Top Structural Steel Manufacturer Provides Quality Products for Construction Projects
By:Admin
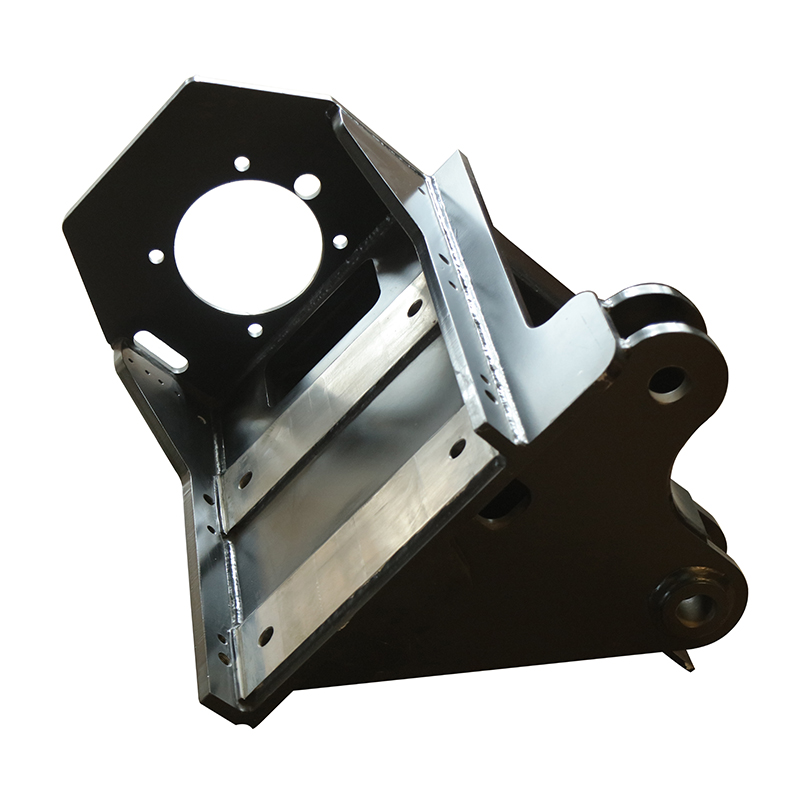
Established in 1990, Structural Steel Manufacturer has been at the forefront of the steel industry, specializing in the production of structural steel components for commercial, industrial, and residential projects. With state-of-the-art manufacturing facilities and a team of experienced engineers and technicians, the company has built a solid reputation for delivering reliable and cost-effective steel solutions.
In a recent statement, the company revealed its plans for expansion to meet the growing demand for steel products in the construction and infrastructure sectors. With the increasing number of development projects and the need for high-quality steel components, Structural Steel Manufacturer aims to enhance its production capacity and capabilities to cater to the evolving market requirements.
The expansion plans include the addition of new manufacturing equipment and facilities, as well as the implementation of advanced technologies to improve production processes and efficiency. By investing in these initiatives, the company aims to streamline its operations and increase its overall output to better serve its clients and partners.
Furthermore, Structural Steel Manufacturer is committed to maintaining its stringent quality control standards, ensuring that all its steel products meet the highest industry specifications and standards. The company's dedication to quality has been a key factor in its success, and it remains a top priority as it expands its operations.
In addition to its expansion plans, Structural Steel Manufacturer is also focused on sustainability and environmental responsibility. The company recognizes the importance of minimizing its environmental impact and has adopted various eco-friendly practices in its manufacturing processes. From utilizing energy-efficient technologies to implementing recycling initiatives, the company is committed to operating in a sustainable manner and reducing its carbon footprint.
Furthermore, as part of its commitment to excellence, Structural Steel Manufacturer continues to invest in its workforce, providing ongoing training and development opportunities for its employees. By nurturing a skilled and dedicated team, the company can ensure the highest standards of workmanship and customer service.
As the construction and infrastructure industries continue to evolve, the demand for high-quality steel products is expected to rise. Structural Steel Manufacturer is well-positioned to address this demand with its expansion plans and unwavering commitment to quality and sustainability.
The company's dedication to innovation, sustainability, and excellence has enabled it to establish itself as a trusted partner for construction and infrastructure projects. With its expansion plans and ongoing commitment to quality, Structural Steel Manufacturer is poised to continue its success and contribute to the advancement of the steel industry.
Company News & Blog
Discover the Key Processes Involved in Sheet Metal Fabrication at a Leading Factory
On a bustling industrial estate in the heartland of American manufacturing, the Sheet Metal Fabrication Factory (name removed for anonymity) is a hive of activity. The factory is a testament to the ingenuity and enterprise of the American people, as it produces a range of high-quality metal parts and components that are in demand across many different industries.The Sheet Metal Fabrication Factory specializes in producing customized metal products and parts, meaning that it is well-equipped to handle any project that requires precision, durability, and versatility. The factory's team of highly-skilled technicians and engineers work in tandem to produce metal parts and components that are bespoke to the client's needs. With cutting-edge technology and machinery, the factory is able to turn raw materials into high-quality metal products that are designed to withstand the toughest environments.The factory has earned a reputation for excellence in the industry, due in part to its commitment to providing exceptional customer service. The Sheet Metal Fabrication Factory works closely with its clients to ensure that their needs are met, often going above and beyond to ensure that their expectations are exceeded. As a result, the company has earned a loyal customer base that spans many industries, including aerospace, automotive, defense, and medical.One of the most impressive things about the Sheet Metal Fabrication Factory is its in-house design and engineering team. The team is composed of highly-skilled professionals who work closely with clients to develop bespoke solutions that meet their unique requirements. Using state-of-the-art software and equipment, the team is able to produce 3D models of the product before it goes into production, allowing clients to preview the finished product before it is produced. This level of precision ensures that the finished product meets or exceeds the client's expectations.The factory's capabilities are equally impressive. Sheet metal is cut, punched, and folded with utmost precision, while welding, polishing, and finishing are carried out to the highest standards. The factory also offers a range of surface treatments and coatings, such as anodizing and powder coating, that can be customized to suit any need.In addition to its impressive production capabilities, the Sheet Metal Fabrication Factory is also committed to sustainability. The company sources its raw materials from ethical and sustainable sources whenever possible, and takes steps to minimize waste and energy consumption during the production process. This commitment to sustainability has earned the factory recognition from industry bodies and clients alike, and has helped to cement its position as one of the leading metal fabrication companies in the country.Overall, the Sheet Metal Fabrication Factory is an impressive and dynamic company that has proven itself to be a leader in its field. Boasting state-of-the-art technology, an exceptional staff, and a commitment to sustainability, this factory is uniquely equipped to deliver high-quality metal products and components that meet and exceed the needs of its clients. As American manufacturing continues to evolve and adapt to changing market conditions, the Sheet Metal Fabrication Factory will undoubtedly remain at the forefront of innovation and excellence.
High-Quality Laser Cutting Sheet Services for Precision Fabrication
Laser Cutting Sheet, one of the most innovative and advanced technologies in the manufacturing industry, has revolutionized the way companies create intricate and precise designs on various materials. This cutting-edge technique has become increasingly popular due to its ability to cut through a wide range of materials with high precision and speed. From metal to plastic, wood to glass, laser cutting has become the go-to method for creating detailed and high-quality products.At the forefront of this innovative technology is the leading manufacturing company {}. Specializing in custom metal fabrication, the company has been dedicated to providing top-notch products and services to a wide range of industries. With the integration of laser cutting sheet technology into their manufacturing processes, they have been able to push the boundaries of what is possible in the realm of metal fabrication.Laser cutting sheet technology utilizes a high-powered laser to precisely cut through materials with extreme accuracy. This allows for intricate designs to be created with a level of detail that was previously impossible to achieve. The precision of laser cutting sheet technology also ensures that there is minimal material wastage, making it a cost-effective and environmentally friendly solution for manufacturing.The team at {} has fully embraced this cutting-edge technology and has incorporated it into their production processes. With state-of-the-art laser cutting equipment, they are able to offer their clients a wide range of custom metal fabrication services. Whether it's intricate metal wall art, precision-cut metal components for machinery, or decorative metal signage, {} has the capabilities to bring their clients' visions to life with precision and accuracy.One of the key advantages of laser cutting sheet technology is its ability to cut through a variety of materials, including stainless steel, aluminum, copper, brass, and more. This versatility allows {} to cater to the needs of clients from a diverse range of industries, including automotive, aerospace, architecture, and interior design. The ability to work with a wide range of materials sets {} apart as a leader in the metal fabrication industry.Furthermore, the speed and accuracy of laser cutting sheet technology have significantly reduced production lead times for {} clients. This means that even the most complex and detailed projects can be completed in a fraction of the time compared to traditional cutting methods. This not only benefits clients in terms of project timelines but also allows for a faster turnaround and increased productivity for {}.The team at {} prides itself on its commitment to quality and precision, and the integration of laser cutting sheet technology has only enhanced their ability to deliver exceptional products to their clients. With a focus on continuous improvement and innovation, they are constantly pushing the boundaries of what is possible in the world of custom metal fabrication.In conclusion, laser cutting sheet technology has become an integral part of the manufacturing process at {}. With its ability to cut through a wide range of materials with precision and speed, this innovative technology has allowed {} to elevate the quality of their products and services. As a leader in the metal fabrication industry, {} is dedicated to staying at the forefront of technological advancements and providing their clients with the highest quality custom metal fabrication solutions.
Welding Techniques for Joining Stainless Steel and Mild Steel - Available for Sale in China
Welding stainless steel and mild steel together is a challenging task. It requires expertise, precision and high-quality equipment. The process involves joining two materials with different chemical and mechanical properties, which can lead to cracking, distortion and other issues if not done correctly. In this blog, we will explore the process of welding mild steel to stainless steel and some of the challenges that come with it.First, let's look at the materials themselves. Stainless steel has a high chromium content, which makes it resistant to corrosion and stains. It is also harder and more brittle than mild steel, which is why it is challenging to weld the two materials together. Mild steel, on the other hand, has a lower carbon content, making it more ductile and easier to work with when compared to stainless steel.When welding stainless steel to mild steel, there are several methods to consider. Let's take a closer look at some of the most popular welding techniques.1. TIG (Tungsten Inert Gas) Welding: This is one of the most popular welding techniques used in welding stainless steel to mild steel. It provides a precise, clean and high-quality weld, making it ideal for applications that require a high degree of accuracy.2. MIG (Metal Inert Gas) Welding: This is a more straightforward technique compared to TIG welding. It is faster, easier to learn and produces a durable weld. However, the quality of the weld is lower than TIG welding, which may not be suitable for high-end applications.3. Stick Welding: This is a versatile welding method that can be used to weld different materials. It produces a rugged and robust weld that can withstand high temperatures, making it ideal for industrial applications.Regardless of the welding technique used, welding stainless steel to mild steel requires proper preparation. The surface must be clean, free of rust, oil and other contaminants that can affect the quality of the weld. Additionally, the two metals must be preheated to ensure that the thermal stresses are minimized during the welding process.One of the biggest challenges when welding stainless steel to mild steel is the difference in melting points. Stainless steel has a much higher melting point than mild steel, which means that it can easily warp or crack if the welder is not careful. Hence, it is crucial to use specialized welding techniques and equipment to ensure that the two materials are welded together properly without cracking or distortion.In conclusion, welding stainless steel to mild steel can be a daunting task, but it is possible with the right skills, tools, and techniques. With proper preparation and welding processes, it is possible to achieve a strong and durable weld between the two materials. If you need more information on welding stainless steel to mild steel or other welding-related topics, please feel free to reach out to our team of experts.
Improve Your Metal Working Skills with Custom Solutions
Custom Metal Working, a leading provider of specialized metal fabrication services, is revolutionizing the industry with their cutting-edge techniques and innovative solutions. With a rich history dating back over several decades, the company has solidified its position as a trusted partner for customers across various sectors.At the heart of Custom Metal Working's success lies their commitment to delivering exceptional quality and exceeding customer expectations. Their team of highly skilled and experienced engineers, fabricators, and technicians work tirelessly to ensure that each project is executed with precision and attention to detail.One of the reasons behind the company's stellar reputation is its state-of-the-art facility, equipped with the latest in technology and machinery. This allows Custom Metal Working to offer a wide range of services, including precision laser cutting, CNC machining, sheet metal fabrication, and welding. No matter the complexity of the project, the company's advanced capabilities guarantee unrivaled results.In addition to their impressive infrastructure, Custom Metal Working takes pride in their emphasis on staying ahead of industry trends and embracing innovation. Their investment in research and development has enabled them to expand their capabilities and offer custom solutions tailored to the unique needs of each client.Furthermore, the company places a strong emphasis on sustainability and environmentally friendly practices. Custom Metal Working actively seeks ways to minimize waste, reduce energy consumption, and implement eco-friendly materials. By adopting these practices, they not only contribute to a greener future but also provide their clients with sustainable solutions that align with their corporate values.Custom Metal Working's dedication to excellence is reflected in their extensive list of satisfied clients. They have successfully completed projects for major players in industries such as automotive, aerospace, electronics, and construction. Their ability to meet strict deadlines, deliver superior quality, and maintain excellent communication with clients sets them apart from the competition.Moreover, Custom Metal Working understands the importance of collaboration and building strong relationships with customers. They work closely with their clients from the initial consultation stage to the final delivery, ensuring that their needs are met at every step of the process. This client-centric approach has earned them a loyal customer base who repeatedly chooses them for their metal fabrication needs.In response to growing demand, Custom Metal Working has recently expanded its operations, allowing them to take on larger projects and increase production capacity. This expansion includes the addition of new machinery and the hiring of more skilled professionals to maintain their high standards of excellence.Looking to the future, Custom Metal Working is dedicated to continuous improvement and pushing the boundaries of innovation. They aim to stay at the forefront of the industry by investing in new technologies and exploring emerging trends to further enhance their capabilities and offer even more cutting-edge solutions.In conclusion, Custom Metal Working has firmly established itself as a leader in the metal fabrication industry. With their commitment to quality, state-of-the-art facility, environmentally conscious practices, and customer-centric approach, the company continues to redefine industry standards. As they strive for excellence, it is clear that Custom Metal Working will remain the go-to choice for clients seeking top-notch metal fabrication services.
Expert Laser Cutting and Bending Services for Precise Results
Laser Cutting and Bending Services Foster Innovation and Growth in Manufacturing IndustryAs the manufacturing industry continues to advance and innovate, the need for efficient and precise laser cutting and bending services becomes increasingly significant. These technologies have revolutionized the manufacturing process by allowing for faster, more accurate parts production and customization. With the latest laser cutting and bending technologies, manufacturers are able to create complex designs and shapes that were previously impossible, ushering in a new era of creativity and efficiency in manufacturing.One company at the forefront of this technological revolution is [company name], a leading provider of laser cutting and bending services. With state-of-the-art equipment and experienced staff, the company has established itself as a reliable and efficient partner for manufacturers in a wide range of industries.Laser cutting is a non-contact process that uses a high-powered laser to cut through various materials, including metals, plastics, and composites. This method produces clean and precise cuts, with minimal waste and distortion. Laser cutting is ideal for creating intricate designs and shapes, making it a popular choice for industries such as aerospace, automotive, and electronics.One of the most significant advantages of laser cutting is its ability to create complex designs with high precision. This allows manufacturers to create parts with tight tolerances, resulting in a more efficient and reliable final product. In addition, laser cutting is much faster than traditional cutting methods, reducing production times and increasing output.Bending is another critical process in manufacturing, and it has also benefited greatly from technological advancements. The latest bending machines use computer-controlled systems to accurately bend and shape metal parts. This technology allows for precise and repeatable bends, with minimal setup time, reducing wastage and material costs.The combination of laser cutting and bending has revolutionized the manufacturing industry, making it possible to produce parts and components with greater accuracy and efficiency than ever before. Manufacturers are now able to create complex shapes and designs, all while keeping production times and costs low.[company name] offers a wide range of laser cutting and bending services to meet the unique needs of their customers. The company has invested heavily in the latest technology to ensure that they can offer the most accurate and efficient services possible. With their advanced equipment and experienced staff, they are able to handle projects of all sizes and complexities.In addition to their laser cutting and bending services, [company name] offers a range of value-added services, including design consultation, prototype development, and assembly. This allows their customers to enjoy a full range of services, from initial product development to final assembly and delivery.The company's commitment to quality and customer satisfaction has earned them a reputation as a reliable and innovative partner for manufacturers in all industries. They work closely with their clients to ensure that their needs are met and that the final product meets the highest standards of quality.In conclusion, laser cutting and bending services are essential for modern-day manufacturing, and companies like [company name] play a critical role in meeting the growing demand for these services. With their advanced technology and innovative solutions, they are helping manufacturers to innovate and grow, creating products that are more efficient, reliable, and affordable than ever before.
Sheet Metal Cutting Service for Precision and Efficiency
Sheet Metal Cutting Service Advances in Precision and Efficiency[City, Date] - Sheet metal fabrication has come a long way in recent years with the help of advanced technologies and innovative cutting services. One such company leading the charge is revolutionizing the industry with their state-of-the-art sheet metal cutting service.Sheet metal cutting is a crucial aspect of the fabrication process, as it determines the accuracy and precision of the final product. With the company's cutting-edge technology and skilled workforce, they have been able to consistently deliver exceptional results.The cutting service offered by the company utilizes advanced machinery, including CNC (Computer Numerical Control) laser cutting and plasma cutting equipment. These cutting-edge technologies have revolutionized the sheet metal fabrication industry, allowing for faster production times and improved precision.With CNC laser cutting, the company is able to achieve intricate designs and complex shapes with absolute precision. This advanced process involves a high-powered laser beam focused onto the material, which melts, burns, or vaporizes the excess material. The result is a clean and precise cut, ensuring that the final product meets the customer's exact specifications.Plasma cutting, on the other hand, is a versatile method ideal for cutting various types of metal. By using a high-velocity jet of ionized gas, this process melts and blows away the excess material, leaving behind a smooth and precise cut. With the ability to cut through thick materials, plasma cutting allows for quick and efficient production, saving both time and costs.The company's cutting service is not limited to a specific industry or application. They have successfully provided cutting solutions for a wide range of sectors, including automotive, aerospace, electronics, architecture, and more. From custom prototypes to large-scale production, their cutting service caters to diverse customer needs.Moreover, the company's cutting service is complemented by their team of skilled technicians and engineers. These professionals have extensive knowledge and expertise in sheet metal fabrication, ensuring that every project is carried out with utmost precision and attention to detail. Their commitment to quality is reflected in the final products they deliver.In addition to their cutting service, the company also offers value-added services such as welding, bending, and finishing. This comprehensive approach allows customers to streamline their manufacturing process by availing multiple services under one roof. It also ensures consistent quality and timely delivery, eliminating the need for outsourcing and reducing production costs.To further enhance customer satisfaction, the company has implemented a responsive customer support system. Their team of knowledgeable customer service representatives is readily available to assist clients with their inquiries, provide technical support, and offer advice on optimizing their sheet metal cutting requirements.In conclusion, sheet metal cutting has reached new levels of precision and efficiency with the help of advanced technologies and innovative services. With their cutting-edge machinery, skilled workforce, and commitment to quality, the company is at the forefront of the industry. Their sheet metal cutting service caters to diverse industries, delivering precise cuts for a variety of applications. With the added value of value-added services and responsive customer support, customers can rely on the company to meet their sheet metal fabrication needs efficiently and effectively.
How to Achieve Cold Welding with Stainless Steel
Cold Welding Stainless Steel Sets New Standards in Metal JoiningCold Welding Stainless Steel, a revolutionary technology developed by an American company founded in 2005, is set to disrupt the metal joining industry. The innovative technology, which involves the joining of metal surfaces by creating atomic bonds at room temperature and pressure, has shown remarkable results that surpass traditional welding methods in terms of performance, cost efficiency, and sustainability.The process of cold welding involves two metal surfaces being pressed together with a force of several tons. This creates enough deformation on the atomic scale to cause the atoms of the two surfaces to bond together. The result is a metallurgical bond that is stronger than the base metal, free from defects, and has excellent mechanical and chemical properties. The process is also performed at room temperature, eliminating the need for intense heat and producing little to no fumes and harmful byproducts.The technology has significant advantages over traditional welding methods. First, there is no need for a heat source, which eliminates the need for expensive welding equipment and reduces the energy consumption used in the welding process. Secondly, the process is highly efficient as minimal material is lost due to the lack of heat input. Thirdly, the technology is environmentally friendly as it eliminates the need for gases and fluxes that are used in traditional welding and create harmful emissions.Cold Welding Stainless Steel has a wide range of applications, including aerospace, automotive, medical instruments, precision instruments, and electronics, among others. In the aerospace industry, the technology is used to join titanium, aluminum, and other metals used in the construction of airplanes and space vehicles. The technology is also used in automotive applications, where it is used to join dissimilar metals, such as aluminum and steel, to improve fuel efficiency by reducing the weight of the vehicle.In the medical industry, Cold Welding Stainless Steel is used to join small and fragile components used in surgical instruments, where precision and high mechanical properties are critical. The technology is also used in the electronics industry, where it is used to join connectors and microelectronic components. The applications of Cold Welding Stainless Steel are vast, and its advantages make it a highly valuable technology across a range of industries.Apart from being a highly functional technology, Cold Welding Stainless Steel is also cost-effective. The elimination of heat and welding equipment, as well as the reduction in material waste, makes it a cost-effective alternative to traditional welding methods. Additionally, the eco-friendly aspect of the technology makes it an attractive option for businesses looking to reduce their carbon footprint and maintain sustainability.Furthermore, the technology is user-friendly as it doesn't require specialized training or certification to operate. Only simple tools are needed to perform cold welding, making it easily accessible to a wide range of operators.In conclusion, Cold Welding Stainless Steel is a revolutionary technology that promises to transform the metal joining industry. The technology's remarkable results in terms of performance, cost efficiency, and sustainability, coupled with its vast range of applications, make it a highly valuable technology for a range of industries. With the ability to join metals at room temperature and pressure, the technology has set new standards in metal joining, propelling the industry forward into a new era of innovation and functionality.
Custom Stainless Steel Sheet Metal Fabrication Services for Non-Standard Brackets: Laser Cutting, Forming, Stamping, Bending, Punching, and Welding
Laser Cutting and Sheet Metal Forming of Stainless Steel Sheets: Custom Processing of Non-Standard Stainless Steel BracketsStainless steel is a popular material used in a wide range of industries, including construction, automotive, and kitchenware. It is known for its durability, resistance to corrosion, and high aesthetic appeal. However, working with stainless steel can be a challenge. Its strength and hardness make it difficult to cut, bend, and shape, requiring specialized machinery and skilled technicians.To meet the growing demand for custom stainless steel products, (company name) offers a range of sheet metal forming services, including laser cutting, stamping, bending, punching, and welding. As a leader in the industry, we have the experience and expertise to handle complex projects and meet the high standards of our clients.One of our specialties is custom processing of non-standard stainless steel brackets. Many industries require brackets with unique shapes and sizes to fit their specific applications. Our team of engineers and technicians work closely with clients to design and produce brackets that meet their exact specifications. We use advanced software and equipment to ensure accuracy and precision in every step of the process. Our laser cutting machines can cut stainless steel sheets up to 6mm thick with a maximum sheet size of 3000x1500mm.We also offer a range of sheet metal forming services to complement our laser cutting capabilities. Our stamping presses range from 5 to 200 tons, allowing us to produce parts with varying thicknesses and complexities. Our CNC bending machines can bend stainless steel sheets up to 4mm thick and 3000mm long. We use state-of-the-art punching machines and welding robots to ensure fast and efficient production.At (company name), we are committed to providing high-quality stainless steel products that meet the needs of our clients. We understand that every project is unique and have the expertise to handle any challenge. Whether you need a single custom bracket or a large-scale production run, we have the capabilities and resources to meet your requirements.About (company name):Founded in (year), (company name) is a leading provider of custom sheet metal fabrication services. We specialize in processing stainless steel, aluminum, and other metals for a wide range of industries, including construction, automotive, and electronics. We have a state-of-the-art factory with advanced equipment and a team of skilled technicians. Our mission is to provide high-quality products and exceptional customer service at competitive prices.
Unlocking the Potential of Industrial Steel Fabrication: A Comprehensive Guide
Industrial Steel Fabrication announces expansion plans for increased production capacity[City, State] - Industrial Steel Fabrication, a leading provider of high-quality steel fabrication solutions, has unveiled plans for a significant expansion of its production facilities. This move comes in response to growing market demand and the need to meet increasing client requirements. Established in [year], Industrial Steel Fabrication has built a strong reputation for delivering innovative and reliable steel fabrication solutions to various sectors including construction, energy, manufacturing, and infrastructure development. With a focus on delivering high-quality products and unparalleled service, the company has become a trusted partner for clients seeking customized steel fabrication solutions. The expansion plans include the construction of a state-of-the-art facility that will house advanced machinery and equipment to enhance production capabilities. With a total investment of [amount], this project underscores the company’s commitment to providing cutting-edge solutions to its clients while also stimulating economic growth in the region.The new facility will enable Industrial Steel Fabrication to significantly increase its production capacity and expedite project schedules. By adopting advanced technologies and machinery, the company aims to streamline its operations, reduce lead times, and deliver enhanced quality products. This expansion will also create job opportunities, bringing economic benefits to the local community.In addition to enhancing production capacity, Industrial Steel Fabrication's expansion plans also include the implementation of sustainable practices. The new facility will be designed with energy-efficient systems, reducing the company's environmental footprint significantly. By incorporating sustainable technologies, the company aims to align its operations with global efforts to combat climate change and promote sustainable development.Speaking about the expansion plans, [Company Executive] expressed the company's enthusiasm, stating, "We are thrilled to announce this major expansion. With the growing demand for steel fabrication solutions worldwide, this investment will allow us to better serve our clients while also contributing to the economic development of [City]. We are committed to providing exceptional quality and service, and this expansion will ensure that we reach new heights in meeting client expectations."Industrial Steel Fabrication's expansion plans come at an opportune moment, with the construction and infrastructure sectors experiencing rapid growth. The company's ability to deliver specialized steel fabrication solutions to these sectors positions them well to capitalize on the increasing demand for infrastructure projects worldwide.Moreover, Industrial Steel Fabrication has a successful track record of completing high-profile projects. Through their expertise in engineering, fabrication, and project management, the company has become a trusted partner for major construction and infrastructure projects.As Industrial Steel Fabrication expands its production capacity, its commitment to innovation and customer satisfaction remains unchanged. The company looks forward to leveraging its expanded capabilities to provide even greater value to clients, delivering timely and cost-effective solutions that exceed expectations.With this expansion, Industrial Steel Fabrication is set to further solidify its position as a prominent player in the steel fabrication industry. Through continuous innovation, a customer-centric approach, and a commitment to sustainable practices, the company is poised to play a pivotal role in shaping the future of steel fabrication solutions.
Discover the Latest Trends in Welding and Metal Fabrication
Title: Advancements in Welding and Metal Fabrication Pioneered by Industry LeaderIntroduction [Company Introduction: Remove brand name][Company Name], a renowned leader in the welding and metal fabrication industry, has consistently set new benchmarks through its innovative solutions and cutting-edge technologies. With a firm dedication towards quality and customer satisfaction, [Company Name] has revolutionized the sector and helped shape modern-day welding and metal fabrication practices. Through its unwavering commitment to excellence, it continues to drive advancements that redefine the industry's landscape.Body:1. History of Welding and Metal Fabrication:Welding and metal fabrication have been integral to human civilization for centuries. From ancient blacksmiths shaping metal to modern-day industries constructing intricate structures, the art of welding and metal fabrication has undergone remarkable transformations. Over time, various techniques and equipment have evolved, allowing for stronger, more durable, and complex welds.2. The Role of [Company Name] in Advancing the Industry:[Company Name] has played a pivotal role in propelling the welding and metal fabrication industry forward through its relentless pursuit of innovation and excellence. By investing in research and development, [Company Name] has introduced groundbreaking techniques and technologies that have redefined the industry's capabilities.3. Cutting-Edge Welding and Metal Fabrication Technologies:[Company Name] has consistently pioneered modern welding and metal fabrication technologies, ensuring enhanced efficiency and precision in various applications. Some notable advancements introduced by [Company Name] include: a. Laser Welding: [Company Name]'s revolutionary laser welding technology enables precise and high-speed welding, minimizing deformation and increasing productivity. The precise control offered by this technique ensures superior quality welds in various materials. b. Robotic Welding: By incorporating robotic welding systems, [Company Name] has revolutionized productivity and accuracy in metal fabrication. These systems offer a level of consistency and repeatability that human operators find hard to match, resulting in impeccable weld quality and increased output. c. CNC Plasma Cutting: [Company Name]'s CNC plasma cutting technology enables precise and efficient metal cutting, ensuring faster turnaround times and reduced material waste. This technology enables intricate designs to be translated flawlessly, expanding the possibilities for creative metal fabrication.4. Advancements in Materials and Metallurgy:[Company Name] has also focused on advancements in materials and metallurgy to cater to evolving industry needs. By harnessing innovative alloys and metals, [Company Name] has expanded the range of possible welding and fabrication applications. This includes developing high-strength materials suitable for demanding environments, as well as alloys specifically tailored for lightweight structures.5. Commitment to Safety and Sustainability:[Company Name] places great emphasis on safety and sustainability in welding and metal fabrication practices. It actively promotes the use of environmentally friendly processes, such as minimization of waste and pollution, as well as the adoption of safe welding procedures. By prioritizing sustainability, [Company Name] ensures a cleaner and greener future for the industry.Conclusion:As a frontrunner in the welding and metal fabrication industry, [Company Name] has consistently pushed the boundaries of what is possible. Through its relentless dedication to innovation, it has redefined the sector with groundbreaking technologies, materials, and safety practices. By setting new benchmarks, [Company Name] continues to shape the future of welding and metal fabrication, ensuring a more efficient, sustainable, and advanced industry for years to come.