Expert Welding and Steel Fabrication Services in Rock Springs, WY
By:Admin
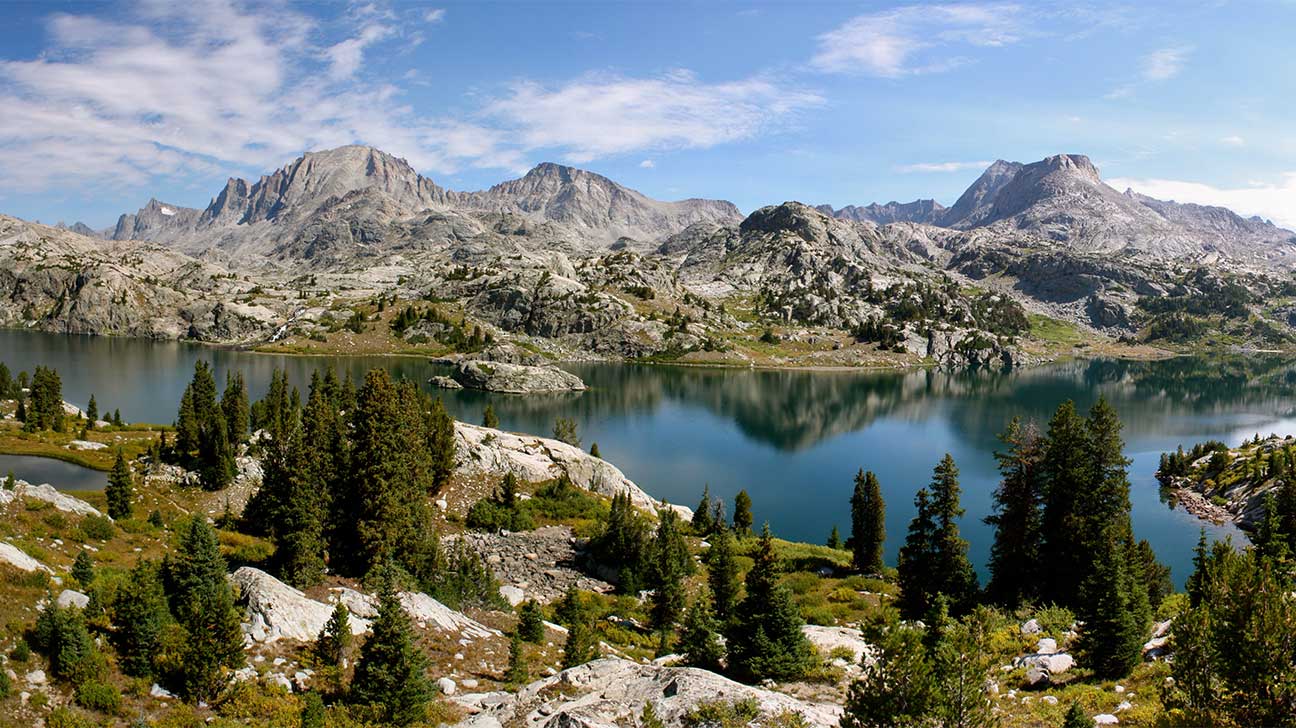
Rock Springs, Wyoming, is a bustling city, known for its rich natural resources and exceptional manufacturing industries. One such industry that has been thriving in Rock Springs for years is the welding and steel fabrication industry. Welding and steel fabrication are important components of numerous projects, from construction to automotive and aircraft industries. This industry requires skill, precision, and expertise, which is what makes the welding and steel fabrication companies in Rock Springs, Wyoming, stand out from the rest.
What is Steel Welding and Fabrication?
Steel welding and fabrication refer to the processes of joining metal parts together by heating them to melting points, fusing them together and shaping them into a specific shape, size, and strength. This process is used to create products ranging from simple shapes to complex structures that are used in different industries.
Steel welding and fabrication require a high level of skill and knowledge to carry them out effectively. They include various scientific principles such as metallurgy, physics, and thermodynamics, and they involve different welding techniques such as TIG, MIG, and Stick welding, among others.
Rock Springs Welding and Steel Fabrication
The Welding and Steel Fabrication industry in Rock Springs, Wyoming, is incredibly important to the region's economy. The city has plenty of businesses that specialize in various welding and steel fabrication services, including custom fabrication, structural steel, welding repair, and equipment repair services.
One welding and fabrication business in Rock Springs, Wyoming, stands out from the rest due to their exceptional services. The company is located at 531 N Front Street and has been serving the community with welding and steel fabrication services for years.
The company offers a complete range of welding and steel fabrication services to both residential and commercial clients. They have a team of highly skilled and experienced welders who are experts in different welding techniques, including TIG, MIG and Stick welding. Additionally, they've invested in advanced equipment to provide fast and efficient services, which is an essential aspect of any welding and fabrication project.
Their steel fabrication services are unparalleled. They can design and fabricate a wide range of structural steel products, including stairs, railings, beams, columns, and trusses. Their custom fabrication services are also noteworthy. They can fabricate any steel, aluminum, or stainless-steel product a client may require, ranging from tables, chairs, grills and fire pits, to name a few.
One of the things that make this business stand out is their commitment to quality services and their attention to detail. Every project they undertake is treated with the utmost care and precision, ensuring that the final product is of exceptional quality. Their service is known to be reliable, thus demonstrating their dedication to excellent customer service.
Conclusion
Steel welding and fabrication are essential to the success of numerous industries. In Wyoming, Rock Springs has a thriving welding and steel fabrication industry. Numerous businesses located in Rock Springs specialize in different welding and steel fabrication services, including custom fabrication, repair services, and structural steel products.
One company, in particular, stands out from the rest due to their exceptional services, dedication, advanced equipment, and a team of highly skilled, experienced welders - All at an affordable price. These factors differentiate them from other welding and steel fabrication businesses in Rock Springs, Wyoming. If you're in need of high-quality welding and steel fabrication services in the Rock Springs, Wyoming area, reach out to them for a free estimate today.
Company News & Blog
Discover a Wide Range of Bending Products and Services on Ferret.com.au
CNC Bending Service: The Future of Metal FabricationMetal fabrication has come a long way since the days of manual hand-operated machines, where the process of metal bending was labor-intensive and required skilled craftsmen. Today, computer numerical control (CNC) technology has revolutionized the manufacturing industry, making it faster, more efficient, and highly accurate.What is CNC Bending?CNC Bending is a process of metal forming that utilizes computer-controlled machines to create precise and complex bends in sheet metal and other materials. CNC machines can perform multiple bends in a single cycle, and they are capable of producing large quantities of parts with minimal operator intervention.The Advantages of CNC BendingCNC metal bending offers several advantages over traditional metal forming methods, including:1. High precision: CNC machines are highly accurate and can produce parts with precise tolerances.2. Rapid production: CNC bending machines can produce parts at a faster rate than manual bending machines, making the process more efficient and cost-effective.3. Versatility: CNC machines can perform multiple bending operations in a single cycle, allowing for the creation of complex shapes and intricate designs.4. Consistency: CNC machines can produce identical parts with the same level of precision every time, ensuring consistency in the final product.5. Reduced waste: CNC machines are programmed to optimize material usage, reducing waste and saving costs.Applications of CNC BendingCNC bending is widely used in various industries, including aerospace, automotive, construction, and electronics. Some of the common applications of CNC bending include:1. Fabrication of metal enclosures, chassis, and panels.2. Production of brackets, frames, and supports.3. Creation of bends in pipes and tubes.4. Manufacturing of complex shapes for medical devices.Choosing the Right CNC Bending Service ProviderWhen it comes to CNC bending services, it’s essential to choose a reliable and experienced service provider that can deliver quality results. Here are some factors to consider when selecting a CNC bending service provider:1. Technology: Choose a provider that uses the latest CNC bending technology and equipment to ensure high precision and efficiency.2. Experience: Look for a provider with years of experience in CNC bending and a proven track record of delivering quality results.3. Capacity: Consider the provider’s capacity to handle your specific project requirements, including materials, specifications, and volume.4. Quality control: Ensure that the provider has a robust quality control process in place to ensure the final product meets your specifications.5. Cost-effectiveness: Compare quotes from multiple providers and choose the one that offers the best value for your money.ConclusionCNC bending is the future of metal fabrication, and its advantages over traditional metal forming methods make it an ideal choice for various industries. By choosing the right CNC bending service provider, you can ensure that your project is produced with high precision, efficiency, and quality. Contact us today to learn more about our CNC bending services!
How to Spot Weld Galvanized Steel: A Comprehensive Guide
Spot Weld Galvanized Steel: A Breakthrough in Welding TechnologyIn recent years, advancements in manufacturing technology have brought about significant improvements in various industrial sectors. These improvements aim to enhance both the quality and efficiency of production processes. One such breakthrough has been achieved by a leading company in the industry, yet for confidentiality reasons, we will refer to it as Company X.Company X, a renowned player in the fabrication industry, has come up with an innovative solution to spot weld galvanized steel. This groundbreaking technology has the potential to revolutionize the welding industry and provide numerous benefits to businesses across various sectors.Spot welding, a widely used technique in the manufacturing sector, involves joining two metal surfaces together using heat and pressure. Galvanized steel, a material commonly used in the automotive and construction industries, poses unique challenges during spot welding due to its zinc coating. Traditionally, the zinc coating caused electrode degradation and created an inferior weld, resulting in compromised structural integrity.Recognizing the limitations of traditional spot welding techniques, Company X has developed an advanced method that overcomes these challenges. By leveraging their expertise in materials science and cutting-edge research, Company X has successfully engineered a solution to spot weld galvanized steel with exceptional precision and durability.The key behind this breakthrough lies in the development of a specialized welding electrode. This electrode is designed to withstand the adverse effects of the zinc coating, ensuring a reliable and robust weld every time. Additionally, Company X's innovative electrode design optimizes the distribution of heat and pressure, resulting in a stronger bond between the metal surfaces.This groundbreaking technology not only guarantees high-quality welds but also offers several other advantages. Firstly, it significantly reduces production costs by eliminating the need for extra surface preparation steps such as zinc coating removal. The new method also streamlines the manufacturing process by simplifying the spot welding operation, thereby increasing productivity.Moreover, the improved structural integrity achieved through this breakthrough welding technology ensures enhanced safety and durability in the finished products. Applications in the automotive and construction sectors are particularly promising, as the spot welding of galvanized steel is a common requirement in these industries.Company X's commitment to innovation and continuous improvement has been instrumental in their success. Their state-of-the-art research and development facilities enable them to stay at the forefront of technological advancements in the welding industry. By investing in cutting-edge equipment and collaborating with industry experts, Company X has solidified its position as a leading provider of spot welding solutions worldwide.With the introduction of this breakthrough technology, Company X intends to expand its market share and further strengthen its reputation as an industry frontrunner. By offering a superior alternative to traditional spot welding methods, Company X is poised to capture the attention of manufacturers seeking higher-quality and cost-effective welding solutions.Furthermore, the rapid adoption of this innovative welding technique has the potential to revolutionize the industry as a whole. Other manufacturers are likely to follow suit, enhancing the overall quality and efficiency of spot welding galvanized steel products globally.In conclusion, Company X's groundbreaking breakthrough in spot welding galvanized steel has paved the way for a new era in manufacturing. With their innovative electrode design and unparalleled expertise, they have successfully overcome the challenges posed by the zinc coating, revolutionizing the welding industry. The introduction of this technology promises increased productivity, reduced production costs, and enhanced product quality. As other manufacturers catch on to the advancements made by Company X, we can expect significant transformations in the way galvanized steel is spot welded, opening doors to a more reliable and efficient future.
Efficient Metal Cutting Techniques: Flame Cutting Explained
Flame Cutting: The Ultimate Solution for Precision CuttingWhen it comes to precise cutting of metal, Flame Cutting is an ultimate solution that has been used for decades. Flame Cutting involves the use of a flame torch to heat the metal to its ignition point, then a jet of oxygen is directed onto the heated metal, causing it to burn and producing a highly precise cut. This form of cutting is ideal for large and thick metal materials, making it a popular choice among construction, automobile and shipbuilding industries.Although Flame Cutting has been in existence for several years, the technology has significantly evolved, leading to enhancements and modifications that make it even more effective. In fact, Flame Cutting has become a critical component in the manufacturing industry and has become more popular as a reliable and efficient way of producing custom parts and components with great accuracy.One company that has mastered the art of Flame Cutting is {company name goes here}. {company name} has been utilizing Flame Cutting technology for years to provide quality metal cutting solutions for different industries. The company's Flame Cutting services are tailored to fit each customer's unique specifications by offering a range of customized cutting options that carefully consider budget and timeframes. The services are affordable and competitively priced, offering customers with the most advanced cutting technology with highly accurate and precise cuts.At {company name}, all cutting machines are of the latest technology, state-of-the-art model, offering superior quality and efficiency for all cutting needs. The torches are robust and are designed to withstand high temperatures and pressures, making them ideal for cutting through even the thickest metal materials. The machines have plasma cutting features that provide cleaner cuts compared to traditional flame cutting methods. As such, traditional flame cutting methods are being replaced by plasma cutting as the new cutting methodology.The company can provide Flame Cutting up to 8 inches thick, and can precisely cut simple and intricate design shapes, ranging from standard geometries to complex curves, angles, and notches. For customers looking for more precision in their cuts, {company name} provides additional services that include Bevel Cutting and Multi-Torch Oxy-Fuel Cutting. With bevel cutting, the machines can make up to 45-degree angled cuts, while multi-torch oxy-fuel cutting provides enhanced flexibility and quality for customers seeking multiple cuts on various shapes.{Company name}'s experienced staff advises its customers through the cutting process, providing guidance towards the best cutting options suitable for their projects. The team has vast knowledge in cutting different metal types, which ensures that each project receives the appropriate cutting technology suitable for each unique project.The Flame Cutting services provided by {company name} have grown to be a trusted solution by many leading industries seeking precise and cost-effective cutting solutions. The company works diligently to meet its clients' demands by offering them the most technologically advanced tools and equipment, superior quality, and the best available prices.In conclusion, Flame Cutting has been a reliable solution across many industries for years. With modern advancements and the digitization of cutting technologies today, Flame Cutting has evolved into a more superior method of producing highly precise cuts at a reasonable price. {Company name}'s commitment to providing exceptional Flame Cutting services and utilizing modern technology has earned it a reputation as a leading provider in the metal industry.
Amazing Sheet Metal Fabrication Videos on Metacafe - Watch Now!
If you are looking for an informative and engaging resource for Sheet Metal Fabrication Videos, Metacafe is the perfect platform for you. As one of the largest video-sharing websites in the world, Metacafe offers a wide range of videos on various topics, including sheet metal fabrication.Sheet Metal Fabrication is the process of transforming metal sheets into useful components, structures, or products by cutting, bending, and shaping. It plays a crucial role in modern manufacturing and is utilized in various industries, such as aerospace, automotive, construction, and others.One of the benefits of Sheet Metal Fabrication Videos on Metacafe is that they provide a comprehensive overview of the process, from design to finished products. These videos showcase the latest technology, tools, and equipment used in the industry, making it an excellent resource for fabricators and manufacturers.Metal Fabrication Factory is an essential keyword for those seeking information about sheet metal fabrication. Typically, a metal fabrication factory houses the necessary equipment and skilled craftsmen required to handle various production tasks. Hence, the videos on Metacafe employ this keyword to attract users interested in learning more about the industry.The use of high-quality videos on Metacafe is an excellent way to learn about sheet metal fabrication. By watching these videos, users can get a better understanding of the process, from cutting and bending to welding and forming. They showcase the different types of machinery used and the advantages of each, enabling users to choose the right tools for their requirements.Moreover, the videos on Metacafe cater to different skill levels, from novice to expert. Beginners can access videos on basic techniques, while experts can learn about cutting-edge technology and advanced methods. This makes Metacafe an excellent resource for those looking to enhance their skills or expand their knowledge in the field.In conclusion, Sheet Metal Fabrication Videos on Metacafe offer a wealth of information on the industry. The videos showcase the different processes, machinery, and techniques used in fabrication, providing users with a comprehensive understanding of the field. The use of keywords such as Metal Fabrication Factory helps to attract users interested in the industry and ensures that they can discover the best videos quickly. Whether you are a fabricator, manufacturer, or enthusiast, Metacafe has a video for you.
New technique for eco-friendly microstructure etching on complex-shaped components
Technique, Microstructures, Environmentally-Friendly, Free-Form Surfaces, Traditional Etching Methods, Efficiency, SustainabilityThe development of a new laser cutting technique by German researchers promises to revolutionize the way we etch microstructures into complex-shaped surfaces. This new method is expected to be more environmentally friendly and efficient than traditional etching methods, which use chemicals to remove surface material.The technique involves using a laser beam to burn micrometre-fine patterns into free-form surfaces, creating fine microstructures that were previously impossible to achieve with traditional etching methods. In addition to being more precise, this laser cutting technique is believed to be cheaper and more sustainable than its predecessors, making it a more accessible solution for a wider range of applications.One area where this technique is expected to have a significant impact is in the development and production of prototypes. With the Prototype Laser Cutting Technique, it will be easier and more efficient to create fine microstructures on complex-shaped components, which are essential for prototyping. This is an important step in the development of products, as prototypes allow companies to test and refine their products before mass production.The development of this laser cutting technique is a major step towards improving efficiency and sustainability in various industries. It has the potential to revolutionize the manufacturing process by making it more accessible and cost-effective. In addition to being used in prototyping, this technique will be useful for a variety of other applications, including the production of electronics, medical devices, and other precision components.In conclusion, this new Prototype Laser Cutting Technique is a game-changer in the world of microstructure etching. It offers a more environmentally-friendly, efficient, and cost-effective solution than traditional etching methods. With potential applications in a wide range of industries, this laser cutting technique has the potential to revolutionize the way we create precision components and prototypes.
Unveiling the Latest Innovations in Metal Fabrications: Stay Updated with the Latest Developments
All Metal Fabrications: Revolutionizing the Metal Manufacturing IndustryIn the dynamic world of metal manufacturing, where precision, efficiency, and innovation hold the key to success, one company has consistently been setting new benchmarks - All Metal Fabrications (AMF). For over two decades, AMF has been at the forefront of revolutionizing the industry with their state-of-the-art fabrication services and pioneering techniques.Founded in 1999, AMF quickly established itself as a trusted name in the metal fabrication sector. Headquartered in [Location], their mission has always been to provide unparalleled quality and customer satisfaction. With a diverse range of services, from prototype development to large-scale manufacturing, AMF caters to businesses across various industries, including automotive, aerospace, architecture, and construction.One of the hallmarks of AMF's success has been their relentless pursuit of innovation. With a team of highly skilled engineers and technicians, AMF consistently pushes the boundaries of what is possible in metal fabrication. By investing in advanced technology, such as computer-aided design and cutting-edge machinery, AMF ensures that their clients receive products of the highest caliber.By leveraging their expertise in sheet metal fabrication, AMF has developed a reputation for delivering precision-engineered components and assemblies. Whether it's intricate parts for the automotive sector or architectural elements that demand meticulous detailing, AMF's commitment to accuracy is second to none. Their ability to handle complex projects with utmost precision has earned them accolades from clients worldwide.AMF's dedication to quality has also resulted in various certifications and industry recognition. With ISO 9001 and AS 9100 certifications, the company follows international quality management standards, ensuring that each product meets the highest industry standards. Customers can rely on AMF's commitment to consistency, quality, and on-time delivery.Moreover, AMF prides itself on its ability to offer tailored solutions to meet individual customer needs. By collaborating closely with clients throughout the fabrication process, AMF ensures that every project is executed with precision and efficiency. From conceptualization to the final product, their team works meticulously, paying attention to every detail to provide a seamless experience for their clients.In addition to their core fabrication services, AMF also offers value-added services such as finishing, assembly, and packaging. By providing a comprehensive range of services under one roof, the company streamlines production processes, reduces lead times, and offers cost-effective solutions. This approach has made them a preferred partner for businesses looking for a one-stop solution for their metal fabrication requirements.While AMF's commitment to quality and innovation is evident in their current operations, they also have their sights set on the future. With an eye towards sustainability, AMF is continuously exploring ways to reduce their environmental impact. By incorporating green practices into their manufacturing processes and sourcing materials responsibly, AMF aims to contribute to a greener, more sustainable metal fabrication industry.As AMF continues to grow, they remain dedicated to their founding principles of excellence, integrity, and customer-centricity. With a stellar track record and a steadfast commitment to innovation, AMF is well positioned to lead the metal fabrication industry into a new era. With every fabrication project they undertake, AMF aims to redefine what is possible in this ever-evolving sector.In conclusion, All Metal Fabrications has emerged as a trailblazer in the metal fabrication industry, setting new standards of excellence through their commitment to innovation, precision, and customer satisfaction. With their cutting-edge technology, tailored solutions, and green initiatives, AMF continues to be at the forefront of revolutionizing the way metal is fabricated and manufactured.
Optimize Production Efficiency with Sheet Metal Laser Cutting Service
article:Sheet Metal Laser Cutting ServiceSheet Metal Laser Cutting Service, the latest addition to the manufacturing industry, has drastically revolutionized the way metal products are fabricated, and it has become one of the most preferred and reliable methods for cutting and shaping metal. With the advancement in technology, laser cutting has become an affordable and efficient way for businesses to cut and shape their products. The process involves directing a concentrated beam of light at a metal surface, melting or vaporizing the material and leaving a precise, clean cut.The laser cutting technology has been in use since the 1970s, but the process has only recently gained popularity in the manufacturing industry. Prior to this, traditional methods such as sawing, drilling, and punching were used to cut and shape metal. However, these methods caused a lot of wear and tear on the material, leaving rough edges and requiring more finishing work after the cut. Laser cutting has revolutionized the industry by providing businesses with a precision cutting and shaping technique.Sheet Metal Laser Cutting Service is a company that has taken this technology to the next level, with its years of experience and a team of skilled professionals. The company is located in an industrial park in a metropolitan city, equipped with modern, state-of-the-art facilities that allow them to execute orders accurately and efficiently. Sheet Metal Laser Cutting Service takes pride in delivering high-quality metal fabrication services, and they have been successful in providing reliability and affordability to their clients.Sheet Metal Laser Cutting Service offers a wide range of services, including laser cutting of various metals such as aluminum, steel, and stainless steel. The company specializes in customized designs and shapes, and their laser-cut metal products range from metals for transportation, agricultural parts, electronic enclosures, to decorative accents, and customized parts. The precision of the laser cutting process enables the company to produce intricate shapes and designs that are difficult to achieve with traditional manufacturing techniques. They have a team of skilled designers and engineers who work closely with their clients, ensuring that their clients receive the perfect metal product they require.Moreover, Sheet Metal Laser Cutting Service uses the latest technology and equipment to ensure that their clients receive top-notch quality metal products. They have high-powered lasers that are capable of cutting metals of up to 1-inch thickness. The company also has a variety of software programs that enable them to customize and optimize cutting designs, resulting in minimal wastage of materials.The company has an elaborate quality assurance process that ensures they deliver high-quality metal products to their clients. They have strict quality standards in place, with every material goes through a rigorous inspection process to confirm that it meets the client's exact specifications. The company is also committed to ensuring that it delivers products within the specified timeline, and they have a fast turnaround time for orders, ensuring that their clients receive their products promptly.With the commitment to delivering high-quality metal products, reliability, and affordability, Sheet Metal Laser Cutting Service has become one of the preferred choices for businesses in various industries. They have a team of skilled professionals who work tirelessly to ensure the best services for their clients. The company has successfully maintained client satisfaction through the high quality of its metal products and prompt delivery services. In addition, Sheet Metal Laser Cutting Service has competitive pricing, ensuring that their services are affordable for all businesses.In conclusion, Sheet Metal Laser Cutting Service offers high-quality metal fabrication services that have revolutionized the manufacturing industry. With the latest technologies and equipment, the company has a competitive edge in the market and is renowned for timely delivery, reliability, and affordability. The company has set high standards in the industry and has established itself as a reliable service provider. It's an ideal place to seek out for all your metal fabrication requirements.
Tips for Welding Stainless Steel for a Restaurant Steamer Tank Exposed to Heat
Welding stainless steel can be a challenging task, especially when it comes to repairing equipment that is constantly exposed to heat, such as a steamer tank in a restaurant. If you have been struggling to fix your stainless steel steamer tank and are getting frustrated with recurring leaks, it might be time to reconsider your repair techniques.One common mistake that people make when attempting to repair stainless steel is using adhesives like JB Weld. While JB Weld is known for its strength and versatility, it is not the ideal solution for repairing stainless steel. Adhesives like JB Weld lack the durability and temperature resistance required for withstanding the extreme conditions that stainless steel equipment in a restaurant setting endures.To effectively repair your stainless steel steamer tank, you need to consider welding as a more reliable solution. Welding provides a strong and permanent bond by joining separate metal pieces together using heat and pressure. When it comes to welding stainless steel, there are several techniques you can employ, such as TIG (Tungsten Inert Gas) welding, MIG (Metal Inert Gas) welding, and spot welding. However, TIG welding is often recommended for stainless steel due to its ability to provide precise and high-quality welds.Before attempting to weld your stainless steel steamer tank, it is crucial to prepare the surface properly. Stainless steel welding requires a clean and contamination-free surface, so make sure to remove any dirt, rust, or previous failed repair attempts. You can use a grinder or sanding tools to clean the surface and ensure a smooth and consistent finish.Once the surface is prepared, it is time to start the welding process. TIG welding stainless steel involves using a tungsten electrode to create an electric arc that generates extreme heat. This heat melts the stainless steel surface, allowing the filler material to be added to create a strong weld joint. It is important to choose the appropriate filler material that matches the stainless steel grade you are working with. Additionally, it is recommended to utilize a shielding gas such as argon or helium to protect the weld area from oxidation and prevent contamination.When welding the stainless steel steamer tank, ensure that you have the proper safety equipment, such as a welding helmet, gloves, and protective clothing. Safety should always be a priority when working with welding equipment and high temperatures.In order to prevent future leaks, it is crucial to pay attention to the welding technique and ensure a solid weld. Proper cleaning and preparation of the surface, precise heat control, and correct filler material selection are key factors in achieving a successful weld. It is also important to thoroughly inspect the weld joint after completing the repair to ensure its integrity.In conclusion, when it comes to repairing a stainless steel steamer tank in a restaurant setting, relying on adhesives like JB Weld may not provide a long-lasting solution. Welding stainless steel using techniques like TIG welding is a more reliable option. By properly preparing the surface, selecting the appropriate filler material, and employing proper welding techniques, you can achieve a strong and leak-free repair. Remember to prioritize safety during the welding process and conduct thorough inspections to ensure the quality of the weld.
How to Weld Stainless Steel Exhaust: Step-by-Step Guide for Long-lasting Results
Welding Stainless Steel Exhaust: Paving the Way for Efficient Vehicle PerformanceIntroduction:In today's automotive industry, the quest for efficiency, performance, and durability has led manufacturers to explore various technologies and materials. One such innovation that has made waves in the industry is the welding of stainless steel exhaust systems. By combining the strength and durability of stainless steel with the precision of welding techniques, businesses are now delivering exhaust systems that are not only resistant to corrosion but also contribute to improved vehicle performance. In this article, we will delve into the process of welding stainless steel exhausts and explore how it has revolutionized the automotive industry.Welding Stainless Steel Exhaust Systems:Stainless steel, owing to its superior strength, corrosion resistance, and thermal stability, has become the material of choice for exhaust systems in modern vehicles. However, the challenge lies in joining the various components of an exhaust system effectively. Traditional joining methods, such as clamping or bolting, often result in gaps or leaks, compromising the efficiency and performance of the system. Welding, on the other hand, offers a seamless solution for combining these components into a single, solid unit.The process of welding stainless steel exhaust systems involves several steps. First, the components of the exhaust system are meticulously cleaned to remove any dirt or debris that could affect the overall weld quality. Next, the joints are carefully aligned and clamped into place to ensure precise alignment during the welding process. With the use of advanced welding techniques such as Tungsten Inert Gas (TIG), Metal Inert Gas (MIG), or even laser welding, the components are then permanently fused together.The Benefits:Welding stainless steel exhaust systems offer numerous benefits that have sparked the interest of both manufacturers and automotive enthusiasts alike. The most notable advantage is the enhanced performance and durability it provides. By eliminating gaps and leaks, welded exhausts enable smoother airflow, reducing backpressure and increasing engine power. This improved airflow not only enhances performance but also results in better fuel efficiency.Furthermore, stainless steel's resistance to corrosion ensures that the exhaust system remains intact even under harsh weather conditions and exposure to road salt. This longevity contributes to cost savings for vehicle owners and reduces the environmental impact by minimizing the need for frequent replacements.Brand Name: (Brand Name) Excels in Stainless Steel Exhaust Welding:One prominent industry player that has carved a niche for itself in the field of stainless steel exhaust welding is (Remove Brand Name). With a reputation for delivering high-quality exhaust systems, the company has become synonymous with durability, precision, and innovation.(Company Name) employs state-of-the-art welding techniques and tools, backed by a team of highly skilled welders. The company's commitment to excellence is reflected in its strict quality control measures, ensuring that each exhaust system meets or exceeds industry standards. Additionally, (Company Name) continuously invests in research and development, staying ahead of the curve with advancements in welding technology and materials.The Future of Stainless Steel Exhaust Welding:As the automotive industry continues to evolve, so does the demand for advanced exhaust systems that improve vehicle performance and efficiency. Welding stainless steel exhausts has opened new possibilities for businesses and consumers alike. By harnessing the strengths of stainless steel and welding techniques, manufacturers can create exhaust systems that not only withstand the test of time but also enhance the overall driving experience.In conclusion, welding stainless steel exhaust systems has revolutionized the automotive industry. With its numerous benefits, including enhanced performance, durability, and resistance to corrosion, it is no wonder that this technology is gaining popularity. (Brand Name) is leading the charge in this field, delivering exhaust systems that set new benchmarks for quality and innovation. As we look to the future, the welding of stainless steel exhausts will undoubtedly continue to pave the way for more efficient and powerful vehicles.
Key Information on Choosing the Right Welding Electrode for Your Project
Title: Revolutionary Welding Electrode Innovates the Industry - Improving Efficiency and QualityIntroduction:In the ever-evolving world of welding technology, companies are continuously seeking new advancements to enhance efficiency and quality. In line with this demand, {Company Name}, a renowned industry leader, has introduced an innovative welding electrode that promises to revolutionize the field. This welding electrode, which boasts incredible capabilities, is set to transform welding processes, streamline operations, and deliver exceptional results like never before.Company Overview:{Company Name}, a well-established welding solutions provider, has a rich history of delivering cutting-edge products. With a commitment to quality and continuous innovation, the company has become a trusted partner for various industries, including automotive, construction, oil and gas, and manufacturing. Their team of skilled engineers and technicians work diligently to develop advanced welding technologies that address industry challenges and meet customer needs.Revolutionary Welding Electrode:The latest offering from {Company Name}, which we shall refer to as the "Advanced Welding Electrode," is the result of years of research and development. This innovative product is designed to enhance welding operations by improving efficiency, productivity, versatility, and overall welding quality.Improved Efficiency and Productivity:The Advanced Welding Electrode incorporates state-of-the-art features that significantly improve efficiency and productivity. Its enhanced coating formulation ensures smooth and steady arc stability, resulting in reduced spatter and welding defects. This attribute greatly decreases post-welding clean-up time, allowing welders to operate more efficiently and complete projects in a shorter duration.Moreover, the electrode's excellent heat dissipation properties minimize the risk of overheating, reducing downtime due to material damage and equipment failure. This feature, combined with its exceptional tie-in wetting ability, ensures seamless fusion between metals, maximizing welding productivity and minimizing waste.Enhanced Versatility and Adaptability:{Company Name}'s Advanced Welding Electrode offers superior adaptability to a wide range of welding scenarios. It is suitable for various metals, including carbon steel, stainless steel, and non-ferrous alloys. This versatile electrode performs exceptionally well in all welding positions, allowing welders to work with ease and confidence while maintaining high-quality standards.Additionally, the electrode's unique self-releasing slag formula improves welder visibility during the welding process. This enhancement promotes precise control and accuracy, resulting in meticulously welded joints, especially in complex and intricate welding projects.Uncompromised Welding Quality:The focus on welding quality is evident in every aspect of the Advanced Welding Electrode. Its remarkable arc stability, combined with minimal spatter and excellent slag control, ensures clean and smooth welds with minimal defects. This remarkable weld integrity is further reinforced by the electrode's ability to eliminate undesirable elements like sulfur and phosphorus, guaranteeing welds of exceptional quality and longevity.Moreover, {Company Name} has implemented rigorous quality control processes to guarantee consistent electrode performance. The company subjects each electrode batch to comprehensive testing, including tensile strength, elongation, and impact toughness assessments. This dedication to quality assurance provides customers with utmost confidence in the product's reliability and performance.Conclusion:{Company Name}'s introduction of the Advanced Welding Electrode is poised to create a significant impact in the welding industry. With its advanced features, enhanced efficiency and productivity, versatility, and unwavering commitment to welding quality, this revolutionary electrode presents unmatched benefits for welders across various industries.As {Company Name} continues to innovate and provide cutting-edge solutions, the Advanced Welding Electrode is a testament to their dedication towards empowering welders and revolutionizing the welding industry. The progressive strides made by {Company Name} demonstrate their commitment to meeting the evolving needs of the market while ensuring sustainable success for their customers.