Unlocking the Potential of Steel and Metal Fabrication: A Comprehensive Guide
By:Admin
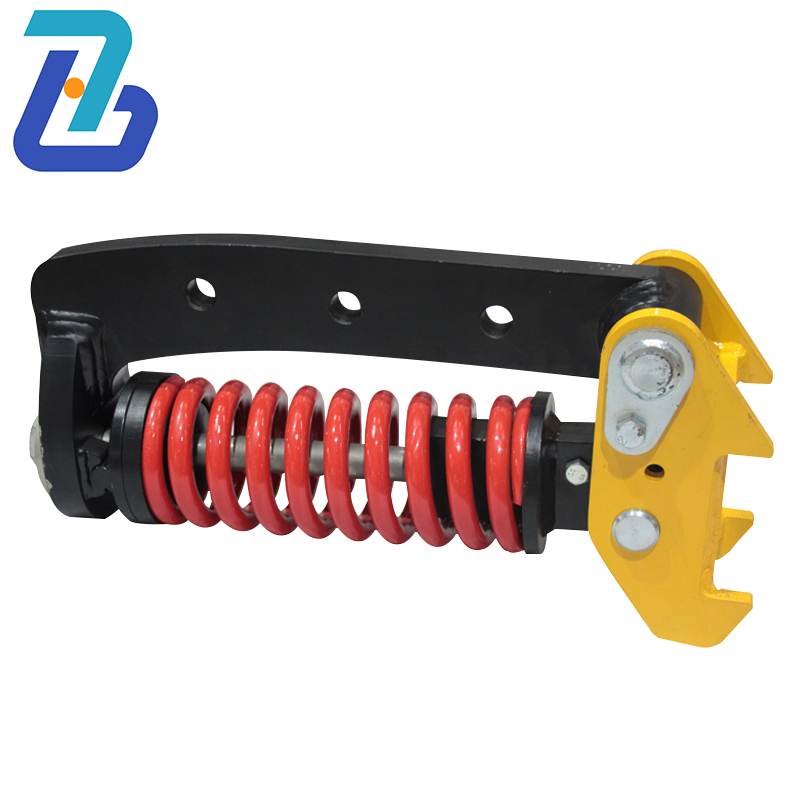
Introduction to {Company Name}:
With a rich history spanning over decades, {Company Name} has emerged as a leading player in the highly competitive steel and metal fabrication industry. Known for its commitment to innovation, superior quality, and customer satisfaction, {Company Name} has set new standards in the market. It is a trusted name when it comes to precision engineering, complex metal structures, and customized steel solutions. As the demand for steel and metal fabrication continues to rise, {Company Name} remains at the forefront, successfully catering to the evolving needs of diverse industries.
Steel and Metal Fabrication Industry Outlook:
The steel and metal fabrication industry has seen significant growth in recent years due to increasing industrialization, rapid urbanization, and a surge in construction activity. The demand for fabricated steel products is expected to rise even further due to infrastructure development, especially in emerging economies.
One of the key drivers behind the industry's growth is the rising investment in the construction and transportation sectors. Infrastructure projects like bridges, roads, railways, and airports require large quantities of fabricated steel products, creating a substantial market for {Company Name} to tap into.
Additionally, the automotive sector is also a major consumer of fabricated steel. The demand for lightweight, high-strength steel components to enhance fuel efficiency and safety in vehicles presents opportunities for {Company Name} to expand its footprint in this market.
Market Expertise and Innovative Solutions:
{Company Name}, backed by its extensive experience, possesses unmatched expertise in the steel and metal fabrication industry. The company is equipped with state-of-the-art manufacturing facilities, cutting-edge technologies, and a highly skilled workforce. This allows {Company Name} to provide tailor-made solutions to its clients, no matter how complex or challenging their requirements may be.
From designing and engineering to fabrication and installation, {Company Name} ensures a seamless process that adheres to industry standards and delivers unmatched quality. The company's customer-centric approach enables it to build strong relationships, resulting in long-term partnerships with clients across various sectors.
Quality and Sustainability as Cornerstones:
As the steel and metal fabrication industry continues to evolve, quality and sustainability have become crucial considerations for businesses and end-users. {Company Name} understands the significance of these factors and has made them the cornerstones of its operations.
{Company Name} is committed to delivering products that not only meet but exceed the highest industry standards. The company's quality control measures guarantee precision, durability, and consistency in every fabricated steel component. Furthermore, strict adherence to eco-friendly practices minimizes the environmental impact of their manufacturing processes, enhancing sustainability.
Investing in Research and Development:
Innovation plays a vital role in {Company Name}'s success. The company continuously invests in research and development to stay ahead of the curve and provide cutting-edge solutions to its clients. By actively monitoring industry trends and embracing technological advancements, {Company Name} consistently introduces new products and improves existing ones, ensuring its clients always benefit from the latest innovations.
Conclusion:
As the global demand for steel and metal fabrication continues to rise, {Company Name} stands prepared to capitalize on the lucrative market opportunities. With a strong focus on quality, sustainability, and innovation, the company has established itself as a reliable partner across a wide range of industries. As {Company Name} moves forward, it remains committed to delivering top-notch fabricated steel products that meet the evolving needs of its clients, thereby cementing its position as a leader in the steel and metal fabrication industry.
Company News & Blog
Discover the Evolution of Butt Welding: A Comprehensive Insight into Steel Welding Techniques
Title: Revolutionizing Steel Butt Welding: A Company IntroductionIntroduction:In the world of industrial manufacturing, steel butt welding plays a vital role in creating strong and reliable joint connections. However, the traditional methods of steel butt welding often come with their fair share of challenges, such as inconsistencies in joint quality, increased labor costs, and a lack of efficiency. But now, a revolutionary solution has emerged that promises to transform the steel welding industry. In this news article, we will dive into the company{} and its groundbreaking advancements in steel butt welding.Company Background:{} is a leading innovator in the field of industrial manufacturing, specializing in advanced techniques and technologies for steel welding. With a rich history dating back to its establishment in [year], the company has continuously strived to push the boundaries of traditional welding methods. Through extensive research and development, {} has successfully developed a state-of-the-art solution for steel butt welding that addresses many of the long-standing challenges faced by the industry.Revolutionary Advancements in Steel Butt Welding:The innovative technology developed by {} aims to revolutionize the way steel butt welding is performed. By combining cutting-edge equipment with advanced process control, this groundbreaking method offers several key benefits over traditional approaches. Let's explore some of the noteworthy advancements:1. Enhanced Joint Quality: {}'s steel butt welding technique ensures consistent and high-quality joint connections, thereby minimizing the risk of weld failures. With a focus on precision and accuracy, the company's technology eliminates common discontinuities and imperfections often associated with traditional welding methods.2. Increased Efficiency: The new steel butt welding method drastically improves efficiency, resulting in significant time and cost savings for manufacturers. By streamlining the welding process and reducing the need for manual intervention, {} enables faster production cycles while maintaining strict adherence to quality standards.3. Reduced Labor Costs: Traditional welding methods involve labor-intensive processes, requiring skilled welders to carry out intricate tasks. However, {}'s technology automates several stages of the welding process, reducing the dependency on skilled labor and optimizing workforce utilization. This, in turn, helps reduce labor costs without compromising on the quality of welded joints.4. Seamless Integration: One of the major advantages of {}'s steel butt welding solution is its compatibility with existing manufacturing infrastructure. The technology seamlessly integrates into a wide range of production setups, allowing manufacturers to adopt this revolutionary method without significant modifications or equipment replacements.5. Environmental Sustainability: Recognizing the increasing need for eco-friendly practices, {}'s steel butt welding solution focuses on minimizing environmental impact. By optimizing energy consumption and reducing waste generation, the company's technology promotes sustainable manufacturing processes while maintaining or exceeding industry standards.Conclusion:{}'s revolutionary advancements in steel butt welding are poised to redefine the industrial manufacturing landscape. By addressing the challenges of joint quality, efficiency, labor costs, compatibility, and sustainability, the company has successfully positioned itself as a frontrunner in the field. As manufacturers worldwide strive for improved welding solutions, {} provides an innovative and reliable option that promises long-term benefits for all stakeholders involved. With {}.
Top Supplier of Welding and Steel for Interstate Projects: Get Quality Supplies Now!
Interstate Welding And Steel Supply Announces Exciting Developments in the Welding IndustryIn a recent announcement, Interstate Welding And Steel Supply, a leading player in the welding and steel supply market, confirmed a series of exciting developments that are set to reshape the industry. As one of the most trusted and reliable companies in this sector, Interstate Welding And Steel Supply has been at the forefront of providing cutting-edge solutions and high-quality services to its customers. With a strong focus on innovation and customer satisfaction, the company has cemented its position as a market leader.Interstate Welding And Steel Supply prides itself on having a team of highly skilled professionals who are dedicated to delivering the best possible results. By constantly striving for excellence, the company has been able to create a strong reputation for its commitment to exceptional customer service and top-of-the-line products. Whether it is providing welding equipment and accessories or supplying high-grade steel, Interstate Welding And Steel Supply ensures that it stays ahead of the competition by understanding market demands and addressing them proactively.To further strengthen its position in the welding industry, Interstate Welding And Steel Supply has invested in advanced technologies and machinery. By doing so, the company enables its clients to benefit from next-generation welding solutions that allow for greater precision and efficiency. This strategic investment not only sets the company apart but also allows it to meet the evolving needs of modern industries.Recognizing the significance of sustainability and environmental responsibility, Interstate Welding And Steel Supply has incorporated eco-friendly practices into its operations. By implementing energy-saving measures and reducing waste, the company is committed to minimizing its environmental footprint. This dedication to sustainable practices not only showcases Interstate Welding And Steel Supply's commitment to the future but also highlights the company's efforts to align its business with global environmental goals.As part of its ongoing commitment to fostering innovation and collaboration, Interstate Welding And Steel Supply has also formed strategic partnerships with key industry players. By joining forces with other leading companies, the organization aims to exchange knowledge, share resources, and drive the industry forward collectively. By collaborating with trusted partners, Interstate Welding And Steel Supply is confident that it can deliver unprecedented value to its customers.Furthermore, Interstate Welding And Steel Supply understands the importance of investing in its workforce. By providing comprehensive training and development programs, the company ensures that its employees stay up-to-date with the latest industry trends and advancements. This investment in human capital not only plays a crucial role in maintaining the company's competitive edge but also contributes to the growth and success of its employees.In conclusion, Interstate Welding And Steel Supply's recent developments are a testament to the company's unwavering commitment to excellence and innovation. By investing in advanced technologies, ensuring sustainability, fostering collaborations, and prioritizing employee development, the company continues to solidify its position as a market leader in the welding and steel supply industry. As Interstate Welding And Steel Supply moves forward, it remains focused on delivering exceptional products and services to its valued customers while shaping the future of the industry through its continuous efforts and dedication.
How to Weld Stainless Steel to Regular Steel
Welding Stainless Steel to Steel - A Revolutionary Technique!Welding stainless steel to steel has never been an easy task. Professionals in the industry have been struggling with this challenge for decades. However, the good news is that {} has recently made a breakthrough in this area, with a new welding technique that promises to revolutionize the industry.As experts in the field of welding, {} has been working tirelessly to solve some of the most complex challenges facing the industry. One such challenge is the inability to weld stainless steel to steel, which has been a frustrating issue for many professionals.According to company sources, after years of research and experimentation, {} has developed a new welding technique that can successfully join stainless steel and steel together. This new method promises to expand the application of stainless steel, which will have a significant impact on various industries, including automotive, construction, aerospace, and more.This technique involves the use of specially formulated welding wire with built-in flux that is capable of removing impurities from the steel surface, ensuring a strong and durable bond. The process is quick, efficient, and cost-effective, which makes it a game-changer for the industry.In addition to the innovative welding technique, {} is also proud to offer a range of welding solutions for other challenging applications, including aluminum, copper, and other exotic materials. The company, which has been in the industry for over 20 years, has built a reputation as a reliable and trusted source of welding solutions.{} sources say that the company's team of experts is committed to providing the highest quality of products and services to their clients. They work closely with clients to understand their unique needs and offer customized solutions that meet their specific requirements.With a strong focus on research and development, {} is constantly on the lookout for new techniques and technologies that can improve the welding process. The company is known for its innovation and creativity, and its team of experts is always ready to take on new challenges.The news of this breakthrough welding technique is already making waves in the industry. Many professionals are eager to try out this new method and see its impact on their work.One of {}'s clients, a leading manufacturer of automotive parts, has already tested this new technique and reported excellent results. They were able to weld stainless steel and steel together without any issues, and the joints were strong and durable.The CEO of {} said in a statement, "We are thrilled to offer this new welding technique to our clients. It is a game-changer for the industry, and we are confident that it will make a significant impact on various industries. Our team has worked hard to develop this innovation, and we are excited to see its potential."He added, "We are committed to providing the highest quality of products and services to our clients, and this new technique is one of the many ways we are demonstrating that commitment."In conclusion, the breakthrough welding technique developed by {} promises to revolutionize the industry and expand the application of stainless steel. With a focus on innovation and creativity, {} is leading the way in the welding industry, and their commitment to providing the highest quality of products and services is unwavering. Professionals in the industry are excited to try out this new method and see its potential.
Reliable Metal Forming Services Revamp Manufacturing Processes for Enhanced Efficiency
Metal Forming Services, a renowned manufacturer in the metalworking industry, continues to revolutionize the sector with its cutting-edge technology and efficient solutions. With a dedicated team of experts and state-of-the-art facilities, the company has built a strong reputation for delivering high-quality products and exemplary customer service.Metal Forming Services is committed to meeting the growing demands of various industries, including automotive, aerospace, and construction. They offer a wide range of metal forming services, such as stamping, bending, and deep drawing. Their advanced equipment and skilled technicians allow them to tackle complex projects with precision and consistency.One of Metal Forming Services' key strengths lies in their ability to customize solutions that meet individual client specifications. They understand that every project is unique and requires a tailored approach. Through close collaboration with customers, they gather detailed requirements and provide innovative solutions that fulfill their specific needs.The company's commitment to cutting-edge technology has been instrumental in their success. They continuously invest in the latest equipment, allowing them to stay at the forefront of the industry. By embracing automation and digitalization, Metal Forming Services ensures increased efficiency, reduced lead times, and enhanced product quality.Moreover, Metal Forming Services prioritizes sustainability and adopts environmentally friendly practices throughout their operations. They understand the importance of minimizing their ecological footprint and strive to make a positive impact on the environment. From employing energy-efficient machinery to recycling waste materials, they are dedicated to promoting sustainability in the metalworking industry.As a customer-centric company, Metal Forming Services places great emphasis on delivering exceptional service. They value their relationships with clients and strive to exceed expectations at every opportunity. Their knowledgeable and friendly staff are always available to address any concerns and provide prompt assistance, making the customer experience seamless and enjoyable.To ensure consistent excellence, Metal Forming Services employs a rigorous quality control process. They adhere to stringent industry standards and implement stringent quality assurance measures. With a comprehensive inspection system in place, they guarantee that every product leaving their facility meets or exceeds the highest quality benchmarks.In addition to their commitment to quality, Metal Forming Services believes in fostering a culture of safety in the workplace. They prioritize the well-being of their employees and strictly adhere to safety protocols to minimize accidents and injuries. By providing a safe and secure working environment, they promote employee satisfaction and productivity.Metal Forming Services also prides itself on its continuous commitment to research and development. They understand the importance of staying ahead of technological advancements and industry trends. Through ongoing innovation and learning, they anticipate emerging needs and deliver solutions that cater to the evolving demands of their customers.As a market leader in the metalworking industry, Metal Forming Services continues to set the benchmark for excellence. Their unwavering dedication to customer satisfaction, technological innovation, and sustainable practices ensures that they remain at the forefront of the industry. With each project they undertake, they strive to create lasting partnerships and deliver unparalleled value to their clients.In summary, Metal Forming Services is a dynamic and forward-thinking manufacturer that offers a comprehensive range of metal forming services. With their state-of-the-art facilities, skilled workforce, and commitment to quality, the company consistently delivers exceptional solutions to a diverse clientele. Through their ongoing investment in technology and environmentally friendly practices, Metal Forming Services sets itself apart as an industry leader that is capable of meeting the ever-changing demands of modern manufacturing.
Top Metal Cutting Service Provider: Delivering Precision and Efficiency
FOR IMMEDIATE RELEASELeading Metal Cutting Service Provider Revolutionizes Industry with Advanced Technology and Unparalleled PrecisionCITY, DATE – Metal Cutting Service (MCS), a prominent player in the metal cutting industry, has recently introduced a groundbreaking technology that is set to revolutionize the way metal components are cut and fabricated. With an extensive track record of delivering high-quality products and services, MCS continues to push boundaries, emphasizing precision, efficiency, and innovation.Founded over two decades ago, MCS has steadily gained recognition in the industry as a reliable partner for all metal cutting requirements. The company has consistently stayed ahead of the competition by investing in state-of-the-art machinery and adopting cutting-edge techniques. Renowned for its commitment to perfection and unparalleled precision, MCS has been the go-to choice for clients across various sectors, ranging from aerospace and automotive to construction and healthcare.At the heart of MCS's success lies their team of highly skilled technicians and engineers who possess profound expertise and experience in metal cutting and fabrication. Adhering to strict quality standards, the team meticulously examines each project, ensuring that all specifications are met to perfection. By focusing on the finest details, MCS consistently delivers exceptional results, earning them a trusted reputation within the industry.What sets MCS apart from its competitors is its unwavering commitment to innovation. The company continually invests in cutting-edge technology to ensure optimal precision and efficiency. With the introduction of their latest revolutionary technology, MCS has taken metal cutting to an entirely new level. This cutting-edge advancement allows for intricate designs and complex geometries to be precisely fabricated with unparalleled accuracy, reducing lead times and significantly increasing production output.MCS's new technology is equipped with advanced software that enables seamless integration between design and production, fostering a streamlined workflow. The software provides real-time feedback, allowing for quick adjustments and modifications, ultimately leading to improved overall project efficiency. Moreover, this technology enhances operator safety by minimizing human intervention during the cutting process.One of the key advantages of MCS's advanced technology is its ability to handle a wide range of materials, including steel, aluminum, titanium, and more. The versatility of this technology positions MCS as a top-tier metal cutting service provider capable of catering to diverse industries and customizing solutions to meet the unique demands of each client.With the introduction of this advanced technology, MCS aims to address the growing demands of the market, particularly in an era driven by rapid industrialization and innovation. By extending its capabilities and setting new industry standards, MCS remains steadfast in its commitment to delivering exceptional service to its clients.As an environmentally conscious company, MCS places great emphasis on sustainability and eco-friendly practices. The utilization of advanced technology enables the optimization of material usage, reducing waste and minimizing the carbon footprint. By adopting sustainable measures, MCS ensures its role as a responsible industry leader.As the metal cutting industry continues to evolve, MCS remains dedicated to staying at the forefront of innovation and excellence. With their unparalleled precision, commitment to quality, and advanced technology, MCS is poised to reshape the industry, empowering businesses to achieve unprecedented levels of success.For more information about MCS, their state-of-the-art technology, and the services they offer, please visit [Company Website].###About Metal Cutting Service:Metal Cutting Service (MCS) is a leading provider of metal cutting and fabrication solutions. With over two decades of experience, MCS is renowned for its precision, reliability, and commitment to excellence. The company's dedication to investing in advanced technology has allowed them to consistently deliver exceptional results, positioning them as an industry leader. MCS caters to a wide range of sectors, offering customized solutions to meet diverse client needs. For more information, visit [Company Website].
Top Small Metal Fabrication Techniques and Services for All Your Needs
Title: Small Metal Fabrication Company Revolutionizes the Industry with Expertise and Cutting-Edge TechnologyIntroduction:In an era where the manufacturing industry is rapidly evolving, one company has managed to disrupt the metal fabrication sector through its exceptional prowess and innovative technology. This revolutionary company, which prefers to remain anonymous, aims to transform the way we perceive small metal fabrication. With its commitment to precision, efficiency, and customer satisfaction, the company has become a pioneer in shaping the future of metalworks.Body:I. A Tradition of Excellence:Small Metal Fabrication has a rich history dating back several decades, during which it has established itself as an industry leader. With an unyielding dedication to quality, the company has consistently produced superior metal products for a variety of applications. Small Metal Fabrication's commitment to excellence has earned it recognition as a trusted partner by numerous clients across different sectors, ranging from automotive and aerospace to electronics and construction.II. Innovating the Fabrication Process:Integral to the company's success lies its relentless pursuit of innovation. Investing heavily in advanced technology, Small Metal Fabrication has transformed the traditional fabrication process into a highly efficient, precise, and cost-effective system. By leveraging cutting-edge machinery, automation, and robotics, the company has significantly reduced production time and minimized errors, ensuring consistent quality and higher productivity.III. Expert Team and State-of-the-Art Facilities:Central to Small Metal Fabrication's ability to deliver exceptional results is its highly skilled and experienced team. With a passion for metalworks, the company's personnel are experts in their respective fields, meticulously trained to handle intricate projects with utmost precision. Moreover, the company's state-of-the-art facilities provide an ideal environment for their experts to bring their visions to life.IV. Customization and Flexibility:Understanding the unique demands of its diverse clientele, Small Metal Fabrication excels in providing tailor-made solutions for each project. The company's flexible production capabilities enable them to accommodate various specifications, size requirements, and design preferences. This commitment to customization sets the company apart and has contributed to its long-standing client relationships.V. Sustainability and Eco-Friendly Practices:Small Metal Fabrication is acutely aware of its responsibility towards the environment. In an effort to contribute to a sustainable future, the company actively implements eco-friendly policies throughout its operations. Reusable materials, responsible waste management, and energy-efficient practices are just a few examples of Small Metal Fabrication's dedication to minimizing its ecological footprint.VI. Industry Recognition and Awards:Proving its industry dominance and commitment to excellence, Small Metal Fabrication has garnered several industry awards and accolades. Its dedication to innovation, customer satisfaction, and sustainable practices has earned the company widespread recognition and the trust of clients and partners alike. These prestigious awards further cement Small Metal Fabrication's reputation as a leading force in metal fabrication.VII. Looking Ahead:As the industry continues to evolve, Small Metal Fabrication remains at the forefront of innovative metalworks solutions. By staying abreast of technological advancements and continuously honing their skills, the company remains well-positioned to meet the ever-changing demands of their clients. Through their unwavering commitment to quality, customization, and sustainability, Small Metal Fabrication is poised to leave an indelible mark on the metal fabrication industry.Conclusion:Small Metal Fabrication's unwavering dedication to excellence and innovation has revolutionized the metal fabrication industry. With its cutting-edge technology, expert team, and commitment to sustainability, the company continues to lead the way in providing tailor-made metal products for a vast array of industries. Small Metal Fabrication's legacy as a pioneer in the field is secure, as they continue to shape the future of metal fabrication with their relentless pursuit of perfection.
Efficient Metal Cutting Techniques: Flame Cutting Explained
Flame Cutting: The Ultimate Solution for Precision CuttingWhen it comes to precise cutting of metal, Flame Cutting is an ultimate solution that has been used for decades. Flame Cutting involves the use of a flame torch to heat the metal to its ignition point, then a jet of oxygen is directed onto the heated metal, causing it to burn and producing a highly precise cut. This form of cutting is ideal for large and thick metal materials, making it a popular choice among construction, automobile and shipbuilding industries.Although Flame Cutting has been in existence for several years, the technology has significantly evolved, leading to enhancements and modifications that make it even more effective. In fact, Flame Cutting has become a critical component in the manufacturing industry and has become more popular as a reliable and efficient way of producing custom parts and components with great accuracy.One company that has mastered the art of Flame Cutting is {company name goes here}. {company name} has been utilizing Flame Cutting technology for years to provide quality metal cutting solutions for different industries. The company's Flame Cutting services are tailored to fit each customer's unique specifications by offering a range of customized cutting options that carefully consider budget and timeframes. The services are affordable and competitively priced, offering customers with the most advanced cutting technology with highly accurate and precise cuts.At {company name}, all cutting machines are of the latest technology, state-of-the-art model, offering superior quality and efficiency for all cutting needs. The torches are robust and are designed to withstand high temperatures and pressures, making them ideal for cutting through even the thickest metal materials. The machines have plasma cutting features that provide cleaner cuts compared to traditional flame cutting methods. As such, traditional flame cutting methods are being replaced by plasma cutting as the new cutting methodology.The company can provide Flame Cutting up to 8 inches thick, and can precisely cut simple and intricate design shapes, ranging from standard geometries to complex curves, angles, and notches. For customers looking for more precision in their cuts, {company name} provides additional services that include Bevel Cutting and Multi-Torch Oxy-Fuel Cutting. With bevel cutting, the machines can make up to 45-degree angled cuts, while multi-torch oxy-fuel cutting provides enhanced flexibility and quality for customers seeking multiple cuts on various shapes.{Company name}'s experienced staff advises its customers through the cutting process, providing guidance towards the best cutting options suitable for their projects. The team has vast knowledge in cutting different metal types, which ensures that each project receives the appropriate cutting technology suitable for each unique project.The Flame Cutting services provided by {company name} have grown to be a trusted solution by many leading industries seeking precise and cost-effective cutting solutions. The company works diligently to meet its clients' demands by offering them the most technologically advanced tools and equipment, superior quality, and the best available prices.In conclusion, Flame Cutting has been a reliable solution across many industries for years. With modern advancements and the digitization of cutting technologies today, Flame Cutting has evolved into a more superior method of producing highly precise cuts at a reasonable price. {Company name}'s commitment to providing exceptional Flame Cutting services and utilizing modern technology has earned it a reputation as a leading provider in the metal industry.
How to Plasma Cut Stainless Steel Using Nitrogen Gas
Plasma Cutting Stainless Steel With Nitrogen: A New Era of Precision ManufacturingManufacturing precision components has always been a challenging task, requiring highly specialized equipment and skilled workers. To meet market demands, manufacturing companies are constantly seeking new and innovative methods to improve production efficiency and maintain the highest standards of quality. One such method is plasma cutting with nitrogen, a cutting-edge technology that has revolutionized the way in which stainless steel components are manufactured. Here, we explore the latest developments in the field of plasma cutting with nitrogen, its advantages, and the companies that are leading the way.What is Plasma Cutting with Nitrogen?Plasma cutting is a technique used to cut materials, such as metals, using a high-temperature plasma arc. It works by passing an electrical current through a gas, such as oxygen or nitrogen, to generate a plasma arc that can melt through metal. By manipulating the arc's intensity and jet's velocity, the operator can control the quality of the cut and ensure a fine finish. Plasma cutting is widely used in metal fabrication as it allows the creation of intricate shapes and designs in a variety of materials, including stainless steel.Specifically, plasma cutting with nitrogen is a process that uses pure nitrogen gas as the cutting medium. Compared to plasma cutting with oxygen, nitrogen provides a cleaner cut and minimizes the risk of oxidation or discoloration of the cut edge. Because nitrogen is an inert gas, it also creates a safer working environment for operators and reduces the risk of fire.Advantages of Plasma Cutting with NitrogenThe benefits of cutting stainless steel with plasma and nitrogen are numerous. Firstly, the process can handle stainless steel's high reflective nature and thicker gauge metals. Secondly, the method can boost productivity while reducing waste by limiting aspects like kerf width and dross production. The cleaner cuts and minimal bevel make for faster removal of excess material and the ability to reduce labor-intensive grinding and cleaning. Cutting with nitrogen produces minimal thermal distortion, ensuring the final parts maintain tight tolerances.The process is also highly flexible, allowing workers to cut shapes or designs on a customer's request with relative ease. With this technique, the cutting's quality, accuracy, and finish are impeccable every single time. And since nitrogen is a non-reactive gas, the risk of oxidization, warping, or disfigurement of the metal is eliminated. This reduces the chances of rework, saving both time and money.Companies Making Strides In Plasma Cutting With NitrogenOne of the enterprises making significant strides in plasma cutting with nitrogen is {Unnamed company}. Founded in {year}, this young company has established itself as a leading player in the precision manufacturing industry. With the mission of providing the highest quality metal cutting services, the company has invested in the latest equipment and technology to stay ahead of the curve.To that end, the company has adopted plasma cutting techniques with nitrogen to achieve unparalleled precision and quality in its metal fabrication processes. Equipped with a state-of-the-art CNC machine, the company can cut intricate shapes and designs into stainless steel with remarkable accuracy and speed. With such precision, the company can fulfill custom orders on a tight schedule while maintaining exceptional quality.{Unnamed company} is also renowned for investing in its people. They employ a team of highly skilled technicians who remain dedicated to the company's philosophy by delivering high-quality products and services to customers. Committed to innovation, they seek to leverage the latest techniques and technology to enhance their services, continually pushing the boundaries of what's possible.Final ThoughtsWithout a doubt, plasma cutting with nitrogen is an innovative manufacturing process that has revolutionized the world of metal cutting. Stainless steel, a notoriously difficult material to cut, has become easier to manage and meet the precision demands. Thanks to this method's accuracy, speed, and superior quality finishes, manufacturers are now capable of delivering precision components that are beyond excellence. As for {Unnamed company}, this forward-thinking enterprise is leading the way in this manufacturing process, continually seeking to refine its services for the benefit of its customers. When it comes to plasma cutting with nitrogen, there’s no doubt that the future remains bright.
Techniques for Welding Thin Sheets of Stainless Steel
Welding Thin Stainless Steel: Tips and Tricks for Perfect WeldsStainless steel is a popular choice of material for many applications due to its corrosion resistance, durability, and aesthetic appeal. However, welding thin sheets of stainless steel can be a challenging task, requiring careful preparation, skill, and the right equipment. In this blog post, we will provide some tips and tricks for welding thin stainless steel, including the use of advanced welding techniques and tools to achieve the perfect weld.PreparationBefore you begin welding thin stainless steel sheets, it is essential to prepare the workpiece properly. First, ensure that the surfaces to be welded are clean and free of any contaminants that may affect the quality of the weld. Use a degreaser or solvent to remove any oil, dirt, grease or oxide layers that may be present on the surface. You can also use a wire brush or grinder to remove the oxide layer and create a clean surface for welding.Next, ensure that the edges of the workpieces are aligned properly, with an even gap of around 1-2mm between them. A precise fit is essential for achieving a good weld, so take the time to check and recheck the alignment before beginning the welding process.TechniquesSeveral advanced welding techniques can be used to weld thin sheets of stainless steel, including TIG (Tungsten Inert Gas) welding and laser welding. TIG welding is a popular choice for welding thin stainless steel sheets because it offers precise control over the welding process, a high-quality finish, and the ability to weld various types of stainless steel.With TIG welding, the torch is held by the welder, and the other line feeds behind the weld using parts of pie plates and other forms of bendy stuff to dam the argon behind the weld. This technique ensures that the weld is protected by an argon gas shield, preventing the weld from being contaminated by oxygen and other atmospheric gases.Another option for welding thin stainless steel is laser welding. Laser welding uses a high-energy laser beam to join the workpieces, resulting in a precise, high-quality weld. Laser welding is particularly useful for welding complex shapes and contours, and it is ideal for welding thin sheets of stainless steel, where precision is essential.ToolsTo achieve the perfect weld on thin stainless steel, it is essential to have the right tools. Some of the key tools you will need for welding thin sheets of stainless steel include a TIG welding machine, a suitable electrode, filler wire, and an argon gas cylinder.A high-quality TIG welding machine is essential for achieving precise control over the welding process, enabling you to adjust the weld speed, current, and voltage for optimal results. The right electrode and filler wire are also critical, as they dictate the quality and strength of the weld.ConclusionWelding thin sheets of stainless steel requires careful preparation, skill, and the right equipment. By following the tips and tricks outlined in this blog post, including proper preparation, advanced welding techniques, and the use of quality tools, you can achieve perfect welds every time. Whether you choose TIG welding or laser welding, remember to take your time, stay focused, and enjoy the impressive results that you can achieve with thin steel.