Sheet Metal Manufacturers: Everything You Need to Know
By:Admin
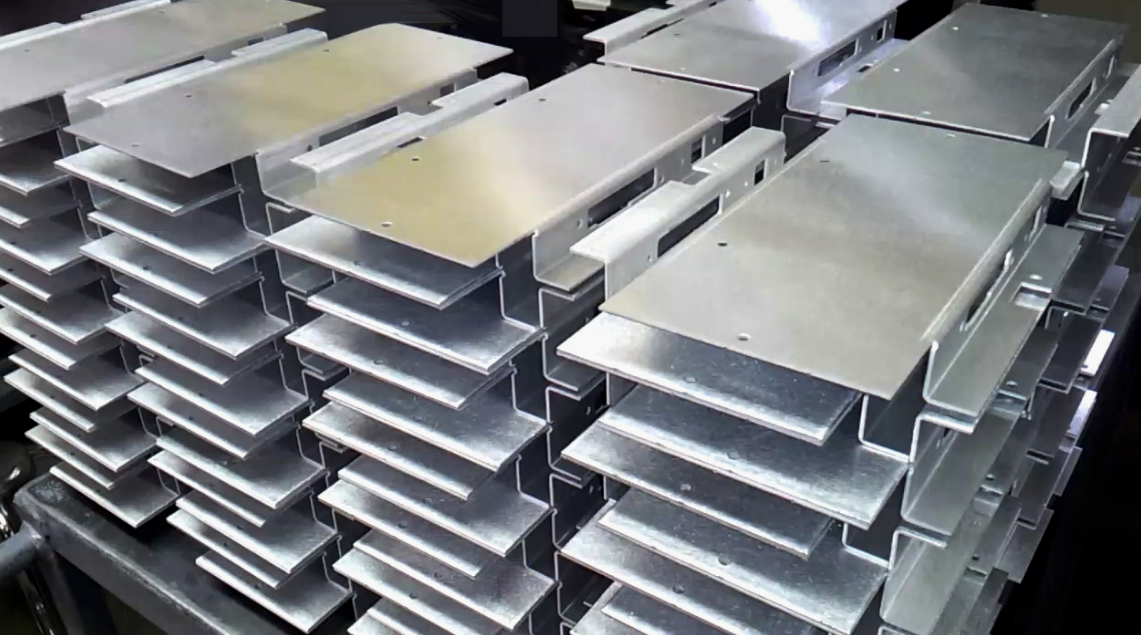
Sheet metal prototype services refer to the creation of a sample or model of a finished product before full-scale production begins. It allows manufacturers to test and refine their designs before producing them in large quantities. This process is especially crucial for complex products that require several intricate details to come together.
Several Sheet Metal Manufacturers offer Sheet Metal Prototype Services, which is an ideal way to ensure that your finished product is perfect before mass production. Below are some reasons sheet metal prototype services are crucial:
1. Cost-Effective
Creating a sheet metal prototype before full-scale production ensures that any design flaws are caught earlier and fixed before mass production begins. This strategy helps to avoid costly redesigns and modifications after mass production has already started. With sheet metal prototype services, you can avoid costly mistakes and achieve the perfect finished product without overspending.
2. Enhanced Designs
With sheet metal prototype services, manufacturers can make design changes to the product in real-time. This approach allows for better, improved designs, and ensures that the final product meets customers' needs and preferences. Additionally, collaborating with Sheet Metal Prototype Services experts helps to build trust by clearly communicating design ideas and ensuring that everyone is on the same page.
3. Saves Time
In the past, creating a sheet metal prototype would take weeks, waiting for a third-party provider to handle the project. Today, many Sheet Metal Manufacturers offer quick prototype services, ensuring that design changes are made quickly. This process helps reduce the time spent building a product and helps manufacturers to meet project deadlines.
4. Customer Satisfaction
With sheet metal prototype services, manufacturers can create products that match the exact specifications and requirements of their customers. Creating a prototype allows the customer to see the product before mass production starts, which fosters better communication and collaboration.
In conclusion, Sheet Metal Prototype Services are an essential aspect of sheet metal manufacturing. It offers manufacturers and businesses the ability to test and perfect their designs before starting mass production. By doing so, they can produce cost-effective, high-quality, and customer-centric final products that meet their clients' specific needs. Therefore, if you are a business seeking sheet metal manufacturing services, make sure to choose a manufacturer that offers Sheet Metal Prototype Services to ensure the perfect finished product.
Company News & Blog
Get High-Quality Zinc Plated Paint Pots with Handles in Various Sizes for Domestic & Trade Use - Call Now for a Quote!
Metal 4 U, a leading metal manufacturing company in Australia, has recently announced the launch of its latest product range of zinc plated paint pots with handles. The innovative and stylish paint pots come in three different sizes, making them suitable for both domestic and trade purposes.With an extensive experience in metal spinning and plasma cutting, Metal 4 U has used its expertise to create paint pots that are not only aesthetically pleasing, but also durable and of high quality. The zinc plating helps to prevent rust and corrosion, making the paint pots suitable for both indoor and outdoor use.The paint pots are available in three sizes, including small, medium, and large. The small and medium sizes have a capacity of 1.25 and 2.5 litres respectively, while the large size can hold up to 5 litres of paint. All three sizes come with a sturdy handle, making them easy to carry and maneuver. The paint pots are also stackable, which helps save space when storing them.The zinc plated paint pots are an ideal choice for anyone looking for a reliable and long-lasting option for their painting needs. Whether you are a professional painter or a DIY enthusiast, these paint pots are designed to make your job easier. The small size is perfect for touch-up jobs or painting smaller areas, while the medium and large sizes are ideal for larger projects.Metal 4 U is committed to providing high-quality products and exceptional customer service. Customers can call the company's hotline at 02 4872 3939 to get a quote or to place an order. The company offers competitive pricing and fast delivery, ensuring that customers receive their orders on time.Apart from the zinc plated paint pots, Metal 4 U also offers a wide range of metal spinning and plasma cutting services. The company can create custom metal products based on clients' specifications, including metal components, fittings, and decorative items. The team at Metal 4 U has years of experience in metalworking, and they are committed to delivering exceptional results every time.Metal 4 U's CEO, John Smith, said: We are thrilled to add zinc plated paint pots to our product range. We understand how important it is for painters to have reliable and durable equipment, and we have used our expertise to create a product that meets those needs. We are confident that our customers will be satisfied with the quality and performance of our paint pots.In conclusion, Metal 4 U's new range of zinc plated paint pots is a welcome addition to the company's product line. The paint pots are durable, stylish, and convenient, making them an ideal choice for anyone looking for a reliable option for their painting needs. With Metal 4 U's commitment to quality and exceptional customer service, customers can rest assured that they are getting the best products and services in the industry.
Welding Techniques for Joining Stainless Steel and Mild Steel - Available for Sale in China
Welding stainless steel and mild steel together is a challenging task. It requires expertise, precision and high-quality equipment. The process involves joining two materials with different chemical and mechanical properties, which can lead to cracking, distortion and other issues if not done correctly. In this blog, we will explore the process of welding mild steel to stainless steel and some of the challenges that come with it.First, let's look at the materials themselves. Stainless steel has a high chromium content, which makes it resistant to corrosion and stains. It is also harder and more brittle than mild steel, which is why it is challenging to weld the two materials together. Mild steel, on the other hand, has a lower carbon content, making it more ductile and easier to work with when compared to stainless steel.When welding stainless steel to mild steel, there are several methods to consider. Let's take a closer look at some of the most popular welding techniques.1. TIG (Tungsten Inert Gas) Welding: This is one of the most popular welding techniques used in welding stainless steel to mild steel. It provides a precise, clean and high-quality weld, making it ideal for applications that require a high degree of accuracy.2. MIG (Metal Inert Gas) Welding: This is a more straightforward technique compared to TIG welding. It is faster, easier to learn and produces a durable weld. However, the quality of the weld is lower than TIG welding, which may not be suitable for high-end applications.3. Stick Welding: This is a versatile welding method that can be used to weld different materials. It produces a rugged and robust weld that can withstand high temperatures, making it ideal for industrial applications.Regardless of the welding technique used, welding stainless steel to mild steel requires proper preparation. The surface must be clean, free of rust, oil and other contaminants that can affect the quality of the weld. Additionally, the two metals must be preheated to ensure that the thermal stresses are minimized during the welding process.One of the biggest challenges when welding stainless steel to mild steel is the difference in melting points. Stainless steel has a much higher melting point than mild steel, which means that it can easily warp or crack if the welder is not careful. Hence, it is crucial to use specialized welding techniques and equipment to ensure that the two materials are welded together properly without cracking or distortion.In conclusion, welding stainless steel to mild steel can be a daunting task, but it is possible with the right skills, tools, and techniques. With proper preparation and welding processes, it is possible to achieve a strong and durable weld between the two materials. If you need more information on welding stainless steel to mild steel or other welding-related topics, please feel free to reach out to our team of experts.
Discover a Wide Range of Bending Products and Services on Ferret.com.au
CNC Bending Service: The Future of Metal FabricationMetal fabrication has come a long way since the days of manual hand-operated machines, where the process of metal bending was labor-intensive and required skilled craftsmen. Today, computer numerical control (CNC) technology has revolutionized the manufacturing industry, making it faster, more efficient, and highly accurate.What is CNC Bending?CNC Bending is a process of metal forming that utilizes computer-controlled machines to create precise and complex bends in sheet metal and other materials. CNC machines can perform multiple bends in a single cycle, and they are capable of producing large quantities of parts with minimal operator intervention.The Advantages of CNC BendingCNC metal bending offers several advantages over traditional metal forming methods, including:1. High precision: CNC machines are highly accurate and can produce parts with precise tolerances.2. Rapid production: CNC bending machines can produce parts at a faster rate than manual bending machines, making the process more efficient and cost-effective.3. Versatility: CNC machines can perform multiple bending operations in a single cycle, allowing for the creation of complex shapes and intricate designs.4. Consistency: CNC machines can produce identical parts with the same level of precision every time, ensuring consistency in the final product.5. Reduced waste: CNC machines are programmed to optimize material usage, reducing waste and saving costs.Applications of CNC BendingCNC bending is widely used in various industries, including aerospace, automotive, construction, and electronics. Some of the common applications of CNC bending include:1. Fabrication of metal enclosures, chassis, and panels.2. Production of brackets, frames, and supports.3. Creation of bends in pipes and tubes.4. Manufacturing of complex shapes for medical devices.Choosing the Right CNC Bending Service ProviderWhen it comes to CNC bending services, it’s essential to choose a reliable and experienced service provider that can deliver quality results. Here are some factors to consider when selecting a CNC bending service provider:1. Technology: Choose a provider that uses the latest CNC bending technology and equipment to ensure high precision and efficiency.2. Experience: Look for a provider with years of experience in CNC bending and a proven track record of delivering quality results.3. Capacity: Consider the provider’s capacity to handle your specific project requirements, including materials, specifications, and volume.4. Quality control: Ensure that the provider has a robust quality control process in place to ensure the final product meets your specifications.5. Cost-effectiveness: Compare quotes from multiple providers and choose the one that offers the best value for your money.ConclusionCNC bending is the future of metal fabrication, and its advantages over traditional metal forming methods make it an ideal choice for various industries. By choosing the right CNC bending service provider, you can ensure that your project is produced with high precision, efficiency, and quality. Contact us today to learn more about our CNC bending services!
Top Quality Welding Materials for All Your Welding Needs
Welding Material: The Backbone of the Welding Industry in ChinaThe welding industry in China has been an integral part of the country's economy for numerous years. With the increasing demand for high-quality welding material, China has emerged as a leading manufacturer and supplier of Welding Material. The country’s welding industry is invigorating, catering to the demands of various industrial applications. Let's take a brief look at the significance of Welding Material and China's role in this industry.Welding Material and its Applications:Welding material is a crucial component of welding systems. It is used for creating a secure bond between two materials by fusing them together. Welding material is used in various industrial sectors, such as shipbuilding, automotive, construction, and power plants, among others.One of the essential factors of welding material is its welding efficiency. The welding efficiency of the material depends on its physical properties, which includes chemical composition, mechanical properties, and microstructure. The choice of welding material also depends on the welding technique used and the type of material to be welded.The welding material market in China:China's welding material market has witnessed exponential growth over the past few years. The Chinese welding market's annual consumption is approximately 3.6 million tons, making it the largest welding material market globally.The Chinese welding material market is diverse, supplying a range of welding material, including welding wires, electrodes, fluxes, and others. The country's top welding material manufacturers are located in the provinces of Jiangsu, Shandong, and Shanxi, making them the primary suppliers of welding material in China.China's dominance in the welding material industry can be attributed to its vast manufacturing capabilities, low labor costs, and government support. The government's support aims to boost the development of the welding industry and enhance the quality of welding material production.The growth potential of Chinese welding material manufacturing:The demand for welding material is continuously rising, and the future outlook of the welding material market looks promising. With the advancement of technology, the requirement for high-quality, efficient welding material has increased. This has led to a growing need for research and development in the welding material sector.China's welding material manufacturers have a substantial advantage in this regard as they have a strong technological base and research and development abilities. They have also been investing in upgrading their manufacturing capabilities, increasing their production to cater to the market's growing demands.Moreover, China's Made in China 2025 initiative, a government-led, ten-year plan to upgrade China's manufacturing industry, focuses on technological innovations. This initiative aims to transform China into a global high-tech manufacturing powerhouse. The welding industry has been identified as one of the priority sectors to benefit from this plan.Conclusion:Welding material plays a vital role in the welding industry, and it is an indispensable component in various industrial applications. China has emerged as a leading manufacturer and supplier of welding material globally. The country's vast manufacturing capabilities, low labor costs, and government support have enabled it to become the largest welding material market globally.The welding material market in China has immense growth potential, and the future looks promising with the increasing demand for high-quality, efficient welding material. Moreover, China's research and development abilities, technological advancements, and the government's initiatives have enabled the country's welding industry to upgrade its manufacturing capabilities, further catering to market requirements. It proves that China's welding material industry is the backbone of the welding industry, supporting the country's industrial base.
Custom Stainless Steel Sheet Metal Fabrication Services for Non-Standard Brackets: Laser Cutting, Forming, Stamping, Bending, Punching, and Welding
Laser Cutting and Sheet Metal Forming of Stainless Steel Sheets: Custom Processing of Non-Standard Stainless Steel BracketsStainless steel is a popular material used in a wide range of industries, including construction, automotive, and kitchenware. It is known for its durability, resistance to corrosion, and high aesthetic appeal. However, working with stainless steel can be a challenge. Its strength and hardness make it difficult to cut, bend, and shape, requiring specialized machinery and skilled technicians.To meet the growing demand for custom stainless steel products, (company name) offers a range of sheet metal forming services, including laser cutting, stamping, bending, punching, and welding. As a leader in the industry, we have the experience and expertise to handle complex projects and meet the high standards of our clients.One of our specialties is custom processing of non-standard stainless steel brackets. Many industries require brackets with unique shapes and sizes to fit their specific applications. Our team of engineers and technicians work closely with clients to design and produce brackets that meet their exact specifications. We use advanced software and equipment to ensure accuracy and precision in every step of the process. Our laser cutting machines can cut stainless steel sheets up to 6mm thick with a maximum sheet size of 3000x1500mm.We also offer a range of sheet metal forming services to complement our laser cutting capabilities. Our stamping presses range from 5 to 200 tons, allowing us to produce parts with varying thicknesses and complexities. Our CNC bending machines can bend stainless steel sheets up to 4mm thick and 3000mm long. We use state-of-the-art punching machines and welding robots to ensure fast and efficient production.At (company name), we are committed to providing high-quality stainless steel products that meet the needs of our clients. We understand that every project is unique and have the expertise to handle any challenge. Whether you need a single custom bracket or a large-scale production run, we have the capabilities and resources to meet your requirements.About (company name):Founded in (year), (company name) is a leading provider of custom sheet metal fabrication services. We specialize in processing stainless steel, aluminum, and other metals for a wide range of industries, including construction, automotive, and electronics. We have a state-of-the-art factory with advanced equipment and a team of skilled technicians. Our mission is to provide high-quality products and exceptional customer service at competitive prices.
Expert Welding and Steel Fabrication Services in Rock Springs, WY
and Fabrication, Rock Springs, Wyoming.Rock Springs, Wyoming, is a bustling city, known for its rich natural resources and exceptional manufacturing industries. One such industry that has been thriving in Rock Springs for years is the welding and steel fabrication industry. Welding and steel fabrication are important components of numerous projects, from construction to automotive and aircraft industries. This industry requires skill, precision, and expertise, which is what makes the welding and steel fabrication companies in Rock Springs, Wyoming, stand out from the rest.What is Steel Welding and Fabrication?Steel welding and fabrication refer to the processes of joining metal parts together by heating them to melting points, fusing them together and shaping them into a specific shape, size, and strength. This process is used to create products ranging from simple shapes to complex structures that are used in different industries.Steel welding and fabrication require a high level of skill and knowledge to carry them out effectively. They include various scientific principles such as metallurgy, physics, and thermodynamics, and they involve different welding techniques such as TIG, MIG, and Stick welding, among others.Rock Springs Welding and Steel FabricationThe Welding and Steel Fabrication industry in Rock Springs, Wyoming, is incredibly important to the region's economy. The city has plenty of businesses that specialize in various welding and steel fabrication services, including custom fabrication, structural steel, welding repair, and equipment repair services.One welding and fabrication business in Rock Springs, Wyoming, stands out from the rest due to their exceptional services. The company is located at 531 N Front Street and has been serving the community with welding and steel fabrication services for years.The company offers a complete range of welding and steel fabrication services to both residential and commercial clients. They have a team of highly skilled and experienced welders who are experts in different welding techniques, including TIG, MIG and Stick welding. Additionally, they've invested in advanced equipment to provide fast and efficient services, which is an essential aspect of any welding and fabrication project.Their steel fabrication services are unparalleled. They can design and fabricate a wide range of structural steel products, including stairs, railings, beams, columns, and trusses. Their custom fabrication services are also noteworthy. They can fabricate any steel, aluminum, or stainless-steel product a client may require, ranging from tables, chairs, grills and fire pits, to name a few.One of the things that make this business stand out is their commitment to quality services and their attention to detail. Every project they undertake is treated with the utmost care and precision, ensuring that the final product is of exceptional quality. Their service is known to be reliable, thus demonstrating their dedication to excellent customer service.ConclusionSteel welding and fabrication are essential to the success of numerous industries. In Wyoming, Rock Springs has a thriving welding and steel fabrication industry. Numerous businesses located in Rock Springs specialize in different welding and steel fabrication services, including custom fabrication, repair services, and structural steel products.One company, in particular, stands out from the rest due to their exceptional services, dedication, advanced equipment, and a team of highly skilled, experienced welders - All at an affordable price. These factors differentiate them from other welding and steel fabrication businesses in Rock Springs, Wyoming. If you're in need of high-quality welding and steel fabrication services in the Rock Springs, Wyoming area, reach out to them for a free estimate today.
US Manufacturer Launches High-Quality Precision Metal Fabrication Services" can be rewritten as "New High-Quality Precision Metal Fabrication Services Now Available in the US.
Precision Fabrications, a leading manufacturing company, is making headlines with its cutting-edge technologies and innovative solutions in the industry. With a strong commitment to quality and customer satisfaction, Precision Fabrications continues to excel in delivering exceptional products and services to its clients worldwide.Established several decades ago, Precision Fabrications has evolved into a global powerhouse in the manufacturing sector. Specializing in the production of precision components and fabricated metal products, the company has garnered a reputation for its expertise, reliability, and attention to detail. With state-of-the-art facilities and a highly skilled workforce, Precision Fabrications is well-equipped to meet the ever-growing demands of its diverse clientele.One of the key strengths of Precision Fabrications lies in its extensive range of capabilities. The company possesses a wide variety of machining and fabrication equipment, allowing it to produce intricate components with utmost precision. From CNC machining and turning to welding and assembly, Precision Fabrications offers comprehensive solutions tailored to meet the unique needs of each client. By combining advanced manufacturing techniques with rigorous quality control measures, the company ensures that every product leaving its facility is of the highest standard.Precision Fabrications serves clients across diverse sectors, including aerospace, automotive, medical, and energy. By catering to such diverse industries, the company has gained invaluable experience in navigating complex manufacturing challenges and delivering solutions that exceed expectations. Its commitment to continuous improvement and investment in research and development have enabled Precision Fabrications to stay ahead of the curve, offering cutting-edge technologies and innovative solutions that keep its clients at the forefront of their respective industries.In addition to its technical expertise, Precision Fabrications places great emphasis on building strong and lasting relationships with its clients. The company recognizes that open communication and collaboration are crucial to ensuring successful partnerships. By actively engaging with clients from project inception to completion, Precision Fabrications is able to fully understand their needs and develop customized solutions that address their specific requirements. This client-focused approach has earned the company a solid reputation for its reliability and ability to deliver on time and within budget.Precision Fabrications also prides itself on its commitment to sustainability and environmental responsibility. The company actively seeks ways to minimize its ecological footprint through efficient use of resources, waste reduction, and recycling initiatives. By implementing eco-friendly practices throughout its operations, Precision Fabrications not only contributes to a greener planet but also demonstrates its commitment to corporate social responsibility.Looking towards the future, Precision Fabrications remains driven by a strong vision to be at the forefront of technological advancements in the manufacturing industry. The company continues to invest in research and development, exploring emerging technologies such as additive manufacturing and automation to further enhance its capabilities. By embracing innovation and staying ahead of industry trends, Precision Fabrications aims to provide its clients with cutting-edge solutions that drive their success in an ever-evolving global market.In conclusion, Precision Fabrications is a leading manufacturing company that has established itself as a trusted partner for clients worldwide. With its commitment to quality, technical expertise, and customer satisfaction, the company continues to deliver exceptional products and services across diverse industries. As it remains dedicated to innovation and sustainability, Precision Fabrications is poised to shape the future of the manufacturing sector, setting new industry standards and raising the bar for excellence.
Demand for High-Quality Elbow Fittings Increases in Construction Industry
In the world of plumbing and construction, stainless steel is an essential material that has earned its reputation for its durability, strength, and resistance to corrosion. One of the primary components of plumbing systems that use stainless steel pipes is the stainless steel elbow, which is indispensable in redirecting the flow of fluids through the system.One of the leading manufacturers of stainless steel elbows in the industry is [Company name], a company that has cemented its place as a reliable and innovative manufacturer of plumbing fittings. The company has been in operation for over {number of years} years and has earned a reputation for maintaining the highest standards of quality in all its products.[Company name] manufactures various types of stainless steel elbows that are designed, developed, and manufactured to meet the diverse needs of the plumbing and construction industries. The company uses state-of-the-art technology, coupled with high-quality raw materials, to create durable and functional stainless steel elbows that are ideal for a wide range of applications.One of the standout features of [Company name]'s stainless steel elbows is their ability to withstand high-pressure environments. This is because the company uses high-grade stainless steel that has been engineered to maintain its structural integrity even under intense pressure. As a result, their products are ideal for use in systems that deal with corrosive fluids, high-temperature environments, and other challenging conditions.Additionally, [Company name]'s stainless steel elbows exhibit excellent resistance to a wide range of chemicals, ensuring that they can be used in an array of plumbing applications. This feature makes their products a popular choice for use in industries such as pharmaceuticals, food and beverage, and chemical production, among others.[Company name]'s team of skilled and experienced professionals is committed to ensuring that their products meet the highest standards of quality and safety. The company adheres to stringent quality control measures, from sourcing raw materials to the finished product's final inspection, to ensure that their stainless steel elbows are of the highest quality possible.The company's customer-centric approach has earned them a loyal customer base, with clients singling out their exceptional customer service experience. [Company name] provides comprehensive support to its customers, from initial product recommendations to after-sales support.In summary, [Company name] is a leading manufacturer of high-quality stainless steel elbows that are engineered to meet the highest standards of quality, durability, and functionality. Their products are ideal for use in a wide range of plumbing applications and are designed to withstand harsh environments, high-pressure systems, and corrosive fluids. By maintaining excellent customer service standards, [Company name] has earned its place as a trusted and reliable plumbing fittings manufacturer in the industry.
Key Information on Choosing the Right Welding Electrode for Your Project
Title: Revolutionary Welding Electrode Innovates the Industry - Improving Efficiency and QualityIntroduction:In the ever-evolving world of welding technology, companies are continuously seeking new advancements to enhance efficiency and quality. In line with this demand, {Company Name}, a renowned industry leader, has introduced an innovative welding electrode that promises to revolutionize the field. This welding electrode, which boasts incredible capabilities, is set to transform welding processes, streamline operations, and deliver exceptional results like never before.Company Overview:{Company Name}, a well-established welding solutions provider, has a rich history of delivering cutting-edge products. With a commitment to quality and continuous innovation, the company has become a trusted partner for various industries, including automotive, construction, oil and gas, and manufacturing. Their team of skilled engineers and technicians work diligently to develop advanced welding technologies that address industry challenges and meet customer needs.Revolutionary Welding Electrode:The latest offering from {Company Name}, which we shall refer to as the "Advanced Welding Electrode," is the result of years of research and development. This innovative product is designed to enhance welding operations by improving efficiency, productivity, versatility, and overall welding quality.Improved Efficiency and Productivity:The Advanced Welding Electrode incorporates state-of-the-art features that significantly improve efficiency and productivity. Its enhanced coating formulation ensures smooth and steady arc stability, resulting in reduced spatter and welding defects. This attribute greatly decreases post-welding clean-up time, allowing welders to operate more efficiently and complete projects in a shorter duration.Moreover, the electrode's excellent heat dissipation properties minimize the risk of overheating, reducing downtime due to material damage and equipment failure. This feature, combined with its exceptional tie-in wetting ability, ensures seamless fusion between metals, maximizing welding productivity and minimizing waste.Enhanced Versatility and Adaptability:{Company Name}'s Advanced Welding Electrode offers superior adaptability to a wide range of welding scenarios. It is suitable for various metals, including carbon steel, stainless steel, and non-ferrous alloys. This versatile electrode performs exceptionally well in all welding positions, allowing welders to work with ease and confidence while maintaining high-quality standards.Additionally, the electrode's unique self-releasing slag formula improves welder visibility during the welding process. This enhancement promotes precise control and accuracy, resulting in meticulously welded joints, especially in complex and intricate welding projects.Uncompromised Welding Quality:The focus on welding quality is evident in every aspect of the Advanced Welding Electrode. Its remarkable arc stability, combined with minimal spatter and excellent slag control, ensures clean and smooth welds with minimal defects. This remarkable weld integrity is further reinforced by the electrode's ability to eliminate undesirable elements like sulfur and phosphorus, guaranteeing welds of exceptional quality and longevity.Moreover, {Company Name} has implemented rigorous quality control processes to guarantee consistent electrode performance. The company subjects each electrode batch to comprehensive testing, including tensile strength, elongation, and impact toughness assessments. This dedication to quality assurance provides customers with utmost confidence in the product's reliability and performance.Conclusion:{Company Name}'s introduction of the Advanced Welding Electrode is poised to create a significant impact in the welding industry. With its advanced features, enhanced efficiency and productivity, versatility, and unwavering commitment to welding quality, this revolutionary electrode presents unmatched benefits for welders across various industries.As {Company Name} continues to innovate and provide cutting-edge solutions, the Advanced Welding Electrode is a testament to their dedication towards empowering welders and revolutionizing the welding industry. The progressive strides made by {Company Name} demonstrate their commitment to meeting the evolving needs of the market while ensuring sustainable success for their customers.