for their specific applications.(Closing Paragraph)With a steadfast commitment to quality, precision, and innovation, {{Company Name}} has become a trusted partner for businesses worldwide, seeking exceptional stainless steel pipe welding solutions. Their unwavering dedication to customer satisfaction, coupled with their continuous drive for excellence, positions them as an industry leader in the competitive stainless steel market.
High-Quality Laser Die Cutting Services for Precision Cutting
Laser Die Cutting Services Revolutionizing the Manufacturing IndustryIn the era of advanced technology, the manufacturing industry continues to evolve and innovate in order to meet the demands of the market. One such innovation that has been making waves in the manufacturing world is laser die cutting services. This cutting-edge technology has revolutionized the way products are made, providing precision, efficiency, and flexibility that traditional die cutting methods simply cannot match.Laser die cutting services utilize high-powered lasers to precisely cut and engrave materials, offering a level of accuracy and intricacy that is unmatched by traditional die cutting methods. This technology has found its way into a wide range of industries, including automotive, electronics, packaging, and medical devices, among others. The ability to cut and shape materials with such precision has opened up new possibilities for manufacturing, allowing for the production of complex and intricate designs that were previously unattainable.One company that has been at the forefront of this innovation is {}. They have been providing cutting-edge laser die cutting services to a diverse range of industries, offering a level of precision and quality that is second to none. With state-of-the-art equipment and a team of skilled professionals, {} has been able to meet the unique and demanding needs of their clients, delivering exceptional results time and time again.The benefits of laser die cutting services are numerous. From intricate and precise cutting to the ability to work with a wide range of materials, including plastics, metals, and composites, this technology offers a level of versatility that traditional die cutting methods simply cannot match. In addition, laser die cutting services can significantly reduce production time and costs, as well as minimize material waste, making it a highly efficient and cost-effective option for manufacturers.Moreover, laser die cutting allows for quick and easy design changes, as there is no need for costly and time-consuming tooling adjustments. This level of flexibility is invaluable in today's fast-paced and ever-changing market, where manufacturers must constantly adapt to meet the demands of consumers.With the increasing demand for precision and efficiency in manufacturing, laser die cutting services have quickly become an essential tool for manufacturers looking to stay ahead of the competition. By offering unparalleled precision, flexibility, and efficiency, this cutting-edge technology has raised the bar for product design and manufacturing, providing a level of quality and intricacy that was once thought to be unattainable.As the manufacturing industry continues to evolve and innovate, it is clear that laser die cutting services will play a critical role in shaping the future of manufacturing. With its ability to produce intricate and precise designs with unparalleled efficiency, this technology is set to revolutionize the way products are made, setting new standards for quality and innovation in manufacturing. And with companies like {} leading the way, the future of manufacturing looks brighter than ever.
Mastering the Art of Tig Welding on Cast Stainless Steel - Expert Guide
Title: Advancements in Tig Welding Techniques for Cast Stainless SteelIntroduction:In today's rapidly advancing manufacturing industry, companies are continually striving to enhance their welding techniques to meet the growing demands of their customers. One such company, renowned for its innovation in the field of cast stainless steel welding, is {Name of Company}. Through a combination of cutting-edge technology and a strong commitment to research and development, they have recently achieved significant progress in Tig welding techniques for cast stainless steel. This article will delve into the latest advancements made by the company and their potential implications for the industry.1. Background on Cast Stainless Steel:Cast stainless steel is widely used in various industries, including automotive, aerospace, energy, and construction, primarily due to its exceptional corrosion resistance and high strength properties. However, welding cast stainless steel poses several challenges due to its unique metallurgical structure and inherent susceptibility to cracks and defects during the welding process. To overcome these challenges, {Name of Company} has dedicated significant resources to develop innovative welding techniques.2. Innovations in Tig Welding for Cast Stainless Steel:Tig welding, also known as Gas Tungsten Arc Welding (GTAW), has long been recognized as a reliable and efficient welding method for stainless steel alloys. However, when it comes to welding cast stainless steel, the process becomes much more intricate. {Name of Company} has made substantial breakthroughs in Tig welding, focusing specifically on cast stainless steel, resulting in enhanced weld quality and overall productivity.a. Improved Pre-welding Preparation: To minimize defects during welding, {Name of Company} has introduced meticulous pre-welding preparation techniques, including thorough cleaning and surface conditioning of the cast stainless steel. By removing impurities and ensuring proper joint fit-up, the likelihood of defects such as porosity and cracking is significantly reduced.b. Enhanced Heat Control: Achieving optimal heat input during the welding process is critical to prevent distortion, eliminate residual stresses, and maintain mechanical properties. {Name of Company} has developed advanced heat control systems, including rapid temperature monitoring and adaptive welding parameters, resulting in precise heat distribution and minimizing the risk of stress-related failures.c. Filler Material Selection: {Name of Company} has extensively researched and tested various filler materials to match the specific metallurgical properties of cast stainless steel. This includes the development of new filler alloys with improved tensile strength, crack resistance, and corrosion resistance. The optimized selection of filler material greatly contributes to the durability and longevity of the welded joint.d. Post-Weld Heat Treatment: Recognizing the importance of post-weld heat treatment for cast stainless steel, {Name of Company} has implemented innovative procedures to relieve residual stresses and improve the overall microstructure of the welded joint. Precisely controlled heat treatment cycles have proven to enhance the mechanical properties of the welded components, ensuring superior performance and longevity.3. Implications for the Industry:The advancements made by {Name of Company} in Tig welding techniques for cast stainless steel have significant implications for the manufacturing industry:a. Improved Product Quality: The enhanced welding techniques result in higher-quality welds, with reduced defects and improved mechanical properties. This directly translates into superior-quality finished products for various industries reliant on cast stainless steel components.b. Increased Productivity: The precise heat control and filler material selection contribute to increased productivity and overall manufacturing efficiency. With fewer defects and reduced post-welding process requirements, {Name of Company}'s advancements enable faster turnaround times and reduced costs.c. Longevity and Reliability: Welded joints incorporating the advanced Tig welding techniques by {Name of Company} exhibit enhanced durability and improved resistance to corrosion, fatigue, and stress-related failures. This ensures the longevity and reliability of products in demanding environments, such as automotive and energy sectors.Conclusion:Through their relentless pursuit of innovation and dedication to delivering unmatched quality, {Name of Company} has revolutionized Tig welding techniques for cast stainless steel. Their advancements in pre-welding preparation, heat control, filler material selection, and post-weld heat treatment have led to superior weld quality, increased productivity, and enhanced product longevity. As the manufacturing industry continues to rely on cast stainless steel components, these advancements will undoubtedly play a pivotal role in shaping the future of Tig welding in this sector.
Top Supplier of Welding and Steel for Interstate Projects: Get Quality Supplies Now!
Interstate Welding And Steel Supply Announces Exciting Developments in the Welding IndustryIn a recent announcement, Interstate Welding And Steel Supply, a leading player in the welding and steel supply market, confirmed a series of exciting developments that are set to reshape the industry. As one of the most trusted and reliable companies in this sector, Interstate Welding And Steel Supply has been at the forefront of providing cutting-edge solutions and high-quality services to its customers. With a strong focus on innovation and customer satisfaction, the company has cemented its position as a market leader.Interstate Welding And Steel Supply prides itself on having a team of highly skilled professionals who are dedicated to delivering the best possible results. By constantly striving for excellence, the company has been able to create a strong reputation for its commitment to exceptional customer service and top-of-the-line products. Whether it is providing welding equipment and accessories or supplying high-grade steel, Interstate Welding And Steel Supply ensures that it stays ahead of the competition by understanding market demands and addressing them proactively.To further strengthen its position in the welding industry, Interstate Welding And Steel Supply has invested in advanced technologies and machinery. By doing so, the company enables its clients to benefit from next-generation welding solutions that allow for greater precision and efficiency. This strategic investment not only sets the company apart but also allows it to meet the evolving needs of modern industries.Recognizing the significance of sustainability and environmental responsibility, Interstate Welding And Steel Supply has incorporated eco-friendly practices into its operations. By implementing energy-saving measures and reducing waste, the company is committed to minimizing its environmental footprint. This dedication to sustainable practices not only showcases Interstate Welding And Steel Supply's commitment to the future but also highlights the company's efforts to align its business with global environmental goals.As part of its ongoing commitment to fostering innovation and collaboration, Interstate Welding And Steel Supply has also formed strategic partnerships with key industry players. By joining forces with other leading companies, the organization aims to exchange knowledge, share resources, and drive the industry forward collectively. By collaborating with trusted partners, Interstate Welding And Steel Supply is confident that it can deliver unprecedented value to its customers.Furthermore, Interstate Welding And Steel Supply understands the importance of investing in its workforce. By providing comprehensive training and development programs, the company ensures that its employees stay up-to-date with the latest industry trends and advancements. This investment in human capital not only plays a crucial role in maintaining the company's competitive edge but also contributes to the growth and success of its employees.In conclusion, Interstate Welding And Steel Supply's recent developments are a testament to the company's unwavering commitment to excellence and innovation. By investing in advanced technologies, ensuring sustainability, fostering collaborations, and prioritizing employee development, the company continues to solidify its position as a market leader in the welding and steel supply industry. As Interstate Welding And Steel Supply moves forward, it remains focused on delivering exceptional products and services to its valued customers while shaping the future of the industry through its continuous efforts and dedication.